Understanding Thermal Conductivity
Thermal conductivity is a physical property that quantifies the ability of a material to transfer heat. It is defined as the rate at which heat is conducted through a material per unit thickness, per unit area, and per unit temperature difference. The SI unit for thermal conductivity is watts per meter-kelvin (W/mK).
Materials with high thermal conductivity allow heat to flow through them easily, while materials with low thermal conductivity act as insulators, resisting the flow of heat. In the context of PCBs, thermal conductivity is crucial because it determines how effectively the board can dissipate heat generated by the components mounted on it.
Factors Affecting Thermal Conductivity
Several factors influence the thermal conductivity of a PCB, including:
- Material Composition: The thermal conductivity of a PCB is largely determined by the materials used in its construction. The most common materials used in PCBs are:
- FR-4: A composite material made of woven fiberglass cloth with an epoxy resin binder. It has a relatively low thermal conductivity of around 0.3 W/mK.
- Metal-Core PCB (MCPCB): A PCB with a metal core, typically aluminum or copper, that provides a high thermal conductivity path for heat dissipation. The thermal conductivity of MCPCBs can range from 1 to 10 W/mK, depending on the metal used and its thickness.
-
Ceramic: A PCB substrate made of ceramic materials, such as aluminum nitride (AlN) or alumina (Al2O3), which offer high thermal conductivity, ranging from 20 to 200 W/mK.
-
Thickness: The thickness of the PCB and its layers can also affect its thermal conductivity. Thicker boards generally have better thermal conductivity than thinner ones, as they provide more cross-sectional area for heat transfer.
-
Copper Thickness: The thickness of the copper traces on the PCB can also impact its thermal conductivity. Thicker copper traces offer lower electrical resistance and better heat spreading capabilities.
-
Thermal Vias: Thermal vias are small, plated holes drilled through the PCB to provide a thermal path for heat to flow from one side of the board to the other. The number, size, and placement of thermal vias can significantly affect the overall thermal conductivity of the PCB.
Thermal Conductivity of Common PCB Materials
Let’s take a closer look at the thermal conductivity values of some common PCB materials:
Material | Thermal Conductivity (W/mK) |
---|---|
FR-4 | 0.3 |
Aluminum (MCPCB) | 150-200 |
Copper (MCPCB) | 350-400 |
Aluminum Nitride (AlN) | 150-200 |
Alumina (Al2O3) | 20-30 |
As seen in the table, MCPCBs with aluminum or copper cores offer significantly higher thermal conductivity compared to traditional FR-4 PCBs. Ceramic materials like aluminum nitride and alumina also provide excellent thermal conductivity, making them suitable for high-power applications.
Measuring Thermal Conductivity
There are several methods used to measure the thermal conductivity of PCBs, including:
-
Guarded Hot Plate Method: This method involves placing the PCB sample between two heated plates and measuring the temperature gradient across the sample. The thermal conductivity is then calculated based on the heat flux and temperature difference.
-
Laser Flash Method: In this method, a short laser pulse is used to heat one side of the PCB sample, and the temperature rise on the opposite side is measured using an infrared detector. The thermal diffusivity and specific heat capacity of the sample are then used to calculate its thermal conductivity.
-
Thermal Imaging: Thermal imaging cameras can be used to visualize the temperature distribution across a PCB during operation. This method allows for the identification of hot spots and the evaluation of the overall thermal performance of the board.
Impact of Thermal Conductivity on PCB Performance
The thermal conductivity of a PCB has a significant impact on its performance and reliability. Poor thermal management can lead to several issues, such as:
-
Component Overheating: When components generate heat faster than the PCB can dissipate it, they can overheat and fail prematurely. This is particularly problematic for high-power components like processors, power amplifiers, and Voltage Regulators.
-
Reduced Lifespan: Elevated operating temperatures can accelerate the aging process of components and reduce their lifespan. Every 10°C increase in temperature can halve the expected life of some electronic components.
-
Performance Degradation: As components heat up, their electrical characteristics can change, leading to performance degradation. For example, the switching speed of transistors can decrease, and the resistance of conductors can increase, resulting in lower efficiency and increased power consumption.
To mitigate these issues, designers must carefully consider the thermal conductivity of the PCB materials and incorporate appropriate thermal management techniques. Some common strategies include:
- Using high thermal conductivity materials like MCPCBs or ceramic substrates for high-power components.
- Incorporating thermal vias to provide a low-resistance thermal path between layers.
- Using thermal interface materials (TIMs) to improve heat transfer between components and the PCB.
- Implementing heat sinks, fans, or other cooling solutions to enhance heat dissipation.
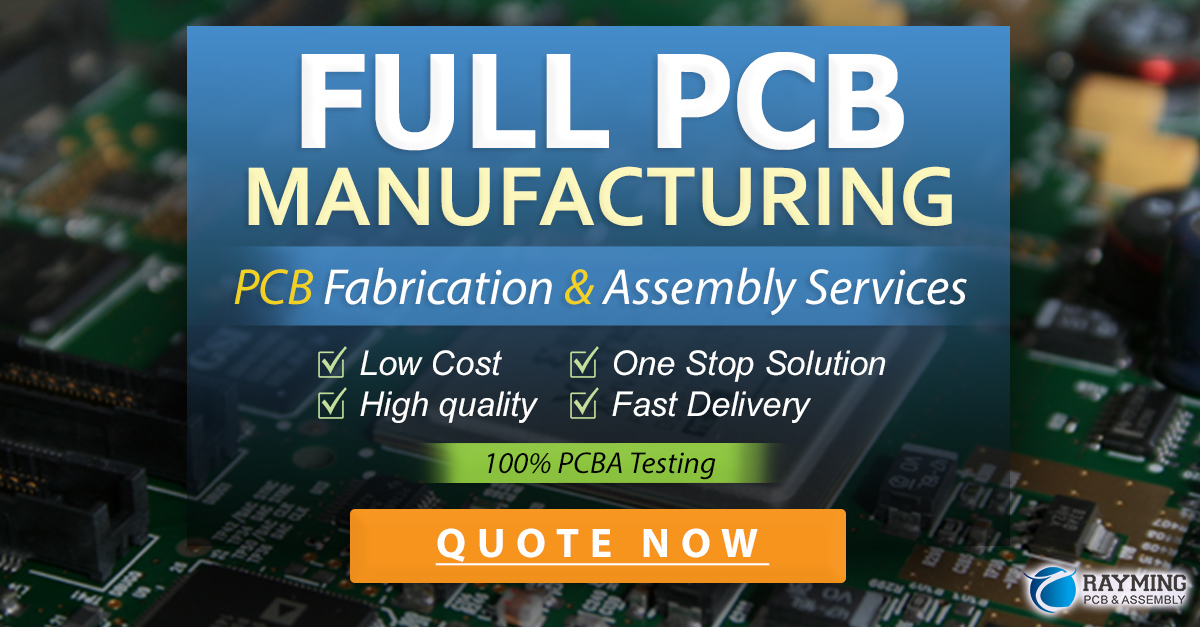
FAQ
-
What is the most common PCB material, and what is its thermal conductivity?
The most common PCB material is FR-4, which is a composite made of woven fiberglass cloth with an epoxy resin binder. FR-4 has a relatively low thermal conductivity of around 0.3 W/mK. -
What are MCPCBs, and how do they differ from traditional PCBs in terms of thermal conductivity?
Metal-Core PCBs (MCPCBs) are PCBs with a metal core, typically aluminum or copper, that provides a high thermal conductivity path for heat dissipation. MCPCBs offer significantly higher thermal conductivity compared to traditional FR-4 PCBs, with values ranging from 1 to 10 W/mK, depending on the metal used and its thickness. -
How does the thickness of a PCB affect its thermal conductivity?
Thicker PCBs generally have better thermal conductivity than thinner ones, as they provide more cross-sectional area for heat transfer. However, increasing the thickness of a PCB can also increase its weight and cost. -
What are thermal vias, and how do they influence the thermal conductivity of a PCB?
Thermal vias are small, plated holes drilled through the PCB to provide a thermal path for heat to flow from one side of the board to the other. The number, size, and placement of thermal vias can significantly affect the overall thermal conductivity of the PCB by providing low-resistance paths for heat transfer. -
How can poor thermal management impact the performance and reliability of electronic devices?
Poor thermal management can lead to several issues, such as component overheating, reduced lifespan, and performance degradation. When components generate heat faster than the PCB can dissipate it, they can overheat and fail prematurely. Elevated operating temperatures can also accelerate the aging process of components and cause their electrical characteristics to change, resulting in lower efficiency and increased power consumption.
In conclusion, the thermal conductivity of PCBs plays a crucial role in the thermal management and overall performance of electronic devices. By understanding the factors that influence thermal conductivity and the properties of different PCB materials, designers can make informed decisions to ensure optimal heat dissipation and reliability. Incorporating appropriate thermal management techniques, such as using high thermal conductivity materials, thermal vias, and cooling solutions, can significantly improve the thermal performance of PCBs and extend the lifespan of electronic components.
Leave a Reply