Introduction to PCB Parameters
Printed Circuit Boards (PCBs) are the backbone of modern electronics. They provide a platform for mounting and interconnecting electronic components to create a functional circuit. To ensure proper functionality, reliability, and manufacturability of a PCB, several key parameters must be considered during the design process. This article will delve into the essential PCB parameters that every designer should understand.
PCB Material Selection
PCB Substrate Materials
The choice of PCB substrate material is crucial as it affects the board’s electrical, mechanical, and thermal properties. Common substrate materials include:
Material | Description | Applications |
---|---|---|
FR-4 | Flame Retardant, Glass-Reinforced Epoxy Laminate | General-purpose, cost-effective |
High Tg FR-4 | Improved thermal stability and higher glass transition temperature | High-reliability applications |
Polyimide | High temperature resistance, flexibility | Aerospace, military, flexible circuits |
PTFE (Teflon) | Low dielectric constant, high frequency performance | RF and microwave applications |
Aluminum | Excellent thermal conductivity | High-power LED lighting, heat dissipation |
Copper Foil Thickness
The thickness of the copper foil used on the PCB affects its current carrying capacity, impedance, and manufacturing process. Standard copper foil thicknesses are:
Thickness (oz) | Thickness (μm) | Common Applications |
---|---|---|
0.5 oz | 17.5 μm | Low-power, high-density designs |
1 oz | 35 μm | General-purpose, most common |
2 oz | 70 μm | Higher current carrying capacity |
3 oz | 105 μm | Power electronics, high-current applications |
PCB Stack-up
Number of Layers
The number of layers in a PCB depends on the complexity of the circuit and the required functionality. Common layer configurations include:
- Single-layer: Simple, cost-effective designs
- Double-layer: Most common, allows for more complex routing
- Multi-layer (4, 6, 8, or more): High-density designs, improved signal integrity, and EMI reduction
Layer Stack-up Arrangement
The arrangement of layers in a multi-layer PCB is critical for signal integrity and EMI reduction. A typical 4-layer stack-up might include:
Layer | Function |
---|---|
Top | Signal, components |
Inner 1 | Ground plane |
Inner 2 | Power plane |
Bottom | Signal, components |
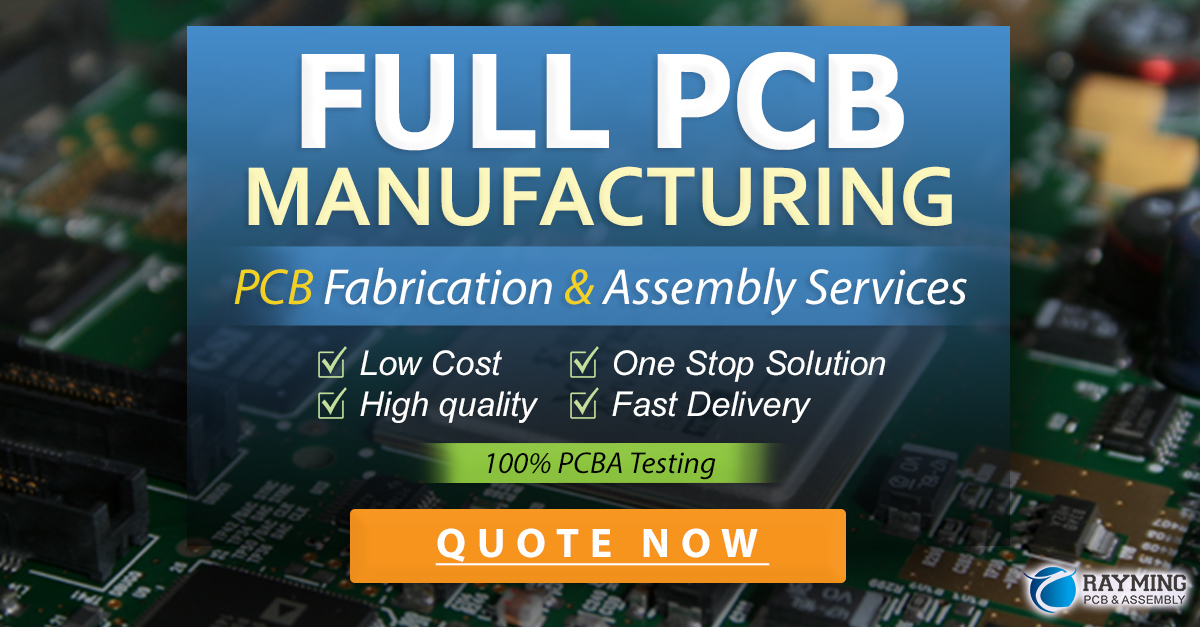
PCB Trace Parameters
Trace Width
The width of PCB traces determines their current carrying capacity and impedance. Wider traces can carry more current but may increase the board size. Narrower traces allow for higher density but have limited current capacity. Trace width is typically determined by:
- Current requirements
- Manufacturing constraints
- Impedance matching
Trace Spacing
The spacing between PCB traces affects signal integrity, crosstalk, and manufacturing yield. Minimum trace spacing is determined by:
- Voltage difference between traces
- PCB manufacturing capabilities
- Design standards (e.g., IPC)
Trace Thickness
Trace thickness, or height, is determined by the copper foil thickness used. Thicker traces have lower resistance and higher current carrying capacity but may increase manufacturing costs.
PCB Hole Parameters
Drill Hole Size
The size of drilled holes in a PCB depends on the component leads and manufacturing constraints. Common drill hole sizes range from 0.2 mm to 6 mm. Smaller drill sizes allow for higher density but may increase manufacturing costs.
Annular Ring
The annular ring is the copper pad surrounding a drilled hole. It provides a connection between the hole and the trace. The minimum annular ring size is determined by:
- Manufacturing tolerances
- Mechanical strength requirements
- Electrical connectivity
Hole-to-Hole Spacing
The spacing between drilled holes affects the mechanical strength and manufacturability of the PCB. Minimum hole-to-hole spacing is determined by:
- PCB thickness
- Drilling capabilities
- Design standards (e.g., IPC)
PCB Surface Finish
The surface finish on a PCB protects the copper from oxidation and enhances solderability. Common surface finishes include:
Finish | Description | Advantages |
---|---|---|
HASL (Hot Air Solder Leveling) | Solder coating | Cost-effective, good solderability |
ENIG (Electroless Nickel Immersion Gold) | Nickel and gold plating | Flat surface, excellent solderability |
OSP (Organic Solderability Preservative) | Organic compound coating | Cost-effective, good shelf life |
Immersion Silver | Silver plating | Good solderability, lower cost than ENIG |
PCB Design Rules
Clearance and Creepage
Clearance is the shortest distance through air between two conductors, while creepage is the shortest distance along the surface of the PCB. Minimum clearance and creepage distances are determined by:
- Voltage levels
- Environmental conditions
- Safety standards
Solder Mask and Silkscreen
Solder mask is a polymer coating that protects the PCB from solder bridging and corrosion. Silkscreen is used to print component identifiers and other markings on the PCB surface. Key parameters include:
- Solder mask expansion
- Silkscreen line width
- Solder mask and silkscreen color
Frequently Asked Questions (FAQ)
1. What is the most common PCB substrate material?
FR-4 is the most common PCB substrate material due to its cost-effectiveness and good electrical and mechanical properties. It is suitable for a wide range of general-purpose applications.
2. How does the number of layers in a PCB affect its performance?
Increasing the number of layers in a PCB allows for more complex routing, improved signal integrity, and better EMI reduction. However, it also increases the manufacturing cost and complexity.
3. What factors determine the minimum trace width and spacing?
The minimum trace width and spacing are determined by the current requirements, manufacturing constraints, impedance matching, and voltage differences between traces. PCB manufacturers typically have specific capabilities and limitations that must be considered.
4. Why is the annular ring important in PCB design?
The annular ring provides a connection between the drilled hole and the trace. It ensures proper electrical connectivity and mechanical strength. The minimum annular ring size is determined by manufacturing tolerances and design standards.
5. How do I choose the appropriate surface finish for my PCB?
The choice of surface finish depends on factors such as cost, solderability, shelf life, and compatibility with the assembly process. HASL is a cost-effective option for general-purpose applications, while ENIG provides a flat surface and excellent solderability for high-reliability applications.
Conclusion
Understanding basic PCB parameters is essential for designing reliable, manufacturable, and cost-effective printed circuit boards. By considering factors such as substrate material, copper thickness, layer stack-up, trace dimensions, hole parameters, and surface finish, designers can ensure their PCBs meet the required electrical, mechanical, and thermal performance criteria. Adhering to industry standards and manufacturer capabilities is also crucial for successful PCB fabrication and assembly.
Leave a Reply