Introduction to PCB Stack-up
A PCB stack-up refers to the arrangement of copper layers and insulating materials that make up a printed circuit board (PCB). The stack-up defines the number of layers, their order, and the thickness of each layer. In this article, we will focus on the basic stack-up of a 16-layer PCB board and discuss its various aspects.
Understanding the 16 Layer PCB Stack-up
A 16-layer PCB is a complex and high-density board that is commonly used in advanced electronic applications such as telecommunications, aerospace, and military systems. The basic stack-up of a 16-layer PCB typically consists of the following layers:
- Top Layer (Signal)
- Ground Plane
- Signal Layer
- Signal Layer
- Ground Plane
- Signal Layer
- Signal Layer
- Power Plane
- Signal Layer
- Signal Layer
- Ground Plane
- Signal Layer
- Signal Layer
- Ground Plane
- Signal Layer
- Bottom Layer (Signal)
Signal Layers
The signal layers in a 16-layer PCB are used for routing the electrical signals between components. These layers are typically located on the outer surfaces of the board (top and bottom) and in between the power and ground planes. The number of signal layers in a 16-layer PCB can vary depending on the design requirements, but a common configuration is to have 12 signal layers (1, 3, 4, 6, 7, 9, 10, 12, 13, 15, and 16).
Power Planes
Power planes are used to distribute power to the components on the PCB. In a 16-layer PCB, there is usually one dedicated power plane (layer 8) that provides a stable and low-impedance power source to the entire board. The power plane is typically made of a solid copper sheet and is connected to the power supply through vias.
Ground Planes
Ground planes are used to provide a reference point for the electrical signals and to reduce electromagnetic interference (EMI). In a 16-layer PCB, there are typically four ground planes (layers 2, 5, 11, and 14) that are evenly distributed throughout the stack-up. The ground planes are also made of solid copper sheets and are connected to the ground of the power supply through vias.
Advantages of a 16 Layer PCB Stack-up
Using a 16-layer PCB stack-up offers several advantages over boards with fewer layers:
-
Increased routing density: With 16 layers, there is more space available for routing traces, which allows for higher component density and more complex designs.
-
Better signal integrity: The dedicated power and ground planes help to reduce noise and improve signal quality by providing a stable reference point for the signals.
-
Reduced EMI: The multiple ground planes help to shield the signals from external interference and reduce EMI emissions from the board.
-
Improved thermal management: The increased number of layers helps to distribute heat more evenly across the board, which can improve the overall thermal performance of the system.
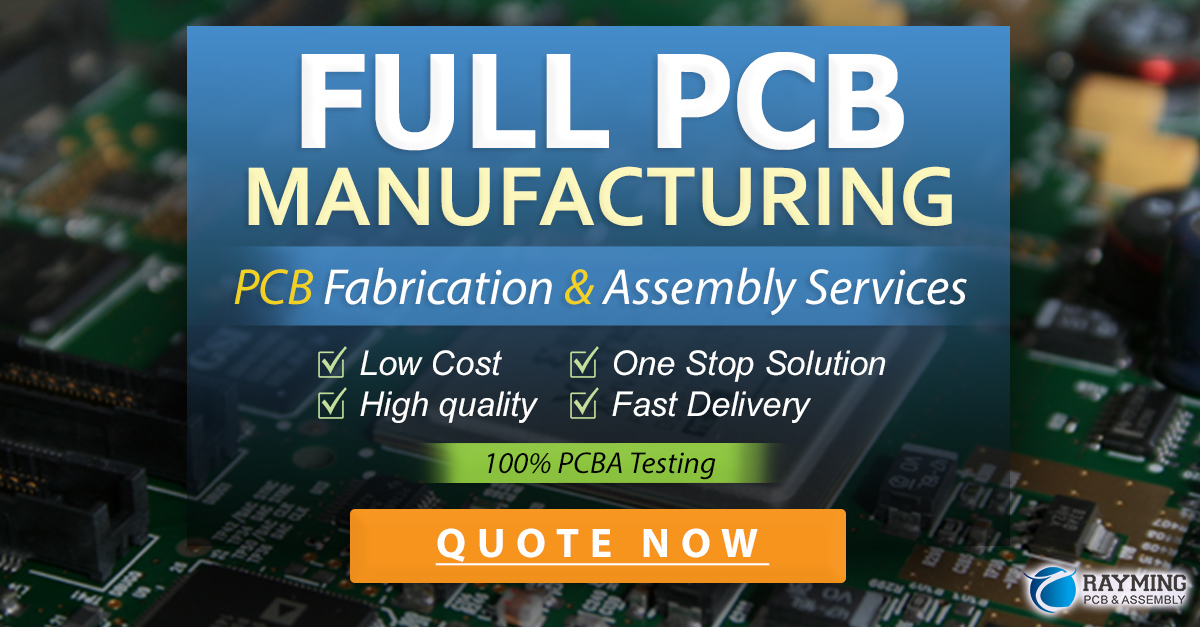
Challenges of a 16 Layer PCB Stack-up
Despite the advantages, designing and manufacturing a 16-layer PCB also presents some challenges:
-
Increased complexity: With 16 layers, the design and layout process becomes more complex and time-consuming. It requires careful planning and attention to detail to ensure that all the signals are routed correctly and that there are no conflicts between layers.
-
Higher cost: The increased number of layers and the complexity of the manufacturing process make 16-layer PCBs more expensive than boards with fewer layers.
-
Longer lead times: Due to the complexity of the design and manufacturing process, 16-layer PCBs typically have longer lead times than simpler boards.
-
Difficulty in debugging: With so many layers, it can be challenging to debug and troubleshoot issues on a 16-layer PCB. Special tools and techniques may be required to isolate and resolve problems.
Design Considerations for a 16 Layer PCB Stack-up
When designing a 16-layer PCB stack-up, there are several key factors to consider:
-
Material selection: The choice of materials for the PCB substrate and the copper layers can have a significant impact on the performance and reliability of the board. Factors such as the dielectric constant, dissipation factor, and thermal conductivity should be carefully considered.
-
Thickness of layers: The thickness of each layer in the stack-up should be optimized based on the electrical and mechanical requirements of the design. Thicker layers may be needed for high-current power planes, while thinner layers may be used for dense signal routing.
-
Via design: The design of the vias that connect the layers is critical for ensuring reliable and efficient signal transmission. The size, shape, and placement of the vias should be carefully considered to minimize signal loss and reflections.
-
Impedance control: Maintaining consistent impedance across the signal layers is important for ensuring signal integrity and reducing reflections. This can be achieved through careful design of the trace widths and spacing, as well as the use of controlled impedance materials.
-
Thermal management: Adequate thermal management is essential for ensuring the reliability and longevity of the PCB. The stack-up should be designed to promote efficient heat dissipation, with the use of thermal vias and heat spreaders where necessary.
Manufacturing Process for a 16 Layer PCB
The manufacturing process for a 16-layer PCB is complex and requires specialized equipment and expertise. The basic steps involved in the process are as follows:
-
Inner layer fabrication: The inner layers of the PCB are fabricated by etching the copper on the substrate material according to the design pattern. The etched layers are then inspected for defects and cleaned.
-
Lamination: The inner layers are stacked and aligned according to the stack-up design, with insulating material (prepreg) placed between each layer. The stack is then laminated under high pressure and temperature to fuse the layers together.
-
Drilling: Holes are drilled through the laminated board to create vias and mounting holes for components. The holes are then cleaned and debris is removed.
-
Plating: The drilled holes are plated with copper to create a conductive pathway between the layers. Additional copper is also plated on the outer layers to create pads and traces.
-
Outer layer fabrication: The outer layers of the PCB are fabricated by etching the copper according to the design pattern, similar to the inner layer fabrication process.
-
Solder mask and silkscreen: A solder mask is applied to the outer layers to protect the copper traces and prevent solder bridging. A silkscreen layer is also applied to provide labeling and identification of components.
-
Surface finish: A surface finish, such as HASL (Hot Air Solder Leveling) or ENIG (Electroless Nickel Immersion Gold), is applied to the exposed copper surfaces to protect them from oxidation and enhance solderability.
-
Electrical testing: The completed PCB is electrically tested to ensure that all connections are sound and that there are no short circuits or open circuits.
Common Applications of 16 Layer PCBs
16-layer PCBs are used in a wide range of industries and applications where high density, high performance, and reliability are critical. Some common applications include:
-
Telecommunications: 16-layer PCBs are used in high-speed networking equipment, such as routers and switches, to handle the complex routing and switching of data signals.
-
Aerospace and defense: In aerospace and defense applications, 16-layer PCBs are used in radar systems, satellite communications, and avionics equipment where reliability and performance are paramount.
-
Medical devices: Advanced medical devices, such as imaging systems and patient monitoring equipment, rely on 16-layer PCBs to process and transmit large amounts of data in real-time.
-
Industrial automation: 16-layer PCBs are used in industrial automation systems, such as robotics and process control equipment, to handle the complex control and communication functions required for high-speed, high-precision operations.
-
High-performance computing: In data centers and supercomputing applications, 16-layer PCBs are used to provide the high-speed interconnects and power distribution required for processing massive amounts of data.
Conclusion
A 16-layer PCB stack-up is a complex and highly engineered structure that is designed to meet the demands of advanced electronic applications. By understanding the basic structure and design considerations of a 16-layer PCB, engineers can create boards that offer high performance, reliability, and functionality. However, the complexity and cost of 16-layer PCBs also present challenges that must be carefully managed through proper design, manufacturing, and testing processes.
FAQ
-
Q: What is the typical thickness of a 16-layer PCB?
A: The thickness of a 16-layer PCB can vary depending on the specific design and material requirements, but a typical thickness range is between 0.093 inches (2.36 mm) and 0.125 inches (3.175 mm). -
Q: Can a 16-layer PCB be manufactured with a different stack-up configuration?
A: Yes, the stack-up configuration of a 16-layer PCB can be customized based on the specific design requirements. The number and arrangement of signal, power, and ground layers can be adjusted to optimize performance and manufacturability. -
Q: What is the minimum trace width and spacing that can be achieved on a 16-layer PCB?
A: The minimum trace width and spacing on a 16-layer PCB depends on the manufacturing capabilities of the PCB fabricator. Typically, trace widths and spacing of 3-4 mils (0.003-0.004 inches or 0.0762-0.1016 mm) can be achieved on the inner layers, while the outer layers may have slightly larger minimums. -
Q: How does the cost of a 16-layer PCB compare to boards with fewer layers?
A: 16-layer PCBs are significantly more expensive than boards with fewer layers due to the increased complexity of the manufacturing process and the higher material costs. The cost of a 16-layer PCB can be several times higher than a 4-layer or 6-layer board of the same size. -
Q: What are the key challenges in designing a 16-layer PCB?
A: The key challenges in designing a 16-layer PCB include ensuring proper signal integrity, managing the complex routing of traces, maintaining consistent impedance, and ensuring adequate thermal management. The design process requires careful planning and simulation to ensure that the board will meet the performance and reliability requirements of the application.
Leave a Reply