Introduction
When it comes to designing and manufacturing printed circuit boards (PCBs), selecting the appropriate surface finish is crucial for ensuring the reliability, durability, and functionality of the final product. The surface finish not only protects the copper traces from oxidation and corrosion but also plays a vital role in the solderability and assembly process. With a wide range of PCB Surface Finishes available, each with its unique properties and advantages, it can be challenging to determine the best option for your specific application. In this comprehensive article, we will explore the various PCB surface finishes, their characteristics, and the factors to consider when making your selection.
Understanding PCB Surface Finishes
What is a PCB Surface Finish?
A PCB surface finish is a coating applied to the exposed copper traces and pads on a printed circuit board. Its primary purpose is to protect the copper from oxidation and corrosion, enhance solderability, and improve the overall reliability of the PCB. The surface finish also plays a crucial role in the assembly process, as it affects the ease and quality of component attachment.
Why is Selecting the Right Surface Finish Important?
Choosing the appropriate surface finish for your PCB is essential for several reasons:
- Protection: The surface finish acts as a barrier, preventing the copper from oxidizing and corroding when exposed to environmental factors such as humidity and air.
- Solderability: The surface finish influences the ability of solder to wet and adhere to the copper pads, ensuring a strong and reliable connection between components and the PCB.
- Compatibility: Different surface finishes have varying levels of compatibility with different assembly processes, components, and environmental conditions.
- Cost: The choice of surface finish can impact the overall cost of PCB manufacturing, as some finishes are more expensive than others.
- Reliability: Selecting the right surface finish contributes to the long-term reliability and performance of the PCB, reducing the risk of failures and ensuring the product meets its intended lifespan.
Common PCB Surface Finishes
Hot Air Solder Leveling (HASL)
HASL is one of the most widely used PCB surface finishes, known for its excellent solderability and cost-effectiveness. In this process, the PCB is dipped into a molten solder bath, and then hot air is used to blow off the excess solder, leaving a thin, uniform coating on the copper pads. HASL provides good protection against oxidation and is compatible with a wide range of assembly processes.
Advantages:
- Excellent solderability
- Cost-effective
- Widely available and compatible with most assembly processes
- Good shelf life
Disadvantages:
- Solder thickness can be inconsistent, leading to uneven surfaces
- Not suitable for fine-pitch components due to the risk of solder bridging
- Limited flatness, which can affect component placement accuracy
- Contains lead, which may not be suitable for RoHS-compliant products
Immersion Silver (IAg)
Immersion silver is a popular lead-free surface finish that offers excellent solderability and electrical conductivity. In this process, the PCB is immersed in a silver solution, resulting in a thin, uniform layer of silver deposited on the copper pads. IAg provides good protection against oxidation and is compatible with most assembly processes.
Advantages:
- Excellent solderability
- Good electrical conductivity
- Lead-free and RoHS-compliant
- Suitable for fine-pitch components
- Relatively low cost compared to other lead-free finishes
Disadvantages:
- Limited shelf life due to silver’s susceptibility to tarnishing
- May require additional processing steps for optimal solderability
- Not suitable for high-temperature applications
Electroless Nickel Immersion Gold (ENIG)
ENIG is a popular surface finish that offers excellent corrosion resistance, good solderability, and extended shelf life. In this two-step process, a layer of nickel is first deposited on the copper pads, followed by a thin layer of gold. The nickel layer provides a barrier against copper diffusion, while the gold layer protects the nickel from oxidation and enhances solderability.
Advantages:
- Excellent corrosion resistance
- Good solderability
- Extended shelf life
- Suitable for fine-pitch components
- Compatible with wire bonding and other advanced assembly processes
- Lead-free and RoHS-compliant
Disadvantages:
- Higher cost compared to other surface finishes
- Potential for “black pad” defects due to improper plating processes
- Gold can be susceptible to scratches and damage during handling
Organic Solderability Preservative (OSP)
OSP is a lead-free, organic coating that is applied to the copper pads to prevent oxidation and enhance solderability. This thin, transparent layer acts as a barrier against environmental factors, while still allowing for excellent solder wetting during the assembly process. OSP is a cost-effective and environmentally friendly option.
Advantages:
- Cost-effective
- Lead-free and RoHS-compliant
- Good solderability
- Suitable for fine-pitch components
- Environmentally friendly
- Flat surface, promoting accurate component placement
Disadvantages:
- Limited shelf life due to the organic nature of the coating
- May require additional processing steps for optimal solderability
- Not suitable for multiple reflow cycles or rework processes
- Can be affected by handling and moisture
Immersion Tin (ISn)
Immersion tin is a lead-free surface finish that provides good solderability and protection against oxidation. In this process, the PCB is immersed in a tin solution, resulting in a thin, uniform layer of tin deposited on the copper pads. ISn offers a cost-effective alternative to other lead-free finishes.
Advantages:
- Good solderability
- Lead-free and RoHS-compliant
- Cost-effective compared to other lead-free finishes
- Suitable for fine-pitch components
- Compatible with most assembly processes
Disadvantages:
- Tin whiskers can form over time, potentially causing short circuits
- Limited shelf life due to the risk of tin oxidation
- May require additional processing steps for optimal solderability
Surface Finish | Solderability | Shelf Life | Cost | RoHS Compliance |
---|---|---|---|---|
HASL | Excellent | Good | Low | No |
Immersion Silver | Excellent | Limited | Moderate | Yes |
ENIG | Good | Excellent | High | Yes |
OSP | Good | Limited | Low | Yes |
Immersion Tin | Good | Limited | Moderate | Yes |
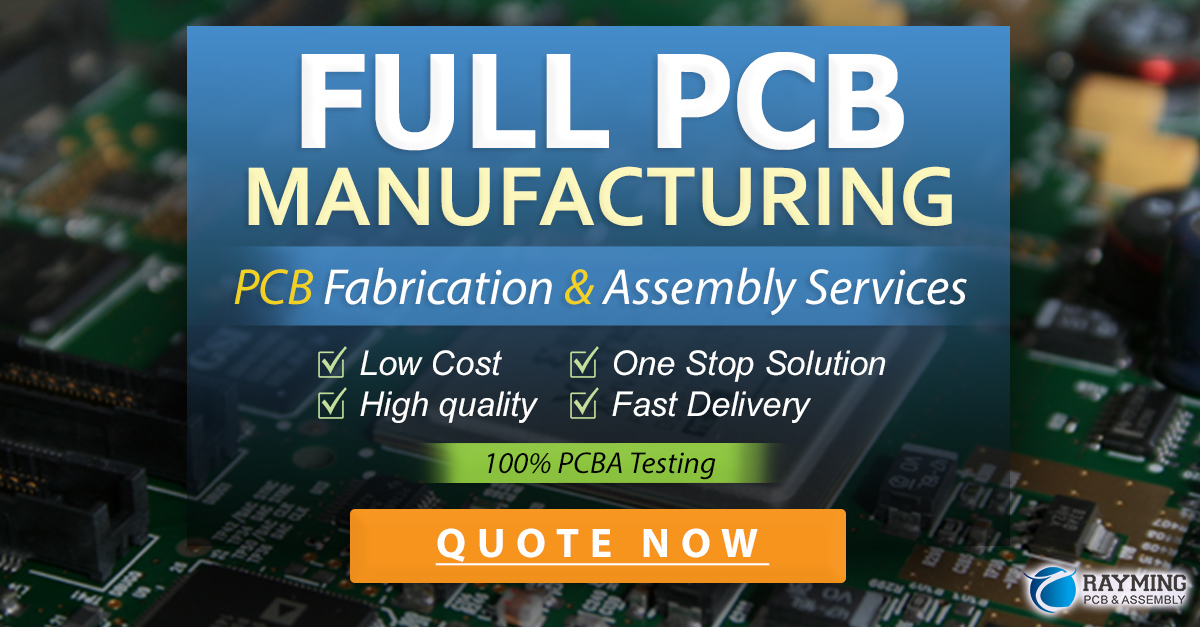
Factors to Consider When Selecting a PCB Surface Finish
When choosing the appropriate surface finish for your PCB, there are several key factors to consider:
- Application requirements: Consider the specific requirements of your application, such as operating environment, temperature range, and expected lifespan.
- Assembly process: Evaluate the compatibility of the surface finish with your intended assembly process, including soldering methods, component types, and rework requirements.
- Cost: Compare the costs of different surface finishes, taking into account both the initial manufacturing cost and the long-term cost implications of reliability and rework.
- Environmental regulations: Ensure that the selected surface finish complies with relevant environmental regulations, such as RoHS and REACH.
- Shelf life: Consider the expected shelf life of the PCB and choose a surface finish that provides adequate protection against oxidation and corrosion for the desired storage duration.
- Electrical performance: Evaluate the electrical properties of the surface finish, such as conductivity and impedance, to ensure compatibility with your application’s requirements.
- Solderability: Assess the solderability of the surface finish, considering factors such as solder wetting, joint strength, and the ability to accommodate fine-pitch components.
- Reliability: Consider the long-term reliability of the surface finish, including its resistance to corrosion, oxidation, and mechanical stress.
FAQ
-
Q: What is the most cost-effective PCB surface finish?
A: HASL and OSP are generally the most cost-effective PCB surface finishes, offering good solderability and protection at a lower cost compared to other options. -
Q: Which surface finishes are RoHS-compliant?
A: Immersion silver, ENIG, OSP, and immersion tin are all lead-free and RoHS-compliant surface finishes. -
Q: Can I use HASL for fine-pitch components?
A: HASL is not recommended for fine-pitch components due to the risk of solder bridging and uneven surfaces. Immersion silver, ENIG, or OSP are better suited for fine-pitch applications. -
Q: What is the shelf life of OSP-coated PCBs?
A: OSP has a limited shelf life due to the organic nature of the coating. Typically, OSP-coated PCBs have a shelf life of 3 to 6 months when stored in a controlled environment. -
Q: Is ENIG suitable for high-temperature applications?
A: Yes, ENIG is suitable for high-temperature applications due to its excellent corrosion resistance and stable performance under elevated temperatures.
Conclusion
Selecting the right surface finish for your PCB is a critical decision that impacts the reliability, solderability, and overall performance of your electronic product. By understanding the characteristics, advantages, and limitations of each surface finish, and considering factors such as application requirements, assembly process, cost, and environmental regulations, you can make an informed choice that meets your specific needs.
Whether you opt for the cost-effective HASL, the lead-free immersion silver, the robust ENIG, the environmentally friendly OSP, or the versatile immersion tin, ensuring that your chosen surface finish aligns with your project’s goals is essential for success.
Remember to work closely with your PCB manufacturer and assembly partners to discuss your requirements and preferences, as their expertise and guidance can help you navigate the selection process and optimize your PCB design for manufacturability and reliability.
By making an informed decision on your PCB surface finish, you can ensure that your electronic product performs at its best, meets industry standards, and delivers a competitive edge in the market.
Leave a Reply