What is a Rigid-Flex PCB?
A Rigid-Flex PCB is a unique type of printed circuit board that combines the best features of both rigid and Flexible PCBs. It consists of multiple layers of flexible and rigid substrates laminated together into a single structure. The flexible layers are made of thin, flexible materials such as polyimide or PEEK, while the rigid layers are made of standard PCB Materials like FR4.
The combination of rigid and flexible layers allows for the creation of three-dimensional circuits that can be folded, bent, or twisted to fit into tight spaces or conform to unique shapes. This makes Rigid-Flex PCBs ideal for applications where space is limited or where the PCB needs to be integrated into a moving or flexing device.
Advantages of Rigid-Flex PCBs
- Space savings: Rigid-Flex PCBs can be folded and bent to fit into tight spaces, reducing the overall size and weight of the device.
- Increased reliability: By eliminating connectors and reducing the number of solder joints, Rigid-Flex PCBs improve reliability and reduce the risk of failure.
- Improved signal integrity: The reduced number of connectors and shorter signal paths in Rigid-Flex PCBs can improve signal integrity and reduce noise and interference.
- Enhanced durability: Rigid-Flex PCBs are more resistant to vibration and shock than traditional PCBs, making them suitable for use in harsh environments.
- Design flexibility: The ability to create three-dimensional circuits allows for greater design flexibility and the creation of unique form factors.
Structure of a Rigid-Flex PCB
A Rigid-Flex PCB is made up of several layers of flexible and rigid materials laminated together. The number and arrangement of these layers can vary depending on the specific application and design requirements. A typical Rigid-Flex PCB structure might include:
- Flexible layers: These are made of thin, flexible materials such as polyimide or PEEK. They are typically used for the interconnections between rigid sections and for areas that require flexibility.
- Rigid layers: These are made of standard PCB materials like FR4. They provide structural support and are used for mounting components and connectors.
- Adhesive layers: These are used to bond the flexible and rigid layers together. They are typically made of acrylic or epoxy-based adhesives.
- Coverlay: This is a protective layer applied to the outer surfaces of the flexible sections to provide insulation and protection against damage.
Types of Rigid-Flex PCBs
Rigid-Flex PCBs can be categorized based on the number and arrangement of flexible and rigid layers:
- Single-sided Rigid-Flex PCBs: These have a single flexible layer bonded to one or more rigid layers. They are the simplest and most cost-effective type of Rigid-Flex PCB.
- Double-sided Rigid-Flex PCBs: These have flexible layers on both sides of the rigid layers. They offer more design flexibility and can accommodate more complex circuitry.
- Multi-layer Rigid-Flex PCBs: These have multiple flexible and rigid layers laminated together in a stack. They are used for the most complex and demanding applications.
Cost Considerations for Rigid-Flex PCBs
Rigid-Flex PCBs are generally more expensive than traditional rigid PCBs due to the additional materials and processing steps involved in their manufacture. The cost of a Rigid-Flex PCB can be influenced by several factors:
- Number of layers: More layers generally mean higher costs due to the increased complexity and material requirements.
- Size and shape: Larger and more complex shapes can be more difficult and expensive to manufacture.
- Material selection: The choice of flexible and rigid materials can affect the cost, with some high-performance materials being more expensive than others.
- Quantity: As with most PCBs, higher quantities can lead to lower per-unit costs due to economies of scale.
- Design complexity: More complex designs with tighter tolerances and smaller features can be more expensive to manufacture.
Cost Comparison: Rigid vs. Flex vs. Rigid-Flex PCBs
PCB Type | Relative Cost |
---|---|
Rigid PCB | 1x |
Flex PCB | 2-3x |
Rigid-Flex | 3-5x |
As shown in the table above, Rigid-Flex PCBs are typically the most expensive option, followed by Flex PCBs and then traditional Rigid PCBs. However, the cost premium for Rigid-Flex PCBs can be justified in applications where their unique benefits – such as space savings, reliability, and design flexibility – are critical.
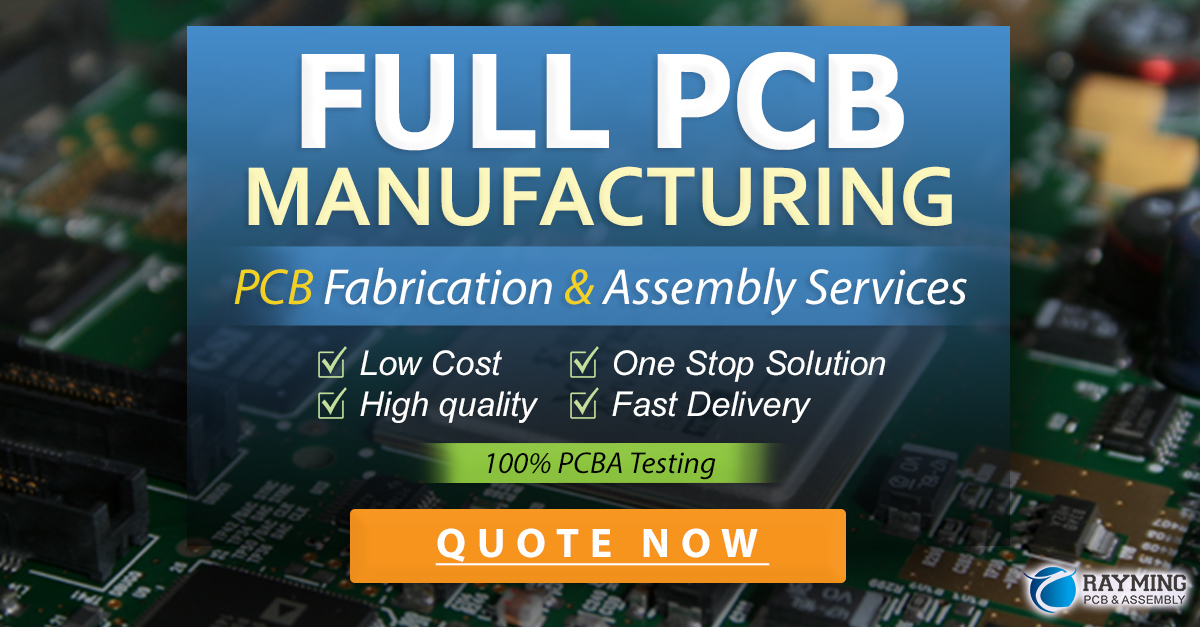
Choosing a Rigid-Flex PCB Manufacturer
Selecting the right manufacturer is critical to ensuring the success of your Rigid-Flex PCB project. Here are some key factors to consider when choosing a Rigid-Flex PCB manufacturer:
- Experience and expertise: Look for a manufacturer with a track record of successfully producing Rigid-Flex PCBs for a variety of applications and industries.
- Technical capabilities: Ensure that the manufacturer has the necessary equipment, processes, and expertise to meet your specific technical requirements, such as layer count, material selection, and feature size.
- Quality control: Choose a manufacturer with robust quality control processes and certifications, such as ISO 9001, to ensure consistent and reliable product quality.
- Customer support: Look for a manufacturer that offers responsive and knowledgeable customer support, from initial design consultation through to post-sales support.
- Cost and lead time: Consider the manufacturer’s pricing and lead times to ensure they align with your budget and project schedule.
Top Rigid-Flex PCB Manufacturers
Manufacturer | Location | Website |
---|---|---|
Würth Elektronik | Germany | www.we-online.com |
Nippon Mektron | Japan | www.mektron.co.jp |
TTM Technologies | United States | www.ttm.com |
Flex | United States | www.flex.com |
Kingfield Electronics | Hong Kong | www.kingfield-elec.com |
The table above lists some of the top Rigid-Flex PCB manufacturers globally. However, the best choice for your project will depend on your specific requirements and priorities.
Frequently Asked Questions (FAQ)
-
Q: What is the minimum bend radius for a Rigid-Flex PCB?
A: The minimum bend radius depends on the thickness and material of the flexible layers. As a general rule, the minimum bend radius is typically 6-10 times the thickness of the flexible layer. -
Q: Can Rigid-Flex PCBs be used in high-temperature environments?
A: Yes, Rigid-Flex PCBs can be designed for high-temperature applications by using appropriate materials, such as polyimide or PEEK, which can withstand temperatures up to 260°C or higher. -
Q: How do I design for the transition between rigid and flexible sections?
A: The transition between rigid and flexible sections is a critical area that requires careful design consideration. Use gradual transitions, avoid sharp corners, and provide adequate support and strain relief to minimize stress on the flexible layers. -
Q: Can components be mounted on the flexible sections of a Rigid-Flex PCB?
A: Yes, components can be mounted on the flexible sections, but it requires careful selection of components and mounting techniques to ensure reliability under flexing conditions. Surface mount components and low-profile packages are typically preferred. -
Q: What are the typical lead times for Rigid-Flex PCBs?
A: Lead times for Rigid-Flex PCBs can vary depending on the complexity of the design and the manufacturer’s workload. Typical lead times range from 3-5 weeks for standard designs to 8-10 weeks or more for complex, custom designs.
In conclusion, Rigid-Flex PCBs offer a unique combination of flexibility and durability that makes them ideal for a wide range of applications. By understanding the structure, cost considerations, and key factors in choosing a manufacturer, you can effectively incorporate Rigid-Flex PCBs into your designs and take advantage of their many benefits.
Leave a Reply