What is PCBA?
PCBA stands for Printed Circuit Board Assembly, which is the process of assembling electronic components onto a printed circuit board (PCB) to create a functional electronic device. The PCB is a flat board made of insulating materials, such as fiberglass or plastic, with conductive tracks, pads, and other features etched onto its surface. These conductive elements are used to connect various electronic components, such as resistors, capacitors, integrated circuits, and connectors, to form a complete circuit.
PCBA is a crucial step in the manufacturing of electronic devices, as it determines the functionality, reliability, and performance of the final product. The process involves several stages, including component placement, soldering, inspection, and testing, which require precision, accuracy, and adherence to industry standards and specifications.
Types of PCBA
There are several types of PCBA, each with its own characteristics, advantages, and applications. The most common types include:
1. Through-Hole PCBA
Through-hole PCBA is the traditional method of assembling electronic components onto a PCB. In this process, the components have long leads that are inserted through drilled holes in the PCB and soldered onto the opposite side. This type of PCBA is known for its strong mechanical connections and reliability, making it suitable for applications that require high durability and resistance to vibration and shock.
However, through-hole PCBA has some limitations, such as lower component density, larger board size, and higher assembly costs compared to other types of PCBA.
2. Surface Mount PCBA
Surface mount PCBA, also known as SMT (Surface Mount Technology) PCBA, is a more modern and widely used method of assembling electronic components onto a PCB. In this process, the components have small leads or terminations that are soldered directly onto the surface of the PCB, without the need for drilled holes.
SMT PCBA offers several advantages over through-hole PCBA, including:
- Higher component density, allowing for smaller and more compact board designs
- Faster assembly speeds, thanks to automated pick-and-place machines
- Lower assembly costs, due to reduced manual labor and material usage
- Better high-frequency performance, thanks to shorter lead lengths and reduced parasitic capacitance and inductance
However, SMT PCBA also has some challenges, such as the need for precise component placement and soldering, and the difficulty of reworking or replacing defective components.
3. Mixed Technology PCBA
Mixed technology PCBA combines both through-hole and surface mount components on the same PCB. This approach is often used when a design requires components that are not available in SMT packages, or when certain parts of the circuit require the strength and reliability of through-hole connections.
Mixed technology PCBA offers the benefits of both through-hole and SMT PCBA, but also requires careful design and planning to ensure proper component placement, soldering, and compatibility.
Applications of PCBA
PCBA is used in a wide range of electronic devices and systems, across various industries and sectors. Some of the most common applications include:
1. Consumer Electronics
PCBA is the backbone of many consumer electronic devices, such as:
- Smartphones, tablets, and laptops
- Televisions, audio systems, and home appliances
- Wearables, such as smartwatches and fitness trackers
- Gaming consoles and peripherals
2. Automotive Electronics
PCBA plays a crucial role in the automotive industry, powering various electronic systems and features, such as:
- Engine control units (ECUs) and sensors
- Infotainment and navigation systems
- Advanced driver assistance systems (ADAS) and autonomous driving technologies
- Electric vehicle (EV) batteries and charging systems
3. Medical Devices
PCBA is essential for the development and manufacturing of medical devices and equipment, such as:
- Diagnostic and imaging systems, such as X-ray, CT, and MRI machines
- Patient monitoring and life support devices
- Surgical instruments and robotics
- Wearable and implantable devices, such as pacemakers and insulin pumps
4. Industrial Automation and Control
PCBA is widely used in industrial automation and control systems, enabling the monitoring, regulation, and optimization of various processes and operations, such as:
- Programmable logic controllers (PLCs) and human-machine interfaces (HMIs)
- Sensors, actuators, and controllers for temperature, pressure, flow, and level
- Industrial robots and automated guided vehicles (AGVs)
- Smart factory and Industry 4.0 solutions
5. Aerospace and Defense
PCBA is critical for the aerospace and defense industries, powering a wide range of systems and applications, such as:
- Avionics and flight control systems
- Radar, sonar, and communication equipment
- Satellite and spacecraft electronics
- Military vehicles and weapon systems
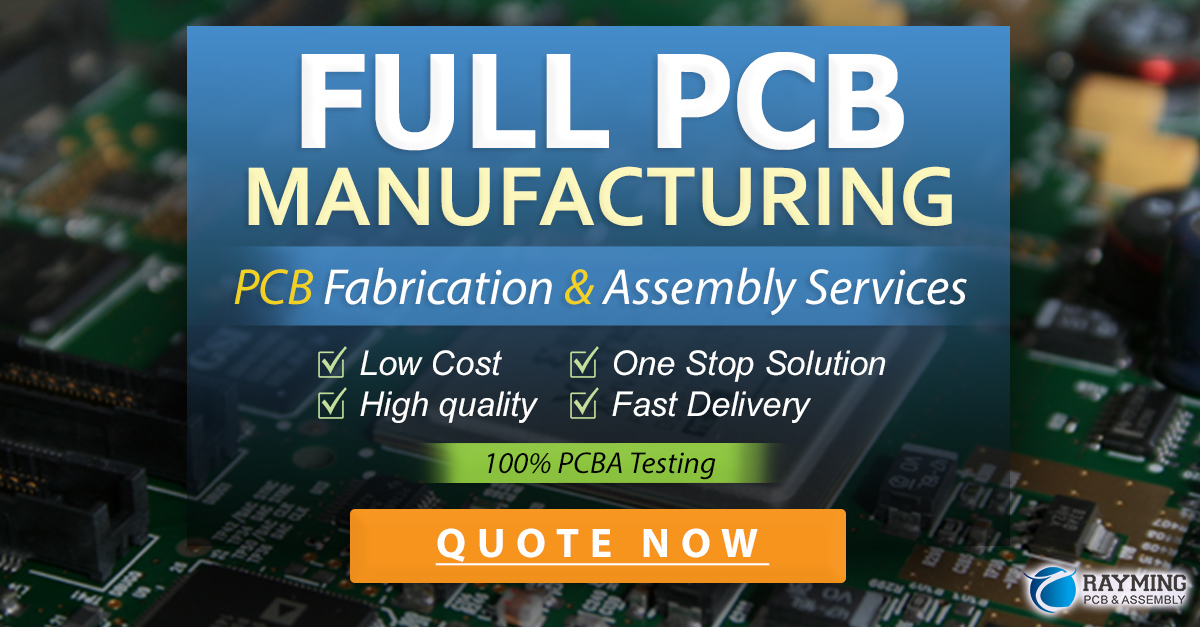
PCBA Process
The PCBA process involves several stages, each with its own set of procedures, equipment, and quality control measures. The main steps in the PCBA process are:
1. PCB Design and Fabrication
The first step in the PCBA process is the design and fabrication of the PCB itself. This involves creating a schematic diagram and a layout of the circuit, specifying the components, connections, and dimensions of the board. The design is then used to fabricate the PCB, typically using a combination of photolithography, etching, and plating processes.
2. Solder Paste Application
Once the PCB is fabricated, the next step is to apply solder paste to the pads and contact points where the components will be placed. Solder paste is a mixture of tiny solder particles and flux, which helps to clean and protect the metal surfaces during the soldering process. The solder paste is typically applied using a stencil printing machine, which ensures precise and consistent deposition of the paste onto the PCB.
3. Component Placement
After the solder paste is applied, the electronic components are placed onto the PCB using automated pick-and-place machines. These machines use vision systems and robotic arms to accurately position the components according to the PCB layout. The components are typically supplied on reels or trays, and the machine picks them up using vacuum nozzles and places them onto the solder paste.
4. Reflow Soldering
Once the components are placed, the PCB undergoes a reflow soldering process, where it is heated in a controlled manner to melt the solder paste and form permanent electrical and mechanical connections between the components and the PCB. The reflow soldering process typically involves passing the PCB through a conveyor oven with multiple temperature zones, each designed to gradually heat and cool the board to prevent thermal stress and damage.
5. Inspection and Testing
After the reflow soldering process, the PCBA undergoes various inspection and testing procedures to ensure its quality, functionality, and reliability. These may include:
- Visual inspection, using human operators or automated optical inspection (AOI) systems to check for missing, misaligned, or damaged components, as well as solder defects such as bridges, voids, or insufficient fillets.
- X-ray inspection, using X-ray imaging to detect hidden defects or anomalies, such as voids, cracks, or shorts, especially in high-density or multi-layer boards.
- In-circuit testing (ICT), using a bed-of-nails fixture to make electrical contact with the board and test the connectivity, resistance, capacitance, and other parameters of each component and net.
- Functional testing, using specialized equipment to simulate the operating conditions and inputs/outputs of the PCBA, and verify its performance and compliance with the specifications.
6. Rework and Repair
If any defects or issues are found during the inspection and testing stages, the PCBA may need to undergo rework or repair processes to correct them. This may involve removing and replacing defective components, adding or modifying solder joints, or modifying the PCB itself. Rework and repair require skilled operators and specialized equipment, such as soldering irons, hot air stations, and microscopes, to ensure precise and reliable modifications.
7. Conformal Coating and Potting
Depending on the application and environment of the PCBA, it may require additional protection against moisture, dust, chemicals, or other contaminants. Conformal coating and potting are two common methods used to provide this protection:
- Conformal coating involves applying a thin layer of a polymer material, such as acrylic, silicone, or urethane, over the surface of the PCBA, covering the components and connections while allowing for heat dissipation and electrical insulation.
- Potting involves encapsulating the PCBA or specific components in a thick layer of a resin or epoxy material, providing a more robust and rigid protection against mechanical stress and environmental factors.
8. Final Assembly and Packaging
Once the PCBA is complete and tested, it is ready for final assembly and packaging. This may involve integrating the PCBA into a larger system or device, such as a chassis, housing, or enclosure, and connecting it to other components, such as displays, buttons, or cables. The final product is then packaged and labeled according to the customer’s specifications and shipping requirements.
PCBA Quality Standards and Certifications
To ensure the quality, reliability, and safety of PCBA products, there are various industry standards and certifications that manufacturers and suppliers must adhere to. Some of the most common standards and certifications include:
- IPC (Association Connecting Electronics Industries) standards, such as IPC-A-610 for acceptability of electronic assemblies, IPC-J-STD-001 for soldered electrical and electronic assemblies, and IPC-7711/7721 for rework, modification, and repair of electronic assemblies.
- ISO (International Organization for Standardization) standards, such as ISO 9001 for quality management systems, ISO 14001 for environmental management systems, and ISO 13485 for medical device quality management systems.
- UL (Underwriters Laboratories) certifications, such as UL 94 for flammability of plastic materials, UL 796 for printed wiring boards, and UL 60950 for information technology equipment safety.
- RoHS (Restriction of Hazardous Substances) directive, which restricts the use of certain hazardous substances, such as lead, mercury, and cadmium, in electronic and electrical products.
- REACH (Registration, Evaluation, Authorization, and Restriction of Chemicals) regulation, which requires manufacturers and importers to register and assess the risks of chemical substances used in their products.
By complying with these standards and certifications, PCBA manufacturers and suppliers can demonstrate their commitment to quality, safety, and sustainability, and meet the requirements and expectations of their customers and end-users.
FAQ
1. What is the difference between PCB and PCBA?
A PCB (Printed Circuit Board) is the bare board without any electronic components assembled on it, while PCBA (Printed Circuit Board Assembly) refers to the complete board with all the components soldered and assembled onto it, ready for use in an electronic device.
2. What are the advantages of using PCBA in electronic devices?
PCBA offers several advantages in electronic devices, including:
- Miniaturization and high component density, enabling smaller and more compact devices
- Automated and standardized manufacturing processes, ensuring consistency and reliability
- Faster assembly speeds and lower costs compared to manual or through-hole assembly
- Improved electrical performance and signal integrity, thanks to shorter connections and reduced parasitic effects
- Flexibility and customization options, allowing for different components, layouts, and features to meet specific design requirements
3. What are the main challenges in PCBA Manufacturing?
Some of the main challenges in PCBA manufacturing include:
- Ensuring proper design and layout of the PCB, considering factors such as component placement, routing, and signal integrity
- Maintaining precise and consistent solder paste application, component placement, and soldering processes, to avoid defects and failures
- Implementing effective inspection and testing methods, to detect and correct any quality issues or anomalies
- Managing the supply chain and inventory of components, materials, and equipment, to avoid shortages or delays
- Keeping up with the latest industry standards, regulations, and technologies, to ensure compliance and competitiveness
4. How can I choose the right PCBA supplier for my project?
When choosing a PCBA supplier for your project, consider the following factors:
- Technical capabilities and experience, including the types of PCBA, components, and processes they can handle
- Quality management and certifications, such as IPC, ISO, and UL standards
- Production capacity and lead times, to ensure they can meet your volume and schedule requirements
- Communication and support, including responsiveness, documentation, and problem-solving skills
- Cost and value, considering not only the price but also the quality, reliability, and long-term benefits of the supplier’s services
5. What are the future trends and opportunities in PCBA?
Some of the future trends and opportunities in PCBA include:
- Adoption of advanced technologies, such as 3D printing, embedded components, and flexible or stretchable circuits, to enable new applications and form factors
- Integration of smart and connected features, such as sensors, wireless modules, and power management, to support the growth of IoT (Internet of Things) and Industry 4.0
- Emphasis on sustainability and circular economy, through the use of eco-friendly materials, design for recyclability, and responsible sourcing and disposal practices
- Collaboration and co-design between PCBA suppliers and customers, to optimize the design, manufacturing, and supply chain processes and achieve better outcomes and innovations.
Conclusion
PCBA is a critical process in the manufacturing of electronic devices, enabling the assembly of complex circuits and components onto a printed circuit board. By understanding the types, applications, and process of PCBA, as well as the quality standards and certifications involved, designers, engineers, and managers can make informed decisions and achieve better results in their projects.
As the electronics industry continues to evolve and innovate, PCBA will play an increasingly important role in enabling new technologies, applications, and business models. By staying up-to-date with the latest trends, challenges, and opportunities in PCBA, companies can position themselves for success and growth in this dynamic and competitive market.
Leave a Reply