What is an Automotive PCB?
An automotive PCB is a specially designed printed circuit board that is used in vehicles to interconnect and support various electronic components. These PCBs are responsible for controlling and managing a wide range of functions, including engine management, infotainment systems, safety features, and more. Unlike regular PCBs, automotive PCBs are designed to withstand the harsh environmental conditions encountered in vehicles, such as extreme temperatures, vibrations, and moisture.
Types of Automotive PCBs
There are several types of automotive PCBs, each designed for specific applications within a vehicle. Some of the most common types include:
- Engine Control Unit (ECU) PCBs
- Infotainment System PCBs
- Body Control Module (BCM) PCBs
- Transmission Control Unit (TCU) PCBs
- Advanced Driver Assistance Systems (ADAS) PCBs
PCB Type | Function |
---|---|
ECU PCB | Controls the engine’s performance, fuel injection, and emissions |
Infotainment System PCB | Manages the vehicle’s audio, video, and navigation systems |
BCM PCB | Controls various body functions, such as lighting, power windows, and locks |
TCU PCB | Regulates the vehicle’s transmission system |
ADAS PCB | Enables advanced safety features, such as lane departure warnings and adaptive cruise control |
Importance of Automotive PCBs
Automotive PCBs play a crucial role in ensuring the reliability, safety, and performance of modern vehicles. Some of the key reasons why automotive PCBs are so important include:
1. Reliability
Automotive PCBs are designed to withstand the rigors of the vehicle environment, ensuring that electronic systems remain functional and reliable even under extreme conditions. This is achieved through the use of high-quality materials, robust design techniques, and stringent testing procedures.
2. Safety
Many of the critical safety features in modern vehicles, such as anti-lock braking systems (ABS), electronic stability control (ESC), and airbag deployment, rely on automotive PCBs to function properly. The failure of these PCBs could potentially lead to serious accidents, making their reliability and performance paramount.
3. Performance
Automotive PCBs play a significant role in optimizing vehicle performance by controlling various aspects of the engine, transmission, and other systems. By ensuring that these components work together seamlessly, automotive PCBs help to improve fuel efficiency, reduce emissions, and enhance the overall driving experience.
Design Considerations for Automotive PCBs
Designing automotive PCBs is a complex process that requires careful consideration of various factors to ensure optimal performance and reliability. Some of the key design considerations include:
1. Environmental Factors
Automotive PCBs must be designed to withstand a wide range of environmental conditions, including:
- Temperature extremes (-40°C to +125°C)
- Humidity and moisture
- Vibration and shock
- Electromagnetic interference (EMI)
To address these challenges, automotive PCBs are typically manufactured using high-quality materials, such as FR-4 or polyimide, and are coated with conformal coatings to protect against moisture and corrosion.
2. Space Constraints
Vehicles have limited space for electronic components, which means that automotive PCBs must be designed to be as compact as possible while still maintaining their functionality. This often involves the use of high-density interconnect (HDI) PCBs, which allow for more components to be placed on a smaller board area.
3. Power Management
Automotive PCBs must be designed to efficiently manage power distribution and consumption, as vehicles have limited power resources. This involves the use of specialized components, such as voltage regulators and power management ICs, to ensure that each component receives the appropriate amount of power.
4. Signal Integrity
Ensuring signal integrity is crucial in automotive PCBs, as even small disturbances can lead to system malfunctions. Designers must carefully consider factors such as trace routing, impedance matching, and cross-talk mitigation to maintain signal integrity throughout the PCB.
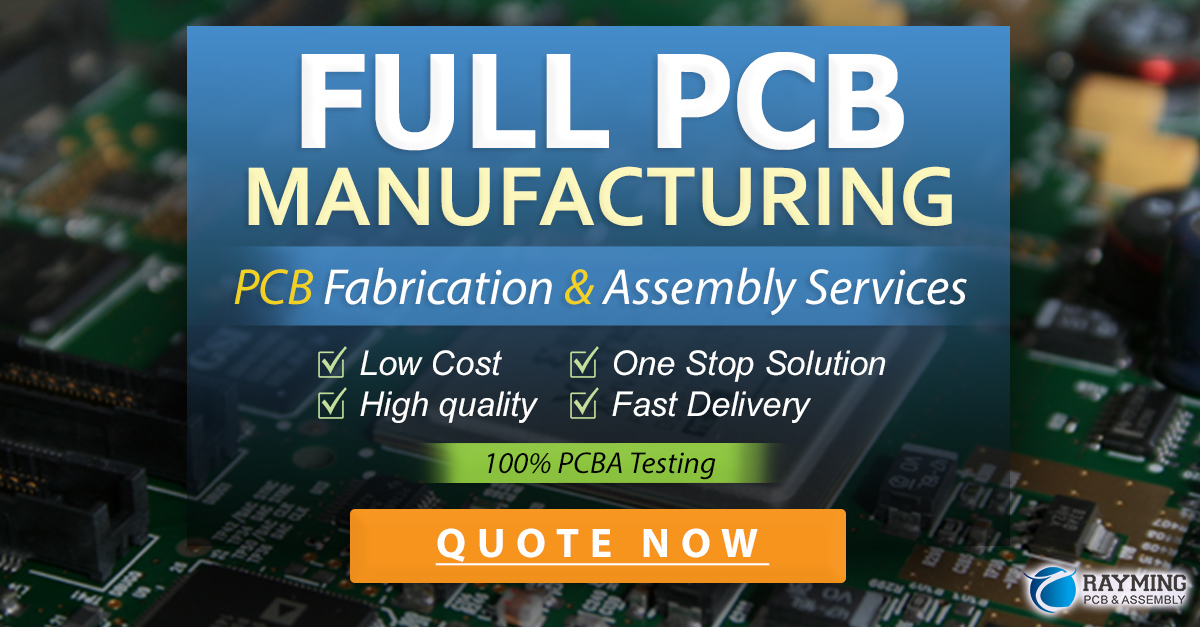
Manufacturing Process for Automotive PCBs
The manufacturing process for automotive PCBs is more stringent than that of regular PCBs due to the high reliability and performance requirements. The process typically involves the following steps:
-
Design and Layout: The PCB design is created using specialized software, taking into account all the design considerations mentioned earlier.
-
Material Selection: High-quality materials, such as FR-4 or polyimide, are chosen based on the specific requirements of the application.
-
Fabrication: The PCB is fabricated using a multi-step process that includes etching, drilling, and plating.
-
Component Assembly: The electronic components are mounted onto the PCB using automated pick-and-place machines and soldered in place.
-
Testing and Inspection: Rigorous testing and inspection procedures are carried out to ensure that the PCB meets all the required specifications and standards.
-
Conformal Coating: A protective coating is applied to the PCB to shield it from moisture, dust, and other environmental factors.
Future Trends in Automotive PCBs
As vehicles become increasingly advanced and autonomous, the role of automotive PCBs is set to become even more critical. Some of the future trends in automotive PCBs include:
1. Miniaturization
The demand for smaller, more compact PCBs will continue to grow as vehicles incorporate more electronic features and functions. This will drive the adoption of advanced manufacturing techniques, such as 3D printing and embedded components.
2. Increased Functionality
Automotive PCBs will need to support an ever-growing range of functions, from advanced driver assistance systems (ADAS) to infotainment and connectivity features. This will require the development of more sophisticated PCB designs and the integration of new technologies, such as 5G and artificial intelligence.
3. Sustainability
As environmental concerns continue to shape the automotive industry, there will be a growing focus on developing more sustainable and eco-friendly automotive PCBs. This may involve the use of biodegradable materials, the adoption of lead-free manufacturing processes, and the implementation of recycling and disposal programs.
Frequently Asked Questions (FAQ)
-
Q: What is the difference between an automotive PCB and a regular PCB?
A: Automotive PCBs are designed to withstand the harsh environmental conditions found in vehicles, such as extreme temperatures, vibrations, and moisture. They also have higher reliability and performance requirements compared to regular PCBs. -
Q: What are the most common materials used in automotive PCBs?
A: The most common materials used in automotive PCBs are FR-4 and polyimide. These materials are chosen for their high-quality and ability to withstand the rigors of the vehicle environment. -
Q: How are automotive PCBs tested to ensure reliability?
A: Automotive PCBs undergo rigorous testing and inspection procedures to ensure that they meet all the required specifications and standards. This may include environmental testing, functional testing, and reliability testing. -
Q: What is the role of conformal coating in automotive PCBs?
A: Conformal coating is a protective coating applied to automotive PCBs to shield them from moisture, dust, and other environmental factors. This helps to ensure the long-term reliability and performance of the PCB. -
Q: What are some of the future trends in automotive PCBs?
A: Some of the future trends in automotive PCBs include miniaturization, increased functionality, and sustainability. As vehicles become more advanced and autonomous, automotive PCBs will need to support a growing range of functions while becoming smaller and more eco-friendly.
In conclusion, automotive PCBs are a critical component in modern vehicles, enabling the smooth functioning of various electrical and electronic systems. By understanding the importance of automotive PCBs, their design considerations, manufacturing processes, and future trends, we can appreciate the crucial role they play in ensuring the reliability, safety, and performance of the vehicles we rely on every day.
Leave a Reply