What is an Automotive PCB?
An automotive PCB is a specialized printed circuit board designed to withstand the harsh environmental conditions and stringent reliability requirements of the automotive industry. These PCBs are found in various electronic systems within a vehicle, such as engine control units (ECUs), infotainment systems, advanced driver assistance systems (ADAS), and more.
Key Characteristics of Automotive PCBs
Automotive PCBs possess unique characteristics that differentiate them from standard PCBs:
- Robustness: Automotive PCBs are designed to withstand extreme temperatures, vibrations, and shock loads.
- Reliability: These PCBs must maintain their performance over the vehicle’s lifetime, often spanning several years.
- Safety: Automotive PCBs are critical for ensuring the safe operation of various vehicle systems, making their reliability paramount.
- Miniaturization: With the increasing complexity of automotive electronics, PCBs need to be compact and space-efficient.
Automotive PCB Design Considerations
Designing an automotive PCB requires careful consideration of several factors to ensure optimal performance and reliability.
Material Selection
The choice of PCB material is crucial for automotive applications. Some commonly used materials include:
Material | Characteristics | Applications |
---|---|---|
FR-4 | Cost-effective, good mechanical and electrical properties | General-purpose automotive electronics |
Polyimide | High temperature resistance, flexibility | High-temperature applications, flexible circuits |
Ceramic | Excellent thermal conductivity, high dielectric strength | High-power applications, LED lighting |
Thermal Management
Automotive PCBs must be designed to dissipate heat effectively to prevent component failure due to thermal stress. Techniques such as thermal vias, copper pours, and heat sinks are employed to improve thermal management.
Electromagnetic Compatibility (EMC)
Ensuring electromagnetic compatibility is crucial in automotive PCBs to prevent interference with other electronic systems. Proper grounding, shielding, and layout techniques are used to minimize electromagnetic interference (EMI) and ensure compliance with EMC standards.
Automotive-Specific Standards
Automotive PCBs must comply with various industry standards to ensure safety and reliability:
- ISO 26262: Functional safety standard for automotive electronics.
- AEC-Q100: Qualification standard for automotive-grade integrated circuits.
- J-STD-020: Joint standard for moisture/reflow sensitivity classification.
Manufacturing Processes for Automotive PCBs
The manufacturing process for automotive PCBs involves several critical steps to ensure high quality and reliability.
PCB Fabrication
The PCB fabrication process includes:
- Etching: Creating conductive traces on the PCB substrate using photolithography and chemical etching.
- Lamination: Bonding multiple layers of the PCB together using heat and pressure.
- Drilling: Creating holes for component mounting and vias for inter-layer connections.
- Plating: Applying conductive coatings to the holes and traces to improve electrical connectivity.
Component Assembly
After PCB fabrication, electronic components are assembled onto the board using one of two methods:
- Through-Hole Assembly (THA): Components with leads are inserted into holes drilled in the PCB and soldered.
- Surface Mount Assembly (SMA): Components are placed directly onto the surface of the PCB and soldered using reflow or wave soldering techniques.
Quality Control and Testing
Stringent quality control and testing procedures are employed throughout the manufacturing process to ensure the reliability of automotive PCBs:
- Automated Optical Inspection (AOI): Visual inspection of PCBs using high-resolution cameras and image processing software.
- X-Ray Inspection: Non-destructive inspection of solder joints and internal layers of the PCB.
- In-Circuit Testing (ICT): Electrical testing of individual components and circuits on the PCB.
- Functional Testing: Verification of the PCB’s overall functionality and performance.
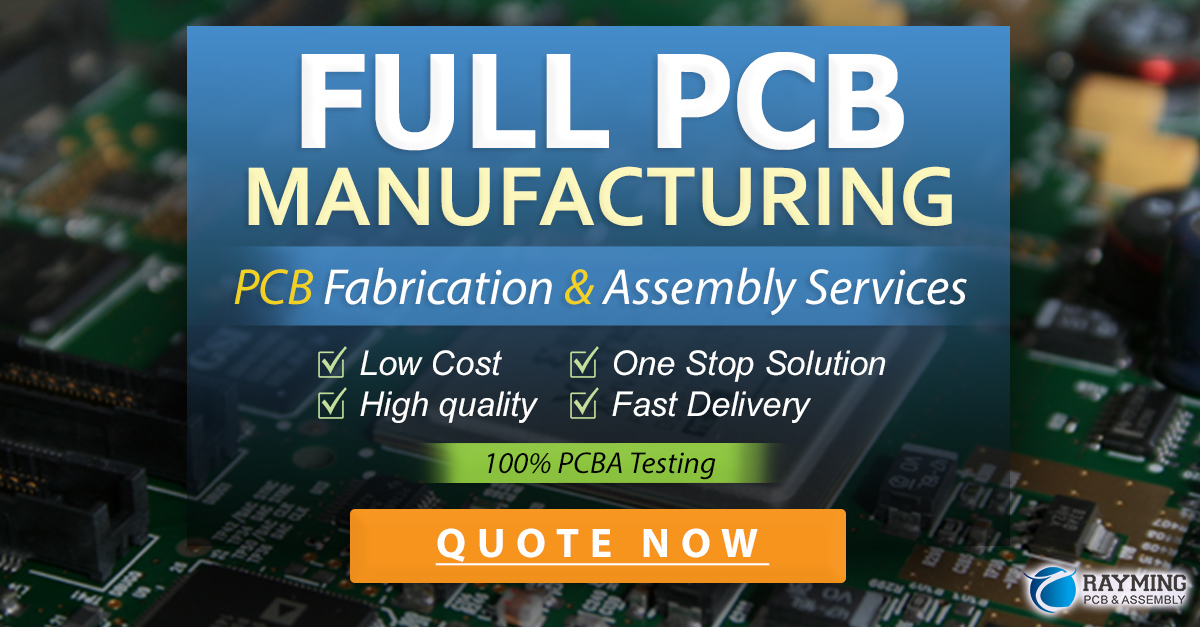
Applications of Automotive PCBs
Automotive PCBs find applications in various electronic systems within a vehicle:
Engine Control Unit (ECU)
The ECU is responsible for managing the engine’s performance and efficiency. Automotive PCBs in ECUs handle tasks such as:
- Fuel injection control
- Ignition timing
- Emission control
- Throttle position sensing
Infotainment Systems
Modern vehicles feature advanced infotainment systems that provide audio, video, and navigation functionalities. PCBs in these systems handle:
- Audio and video processing
- Touch screen interfaces
- Wireless connectivity (Bluetooth, Wi-Fi)
- GPS navigation
Advanced Driver Assistance Systems (ADAS)
ADAS employ sensors and cameras to enhance vehicle safety and provide features such as:
- Lane departure warning
- Adaptive cruise control
- Automatic emergency braking
- Parking assistance
Automotive PCBs in ADAS process sensor data and make real-time decisions to ensure safe vehicle operation.
Frequently Asked Questions (FAQ)
-
Q: What is the difference between automotive PCBs and standard PCBs?
A: Automotive PCBs are designed to withstand harsh environmental conditions and meet stringent reliability requirements specific to the automotive industry. They are more robust, reliable, and safety-critical compared to standard PCBs. -
Q: What materials are commonly used for automotive PCBs?
A: Common materials for automotive PCBs include FR-4, polyimide, and ceramic. The choice of material depends on the specific application and requirements, such as temperature resistance, flexibility, or thermal conductivity. -
Q: Why is thermal management important in automotive PCB design?
A: Automotive PCBs are subject to extreme temperature variations and high-power loads, making thermal management crucial to prevent component failure due to thermal stress. Proper thermal management ensures reliable operation and extends the lifespan of the PCB. -
Q: What industry standards do automotive PCBs need to comply with?
A: Automotive PCBs must comply with various industry standards, including ISO 26262 for functional safety, AEC-Q100 for automotive-grade integrated circuits, and J-STD-020 for moisture/reflow sensitivity classification. -
Q: How are automotive PCBs tested for quality and reliability?
A: Automotive PCBs undergo rigorous testing throughout the manufacturing process, including automated optical inspection (AOI), X-ray inspection, in-circuit testing (ICT), and functional testing. These tests ensure the PCBs meet the required quality and reliability standards.
Conclusion
Automotive PCBs are essential components in the complex electronic systems found in modern vehicles. Their design, manufacturing, and testing processes are tailored to meet the unique challenges and requirements of the automotive industry. By understanding the intricacies of automotive PCBs, engineers and manufacturers can develop reliable and safe electronic systems that enhance vehicle performance, efficiency, and user experience. As the automotive industry continues to evolve with the advent of electric vehicles and autonomous driving technologies, the importance of automotive PCBs will only continue to grow.
[Word count: 1055]
Leave a Reply