Introduction to Via Fill in PCB Design
In the world of printed circuit board (PCB) design, vias play a crucial role in connecting different layers of the board. Vias are essentially small holes drilled through the PCB that allow electrical connections to be made between different layers. There are two main types of via fill: conductive and non-conductive. In this article, we will explore the differences between these two types of via fill and their applications in PCB design.
What is Via Fill?
Via fill is the process of filling the drilled holes in a PCB with a material, either conductive or non-conductive. The purpose of via fill is to provide a reliable electrical connection between layers, improve thermal conductivity, and enhance the mechanical strength of the board.
Types of Via Fill
- Conductive Via Fill
- Copper
- Silver
- Gold
- Non-Conductive Via Fill
- Epoxy
- Resin
Conductive Via Fill
Conductive via fill involves filling the drilled holes with a conductive material, typically copper, silver, or gold. This type of via fill is used when electrical connectivity between layers is required.
Copper Via Fill
Copper is the most common material used for conductive via fill. The process involves electroplating copper into the drilled holes to create a solid connection between layers. Copper via fill offers several advantages:
- Excellent electrical conductivity
- Good thermal conductivity
- Cost-effective compared to other conductive materials
Copper Via Fill Process
- Drilling: Holes are drilled through the PCB at designated locations.
- Desmear: The drilled holes are cleaned to remove any debris and improve adhesion.
- Electroless Copper Deposition: A thin layer of copper is deposited onto the walls of the holes.
- Electroplating: Copper is electroplated into the holes to create a solid connection.
- Planarization: The surface of the PCB is flattened to remove any excess copper.
Silver Via Fill
Silver via fill is another option for conductive via fill. Although less common than copper, silver offers some unique advantages:
- Higher electrical conductivity than copper
- Excellent thermal conductivity
- Resistance to oxidation and corrosion
However, silver via fill is more expensive than copper and is typically used in high-performance applications where the added cost is justified.
Gold Via Fill
Gold via fill is the least common of the conductive via fill materials. It offers the highest level of electrical conductivity and resistance to oxidation and corrosion. However, gold via fill is also the most expensive option and is reserved for specialized applications where performance is critical.
Non-Conductive Via Fill
Non-conductive via fill involves filling the drilled holes with a non-conductive material, typically epoxy or resin. This type of via fill is used when electrical isolation between layers is required.
Epoxy Via Fill
Epoxy via fill is a popular choice for non-conductive via fill. The process involves filling the drilled holes with a liquid epoxy that hardens to create a solid, non-conductive plug. Epoxy via fill offers several advantages:
- Excellent electrical isolation
- Good mechanical strength
- Resistance to moisture and chemicals
Epoxy Via Fill Process
- Drilling: Holes are drilled through the PCB at designated locations.
- Desmear: The drilled holes are cleaned to remove any debris and improve adhesion.
- Epoxy Filling: Liquid epoxy is dispensed into the holes.
- Curing: The epoxy is cured using heat to create a solid, non-conductive plug.
- Planarization: The surface of the PCB is flattened to remove any excess epoxy.
Resin Via Fill
Resin via fill is another option for non-conductive via fill. Similar to epoxy, resin is dispensed into the drilled holes and cured to create a solid, non-conductive plug. Resin via fill offers similar advantages to epoxy, including excellent electrical isolation and good mechanical strength.
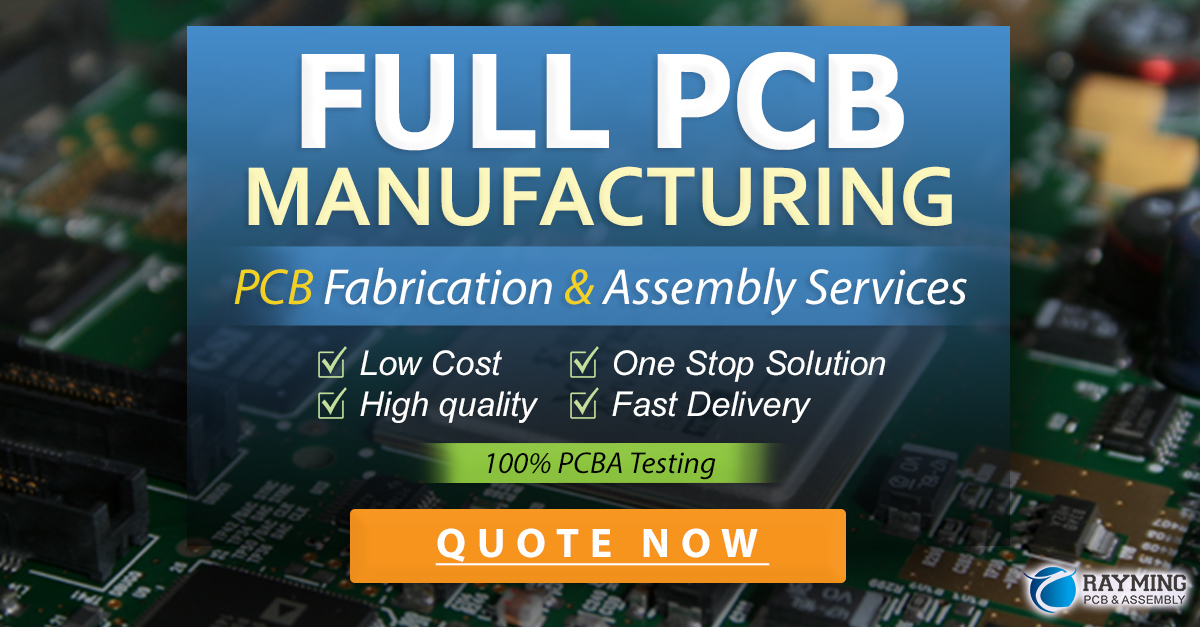
Applications of Via Fill in PCB Design
Via fill, both conductive and non-conductive, has numerous applications in PCB design. Some common applications include:
High-Density Interconnect (HDI) PCBs
HDI PCBs are characterized by their high component density and fine pitch features. Conductive via fill, particularly copper, is essential in HDI designs to ensure reliable electrical connections between layers.
Thermal Management
Conductive via fill can be used to improve the thermal conductivity of a PCB. By filling vias with a conductive material, heat can be efficiently dissipated from components to other layers or heat sinks.
Impedance Control
In high-speed PCB designs, impedance control is critical to maintain signal integrity. Non-conductive via fill can be used to control the impedance of vias by isolating them from surrounding conductive layers.
Mechanical Strength
Both conductive and non-conductive via fill can improve the mechanical strength of a PCB. Filled vias act as small support columns, enhancing the rigidity and durability of the board.
Choosing the Right Via Fill
Choosing the right type of via fill depends on the specific requirements of the PCB design. Factors to consider include:
- Electrical requirements (conductivity vs. isolation)
- Thermal management needs
- Mechanical strength requirements
- Cost constraints
The following table provides a comparison of the different via fill materials:
Material | Conductivity | Thermal Conductivity | Cost |
---|---|---|---|
Copper | High | Good | Low |
Silver | Very High | Excellent | High |
Gold | Highest | Excellent | Very High |
Epoxy | Non-conductive | Poor | Low |
Resin | Non-conductive | Poor | Low |
Frequently Asked Questions (FAQ)
-
Q: What is the difference between conductive and non-conductive via fill?
A: Conductive via fill uses conductive materials (copper, silver, gold) to provide electrical connectivity between layers, while non-conductive via fill uses non-conductive materials (epoxy, resin) to provide electrical isolation. -
Q: When should I use conductive via fill?
A: Conductive via fill should be used when electrical connectivity between layers is required, such as in HDI designs or for thermal management purposes. -
Q: When should I use non-conductive via fill?
A: Non-conductive via fill should be used when electrical isolation between layers is required, such as for impedance control or to prevent signal interference. -
Q: Can via fill improve the mechanical strength of a PCB?
A: Yes, both conductive and non-conductive via fill can improve the mechanical strength of a PCB by acting as small support columns. -
Q: What factors should I consider when choosing a via fill material?
A: Factors to consider when choosing a via fill material include electrical requirements, thermal management needs, mechanical strength requirements, and cost constraints.
Conclusion
Via fill is a critical aspect of PCB design, providing reliable electrical connections, thermal management, and mechanical strength. Understanding the differences between conductive and non-conductive via fill, as well as their applications, is essential for designing high-quality PCBs.
By carefully considering the specific requirements of a PCB design and choosing the appropriate via fill material, designers can ensure optimal performance, reliability, and cost-effectiveness. As PCB technology continues to advance, the importance of via fill will only continue to grow, making it a crucial skill for any PCB designer to master.
Leave a Reply