Selecting the right flexible PCB supplier is crucial for getting high-quality flexible printed circuit boards (flex PCBs) for your products. This comprehensive guide covers the key factors to consider when choosing a flex PCB supplier.
Flexible PCB Basics
What is a Flexible PCB?
A flexible PCB, also known as flex PCB, is a printed circuit board made of flexible insulating substrate material rather than rigid FR-4 material. The flexible substrate allows the PCB to bend and flex without damage to the copper traces.
Flex PCBs have several advantages:
- Can flex and bend to fit mechanically challenging spaces
- Highly customizable with flexible thickness and bend radii
- Lightweight and durable
- Cost-effective for lower complexity designs
Common applications of flex PCBs include wearables, medical devices, consumer electronics, automotive electronics, IoT devices, and aerospace products.
Flexible PCB Construction
A basic flex PCB comprises the following layers:
- Base Material: Polyimide (Kapton) film is most commonly used due to its excellent thermal, mechanical, and electrical properties. Other base materials include PEEK and PET. Base thickness ranges from 25-150 μm.
- Conductive Layer: Copper foil, typically 18-35 μm thick, laminated to the base film.
- Coverlay: A thin polyimide layer that covers and insulates the copper traces.
- Stiffener: Optional FR-4 material laminated on select areas to provide rigidity and mounting support.
- Cover Coat: A solder mask covering over bare copper for electrical insulation.
- Legend: Silkscreened symbols, lines, and text markings for assembly and wiring.
Flex PCB vs Rigid PCBs
The main differences between flex PCBs and rigid PCBs are:
- Substrate material: Flex PCBs use a thin flexible polymer material. Rigid PCBs use rigid FR-4 laminate.
- Flexibility: Flex PCBs can bend and twist. Rigid PCBs cannot flex.
- Density: Flex PCB traces can be very tightly spaced. Rigid PCBs have lower trace density.
- Layers: Flex PCBs typically have 1-2 conductive layers. Rigid boards can have 8 or more layers.
- Cost: Simple flex PCBs have lower NRE costs and per unit costs. High-complexity rigid PCBs are costlier.
Key Factors in Selecting a Flex PCB Supplier
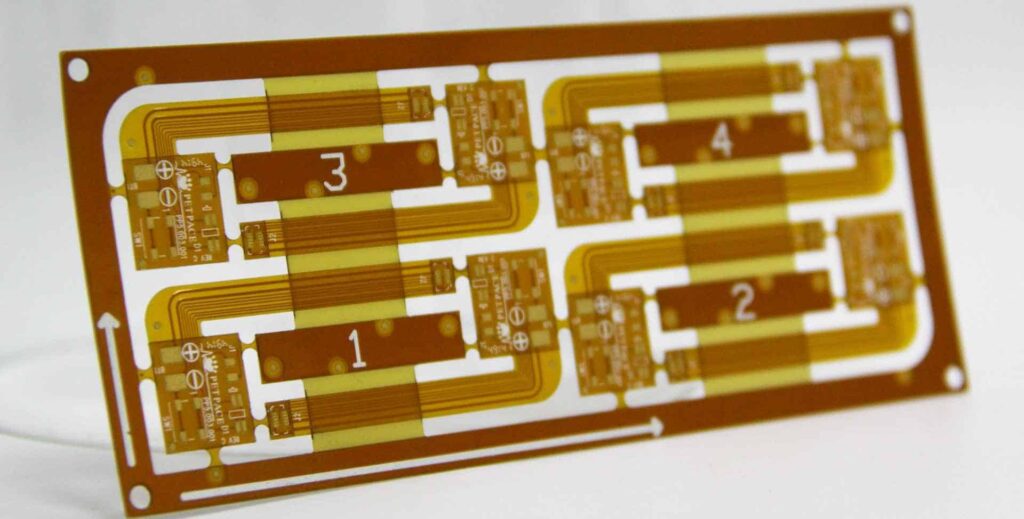
Choosing the right flex PCB supplier requires evaluating various supplier qualifications, capabilities, services, and costs. Here are the most important considerations:
1. Technical Capabilities
The flex PCB supplier should have the technical capabilities to manufacturer your particular type of flex boards. Key considerations:
- Minimum line/space: The smallest trace width and spacing between traces they can achieve. Important for high-density flex designs.
- Minimum bending radius: The smallest flex board bend radius they can fabricate reliably. Relevant for dynamic flexing applications.
- Layer count: Number of conductive layers (1-6 layers typically) they are capable of producing. More layers allow higher complexity.
- Stackups: Ability to fabricate different types of flex stackups e.g. rigid-flex.
- Materials: Variety of base materials (polyimide, PEEK, PET) and stiffeners they can use.
- Quality controls: Extensiveness of quality testing during fabrication.
Evaluate technical specs of your flex PCB design versus the supplier’s demonstrated capabilities.
2. Manufacturing Capacity
The supplier must have sufficient manufacturing capacity to produce the required volumes without excessive lead times. Things to confirm:
- Volume capabilities: Can they handle your expected order volumes per month/quarter? Get details on max volumes for different flex PCB sizes.
- On-time delivery: Historical percentage of on-time deliveries. 80%+ is good.
- Lead times: Typical lead times for flex PCB orders of your size and complexity. 4-6 weeks is common.
- Responsiveness: How quickly do they respond to quote requests and order inquiries? 1-2 days response time is good.
Ensure the supplier has a track record of consistently shipping quality boards on schedule in required quantities.
3. Quality Systems
Rigorous quality control is crucial for flex PCBs. Evaluate the supplier’s quality systems:
- Incoming inspection: Do they thoroughly inspect raw materials like base layers and copper foil before manufacturing?
- In-process inspection: Are quality checks done at each major fabrication step? e.g. lamination, imaging, etching, solder mask.
- AOI: Do they use automated optical inspection (AOI) and testing?
- Outgoing inspection: Is 100% inspection done on finished boards? This step is vital.
- Quality certifications: Do they have ISO 9001 and other certifications? This indicates compliant processes.
- Documentation: Will they provide full quality inspection reports and certifications for each order?
- Failure analysis: Do they thoroughly analyze defects to prevent recurrences when issues occur?
Choose a supplier who adheres to strict quality control standards at all manufacturing stages.
4. Design Support
The flex PCB supplier should provide design support to help optimize your board design for manufacturability and reliability:
- DFM analysis: They should review board designs and provide DFM recommendations when you submit Gerber files. This avoids issues during production.
- Flex PCB guidelines: Ask them to provide their design guideline documents covering flex-specific considerations like dynamic bending, rigid-flex transition zones, and copper thickness.
- Prototype support: Can they manufacture a small number of boards for initial testing before full production? This helps validate the design.
- Design tools: Do they provide useful design resources and tools? e.g. flex PCB stackup templates, minimum bend radius calculators, impedance calculators.
- Designer training: Will they train your team on best practices for designing flex PCBs? e.g. webinars, design guidelines.
Leverage the supplier’s expertise early in the design process to create optimized flex PCB designs.
5. Assembly Capabilities
Many suppliers offer in-house assembly of components on the flex PCBs:
- SMT assembly: Do they have SMT equipment suitable for small components and fine pitch devices often used on flex boards?
- Through-hole assembly: Can they manually assemble connectors and other through-hole components?
- Covers & shields: Do they install necessary covers, shields, and encapsulations?
- Testing: Is functional testing offered? This verifies boards work before shipment.
- Inventory: Do they stock common components for quick turnaround? Or will all components be procured only after order?
Choose a supplier offering high-quality flex PCB assembly if this meets your needs.
6. Certifications
Relevant quality and compliance certifications indicate a supplier’s commitment to proper standards and business continuity:
- ISO 9001: Certifies quality management system processes. ISO 13485 is ideal for medical devices.
- AS 9100: Aerospace quality management standards. Required for aviation/defense projects.
- ISO 14001: Certifies eco-friendly standards and environmental practices.
- ITAR: Registration helps when working on regulated defense projects.
- UL: Necessary for boards going into UL-listed end products.
Carefully verify certifications match your industry and application requirements.
7. Costs
Flex PCB costs include:
- NRE expenses: One-time non-recurring engineering fees for fabrication setup. Gets amortized over the volumes.
- Unit cost: Quoted cost per flex PCB, dependent on size, layer count, quantity, and lead time.
- Tooling costs: Any additional tools like custom test fixtures.
- Assembly costs: If using the supplier’s component assembly services.
- Shipping: Freight charges for shipping the boards.
Compare total costs between suppliers. Get detailed cost breakdowns to identify any hidden charges.
8. Customer Support
The supplier should provide responsive customer support:
- Technical support: Do they have engineers who can answer flex PCB design and fabrication questions?
- Project management: Will you have a dedicated account manager for order status updates and issue resolution?
- Communication: Are they responsive to calls and emails? 1 business day max response time.
- Language: Support available in your preferred language.
- Time zone: Local support during your standard business hours.
Good customer support ensures orders go smoothly and any production issues get addressed quickly.
Finding Flexible PCB Suppliers
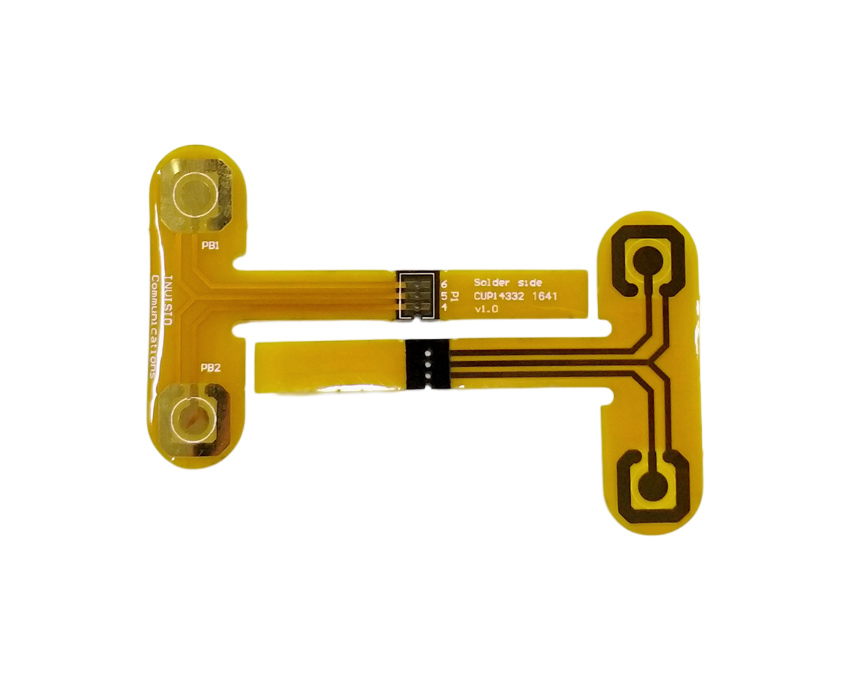
Use these resources to find reputable flex PCB suppliers to evaluate:
- Industry directories: Thomasnet, Kompass, and Electronics Sourcing provide searchable PCB supplier directories.
- Trade shows: Attending industry trade shows lets you network with suppliers and view product samples.
- Online searches: Search “flex PCB manufacturer [location]” to find suppliers in your region.
- Recommendations: Ask colleagues which flex PCB suppliers they use and trust.
- PCB forums: Participate in communities like PCBCart and Reddit’s /r/PrintedCircuitBoard/ to get supplier recommendations from experienced users.
Create a list of 5-10 suppliers to investigate further based on capabilities, services, and customer reviews.
Qualifying and Selecting the Supplier
Follow a process to qualify the potential suppliers and select the best match:
- Send design files to get functional quotes from each supplier.
- Review capabilities against your board requirements to screen out unqualified suppliers.
- Evaluate and rank suppliers based on factors like quality, certifications, costs, lead times, and customer support.
- Create a shortlist of the top 2-3 suppliers.
- Send sample orders to the shortlisted suppliers for quality verification.
- Select the top supplier based on test board quality, responsiveness, and ease of business.
Take time to properly evaluate suppliers rather than just choosing the cheapest option. This ensures you get a great long-term flex PCB manufacturing partner.
Flexible PCB Supplier Management
Once selected, actively manage the supplier relationship for ongoing success:
- Maintain frequent communication for visibility into order status.
- Provide detailed design and specification documentation.
- Work collaboratively when issues occur – avoid blame games.
- Give suppliers early forecasts of future demand.
- Provide suggestions for process and quality improvements.
- Request supplier scorecards with key metrics like quality, lead time, yields.
- Periodically reevaluate suppliers’ capabilities and services.
Proper supplier management reduces risks and ensures optimal collaboration.
Conclusion
Selecting the right flexible PCB supplier and managing the relationship effectively is key to getting high-performing, reliable flex boards for your products. Use the criteria and best practices covered in this guide to partner with a first-rate flex PCB manufacturer suited for your particular requirements and business needs. With the right supplier, your team can focus on designing innovative products rather than worrying about supply chain issues.
Frequently Asked Questions
What are some top flexible PCB manufacturers I should consider?
Some reputable global flexible PCB manufacturers include Multi-Fineline Electronix (MFLEX), Flexium, Compass Circuits, and Ray Ming. Regional suppliers can also offer great quality and service. Do your diligence to find the best match.
Should I select the supplier with the lowest price quote?
No, choosing only based on the lowest quoted cost can be risky. Thoroughly evaluate capabilities, quality systems, certifications, and customer reviews before selecting a supplier. Paying slightly more for better quality, yield, and service often pays off in the long run.
What are some red flags to watch out for when choosing a supplier?
Avoid suppliers that seem evasive about their capabilities, quality procedures, and business practices. Other red flags include lack of customer reviews, missing key certifications, very long lead times, and inability to provide sample boards for design verification.
How can I determine the expected costs for a flexible PCB order?
To determine overall costs, ask potential suppliers to provide a detailed quotation that breaks down NRE fees, unit costs based on volumes, tooling costs, applicable taxes and duties, and shipping. Get quotes from multiple suppliers to compare.
What design support should I expect from a flex PCB supplier?
At minimum, the supplier should offer DFM analysis on your designs and provide a flex PCB design guidelines document. Better support includes prototyping services, access to flex design tools, and design trainings. Taking advantage of these services will improve your design’s manufacturability.
Leave a Reply