SMT vs THT: A Quick Overview
Before we delve into the details, let’s take a quick look at the key differences between SMT and THT Mounting:
Characteristic | SMT | THT |
---|---|---|
Component placement | On the surface of the PCB | Through holes in the PCB |
Solder connection | Surface mount pads | Leads inserted through holes |
Component size | Smaller, more compact | Larger, more robust |
Assembly speed | Faster, automated | Slower, often manual |
PCB design complexity | Higher | Lower |
Rework and repair | More difficult | Easier |
Cost | Lower for high volumes | Higher, but cost-effective for low volumes |
Understanding Surface Mount Technology (SMT)
What is SMT?
Surface Mount Technology, or SMT, is a method of mounting electronic components directly onto the surface of a printed circuit board. In this process, the components are placed on designated pads or lands on the PCB, which are pre-printed with solder paste. The board then goes through a reflow oven, where the solder paste melts and forms a secure electrical and mechanical connection between the component and the PCB.
Advantages of SMT
-
Smaller components and higher density: SMT allows for the use of smaller components, which enables higher component density on the PCB. This is particularly important for modern electronics that require compact designs, such as smartphones, smartwatches, and other portable devices.
-
Faster assembly: SMT is highly automated, using pick-and-place machines to rapidly populate PCBs with components. This speeds up the assembly process, reducing lead times and increasing production efficiency.
-
Lower cost for high volumes: Due to the automated nature of SMT Assembly, it becomes more cost-effective as production volumes increase. The initial setup costs may be higher, but the cost per unit decreases significantly with larger quantities.
-
Improved performance: SMT components generally have shorter leads, which reduces parasitic inductance and capacitance. This results in improved high-frequency performance and reduced signal distortion.
Disadvantages of SMT
-
Higher initial setup costs: SMT assembly requires specialized equipment, such as pick-and-place machines, reflow ovens, and solder paste printers. This can lead to higher initial setup costs compared to THT.
-
More complex PCB design: Designing a PCB for SMT requires careful consideration of component placement, pad sizes, and solder mask openings. This increased complexity can lead to higher design costs and longer development times.
-
Difficult rework and repair: Due to the small size of SMT components and their close proximity to each other, rework and repair can be challenging. Specialized tools and skills are often required to replace or repair SMT components without damaging the PCB or nearby components.
Understanding Through-Hole Technology (THT)
What is THT?
Through-Hole Technology, or THT, is a method of mounting electronic components by inserting their leads through drilled holes in the PCB. The leads are then soldered to pads on the opposite side of the board, creating a strong mechanical and electrical connection. THT was the dominant method of PCB Assembly before the widespread adoption of SMT.
Advantages of THT
-
Stronger mechanical connection: THT components have leads that extend through the PCB, providing a stronger mechanical connection than SMT. This makes THT well-suited for applications that require high mechanical stress or vibration resistance.
-
Easier manual assembly: THT components are larger and easier to handle than their SMT counterparts, making manual assembly more straightforward. This can be advantageous for low-volume production or prototyping.
-
Simpler PCB design: Designing a PCB for THT is generally simpler than for SMT, as there are fewer constraints on component placement and hole sizes. This can lead to lower design costs and shorter development times.
-
Easier rework and repair: THT components are easier to replace or repair than SMT components, as they can be desoldered and removed without the need for specialized equipment.
Disadvantages of THT
-
Larger components and lower density: THT components are generally larger than their SMT equivalents, which limits the component density on the PCB. This can result in larger overall board sizes and reduced design flexibility.
-
Slower assembly: THT assembly is typically slower than SMT, as components need to be inserted manually or with the help of semi-automatic machines. This can lead to longer production times and increased labor costs.
-
Higher cost for high volumes: Due to the slower assembly process and increased labor requirements, THT becomes less cost-effective as production volumes increase. The cost per unit remains relatively constant, regardless of the quantity produced.
-
Limited high-frequency performance: THT components have longer leads, which can introduce higher parasitic inductance and capacitance. This can limit the high-frequency performance of THT assemblies compared to SMT.
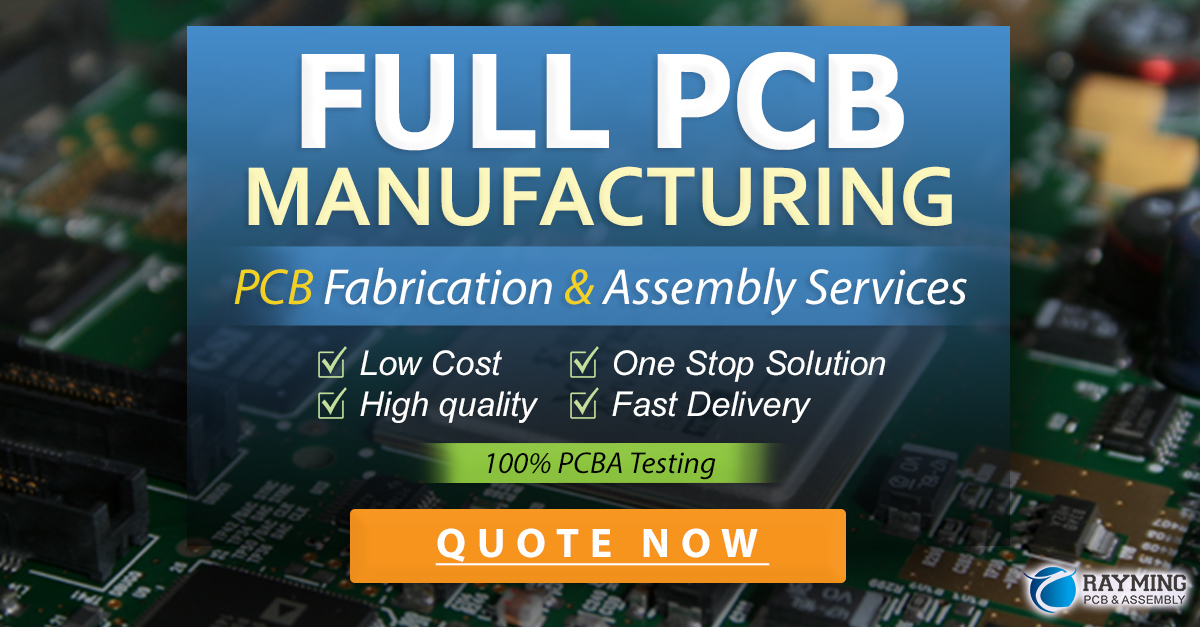
Choosing Between SMT and THT
When deciding between SMT and THT for your PCB assembly, consider the following factors:
-
Production volume: If you’re producing high volumes, SMT is likely to be more cost-effective due to its automated assembly process. For low volumes or prototypes, THT may be more suitable.
-
Component availability: Some components may only be available in SMT or THT packages, which can dictate the assembly method you choose.
-
PCB size and density: If you require a compact design with high component density, SMT is the better choice. THT is more suitable for larger PCBs with lower component counts.
-
Mechanical requirements: If your application demands high mechanical strength or vibration resistance, THT may be the preferred option due to its stronger mechanical connections.
-
High-frequency performance: For applications that require optimal high-frequency performance, SMT is generally the better choice due to its lower parasitic inductance and capacitance.
-
Rework and repair: If ease of rework and repair is a priority, THT may be more suitable, as it allows for easier component replacement without specialized equipment.
FAQ
1. Can SMT and THT be used together on the same PCB?
Yes, it is possible to use both SMT and THT components on the same PCB. This is called a mixed-technology or hybrid assembly. However, it’s essential to consider the assembly process and ensure that the PCB design accommodates both technologies.
2. Is SMT always better than THT?
No, SMT is not always better than THT. The choice between SMT and THT depends on various factors, such as production volume, component availability, mechanical requirements, and design constraints. Each technology has its own strengths and weaknesses, and the best choice will depend on the specific requirements of your project.
3. Can THT components be used in high-frequency applications?
While THT components can be used in high-frequency applications, they may not perform as well as SMT components. THT components have longer leads, which can introduce higher parasitic inductance and capacitance, potentially limiting high-frequency performance. For optimal high-frequency performance, SMT is generally the preferred choice.
4. Are there any components that are only available in THT packages?
Yes, some components, particularly those with high power requirements or specialized functions, may only be available in THT packages. Examples include certain power transistors, high-voltage capacitors, and some connectors. In these cases, THT may be the only option for PCB assembly.
5. Is it more expensive to design a PCB for SMT or THT?
Designing a PCB for SMT can be more complex and time-consuming than designing for THT, due to the smaller component sizes and more stringent layout requirements. This can lead to higher design costs for SMT. However, the overall cost-effectiveness of SMT or THT will depend on factors such as production volume, component availability, and assembly process efficiency.
Conclusion
In summary, Surface Mount Technology (SMT) and Through-Hole Technology (THT) are two distinct methods for mounting electronic components on printed circuit boards. SMT offers advantages such as smaller component sizes, higher density, faster assembly, and lower costs for high-volume production. THT, on the other hand, provides stronger mechanical connections, easier manual assembly, simpler PCB design, and more straightforward rework and repair.
When choosing between SMT and THT, it’s essential to consider factors such as production volume, component availability, PCB size and density, mechanical requirements, high-frequency performance, and ease of rework and repair. By understanding the strengths and weaknesses of each technology and carefully evaluating your project’s specific needs, you can make an informed decision that balances cost, performance, and manufacturing efficiency.
As electronics continue to evolve, both SMT and THT will likely remain relevant, with designers and manufacturers leveraging the strengths of each technology to create innovative and reliable products. By staying informed about the differences between SMT and THT and their respective applications, you’ll be well-equipped to make the best choice for your PCB assembly projects.
Leave a Reply