What is SMT Assembly?
SMT (Surface Mount Technology) assembly is a method used in the manufacture of electronic circuits where components are mounted directly onto the surface of printed circuit boards (PCBs). This technology has largely replaced the through-hole technology construction method of fitting components with wire leads into holes in the circuit board.
SMT assembly involves several key steps:
1. Solder paste application
2. Component placement
3. Reflow soldering
4. Inspection and testing
The main advantages of SMT assembly over through-hole technology include:
- Smaller components and higher component density
- Faster and more automated assembly
- Lower production costs
- Improved mechanical performance under shake and vibration conditions
The SMT Assembly Process
1. Solder Paste Application
The first step in SMT assembly is applying solder paste to the PCB. Solder paste is a mixture of tiny solder particles and flux, a chemical cleaning agent. The paste is applied to the PCB using a solder paste stencil, a thin sheet of stainless steel with laser-cut openings corresponding to the solder pad locations on the PCB.
The stencil is aligned with the PCB, and solder paste is spread over the stencil, filling the openings. When the stencil is removed, the solder paste remains on the PCB pads.
2. Component Placement
After solder paste application, the PCB moves to a pick-and-place machine for component placement. Modern machines use computer vision systems and precise robotics to pick up and accurately place components on the PCB at high speeds.
The components, supplied on reels or trays, are picked up by vacuum nozzles. The machine then rotates and precisely places the components onto their designated locations on the PCB, where they stick to the solder paste.
3. Reflow Soldering
Once all components are placed, the PCB goes through a reflow soldering process. The board passes through a reflow oven, which heats it to temperatures around 250°C, following a precise temperature profile.
The heat melts the solder particles in the paste, which then cools and solidifies, creating a permanent electrical and mechanical bond between the component leads and the PCB pads. The flux in the solder paste cleans the metal surfaces, preventing oxidation during the soldering process.
4. Inspection and Testing
After soldering, each PCB undergoes a rigorous inspection and testing process to ensure the quality and functionality of the assembled board. Several methods are used:
-
Visual Inspection: Manual or automated optical inspection to check for visible defects like misaligned components, solder bridges, or insufficient solder joints.
-
Automated Optical Inspection (AOI): High-resolution cameras compare the assembled PCB against a perfect reference, identifying any defects.
-
X-ray Inspection: Used to inspect solder joints hidden under components, like Ball Grid Arrays (BGAs).
-
In-Circuit Testing (ICT): Electrical tests verify the continuity and functionality of individual components and circuits on the board.
-
Functional Testing: The assembled board is powered on and tested in its end-use configuration to ensure it functions as intended.
Boards that pass inspection and testing are ready for integration into the final product, while defective boards are reworked or scrapped.
Advantages of SMT Assembly
SMT assembly offers several significant advantages over through-hole technology:
-
Smaller Size: SMT components are much smaller than through-hole components, allowing for more compact PCB designs with higher component density.
-
Lighter Weight: Without the need for wire leads, SMT components are lighter, reducing the overall weight of the assembled PCB.
-
Faster Assembly: Pick-and-place machines can place hundreds of SMT components per minute, much faster than the manual insertion of through-hole components.
-
Lower Cost: The automated nature of SMT assembly reduces labor costs. Additionally, SMT components are generally cheaper due to their smaller size and higher production volumes.
-
Improved Reliability: SMT components have shorter leads and are mounted closer to the PCB surface, reducing the risk of damage from vibration and physical stress.
-
Better High-Frequency Performance: The smaller size and lead lengths of SMT components reduce parasitic capacitance and inductance, improving high-frequency performance.
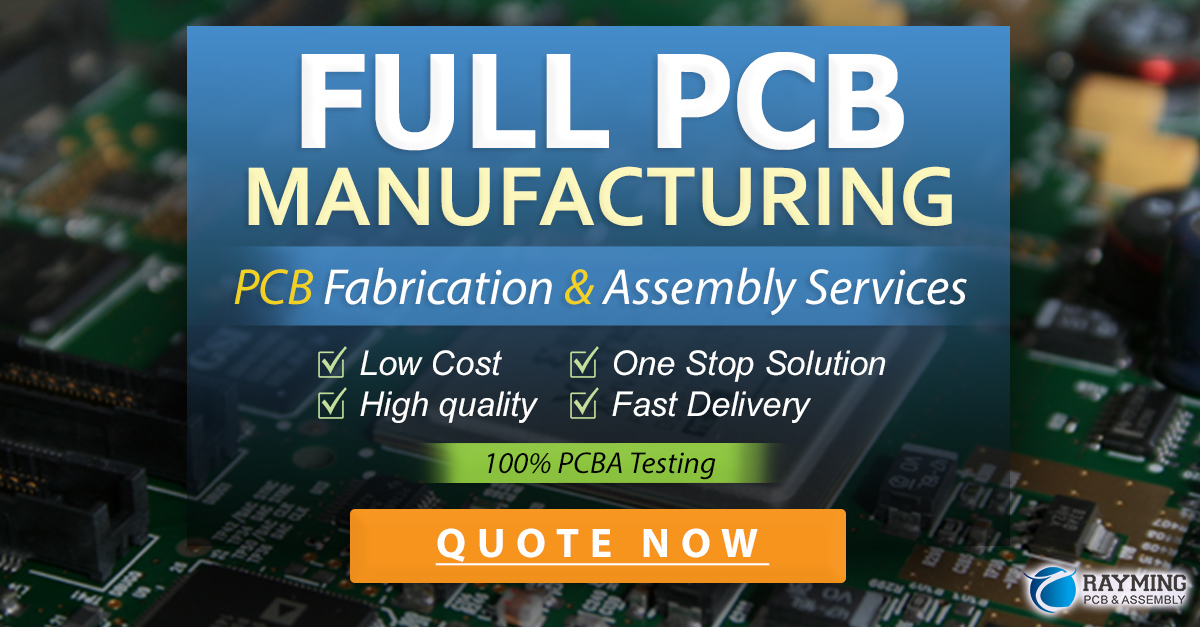
Challenges in SMT Assembly
Despite its many advantages, SMT assembly also presents some challenges:
-
Component Handling: SMT components are much smaller and more delicate than through-hole components, requiring specialized handling equipment and more precise placement.
-
Thermal Management: With higher component density, SMT PCBs can generate more heat, requiring careful thermal management in design and assembly.
-
Rework and Repair: Reworking or replacing SMT components can be more difficult due to their small size and close spacing.
-
Moisture Sensitivity: Some SMT components are sensitive to moisture and require controlled storage and handling to prevent damage during the reflow soldering process.
-
Design Complexity: The smaller size and closer spacing of SMT components can make PCB design more complex, requiring careful consideration of signal integrity, power distribution, and thermal management.
SMT Assembly Equipment
SMT assembly requires specialized equipment for each stage of the process:
-
Solder Paste Printer: Applies solder paste to the PCB using a stencil. Key features include precision alignment, adjustable print pressure, and speed.
-
Pick-and-Place Machine: Places components onto the PCB. Important considerations include placement accuracy, speed, component handling capabilities, and programming flexibility.
-
Reflow Oven: Melts the solder paste to form solder joints. Factors to consider include temperature profiling, conveyor speed, and atmosphere control (for nitrogen reflow).
-
Inspection Equipment: Includes AOI machines, X-ray systems, and ICT fixtures for post-assembly inspection and testing.
Selecting the right equipment depends on factors like production volume, component types, PCB complexity, and budget.
Designing for SMT Assembly
Designing PCBs for SMT assembly requires consideration of several key factors:
-
Component Selection: Choose components that are suitable for SMT assembly, considering package type, size, and pitch.
-
Footprint Design: Ensure component footprints match the selected components and follow manufacturer recommendations for pad size and spacing.
-
Layout Considerations: Optimize component placement for assembly efficiency, considering factors like component orientation, spacing, and access for inspection and rework.
-
Stencil Design: Design the solder paste stencil apertures to ensure the right amount of paste is deposited on each pad, considering factors like aperture size, shape, and wall thickness.
-
Design for Manufacturing (DFM): Follow SMT assembly design guidelines to ensure manufacturability, including minimum pitch, clearances, and spacing requirements.
Collaborating closely with your SMT assembly provider during the design process can help optimize your PCB design for efficient, reliable assembly.
Choosing an SMT Assembly Partner
Selecting the right SMT assembly partner is critical to the success of your project. Key factors to consider include:
-
Capabilities: Ensure the provider has experience with the types of PCBs, components, and volumes you require.
-
Quality Management: Look for providers with robust quality control processes and relevant certifications like ISO 9001, AS9100, or IPC-A-610.
-
Capacity and Lead Times: Ensure the provider has the production capacity to meet your volume requirements and can deliver within your project timelines.
-
Support and Communication: Choose a partner that offers good communication, technical support, and responsiveness to your needs.
-
Cost: While important, cost should be balanced against the other factors to ensure the best overall value for your project.
Frequently Asked Questions (FAQ)
- Q: What is the difference between SMT and through-hole assembly?
A: SMT (Surface Mount Technology) assembly mounts components directly onto the surface of the PCB, while through-hole assembly involves inserting component leads through holes in the board and soldering them on the opposite side. SMT allows for smaller components, higher density, and faster automated assembly compared to through-hole.
- Q: What are the main steps in the SMT assembly process?
A: The main steps in SMT assembly are:
1. Solder paste application: Applying solder paste to the PCB pads using a stencil.
2. Component placement: Placing components onto the solder paste using a pick-and-place machine.
3. Reflow soldering: Melting the solder paste in a reflow oven to form solder joints.
4. Inspection and testing: Verifying the quality and functionality of the assembled PCB.
- Q: What are some advantages of SMT assembly over through-hole?
A: SMT assembly offers several advantages, including:
– Smaller component size and higher density
– Faster, more automated assembly
– Lower production costs
– Improved mechanical performance and reliability
– Better high-frequency performance
- Q: What challenges are involved in SMT assembly?
A: Some challenges in SMT assembly include:
– Handling small, delicate components
– Managing thermal issues with high component density
– Difficulty in reworking or replacing components
– Dealing with moisture-sensitive components
– Increased design complexity
- Q: What should I look for when choosing an SMT assembly partner?
A: When selecting an SMT assembly partner, consider factors such as:
– Their capabilities and experience with your type of PCBs and components
– Quality management processes and certifications
– Production capacity and lead times
– Level of support and communication
– Overall value, balancing cost with other factors
By understanding the SMT assembly process, its advantages and challenges, and how to design for manufacturability, you can effectively leverage this technology for your electronic products. Choosing the right SMT assembly partner is also crucial to ensure a successful, high-quality result.
Leave a Reply