What is THT Mounting?
THT mounting, which stands for “through-hole technology” mounting, is a method of attaching electronic components to a printed circuit board (PCB) by inserting the component leads through holes drilled in the board and soldering them to pads on the opposite side. This is in contrast to surface-mount technology (SMT), where the components are soldered directly onto the surface of the PCB.
THT mounting has been used for decades in the electronics industry and is still widely used today, particularly for larger components such as capacitors, resistors, and connectors that require a more robust physical connection to the board.
Advantages of THT Mounting
There are several advantages to using THT mounting:
-
Strength: THT components are physically secured to the board by their leads, which makes them less likely to become detached due to vibration or physical stress.
-
Heat dissipation: The leads of THT components extend through the board, which allows heat to dissipate more efficiently than with SMT components that are mounted directly on the surface.
-
Ease of replacement: If a THT component fails, it can be easily removed and replaced by desoldering the leads and installing a new component.
-
Visual inspection: Because the solder joints are visible on the opposite side of the board, it is easier to visually inspect the quality of the solder joints and identify any defects.
Disadvantages of THT Mounting
However, there are also some disadvantages to THT mounting:
-
Size: THT components are generally larger than SMT components, which can limit the density of components that can be placed on a board.
-
Cost: THT components and the process of mounting them can be more expensive than SMT due to the additional drilling and soldering required.
-
Speed: The process of inserting and soldering THT components is generally slower than placing and soldering SMT components, particularly for high-volume production.
-
Automation: THT mounting is more difficult to automate than SMT, which can increase labor costs and limit production throughput.
The THT Mounting Process
The THT mounting process involves several steps:
-
Drilling: Holes are drilled in the PCB at the locations where the THT components will be mounted. The hole size is determined by the lead diameter of the component.
-
Component insertion: The leads of the THT components are inserted through the holes in the board. This can be done manually or with automated insertion equipment.
-
Soldering: The leads are soldered to the pads on the opposite side of the board. This is typically done using a wave soldering machine, which applies a wave of molten solder to the bottom of the board, or with a selective soldering machine that applies solder only to the specific leads being soldered.
-
Cleaning: After soldering, any excess flux or solder is cleaned from the board using a cleaning agent or by washing the board in a special cleaning machine.
-
Inspection: The solder joints are visually inspected to ensure that they are properly formed and free of defects such as bridges, voids, or cold joints.
THT Soldering Techniques
There are several techniques that can be used for soldering THT components:
-
Manual soldering: For low-volume production or prototypes, THT components can be soldered manually using a soldering iron. This requires a steady hand and good technique to ensure that the solder joints are properly formed.
-
Wave soldering: For higher-volume production, wave soldering is often used. In this process, the board is passed over a wave of molten solder, which flows up through the holes and around the component leads to form the solder joints.
-
Selective soldering: For boards with a mix of THT and SMT components, selective soldering can be used. In this process, a machine applies solder only to the specific leads being soldered, avoiding the SMT components.
Common THT Soldering Defects
There are several common defects that can occur during THT soldering:
Defect | Description | Cause | Prevention |
---|---|---|---|
Bridging | Solder connects adjacent leads or pads | Excessive solder, leads too close together | Proper solder amount, adequate lead spacing |
Voids | Gaps or holes in the solder joint | Insufficient solder, contamination | Proper solder amount, clean leads and pads |
Cold joints | Dull, rough, or cracked solder joint | Insufficient heat, contamination | Proper heat, clean leads and pads |
Tombstoning | Component stands up on one end | Uneven heating, component misalignment | Even heating, proper component placement |
THT Component Selection
When selecting THT components for a design, there are several factors to consider:
-
Package size: THT components come in a variety of package sizes, from small resistors and capacitors to large connectors and transformers. The package size must be compatible with the available board space and the drilling and soldering equipment.
-
Lead spacing: The spacing between the leads of a THT component must match the hole spacing on the board. Standard lead spacings include 0.1 inch (2.54 mm) and 0.2 inch (5.08 mm).
-
Power rating: The power rating of a THT component must be sufficient for the intended application. Higher power ratings may require larger package sizes or additional heat sinking.
-
Tolerance: The tolerance of a THT component refers to the allowable variation in its electrical characteristics. Tighter tolerances may be required for critical applications, but may also increase cost.
Common THT Components
Some of the most common types of THT components include:
Component | Description | Typical Values |
---|---|---|
Resistors | Passive components that resist the flow of electrical current | 1 ohm to 1 megohm |
Capacitors | Passive components that store electrical charge | 1 picofarad to 1 farad |
Diodes | Semiconductor devices that allow current to flow in only one direction | Various types and ratings |
Transistors | Semiconductor devices used for amplification and switching | Various types and ratings |
Connectors | Devices used to make electrical connections between boards or to external devices | Various types and sizes |
Transformers | Devices used to step up or step down AC voltage | Various types and ratings |
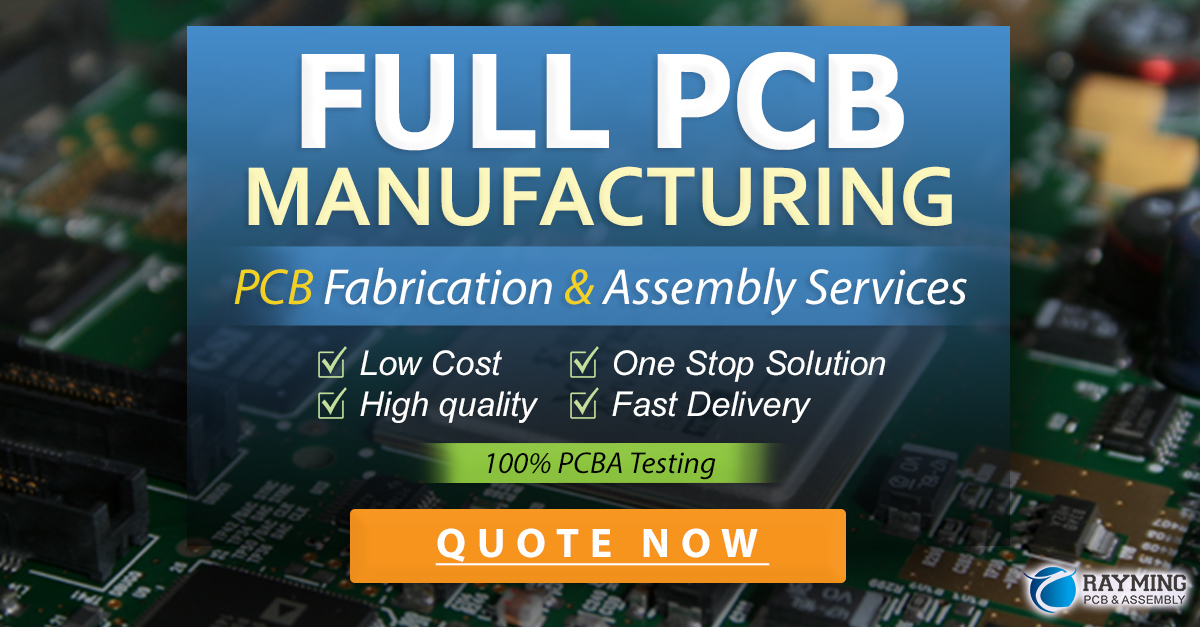
THT Design Considerations
When designing a PCB for THT components, there are several factors to consider:
-
Hole size: The hole size for each component must be large enough to accommodate the lead diameter, but not so large that the solder joint is weak or the component is loose.
-
Pad size: The pad size for each component must be large enough to provide a good solder joint, but not so large that it interferes with adjacent components or traces.
-
Trace width: The width of the traces connecting the component pads must be sufficient to carry the required current without excessive heating or voltage drop.
-
Component spacing: The spacing between components must be sufficient to allow for soldering and inspection, and to prevent electrical or thermal interference between components.
PCB Layout for THT
When laying out a PCB for THT components, there are several best practices to follow:
-
Component placement: Place components in a logical and accessible arrangement, with sufficient space for soldering and inspection. Avoid placing components too close to the edge of the board or to other components.
-
Trace routing: Route traces as directly as possible, avoiding sharp corners or long parallel runs that could cause signal integrity issues. Use appropriate trace widths for the required current and voltage.
-
Ground planes: Use ground planes on one or both sides of the board to provide a low-impedance return path for signals and to reduce electromagnetic interference (EMI).
-
Solder mask: Use a solder mask to prevent solder bridging between adjacent pads or traces, and to protect the board from oxidation and contamination.
FAQ
1. Can THT and SMT components be used on the same board?
Yes, it is common to use both THT and SMT components on the same board, particularly for designs that require a mix of larger and smaller components or that have both high-power and high-density areas. However, this can increase the complexity and cost of the assembly process, as different soldering techniques may be required for each type of component.
2. What is the difference between lead-free and leaded solder?
Lead-free solder is a type of solder that does not contain lead, which is a toxic metal that can be harmful to human health and the environment. Lead-free solder typically contains tin, silver, and copper, and has a higher melting point than leaded solder. Leaded solder, on the other hand, contains a mixture of tin and lead, and has a lower melting point and better wetting properties than lead-free solder. The use of leaded solder is regulated in many countries due to concerns about lead exposure.
3. Can THT components be reworked or replaced?
Yes, one of the advantages of THT mounting is that components can be easily removed and replaced if they fail or need to be upgraded. This is done by desoldering the leads from the board using a soldering iron or desoldering tool, removing the old component, and soldering in a new one. However, this process can be time-consuming and requires careful technique to avoid damaging the board or adjacent components.
4. What is the difference between a plated through-hole and a non-plated through-hole?
A plated through-hole is a hole in a PCB that has been coated with a conductive material, typically copper, to provide an electrical connection between the top and bottom layers of the board. This allows signals to pass through the board and connects the component leads to traces on both sides. A non-plated through-hole, on the other hand, is a hole that has not been coated and does not provide an electrical connection between layers. Non-plated holes are often used for mounting hardware or for components that do not require an electrical connection to the board.
5. Can THT components be used for high-frequency applications?
THT components can be used for high-frequency applications, but they may not be the best choice in all cases. The leads of THT components can act as antennas and can pick up or radiate electromagnetic interference (EMI), which can cause signal integrity issues at high frequencies. Additionally, the larger size and greater lead length of THT components can increase parasitic inductance and capacitance, which can limit the bandwidth and increase the signal distortion. For high-frequency applications, SMT components are often preferred due to their smaller size, shorter lead lengths, and better high-frequency performance. However, THT components can still be used in many high-frequency designs with proper layout and shielding techniques.
Leave a Reply