What is Functional Testing?
Functional testing is a quality assurance process that verifies whether a PCB Assembly performs its intended functions according to the design specifications. It involves subjecting the assembLED PCB to various tests and measurements to ensure that it operates correctly under different conditions and scenarios.
Objectives of Functional Testing
The primary objectives of functional testing in PCB assembly include:
- Verifying the proper operation of the PCB assembly
- Identifying and isolating defects or malfunctions
- Ensuring the PCB assembly meets the design specifications and customer requirements
- Validating the compatibility and interoperability of the PCB assembly with other components or systems
- Establishing the reliability and durability of the PCB assembly
Importance of Functional Testing in PCB Assembly
Functional testing plays a vital role in the PCB assembly process for several reasons:
Quality Assurance
Functional testing helps ensure the quality and reliability of the assembled PCB. By detecting and isolating defects early in the assembly process, functional testing prevents defective or malfunctioning PCBs from reaching the end-users, thereby reducing the risk of product failures and customer complaints.
Cost Savings
Identifying and fixing defects during the functional testing stage is more cost-effective than discovering issues later in the product lifecycle. Early detection of problems helps avoid expensive rework, repairs, or product recalls, ultimately saving time and resources for the manufacturer and the customer.
Compliance with Standards and Regulations
Functional testing helps ensure that the PCB assembly complies with relevant industry standards, safety regulations, and environmental requirements. By verifying the PCB’s performance against these standards, manufacturers can avoid legal and regulatory issues and maintain their reputation in the market.
Customer Satisfaction
Functional testing contributes to customer satisfaction by delivering high-quality and reliable PCB assemblies that meet the customer’s expectations and requirements. By thoroughly testing the PCB’s functionality, manufacturers can provide products that perform as intended, leading to increased customer confidence and loyalty.
Methods of Functional Testing
There are various methods and techniques used in functional testing of PCB assemblies. Some of the common methods include:
In-Circuit Testing (ICT)
In-circuit testing is a method that verifies the functionality of individual components on the PCB assembly. It involves using a bed-of-nails fixture to make electrical contact with specific points on the PCB and measure the electrical characteristics of each component. ICT helps identify component-level faults, such as open circuits, short circuits, and incorrect component values.
Flying Probe Testing
Flying probe testing is an alternative to ICT that uses movable probes to make electrical contact with the PCB assembly. The probes can be programmed to test specific points on the PCB and measure the electrical characteristics. Flying probe testing is more flexible than ICT and can be used for low-volume production or prototypes where creating a bed-of-nails fixture is not feasible.
Boundary Scan Testing
Boundary scan testing, also known as JTAG testing, is a method that uses the built-in test access port (TAP) on the PCB to test the interconnections between the components. It involves sending test patterns through the TAP and verifying the response of the components. Boundary scan testing is particularly useful for testing complex PCBs with high-density interconnects and Ball Grid Array (BGA) packages.
Functional Test Fixtures
Functional test fixtures are custom-designed tools that simulate the operating environment of the PCB assembly. They provide the necessary inputs, loads, and interfaces to test the PCB’s functionality under real-world conditions. Functional test fixtures can be used to test the PCB’s power supply, signal integrity, communication interfaces, and other critical functions.
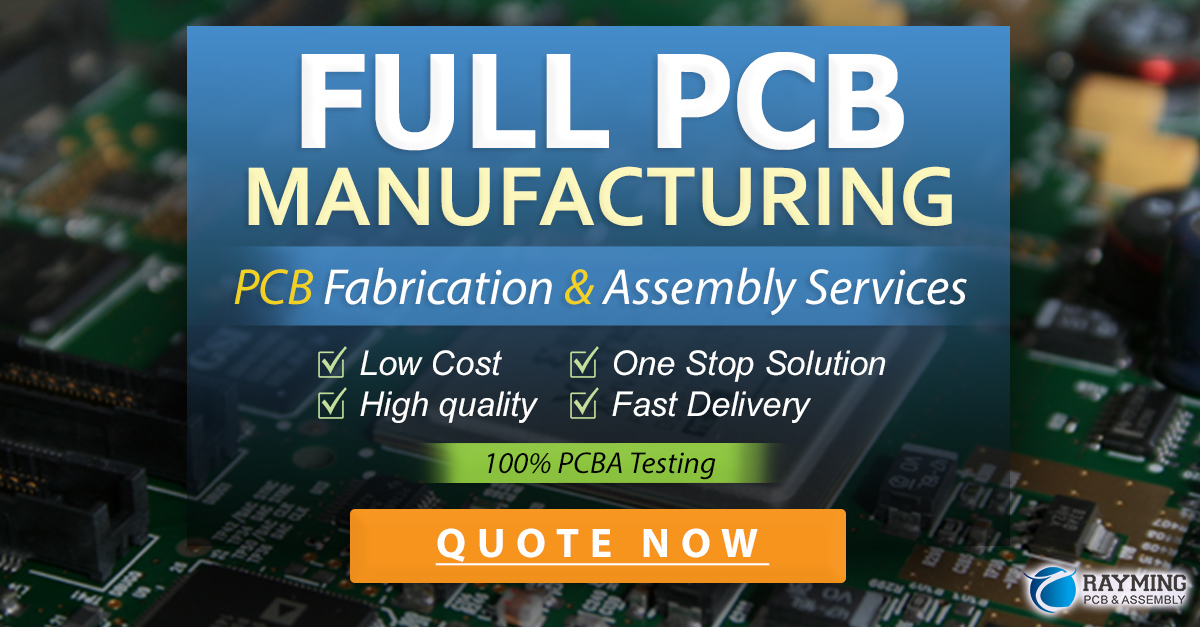
Best Practices for Functional Testing
To ensure effective and efficient functional testing of PCB assemblies, consider the following best practices:
Test Planning
Develop a comprehensive test plan that outlines the test objectives, methods, and acceptance criteria. The test plan should be based on the design specifications, customer requirements, and relevant industry standards. It should also consider the production volume, complexity of the PCB, and available resources.
Test Coverage
Ensure adequate test coverage by identifying the critical functions and parameters to be tested. Use a combination of different test methods to cover all aspects of the PCB’s functionality, including component-level testing, interconnect testing, and system-level testing.
Test Automation
Implement test automation wherever possible to improve the efficiency and repeatability of functional testing. Automated test equipment (ATE) and software tools can help streamline the testing process, reduce human errors, and generate consistent test results.
Failure Analysis and Corrective Action
Establish a systematic approach for analyzing test failures and implementing corrective actions. Document the failure modes, root causes, and corrective actions taken to prevent recurrence. Use the failure data to improve the design, manufacturing, and testing processes continuously.
Traceability and Documentation
Maintain proper traceability and documentation throughout the functional testing process. Keep records of the test plans, test results, failure reports, and corrective actions. Ensure that the documentation is easily accessible and auditable for quality assurance and regulatory compliance.
Frequently Asked Questions (FAQ)
1. What is the difference between functional testing and in-circuit testing?
Functional testing focuses on verifying the overall functionality of the PCB assembly, while in-circuit testing targets individual components and their electrical characteristics. Functional testing ensures that the PCB performs its intended functions under real-world conditions, while in-circuit testing helps identify component-level faults.
2. Can functional testing replace other testing methods like ICT or flying probe testing?
No, functional testing should be used in conjunction with other testing methods to ensure comprehensive coverage. Each testing method has its strengths and limitations, and a combination of different methods helps provide a more thorough evaluation of the PCB assembly’s quality and reliability.
3. How do I determine the appropriate test coverage for functional testing?
The appropriate test coverage depends on various factors, such as the complexity of the PCB, the critical functions to be tested, and the available resources. It is essential to review the design specifications, customer requirements, and relevant industry standards to identify the critical parameters and functions that need to be tested. A risk-based approach can also be used to prioritize the testing efforts based on the potential impact of failures.
4. What are some common challenges in functional testing of PCB assemblies?
Some common challenges in functional testing include:
- Developing comprehensive test plans that cover all critical functions and scenarios
- Designing and fabricating test fixtures that accurately simulate the operating environment
- Identifying and isolating intermittent or transient faults
- Dealing with complex PCBs with high-density interconnects and advanced packaging technologies
- Ensuring the repeatability and reproducibility of test results
5. How can I improve the efficiency and effectiveness of functional testing?
To improve the efficiency and effectiveness of functional testing, consider the following strategies:
- Implement test automation using ATE and software tools
- Develop reusable test scripts and fixtures
- Collaborate with design and manufacturing teams to incorporate testability features into the PCB design
- Establish clear test acceptance criteria and failure thresholds
- Continuously monitor and analyze test data to identify trends and improvement opportunities
Conclusion
Functional testing is a critical step in the PCB assembly process that ensures the proper operation and reliability of the assembled printed circuit board. By verifying the PCB’s functionality against the design specifications and customer requirements, functional testing helps identify and isolate defects early in the assembly process, saving time and resources for the manufacturer and the customer.
Effective functional testing involves a combination of different test methods, such as in-circuit testing, flying probe testing, boundary scan testing, and functional test fixtures. To ensure the success of functional testing, it is essential to develop comprehensive test plans, ensure adequate test coverage, implement test automation, establish systematic failure analysis and corrective action processes, and maintain proper traceability and documentation.
By following best practices and continuously improving the functional testing process, manufacturers can deliver high-quality and reliable PCB assemblies that meet the customers’ expectations and regulatory requirements. Functional testing not only contributes to customer satisfaction but also helps manufacturers maintain their competitive edge in the market by reducing costs, improving efficiency, and enhancing product quality.
Leave a Reply