Introduction to PCB Assembly and First Article Inspection (FIA)
Printed Circuit Board (PCB) assembly is a complex process that involves multiple steps and requires strict quality control measures to ensure the final product meets the required specifications. One crucial aspect of quality control in PCB assembly is First Article Inspection (FIA), a process that verifies the first production run of a new or revised design meets all specified requirements.
RAYPCB, a leading PCB manufacturer, employs a comprehensive PCB assembly process and conducts thorough First Article Inspections to guarantee the highest quality products for their customers. In this article, we will explore the PCB assembly process and the importance of First Article Inspection in detail.
The PCB Assembly Process
Step 1: PCB Fabrication
Before the assembly process begins, the PCB itself must be fabricated. This involves creating the circuit board substrate, applying the copper layers, and etching the desired circuit pattern onto the board. The PCB fabrication process at RAYPCB follows these sub-steps:
-
PCB Design: The PCB design is created using computer-aided design (CAD) software, which generates the necessary files for fabrication, such as Gerber files and drill files.
-
Material Selection: The appropriate substrate material is chosen based on the PCB’s intended application, such as FR-4, high-frequency materials, or flexible substrates.
-
Copper Cladding: Copper foil is laminated onto the substrate using heat and pressure to create the conductive layer.
-
Drilling: Holes are drilled into the PCB according to the drill files generated during the design phase. These holes accommodate through-hole components and provide electrical connections between layers.
-
Patterning: The desired circuit pattern is transferred onto the copper layer using a photoresist and exposure to UV light. The unexposed areas are then etched away, leaving the desired copper traces.
-
Surface Finish: A surface finish, such as HASL (Hot Air Solder Leveling), ENIG (Electroless Nickel Immersion Gold), or OSP (Organic Solderability Preservative), is applied to protect the copper traces and improve solderability.
Step 2: Component Placement
Once the PCB is fabricated, the next step is to place the electronic components onto the board. This process is typically performed using automated pick-and-place machines, which can accurately position components at high speeds. The component placement process involves:
-
Solder Paste Application: Solder paste is applied to the PCB’s surface using a stencil or screen printing process. The solder paste consists of tiny solder particles suspended in a flux medium, which helps to clean and protect the metal surfaces during soldering.
-
Component Placement: The pick-and-place machine uses vacuum nozzles to pick up components from reels or trays and place them onto the PCB’s surface according to the design files. The machine’s high-resolution cameras ensure accurate component positioning.
-
Reflow Soldering: After component placement, the PCB undergoes a reflow soldering process. The board is heated in a controlled manner, causing the solder paste to melt and form electrical and mechanical connections between the components and the PCB.
Step 3: Inspection and Testing
To ensure the quality of the assembLED PCB, several inspection and testing processes are performed, including:
-
Automated Optical Inspection (AOI): An AOI machine uses high-resolution cameras to scan the PCB for any defects, such as missing or misaligned components, solder bridges, or insufficient solder joints.
-
X-ray Inspection: For components with hidden solder joints, such as Ball Grid Arrays (BGAs) or Quad Flat No-leads (QFNs), X-ray inspection is used to verify the integrity of the solder connections.
-
In-Circuit Testing (ICT): ICT is performed using a bed-of-nails fixture that makes electrical contact with specific points on the PCB. This test verifies the presence, orientation, and value of components, as well as the continuity of the circuit.
-
Functional Testing: The assembled PCB is powered on and tested for its intended functionality, ensuring that it performs according to the design specifications.
First Article Inspection (FIA) in PCB Assembly
What is First Article Inspection?
First Article Inspection (FIA) is a process that involves thoroughly inspecting and testing the first production run of a new or revised PCB design. The purpose of FIA is to verify that the manufactured product meets all specified requirements, including dimensional accuracy, material specifications, and performance criteria.
FIA is typically performed before full-scale production begins to identify any issues or deviations from the design early in the manufacturing process. This allows for necessary corrections or adjustments to be made, minimizing the risk of producing non-conforming products and reducing overall manufacturing costs.
The Importance of First Article Inspection
First Article Inspection plays a critical role in ensuring the quality and reliability of PCB assemblies. Some of the key benefits of conducting FIA include:
-
Quality Assurance: FIA verifies that the manufactured product meets all specified requirements, ensuring that the customer receives a high-quality product that functions as intended.
-
Early Issue Detection: By inspecting the first production run, any issues or deviations from the design can be identified and addressed early in the manufacturing process, preventing the production of non-conforming products.
-
Cost Reduction: Identifying and correcting issues during FIA helps to minimize the risk of producing defective products, which can lead to significant cost savings by reducing scrap, rework, and potential product recalls.
-
Customer Satisfaction: Providing customers with products that have undergone rigorous FIA processes demonstrates a commitment to quality and helps to build trust and long-term relationships.
RAYPCB’s First Article Inspection Process
At RAYPCB, First Article Inspection is an integral part of the PCB assembly process. The company follows a comprehensive FIA procedure to ensure the highest quality standards are met. The FIA process at RAYPCB includes:
-
Documentation Review: The FIA team reviews all relevant documentation, including design files, Bill of Materials (BOM), and assembly drawings, to ensure that the product is built according to the specified requirements.
-
Dimensional Inspection: The team measures critical dimensions of the PCB and components using high-precision measurement tools, such as calipers, micrometers, and coordinate measuring machines (CMMs), to verify that they meet the specified tolerances.
-
Material Verification: The FIA team verifies that the materials used in the PCB assembly, such as the substrate, components, and solder, conform to the specified requirements using material certifications and lab tests when necessary.
-
Workmanship Inspection: The team visually inspects the PCB assembly for any workmanship issues, such as proper component placement, solder joint quality, and cleanliness, using magnification tools and Automated Inspection systems.
-
Functional Testing: The FIA team performs functional testing on the assembled PCB to ensure that it operates according to the design specifications. This may include in-circuit testing, boundary scan testing, and system-level functional testing.
-
Documentation: The FIA results, including any deviations or non-conformances, are documented in a detailed report. This report is reviewed by the engineering and quality teams to determine the necessary corrective actions and to approve the product for full-scale production.
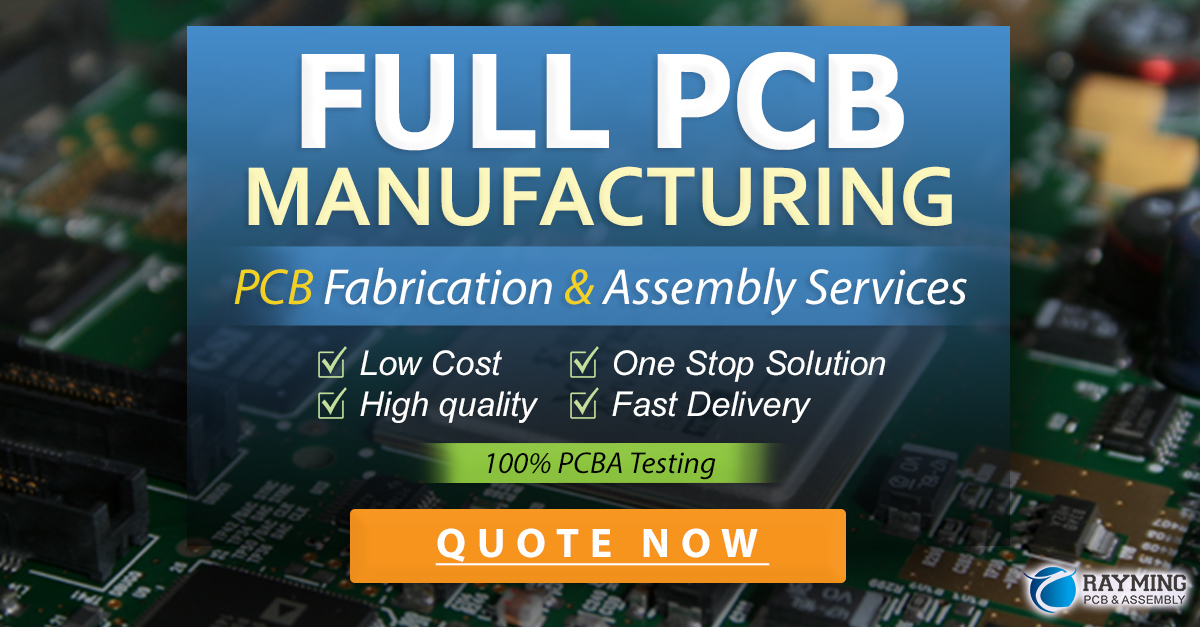
The Benefits of Choosing RAYPCB for PCB Assembly and First Article Inspection
RAYPCB is committed to providing its customers with the highest quality PCB assembly services, and the company’s comprehensive First Article Inspection process is a testament to this commitment. By choosing RAYPCB for your PCB assembly needs, you can expect:
-
Expertise: RAYPCB has a team of experienced engineers and technicians who are well-versed in PCB assembly and First Article Inspection processes, ensuring that your products are built to the highest quality standards.
-
State-of-the-Art Facilities: RAYPCB’s manufacturing facilities are equipped with the latest technology and equipment, enabling the company to handle a wide range of PCB assembly projects, from simple to complex designs.
-
Rapid Turnaround: With streamlined processes and efficient workflows, RAYPCB can deliver high-quality PCB assemblies with short lead times, helping you to bring your products to market faster.
-
Competitive Pricing: RAYPCB offers competitive pricing for its PCB assembly services, including First Article Inspection, without compromising on quality.
-
Customer Support: RAYPCB’s dedicated customer support team is available to answer any questions you may have and to provide guidance throughout the PCB assembly process, ensuring a smooth and successful project.
Frequently Asked Questions (FAQ)
-
What is the difference between PCB fabrication and PCB assembly?
PCB fabrication refers to the process of creating the bare circuit board, which includes designing the circuit, selecting materials, and etching the copper traces onto the substrate. PCB assembly, on the other hand, involves placing and soldering electronic components onto the fabricated PCB to create a functional electronic assembly. -
Why is First Article Inspection important in PCB assembly?
First Article Inspection is important because it verifies that the first production run of a new or revised PCB design meets all specified requirements. This process helps to identify any issues or deviations from the design early in the manufacturing process, allowing for necessary corrections to be made and minimizing the risk of producing non-conforming products. -
How long does the First Article Inspection process take?
The duration of the First Article Inspection process can vary depending on the complexity of the PCB design and the extent of the inspection required. Generally, FIA can take anywhere from a few days to a couple of weeks. At RAYPCB, the FIA process is streamlined to ensure efficient and timely completion without compromising on quality. -
What are some common defects that can be detected during First Article Inspection?
Some common defects that can be detected during First Article Inspection include dimensional inaccuracies, incorrect or missing components, solder joint issues (such as bridging, insufficient solder, or cold joints), and workmanship problems (such as poor component placement or cleanliness issues). -
How can I ensure that my PCB design is ready for First Article Inspection?
To ensure that your PCB design is ready for First Article Inspection, it is important to provide complete and accurate documentation, including design files (such as Gerber files and bill of materials), assembly drawings, and any specific requirements or specifications. It is also recommended to work closely with your PCB assembly provider, such as RAYPCB, to review your design and address any potential issues before starting the assembly process.
Conclusion
The PCB assembly process and First Article Inspection are critical aspects of ensuring the quality and reliability of electronic products. RAYPCB’s comprehensive approach to PCB assembly and FIA demonstrates the company’s commitment to providing its customers with the highest quality products and services.
By understanding the importance of these processes and choosing a reputable PCB assembly provider like RAYPCB, you can have confidence in the quality and functionality of your electronic products, ultimately leading to increased customer satisfaction and success in the market.
Leave a Reply