What is PCB Prototyping?
PCB prototyping is the process of creating a physical representation of a PCB design to test its functionality, performance, and reliability. The prototype is used to identify any design flaws, component compatibility issues, and manufacturing challenges before the final production run.
Why is PCB Prototyping Important?
PCB prototyping is crucial for several reasons:
-
Design Validation: Prototyping allows designers to test and validate their PCB design to ensure it meets the required specifications and functions as intended.
-
Cost Reduction: By identifying and fixing design issues early in the development process, prototyping helps reduce the overall cost of production by avoiding expensive redesigns and manufacturing errors.
-
Time-to-Market: Prototyping enables faster development cycles, allowing companies to bring their products to market more quickly.
PCB Prototyping Design Flow
The PCB prototyping design flow consists of several stages, each with its own set of tasks and considerations. The following table outlines the main stages of the PCB prototyping design flow:
Stage | Description |
---|---|
Schematic Design | Creating a schematic diagram of the circuit, including component selection and connectivity |
PCB Layout | Designing the physical layout of the PCB, including component placement, routing, and layer stackup |
Design Rule Check (DRC) | Verifying the PCB layout against a set of design rules to ensure manufacturability and reliability |
Prototype Fabrication | Manufacturing the physical prototype PCB based on the final design files |
Assembly and Soldering | Populating the PCB with components and soldering them in place |
Testing and Validation | Performing various tests to ensure the prototype meets the required specifications and functions as intended |
Schematic Design
The schematic design stage involves creating a diagram that represents the electrical connections between components in the circuit. This stage includes the following tasks:
-
Component Selection: Choosing the appropriate components based on the circuit requirements, such as voltage, current, and power ratings.
-
Schematic Capture: Drawing the schematic diagram using electronic design automation (EDA) software, such as Altium Designer, Eagle, or KiCad.
-
Design Verification: Checking the schematic for errors, such as missing connections, incorrect component values, or incompatible components.
PCB Layout
Once the schematic design is complete, the next stage is to create the physical layout of the PCB. This stage involves the following tasks:
-
Component Placement: Arranging the components on the PCB in a way that minimizes the overall size, reduces signal interference, and improves manufacturability.
-
Routing: Connecting the components using copper traces on the PCB Layers, ensuring that the traces meet the required width, spacing, and impedance characteristics.
-
Layer Stackup: Defining the number and arrangement of copper and dielectric layers in the PCB, based on the signal integrity and EMC requirements.
Design Rule Check (DRC)
After completing the PCB layout, it is essential to perform a design rule check (DRC) to verify that the design meets the manufacturing and reliability requirements. The DRC checks for various issues, such as:
-
Clearance: Ensuring that there is sufficient space between components, traces, and vias to prevent short circuits and signal interference.
-
Trace Width and Spacing: Verifying that the traces meet the minimum width and spacing requirements based on the current carrying capacity and signal integrity needs.
-
Drill Sizes and Pad Sizes: Checking that the drill holes and component pads are sized correctly for manufacturability and solderability.
Prototype Fabrication
Once the PCB design has passed the DRC, the next stage is to manufacture the physical prototype. This stage involves the following steps:
-
Gerber File Generation: Exporting the PCB design files in the industry-standard Gerber format, which contains information about the copper layers, solder mask, silkscreen, and drill holes.
-
Fabrication: Sending the Gerber files to a PCB fabrication house, which will manufacture the prototype PCBs using processes such as photolithography, etching, and plating.
-
Quality Control: Inspecting the fabricated PCBs for any manufacturing defects, such as short circuits, open circuits, or incorrect hole sizes.
Assembly and Soldering
After receiving the fabricated PCBs, the next stage is to assemble the components onto the board. This stage involves the following tasks:
-
Component Procurement: Sourcing the required components from suppliers, ensuring that they meet the specifications and are available in the correct quantities.
-
Soldering: Attaching the components to the PCB using soldering techniques such as hand soldering, reflow soldering, or wave soldering, depending on the component types and quantities.
-
Inspection: Visually inspecting the assembLED PCBs for any soldering defects, such as bridging, cold joints, or insufficient solder coverage.
Testing and Validation
The final stage of the PCB prototyping design flow is to test and validate the assembled prototype to ensure it meets the required specifications and functions as intended. This stage involves various tests, such as:
-
Power-on Test: Applying power to the prototype and checking for any signs of smoke, sparks, or overheating, which may indicate a short circuit or component failure.
-
Functional Test: Testing the prototype’s functionality by applying input signals and measuring the output signals, ensuring that they match the expected values.
-
Environmental Test: Subjecting the prototype to various environmental conditions, such as temperature, humidity, and vibration, to ensure that it can withstand the intended operating conditions.
-
EMC Test: Testing the prototype for electromagnetic compatibility (EMC), ensuring that it does not emit excessive electromagnetic interference (EMI) and is not susceptible to external EMI sources.
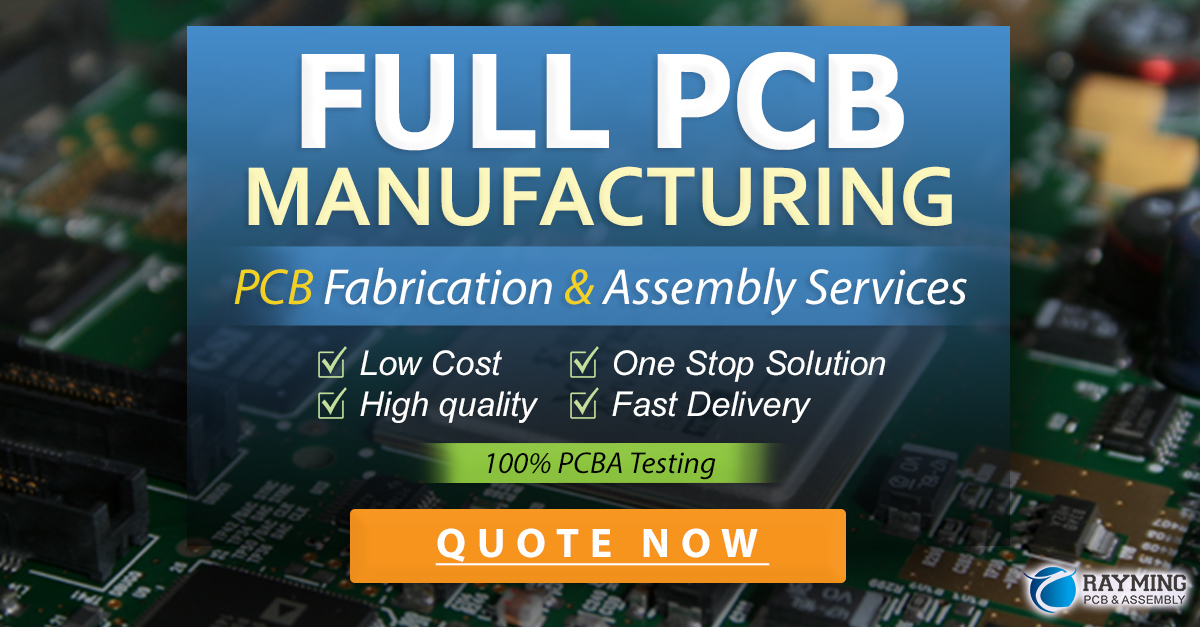
Frequently Asked Questions (FAQ)
-
What is the difference between a PCB Prototype and a final production PCB?
A PCB prototype is a functional representation of the final PCB design, used for testing and validation purposes. It may have minor differences in materials, components, or manufacturing processes compared to the final production PCB, which is optimized for mass production and cost-effectiveness. -
How long does the PCB prototyping process take?
The duration of the PCB prototyping process varies depending on the complexity of the design, the availability of components, and the fabrication and assembly lead times. A simple prototype may take a few days to a week, while a more complex prototype may take several weeks or even months. -
What are the common challenges faced during PCB prototyping?
Some common challenges faced during PCB prototyping include component availability and obsolescence, design errors and incompatibilities, manufacturing defects, and testing and validation issues. Careful planning, thorough design reviews, and close collaboration with fabrication and assembly partners can help mitigate these challenges. -
Can PCB prototyping be outsourced to third-party service providers?
Yes, many companies choose to outsource PCB prototyping to specialized service providers who have the expertise, equipment, and processes to handle the fabrication, assembly, and testing of prototypes. Outsourcing can help reduce costs, minimize risks, and accelerate the development process. -
What are the benefits of using rapid PCB prototyping techniques?
Rapid PCB prototyping techniques, such as 3D printing or milling, can help reduce the time and cost of creating prototypes, especially for low-volume or complex designs. These techniques allow for quick iterations and design changes, enabling faster validation and time-to-market.
Conclusion
PCB prototyping is a critical process in the development of electronic devices, enabling designers to test and validate their designs before committing to mass production. The PCB prototyping design flow involves several stages, including schematic design, PCB layout, design rule check, prototype fabrication, assembly and soldering, and testing and validation.
By following a structured and thorough prototyping process, companies can identify and fix design issues early, reduce development costs and risks, and accelerate time-to-market. Whether performed in-house or outsourced to specialized service providers, PCB prototyping is an essential step in ensuring the success and reliability of electronic products.
Leave a Reply