1. Research and Identify Potential SMT Manufacturers
The first step in finding a good SMT manufacturer is to conduct thorough research and identify potential candidates. Here are some ways to do this:
1.1 Online Directories and Industry Associations
Utilize online directories and industry associations to find SMT manufacturers. Some popular resources include:
- Global Sources
- Alibaba
- IPC (Association Connecting Electronics Industries)
- SMTA (Surface Mount Technology Association)
These platforms provide a comprehensive list of SMT manufacturers, along with their capabilities, certifications, and contact information.
1.2 Referrals and Recommendations
Reach out to your network of industry professionals, colleagues, and business partners for referrals and recommendations. They may have first-hand experience working with reliable SMT manufacturers and can provide valuable insights.
1.3 Trade Shows and Exhibitions
Attend trade shows and exhibitions related to the electronics industry. These events provide an excellent opportunity to meet SMT manufacturers in person, discuss your requirements, and evaluate their expertise.
2. Evaluate the SMT Manufacturer’s Capabilities
Once you have identified potential SMT manufacturers, evaluate their capabilities to ensure they can meet your specific requirements. Consider the following factors:
2.1 Manufacturing Capabilities
Assess the SMT manufacturer’s production capabilities, including:
- PCB Assembly (PCBA) capabilities
- SMT line capacity and throughput
- Automated Optical Inspection (AOI) and testing equipment
- Conformal coating and potting capabilities
- Box build and final assembly services
Ensure that the manufacturer can handle your product complexity, volume requirements, and lead times.
2.2 Quality Control and Certifications
Verify the SMT manufacturer’s commitment to quality by checking their quality control processes and certifications. Look for:
- ISO 9001 certification for quality management systems
- IPC certifications (e.g., IPC-A-610, IPC-J-STD-001)
- RoHS and REACH compliance
- In-house testing and inspection capabilities
A manufacturer with strong quality control measures and relevant certifications is more likely to deliver high-quality products consistently.
2.3 Engineering Support
Evaluate the SMT manufacturer’s engineering support capabilities, such as:
- Design for Manufacturing (DFM) services
- Prototype development and testing
- Component sourcing and supply chain management
- PCB layout and design recommendations
A manufacturer with in-house engineering expertise can provide valuable support throughout the product development process, helping you optimize your design for manufacturability and cost-effectiveness.
3. Assess the SMT Manufacturer’s Experience and Expertise
When selecting an SMT manufacturer, consider their experience and expertise in the industry. Look for the following:
3.1 Industry Experience
Check the SMT manufacturer’s years of experience in the industry and their track record of successfully delivering projects similar to yours. An experienced manufacturer is more likely to have streamlined processes, established supplier relationships, and the ability to handle complex projects.
3.2 Expertise in Your Industry or Application
Evaluate the SMT manufacturer’s expertise in your specific industry or application. For example, if you are developing medical devices, look for a manufacturer with experience in medical electronics and familiarity with relevant regulations and standards.
3.3 Customer References and Case Studies
Request customer references and case studies from the SMT manufacturer. Reach out to their existing or previous clients to gather feedback on their experience, product quality, and overall satisfaction. Positive customer testimonials and successful case studies indicate the manufacturer’s reliability and competence.
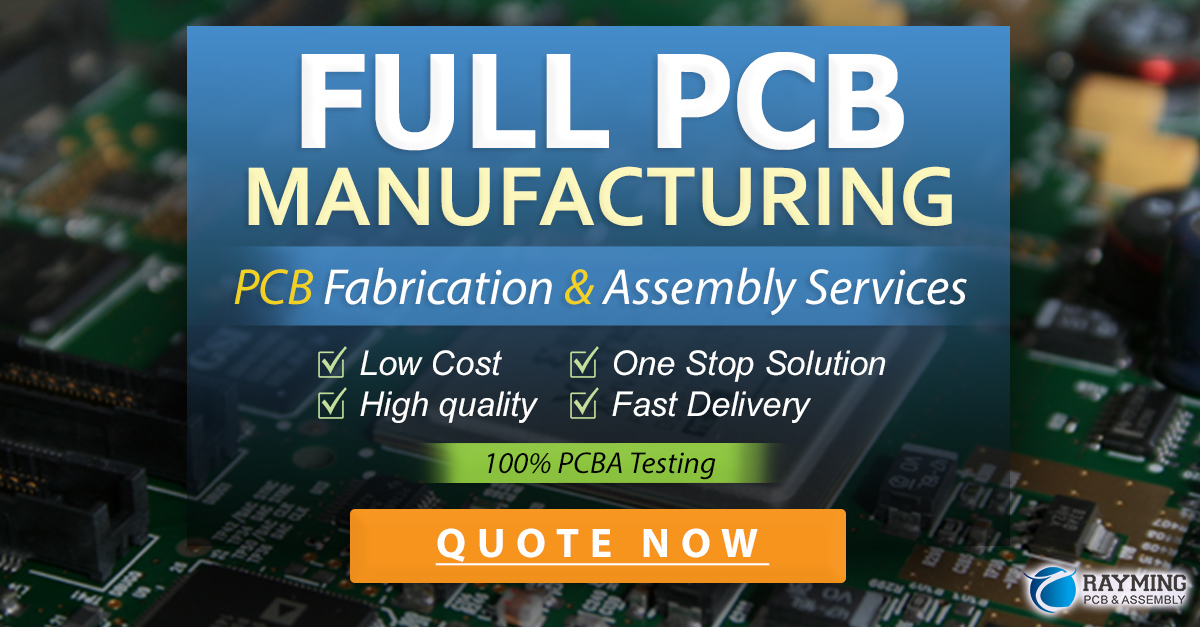
4. Evaluate the SMT Manufacturer’s Communication and Customer Service
Effective communication and responsive customer service are essential for a successful Partnership with an SMT manufacturer. Consider the following aspects:
4.1 Communication Channels
Verify the availability of multiple communication channels, such as email, phone, video conferencing, and a dedicated project manager. Ensure that the manufacturer is responsive and easily accessible to address your queries and concerns.
4.2 Language Proficiency
If you are working with an overseas SMT manufacturer, check their language proficiency in your preferred language (e.g., English). Clear communication is crucial to avoid misunderstandings and ensure your requirements are accurately understood and implemented.
4.3 Reporting and Transparency
Inquire about the SMT manufacturer’s reporting and transparency practices. They should provide regular updates on project progress, manufacturing status, and any potential issues or delays. Transparency builds trust and allows you to make informed decisions.
5. Consider the SMT Manufacturer’s Location and Logistics
The location of the SMT manufacturer and their logistics capabilities can impact your supply chain efficiency and costs. Consider the following factors:
5.1 Proximity to Your Market
Evaluate the SMT manufacturer’s proximity to your target market. A manufacturer closer to your market can reduce shipping times and costs while providing faster response times to market demands.
5.2 Shipping and Logistics Capabilities
Assess the SMT manufacturer’s shipping and logistics capabilities. They should have established relationships with reliable shipping partners and be able to handle international shipping, customs clearance, and documentation if required.
5.3 Inventory Management and Warehousing
Inquire about the SMT manufacturer’s inventory management and warehousing services. Some manufacturers offer Vendor Managed Inventory (VMI) programs, allowing them to maintain an agreed-upon level of inventory on your behalf, reducing your inventory carrying costs and ensuring timely product availability.
6. Evaluate Pricing and Cost-Effectiveness
While cost is an important consideration when selecting an SMT manufacturer, it should not be the sole deciding factor. Consider the following aspects:
6.1 Competitive Pricing
Obtain quotes from multiple SMT manufacturers and compare their pricing. However, be cautious of abnormally low quotes, as they may indicate compromises in quality or hidden costs.
6.2 Total Cost of Ownership (TCO)
Evaluate the Total Cost of Ownership (TCO) rather than just the unit price. TCO includes factors such as manufacturing costs, shipping expenses, inventory carrying costs, and potential cost savings from value-added services like design optimization and supply chain management.
6.3 Value-Added Services
Consider the value-added services offered by the SMT manufacturer, such as design support, testing, and logistics management. These services can streamline your operations, reduce overall costs, and improve time-to-market.
Frequently Asked Questions (FAQ)
- What is the minimum order quantity (MOQ) for SMT manufacturing?
The minimum order quantity varies among SMT manufacturers. Some may offer low MOQs for prototyping and small-volume production, while others may require higher volumes. Discuss your specific requirements with the manufacturer to determine their MOQ policies. - How long does it take to receive a prototype from an SMT manufacturer?
The lead time for receiving a prototype depends on various factors, such as the complexity of your design, the manufacturer’s workload, and the availability of components. Typically, prototype lead times range from a few days to several weeks. Communicate your timeline requirements to the manufacturer and inquire about their prototype turnaround times. - Can SMT manufacturers source components on my behalf?
Yes, many SMT manufacturers offer component sourcing services. They have established relationships with component suppliers and can help you procure components at competitive prices. Discuss your component requirements with the manufacturer and inquire about their sourcing capabilities and policies. - How can I ensure the protection of my intellectual property when working with an SMT manufacturer?
To protect your intellectual property, consider signing a Non-Disclosure Agreement (NDA) with the SMT manufacturer before sharing sensitive information. Additionally, look for manufacturers with strong intellectual property protection policies and a track record of maintaining client confidentiality. - What certifications should I look for in an SMT manufacturer?
When evaluating SMT manufacturers, look for certifications such as ISO 9001 for quality management systems, IPC certifications (e.g., IPC-A-610, IPC-J-STD-001) for electronics manufacturing standards, and RoHS and REACH compliance for environmental regulations. These certifications demonstrate the manufacturer’s commitment to quality, reliability, and adherence to industry standards.
Conclusion
Selecting the right SMT manufacturer is a critical decision that can significantly impact the success of your electronic products. By following these six proven tips – researching and identifying potential manufacturers, evaluating their capabilities, assessing their experience and expertise, considering communication and customer service, evaluating location and logistics, and assessing pricing and cost-effectiveness – you can make an informed decision and find a reliable SMT manufacturer that meets your specific requirements.
Remember to prioritize quality, reliability, and long-term partnership potential over short-term cost savings. A good SMT manufacturer will not only deliver high-quality products but also provide valuable support and expertise throughout your product development journey.
Tip | Description |
---|---|
1 | Research and Identify Potential SMT Manufacturers |
2 | Evaluate the SMT Manufacturer’s Capabilities |
3 | Assess the SMT Manufacturer’s Experience and Expertise |
4 | Evaluate the SMT Manufacturer’s Communication and Customer Service |
5 | Consider the SMT Manufacturer’s Location and Logistics |
6 | Evaluate Pricing and Cost-Effectiveness |
By following these tips and conducting thorough due diligence, you can find the right SMT manufacturer to bring your electronic products to life, ensuring quality, reliability, and success in the market.
Leave a Reply