Introduction to Double-Sided PCBs
Double-sided printed circuit boards (PCBs) are a common type of PCB used in various electronic devices. As the name suggests, these PCBs have conductive layers on both sides of the board, allowing for more complex circuits and higher component density compared to single-sided PCBs. This article will explore the different types of double-sided PCBs and the manufacturing process involved in their production.
Types of Double-Sided PCBs
There are two main types of double-sided PCBs:
1. Double-Sided PTH PCBs
Double-sided plated through-hole (PTH) PCBs have conductive layers on both sides of the board, connected by plated through-holes. These through-holes allow for electrical connections between the top and bottom layers of the PCB. Components can be mounted on both sides of the board, either through through-hole mounting or surface mounting.
2. Double-Sided SMT PCBs
Double-sided Surface Mount Technology (SMT) PCBs also have conductive layers on both sides of the board, but they do not use through-holes for electrical connections. Instead, components are surface mounted on both sides of the PCB using solder pads. This allows for higher component density and smaller board sizes compared to PTH PCBs.
Advantages of Double-Sided PCBs
Double-sided PCBs offer several advantages over single-sided PCBs:
- Increased circuit complexity: With conductive layers on both sides, double-sided PCBs can accommodate more complex circuits and higher component density.
- Improved electrical performance: Double-sided PCBs can reduce electromagnetic interference (EMI) and improve signal integrity by allowing for better grounding and shielding.
- Reduced board size: By utilizing both sides of the board, double-sided PCBs can be smaller than single-sided PCBs with the same functionality.
- Cost-effective: Although double-sided PCBs are more expensive than single-sided PCBs, they can be more cost-effective for complex designs that would otherwise require multiple single-sided PCBs.
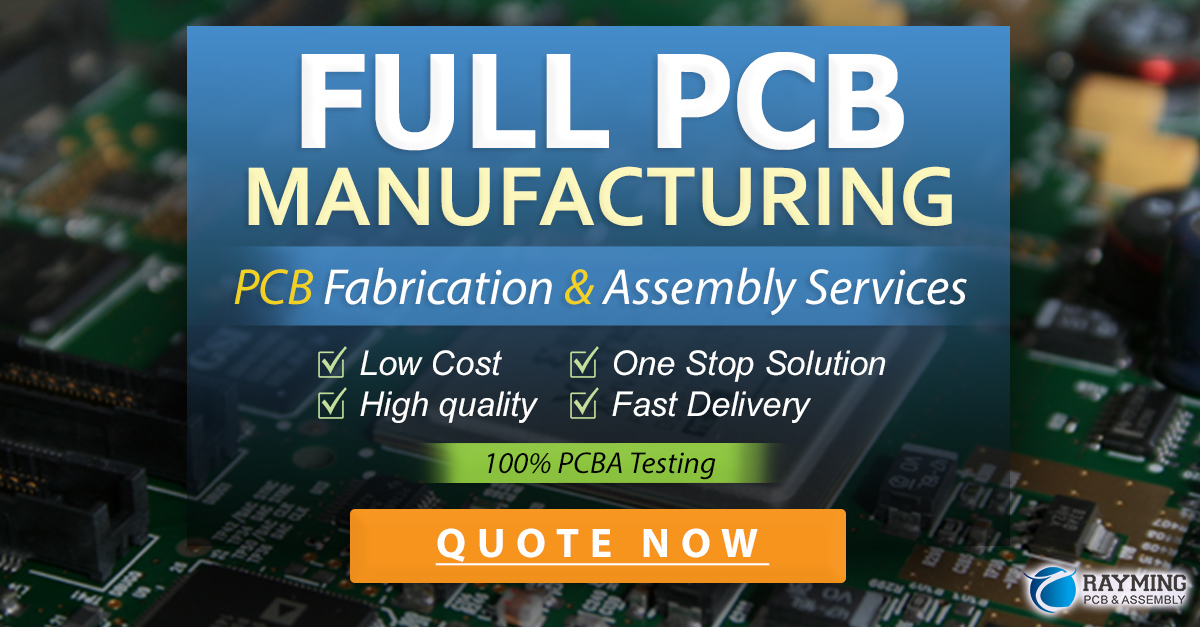
Double-Sided PCB Manufacturing Process
The manufacturing process for double-sided PCBs involves several steps:
1. Design and Preparation
The first step in the manufacturing process is to design the PCB using electronic design automation (EDA) software. The design includes the circuit schematic, component placement, and routing of the conductive traces. Once the design is finalized, the PCB manufacturer prepares the necessary materials and equipment.
2. Copper Clad Laminate
The base material for a double-sided PCB is a copper clad laminate (CCL), which consists of a non-conductive substrate, such as FR-4, with a thin layer of Copper Foil bonded to both sides. The thickness of the copper foil can vary depending on the specific requirements of the PCB.
3. Drilling
Holes are drilled into the CCL to accommodate through-hole components and vias. The drilling process can be done using a CNC drilling machine or a laser drilling machine, depending on the size and complexity of the holes required.
4. Plating
For double-sided PTH PCBs, the drilled holes are plated with a conductive material, such as copper, to create electrical connections between the top and bottom layers. This process is called electroplating and involves depositing a thin layer of copper onto the walls of the drilled holes.
5. Patterning
The next step is to create the desired circuit pattern on both sides of the PCB. This is done by applying a photoresist layer to the copper surfaces and exposing it to UV light through a photomask that contains the circuit pattern. The exposed areas of the photoresist are then developed and removed, leaving the desired circuit pattern protected by the remaining photoresist.
6. Etching
The unprotected copper areas are etched away using a chemical solution, typically ferric chloride or ammonium persulfate. This leaves only the desired circuit pattern on both sides of the PCB.
7. Solder Mask Application
A solder mask, also known as a solder resist, is applied to both sides of the PCB to protect the copper traces from oxidation and prevent solder bridges during the assembly process. The solder mask is typically green in color but can be other colors as well.
8. Silkscreen Printing
A silkscreen layer is printed onto the PCB to add component labels, logos, and other identifying markings. The silkscreen is typically white but can be other colors as well.
9. Surface Finish
A surface finish is applied to the exposed copper areas to protect them from oxidation and improve solderability. Common surface finishes include:
- Hot Air Solder Leveling (HASL)
- Organic Solderability Preservative (OSP)
- Electroless Nickel Immersion Gold (ENIG)
- Immersion Silver (IAg)
- Immersion Tin (ISn)
10. Electrical Testing
Finally, the manufactured PCBs are electrically tested to ensure they meet the required specifications and functionality. This can include continuity tests, insulation resistance tests, and functional tests.
Double-Sided PCB Design Considerations
When designing a double-sided PCB, there are several factors to consider:
1. Component Placement
Components should be placed strategically on both sides of the board to minimize the length of conductive traces and reduce signal interference. It is also important to consider the mechanical constraints of the device in which the PCB will be used.
2. Via Placement
Vias are used to connect the top and bottom layers of the PCB. The placement of vias should be carefully considered to ensure proper electrical connections and minimize signal interference.
3. Trace Width and Spacing
The width and spacing of conductive traces should be designed to meet the electrical requirements of the circuit while minimizing signal interference and ensuring manufacturability.
4. Impedance Control
For high-speed circuits, impedance control is crucial to ensure signal integrity. This involves carefully designing the width and spacing of conductive traces to match the desired impedance.
5. Grounding and Shielding
Proper grounding and shielding techniques should be employed to reduce EMI and ensure signal integrity. This can include the use of ground planes, shielding layers, and proper component placement.
Double-Sided PCB Manufacturing Challenges
Double-sided PCB manufacturing comes with its own set of challenges:
1. Alignment
Ensuring proper alignment between the top and bottom layers of the PCB is critical for proper electrical connections and functionality. Misalignment can lead to short circuits, open circuits, or other defects.
2. Plating Uniformity
Achieving uniform plating thickness in the through-holes can be challenging, especially for high aspect ratio holes. Uneven plating can lead to poor electrical connections and reduced reliability.
3. Solder Mask Application
Applying a uniform and defect-free solder mask layer on both sides of the PCB can be challenging, particularly for fine-pitch components and high-density designs.
4. Warping
Double-sided PCBs are more susceptible to warping compared to single-sided PCBs due to the different thermal expansion rates of the materials used. Warping can cause issues during assembly and affect the reliability of the final product.
FAQ
1. What is the difference between a double-sided PTH PCB and a double-sided SMT PCB?
A double-sided PTH PCB uses plated through-holes to connect the top and bottom layers, allowing for through-hole component mounting. A double-sided SMT PCB does not use through-holes and relies on surface mounted components on both sides of the board.
2. Can double-sided PCBs be used for high-frequency applications?
Yes, double-sided PCBs can be used for high-frequency applications, but proper design considerations must be taken into account. This includes impedance control, grounding, and shielding techniques to ensure signal integrity and minimize EMI.
3. What is the typical turnaround time for double-sided PCB manufacturing?
The turnaround time for double-sided PCB manufacturing varies depending on the complexity of the design, the chosen manufacturer, and the desired quantity. Typically, small to medium-sized orders can be completed within 1-2 weeks, while larger or more complex orders may take 3-4 weeks or longer.
4. How much do double-sided PCBs cost compared to single-sided PCBs?
Double-sided PCBs are generally more expensive than single-sided PCBs due to the additional materials and manufacturing steps involved. However, for complex designs that would otherwise require multiple single-sided PCBs, a double-sided PCB can be more cost-effective in the long run.
5. What are some common applications for double-sided PCBs?
Double-sided PCBs are used in a wide range of electronic devices, including:
- Consumer electronics (smartphones, tablets, laptops)
- Automotive electronics (infotainment systems, engine control units)
- Industrial equipment (control systems, sensors, automation devices)
- Medical devices (diagnostic equipment, monitoring systems)
- Telecommunications equipment (routers, switches, modems)
Conclusion
Double-sided PCBs are a versatile and widely used type of printed circuit board that offer several advantages over single-sided PCBs, including increased circuit complexity, improved electrical performance, and reduced board size. The manufacturing process for double-sided PCBs involves multiple steps, each requiring precision and attention to detail to ensure a high-quality final product.
When designing a double-sided PCB, it is important to consider factors such as component placement, via placement, trace width and spacing, impedance control, and grounding and shielding techniques. Double-sided PCB manufacturing also comes with its own set of challenges, including alignment, plating uniformity, solder mask application, and warping.
Despite these challenges, double-sided PCBs remain a popular choice for a wide range of electronic applications due to their versatility and cost-effectiveness. As electronic devices continue to become more complex and compact, the demand for high-quality double-sided PCBs is likely to grow, driving further advancements in PCB manufacturing technologies and processes.
Leave a Reply