Introduction
Flexible printed circuits (FPCs), commonly known as flex PCBs, are a specialized type of printed circuit board made with flexible substrate materials like polyimide or polyester. This allows the circuit to bend and flex while still maintaining electronic interconnections.
Compared to rigid PCBs, flex circuits can withstand dynamic flexing conditions, conform to space constraints, and simplify assemblies through foldable or wrappable configurations. Key applications demanding flex PCB technology include consumer electronics, automotive, aerospace, medical, robotics and IoT devices.
As these applications drive market growth estimated to reach over $27 billion by 2025, identifying the leading global flex PCB manufacturers becomes critical when assessing suppliers.
This article profiles the top 10 flex PCB companies worldwide as measured by revenue, capabilities, and reputation for quality and innovation.
Leading Global Flex PCB Manufacturers
Here are the 10 largest and most technologically advanced flex PCB producers serving customers worldwide:
1. Flexium Interconnect
- Headquarters: Zhuhai, China
- Revenue: $1.92 billion
- Capabilities: 12+ layer flex and rigid-flex PCBs with features like embedded passives and fine line widths to 0.15mm. High mix production capacity from quick-turn prototypes to over 1 million boards per month.
Flexium produces flex PCBs for products like smartphones, notebooks, servers, telecom infrastructure, smart watches, medical devices, satellites, and IoT. R&D centers in Taiwan and the USA along with manufacturing facilities in China and India give them a global supply chain.
2. Zhen Ding Technology
- Headquarters: Taipei, Taiwan
- **Revenue: ** $1.73 billion
- Capabilities: A wide variety including single, double and multilayer flex PCBs. Production volumes up to 500,000 boards per month. Fine line capabilities down to 15μm and controlled impedance tolerance to 8%.
Zhen Ding Technology serves diverse markets ranging from consumer electronics to automotive, industrial, and medical products with demand for flex PCBs in Asia, Europe and Americas.
3. Nippon Mektron
- Headquarters: Tokyo, Japan
- Revenue: $1.5 billion
- Capabilities: One of the earliest flex PCB manufacturers with over 50 years of expertise. They produce extremely high layer count flex up to 30 layers and rigid-flex boards. Features like sequentially laminated and stacked vias enable high interconnect density and miniaturization.
Nippon Mektron supplies flex PCBs for applications from HDD suspensions to portable medical devices, printers, cameras, and automotive electronics.
4. Tripod Technology
- Headquarters: Taiwan
- Revenue: $0.97 billion
- Capabilities: High volume flex and rigid-flex PCB assembly services. Manufacturing locations in Taiwan and China allow regional support. Solder mask defined (SMD) flex PCB technology along with sequential bonding/lamination.
Key application areas include consumer electronics, computing, automotive, and industrial. Tripod has design centers worldwide to collaborate closely with customers.
5. Career Technologies
- Headquarters: Taiwan
- Revenue: $0.92 billion
- Capabilities: 16 layer flexible circuits with line width/space down to 25/25 μm. Rigid-flex PCBs with high layer counts – up to 32 buildup layers. Specializes in short runs and engineering support.
Career Technologies focuses on flex PCB applications in consumer devices, automotive, IoT, and medical products requiring miniaturization and high density.
6. Flexium Interconnect
- Headquarters: Singapore
- Revenue: $0.74 billion
- Capabilities: A global flex PCB supplier with manufacturing locations in the US and China in addition to their Singapore headquarters. Produces extremely high complexity flex circuits with up to 30 layers along with via-in-pad HDI technology.
Key application expertise includes healthcare, instrumentation, telecom infrastructure, aerospace, defense, and automotive electronics.
7. Sumitomo Electric
- Headquarters: Osaka, Japan
- Revenue: $0.65 billion
- Capabilities: Ultra-fine line single and multilayer flex circuits. Features like thin core construction down to 25μm and multilayer flex with 20μm line/space. Also produces flexible flat cabling (FFC).
Supplies flex PCBs into products for the automotive, consumer, industrial, and communications industries.
8. Multek
- Headquarters: Taiwan
- Revenue: $0.60 billion
- Capabilities: Specializes in rigid-flex PCBs with high layer counts – up to 18 layers. Also offers quick-turn engineering support and prototyping services.
Multek leverages vertically integrated facilities in Asia and North America to provide flex PCBs for smartphones, laptops, servers, telecom infrastructure and other high reliability applications.
9. Ichia Technologies
- Headquarters: Taiwan
- Revenue: $0.46 billion
- Capabilities: Wide range of flex PCB offerings – single layer to multilayer flex/rigid-flex, metal-based circuit boards, and flexible flat cables. Manufacturing locations in Taiwan, China, Vietnam and Mexico.
Key applications include consumer electronics and IoT along with specialized products for servers, networking, automotive and medical devices.
10. All Flex
- Headquarters: Minnesota, USA
- Revenue: $0.23 billion
- Capabilities: Quick-turn engineering support and prototyping for flex PCBs. Circuits ranging from simple single layer to multilayer rigid-flex. Also offers design services and advanced testing.
All Flex provides flex PCB solutions for medical, military, aerospace, telecom infrastructure and ruggedized electronics applications where quality and reliability are critical.
Evaluating Flex PCB Supplier Capabilities
When examining the capabilities of the leading flex PCB manufacturers, here are some of the key considerations:
Production Volumes
- Prototyping to low volume for new product development
- High volume production for mature, cost-sensitive designs
Board Complexity
- Layer count – single layer to 20+ layers
- Line width/space – ability to achieve finer geometries
Design Support
- Collaboration during design stage for DFM
- Quick-turnaround on prototyping designs
Materials and Construction
- Polyimide, polyester, LCP or metal substrates
- Adhesives used for multilayer bonding
- Copper thickness – thin to multilayer
Testing and Certification
- Electrical testing, environmental stress screening (ESS)
- Standards compliance – IPC, ISO, AS
Supply Chain
- Geographic manufacturing locations
- Use of advanced equipment – direct imaging, laser drilling etc.
- Supply continuity through forecasts, capacity expansion
By evaluating both the technical sophistication and business partnerships, customers can determine the ideal flex PCB partner for each application.
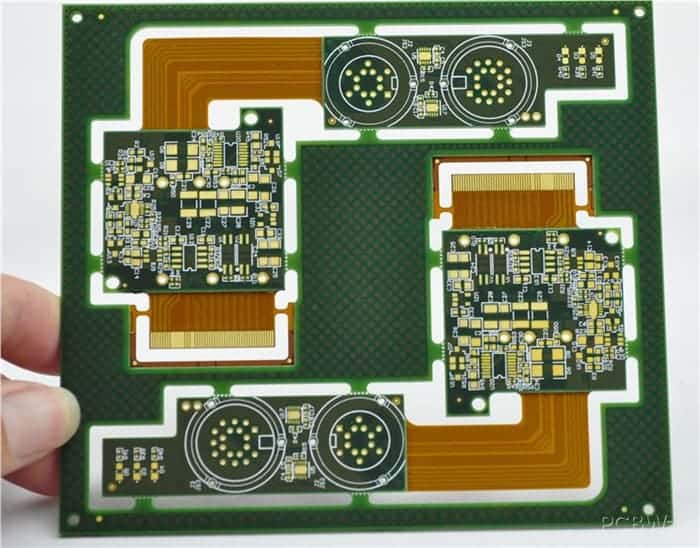
Global Footprint and Localization
Many of the top flex PCB manufacturers maintain a global footprint of design, manufacturing, and sales resources to support customers worldwide:
- Sales/engineering offices near key customer locations
- Multiple manufacturing locations across US, Asia, Europe
- Regional warehousing for reduced logistics time
- Support for common regional languages – Chinese, Japanese, English
Proximity, cultural awareness, and supply chain transparency help build the level of collaboration needed for innovative product development.
At the same time, localization initiatives enhance relationships with domestic customers:
- Local sourcing of raw materials
- Expansion of manufacturing centers
- Hiring/training local workforce
- Compliance with labor, tax, and environmental regulations
This balances the need for both regional expertise and global supply continuity when designing complex products.
Industry Leadership through Innovation
Beyond production capacity and technology, the leading flex PCB companies invest heavily in R&D to pioneer advanced materials, processes, and designs:
- Novel substrates – flexible glass, foldable composites, nano-materials
- Fine line technology – additive processes, ultra-thin cores
- High density interconnect – microvias, buried vias, stacked vias
- Embedded passives – thin film resistors, capacitors
- Printed electronics – sensors, antennas, heaters
- Flexible hybrid electronics – integration with ICs
This innovation delivers next-generation solutions even as products miniaturize with higher performance requirements.
Some ways flex PCB suppliers facilitate customer design innovation:
- Early DFM collaboration and design reviews
- PCB layout services leveraging extensive experience
- Supply of advanced material technology samples for proof of concept
- Sharing of process qualification data to accelerate learning
- Prototyping services to iterate on novel designs
- Published technical resources – white papers, tech briefs, videos
By fostering partnerships beyond just procurement, leading flex PCB manufacturers enable customers to gain competitive advantage through cutting edge flex technologies.
Quality and Reliability Processes
For flex PCBs being designed into mission-critical functions and operating environments, quality and reliability are paramount. The top manufacturers implement stringent processes:
Design Rigor
- DFM analysis using proven design rules for flex PCBs
- Validation through prototyping builds and testing Feedback
Process Control
- Automated optical inspection (AOI) during fabrication
- Real-time process monitoring and alerting
- Traceability through manufacturing execution system (MES)
Materials
- Certificate of conformance from suppliers
- Raw material quality plans – sampling, qualification testing
- Control of shelf life, storage, handling
Testing
- 100% electrical testing (ICT)
- Selective high-pot testing
- Environment stress screening (ESS)
Certifications
- ISO 9001 quality management
- IATF 16949 automotive standard
- AS 9100 aerospace standard
- ISO 13485 medical devices standard
- IPC standards – JPCA 6013C Class 3 target
This rigorous quality infrastructure minimizes risks during product deployments.
Conclusion
As flexible PCB technology moves into diverse applications demanding high reliability combined with design innovation, partnering with an expert flex PCB manufacturer becomes critical.
The leading global suppliers profiled here provide sophisticated technical capabilities along with extensive design support, supply chain infrastructure, and uncompromising quality to deliver advanced flex PCB solutions into the most challenging New Product Introduction programs.
By leveraging their expertise, customers can accelerate flex PCB designs to achieve next-generation products with maximized value.
Frequently Asked Questions
What are some emerging trends in flex PCB technology?
Key trends include higher layer count flex/rigid-flex boards, flexible hybrid electronics integrating sensors and ICs, printed electronics, embedded passives and components, use of new nano-materials as substrates.
What certification standards are most critical for flex PCBs?
IPC 6013 Class 3 certification demonstrates proven fabrication processes. ISO 9001 and IATF 16949 confirms rigorous quality procedures. Aerospace and defense applications may require AS 9100.
How are flex PCB manufacturers optimizing their supply chains?
Expanding manufacturing locations regionally, local sourcing of materials, establishing warehousing hubs close to customers, forecasting tools, and yield improvements provide supply chain continuity.
What factors determine cost for advanced flex PCBs?
High layer counts, smaller line widths, special materials, low volume production, quick turns and engineering support increase flex PCB costs. Optimizing design and supply chain can offset cost drivers.
How do you qualify and select a flex PCB supplier?
Assess technical capabilities relative to application requirements. Examine track record delivering similar flex boards. Review quality certifications and reliability data. Validate regional support infrastructure.
Leave a Reply