What is Impedance?
Before diving into Controlled Impedance, let’s first define impedance itself. Impedance is a measure of opposition to alternating current (AC) in an electrical circuit. It is similar to resistance, but while resistance applies to direct current (DC), impedance encompasses both resistance and reactance, which is the opposition to AC due to capacitance and inductance.
Impedance is measured in ohms (Ω) and is represented by the complex quantity Z:
Z = R + jX
where:
– R is resistance
– X is reactance
– j is the imaginary unit (square root of -1)
The reactance component of impedance can be further broken down into capacitive reactance (Xc) and inductive reactance (Xl):
X = Xc + Xl
Capacitive reactance is inversely proportional to frequency, while inductive reactance is directly proportional to frequency. This means that as the frequency of an AC signal increases, capacitive reactance decreases and inductive reactance increases.
Transmission Lines and Characteristic Impedance
In the context of PCBs and electronic systems, signals travel along transmission lines, which are conductive paths designed to carry high-speed signals with minimal distortion. These transmission lines have a property called characteristic impedance, which is determined by their physical dimensions and the properties of the dielectric material surrounding them.
Characteristic impedance (Z0) is given by the formula:
Z0 = √(L/C)
where:
– L is the inductance per unit length
– C is the capacitance per unit length
For a given dielectric material, the characteristic impedance of a transmission line is determined by its width, thickness, and the distance between it and the reference plane (usually ground or power). Common values of characteristic impedance in PCB Design include 50Ω, 75Ω, and 100Ω.
The Importance of Impedance Matching
When a signal travels along a transmission line, it encounters the characteristic impedance of that line. If the impedance of the source (e.g., a driver circuit) and the load (e.g., a receiver circuit) match the characteristic impedance of the transmission line, the signal will propagate without distortion. This is known as impedance matching.
However, if there is an impedance mismatch, a portion of the signal will be reflected back towards the source, causing signal integrity issues such as ringing, overshoot, and undershoot. These reflections can lead to data corruption, increased electromagnetic interference (EMI), and even damage to components.
To minimize reflections and ensure proper signal transmission, it is crucial to design transmission lines with controlled impedance and match the impedance of the source and load to the characteristic impedance of the line.
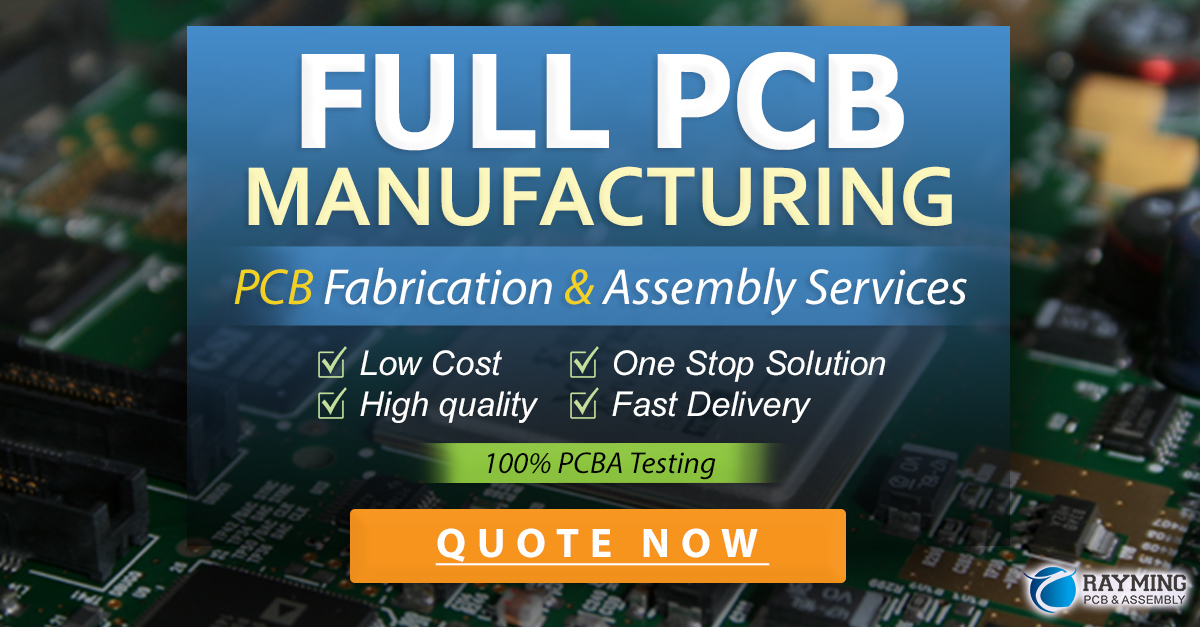
Factors Affecting Impedance Control
Several factors can impact the impedance of a transmission line and, consequently, the quality of signal transmission. These include:
-
Dielectric constant (εr): The dielectric constant of the PCB substrate material influences the capacitance of the transmission line. Materials with higher dielectric constants, such as FR-4, result in lower characteristic impedance for a given geometry.
-
Trace width and thickness: The width and thickness of the conductive trace determine its inductance and capacitance per unit length. Wider traces have lower inductance and higher capacitance, resulting in lower characteristic impedance.
-
Trace spacing: The spacing between a trace and its reference plane (ground or power) affects the capacitance of the transmission line. Closer spacing increases capacitance and lowers characteristic impedance.
-
Copper roughness: The surface roughness of the copper traces can impact impedance by affecting the effective cross-sectional area of the conductor. Rougher surfaces result in higher impedance.
-
Manufacturing tolerances: Variations in PCB manufacturing processes, such as etching and lamination, can lead to deviations from the designed impedance. Tighter tolerances help maintain consistent impedance across the board.
Designing for Controlled Impedance
To achieve controlled impedance in PCB design, several best practices should be followed:
-
Choose an appropriate dielectric material: Select a PCB substrate material with a stable dielectric constant and low loss tangent to minimize signal attenuation and distortion.
-
Calculate trace dimensions: Use impedance calculation tools or formulas to determine the appropriate trace width, thickness, and spacing for the desired characteristic impedance.
-
Maintain consistent trace geometry: Ensure that the trace width and spacing remain constant along the entire length of the transmission line to avoid impedance discontinuities.
-
Use reference planes: Provide uninterrupted reference planes (ground or power) beneath or adjacent to the controlled impedance traces to maintain a constant impedance environment.
-
Minimize vias and transitions: Avoid unnecessary vias and transitions in controlled impedance traces, as they can introduce impedance discontinuities and reflections.
-
Route traces perpendicular to board edges: Route controlled impedance traces perpendicular to the board edges to minimize the impact of board edge effects on impedance.
-
Specify impedance requirements: Clearly communicate the impedance requirements to the PCB Manufacturer, including the target impedance, tolerance, and test method.
Measuring and Verifying Impedance
After designing and manufacturing a PCB with controlled impedance, it is essential to measure and verify the actual impedance of the transmission lines to ensure they meet the specified requirements. Several methods can be used for impedance measurement:
-
Time Domain Reflectometry (TDR): TDR measures the impedance of a transmission line by sending a fast-rising pulse along the line and analyzing the reflections caused by impedance discontinuities. TDR provides a graphical representation of the impedance profile along the line.
-
Frequency Domain Reflectometry (FDR): FDR measures the impedance of a transmission line by sweeping a range of frequencies and analyzing the reflected signal. FDR is useful for characterizing the impedance of a line over a wide frequency range.
-
Vector Network Analyzer (VNA): A VNA measures the scattering parameters (S-parameters) of a transmission line, which can be used to calculate the characteristic impedance and other properties of the line.
-
Impedance Test Coupons: Impedance test coupons are dedicated traces on a PCB designed specifically for impedance measurement. These coupons are typically placed near the edge of the board and can be easily probed or connected to measurement equipment.
Regularly measuring and verifying the impedance of Controlled Impedance PCBs helps ensure that the manufactured boards meet the design requirements and can support reliable, high-speed signal transmission.
Common Controlled Impedance Applications
Controlled impedance is crucial in various applications that involve high-speed digital signals, high-frequency analog signals, or sensitive low-level signals. Some common applications include:
-
High-speed digital interfaces: Controlled impedance is essential for maintaining signal integrity in high-speed digital interfaces such as DDR memory, PCIe, USB, and HDMI.
-
RF and microwave circuits: Impedance matching is critical in RF and microwave circuits to maximize power transfer and minimize reflections between components.
-
Automotive and aerospace electronics: Controlled impedance helps ensure reliable operation of electronic systems in harsh environments with strict EMI and signal integrity requirements.
-
Medical devices: Proper impedance control is important in medical devices to maintain the accuracy and reliability of sensitive analog signals, such as those from sensors and electrodes.
-
Telecommunications equipment: Controlled impedance is essential in telecommunications equipment, such as routers and switches, to support high-speed data transmission and minimize signal distortion.
Impedance Control and EMI
In addition to ensuring signal integrity, controlled impedance plays a crucial role in managing electromagnetic interference (EMI) in electronic systems. Impedance mismatches and discontinuities can act as sources of EMI, radiating unwanted electromagnetic energy that can interfere with nearby devices or cause the system to fail EMC (electromagnetic compatibility) tests.
By maintaining consistent impedance along transmission lines and minimizing reflections, controlled impedance helps reduce EMI generation and improve the overall EMC performance of the system. This is particularly important in applications subject to strict EMC regulations, such as automotive, aerospace, and medical electronics.
To further mitigate EMI, controlled impedance design should be combined with other EMC best practices, such as proper grounding, shielding, and filtering.
FAQ
-
What is the difference between controlled impedance and characteristic impedance?
Characteristic impedance refers to the inherent impedance of a transmission line, determined by its physical dimensions and dielectric properties. Controlled impedance, on the other hand, is the process of designing and manufacturing transmission lines to have a specific characteristic impedance and maintaining that impedance along the entire length of the line. -
Why is it important to match the impedance of the source and load to the transmission line?
Matching the impedance of the source and load to the characteristic impedance of the transmission line minimizes signal reflections caused by impedance mismatches. Reflections can lead to signal integrity issues, such as ringing, overshoot, and undershoot, as well as increased electromagnetic interference (EMI). -
What are some common characteristic impedance values used in PCB design?
Common characteristic impedance values in PCB design include 50Ω, 75Ω, and 100Ω. The choice of impedance value depends on the specific application, the type of signals being transmitted, and the requirements of the components and interfaces involved. -
How does the dielectric constant of a PCB substrate material affect impedance?
The dielectric constant (εr) of a PCB substrate material influences the capacitance of the transmission line. Materials with higher dielectric constants, such as FR-4, result in lower characteristic impedance for a given trace geometry. Conversely, materials with lower dielectric constants, such as Rogers laminates, allow for wider traces and larger gaps to maintain the same characteristic impedance. -
What are some best practices for designing controlled impedance transmission lines?
Some best practices for designing controlled impedance transmission lines include: - Choosing an appropriate dielectric material with a stable dielectric constant and low loss tangent.
- Calculating the optimal trace width, thickness, and spacing for the desired characteristic impedance.
- Maintaining consistent trace geometry along the entire length of the transmission line.
- Using uninterrupted reference planes (ground or power) beneath or adjacent to the controlled impedance traces.
- Minimizing vias and transitions in controlled impedance traces.
- Routing traces perpendicular to board edges to minimize edge effects on impedance.
- Clearly specifying impedance requirements to the PCB manufacturer.
Conclusion
Controlled impedance is a fundamental concept in the design and manufacture of high-speed, high-frequency, and sensitive electronic systems. By carefully managing the impedance of transmission lines and ensuring impedance matching between components, designers can maintain signal integrity, minimize electromagnetic interference, and improve the overall reliability and performance of their systems.
As the demand for faster data rates, higher frequencies, and more complex electronic devices continues to grow, the importance of controlled impedance will only increase. By understanding the principles of impedance control and following best practices in PCB design and manufacturing, engineers can create robust, reliable systems that meet the challenges of today’s rapidly evolving technology landscape.
Leave a Reply