Introduction to RF PCB Design
Radio frequency (RF) printed circuit board (PCB) design is a specialized field that deals with the layout and routing of high-frequency electronic circuits. RF PCB design requires careful consideration of various factors such as signal integrity, impedance matching, electromagnetic interference (EMI), and power dissipation. This ultimate guide will provide you with the essential knowledge and best practices for designing RF PCBs.
Understanding the Basics of RF PCB Design
Key Concepts in RF PCB Design
To effectively design RF PCBs, it is crucial to understand the following key concepts:
- Impedance Matching
- Signal Integrity
- Electromagnetic Interference (EMI)
- Transmission Lines
- Grounding and Shielding
RF PCB Material Selection
Choosing the right PCB material is critical for achieving optimal RF performance. The most common RF PCB materials include:
Material | Dielectric Constant | Dissipation Factor | Applications |
---|---|---|---|
FR-4 | 4.3-4.6 | 0.02 | Low-cost, general-purpose |
Rogers RO4003C | 3.38 | 0.0027 | High-frequency, low-loss |
Isola IS680-280 | 2.80 | 0.0028 | High-speed digital, RF/microwave |
PTFE (Teflon) | 2.1 | 0.0002 | Ultra-low-loss, high-frequency |
RF PCB Layout Techniques
Impedance Matching and Controlled Impedance
Impedance matching is essential for ensuring maximum power transfer and minimizing reflections in RF circuits. Controlled impedance techniques, such as microstrip and stripline, are used to maintain a consistent characteristic impedance throughout the transmission lines.
Microstrip Transmission Lines
Microstrip is a popular transmission line structure for RF PCBs. It consists of a conductive trace on the top layer of the PCB, with a ground plane on the bottom layer. The characteristic impedance of a microstrip line is determined by the trace width, height above the ground plane, and the dielectric constant of the substrate.
Stripline Transmission Lines
Stripline is another transmission line structure that offers better EMI shielding compared to microstrip. In stripline, the signal trace is sandwiched between two ground planes, providing a more uniform dielectric environment. The characteristic impedance of a stripline is determined by the trace width, the distance between the ground planes, and the dielectric constant of the substrate.
Grounding and Shielding Techniques
Proper grounding and shielding are critical for minimizing EMI and ensuring signal integrity in RF PCBs. Some key techniques include:
- Ground Planes: Use solid ground planes to provide a low-impedance return path for high-frequency signals.
- Via Stitching: Place vias along the edges of ground planes to create a Faraday cage and reduce EMI.
- Shielding: Use shielding cans or conductive coatings to isolate sensitive RF components from external interference.
Component Placement and Routing
When placing and routing components on an RF PCB, consider the following guidelines:
- Keep RF signal paths as short as possible to minimize losses and reflections.
- Avoid sharp bends in transmission lines, as they can cause impedance discontinuities.
- Separate RF and digital circuits to minimize crosstalk and interference.
- Use symmetrical layout for differential signals to maintain signal balance.
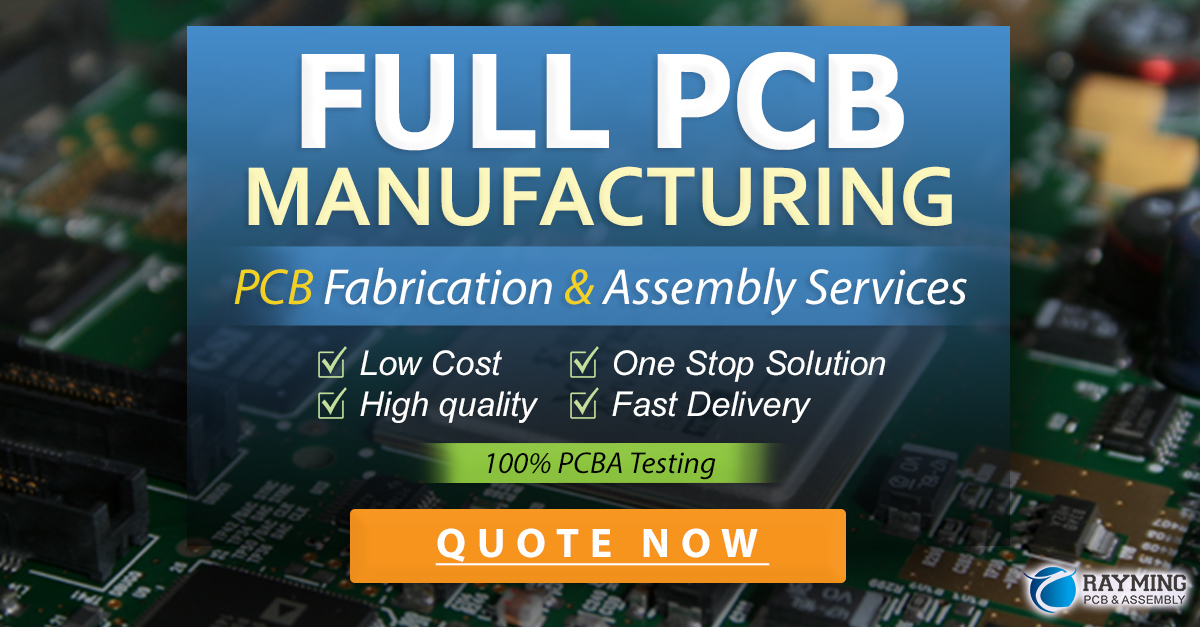
RF PCB Simulation and Optimization
Electromagnetic (EM) Simulation Tools
EM simulation tools, such as Ansys HFSS and Keysight ADS, are essential for analyzing and optimizing RF PCB designs. These tools allow designers to simulate the electromagnetic behavior of the PCB and identify potential issues before fabrication.
Parametric Optimization
Parametric optimization involves iteratively adjusting design parameters, such as trace widths and component values, to achieve the desired RF performance. EM simulation tools often include optimization capabilities that can automatically find the optimal design parameters based on user-defined goals and constraints.
RF PCB Manufacturing and Testing
PCB Fabrication Considerations
When manufacturing RF PCBs, it is important to choose a fabrication house that has experience with high-frequency circuits. Some key considerations include:
- Tight tolerances for trace widths and spacing to maintain impedance control.
- Smooth copper surfaces to minimize skin effect losses.
- Precise layer registration to ensure proper alignment of signal layers and ground planes.
RF PCB Testing and Validation
After fabrication, RF PCBs must undergo thorough testing and validation to ensure they meet the desired performance specifications. Some common RF PCB tests include:
- S-parameter measurements to characterize impedance matching and signal integrity.
- Spectrum analyzer measurements to assess harmonic distortion and spurious emissions.
- Electromagnetic compatibility (EMC) testing to ensure compliance with regulatory standards.
Frequently Asked Questions (FAQ)
1. What is the difference between RF PCB design and regular PCB design?
RF PCB design deals with high-frequency circuits that require special considerations for impedance matching, signal integrity, and EMI, while regular PCB design focuses on lower-frequency digital and analog circuits.
2. What are the most common RF PCB materials?
The most common RF PCB materials include FR-4, Rogers RO4003C, Isola IS680-280, and PTFE (Teflon). The choice of material depends on the specific application, frequency range, and performance requirements.
3. What is the purpose of impedance matching in RF PCB design?
Impedance matching ensures maximum power transfer and minimizes reflections in RF circuits. It is essential for maintaining signal integrity and preventing signal distortion.
4. How can I reduce electromagnetic interference (EMI) in my RF PCB design?
To reduce EMI in RF PCB designs, use solid ground planes, via stitching, and shielding techniques such as shielding cans or conductive coatings. Proper grounding and shielding help to isolate sensitive RF components from external interference.
5. What are the key considerations when manufacturing RF PCBs?
When manufacturing RF PCBs, it is important to choose a fabrication house with experience in high-frequency circuits. Key considerations include tight tolerances for trace widths and spacing, smooth copper surfaces, and precise layer registration to ensure proper impedance control and signal integrity.
Conclusion
RF PCB design is a complex and challenging field that requires a deep understanding of high-frequency electronics, electromagnetic principles, and PCB manufacturing processes. By following the guidelines and best practices outlined in this ultimate guide, you can effectively design, simulate, and optimize RF PCBs for a wide range of applications. Remember to carefully consider factors such as impedance matching, signal integrity, EMI, and material selection throughout the design process, and work closely with experienced RF PCB fabrication houses to ensure successful manufacturing and testing of your designs.
Leave a Reply