Printed circuit boards (PCBs) are laminated sheets used to mechanically support and electrically connect electronic components using conductive pathways etched from copper sheets bonded to a non-conductive substrate. The thickness of the copper layers in a PCB can vary based on the current requirements and application. This article will explore the different copper weights used in PCBs and discuss the thickest copper available.
Copper Thickness in PCBs
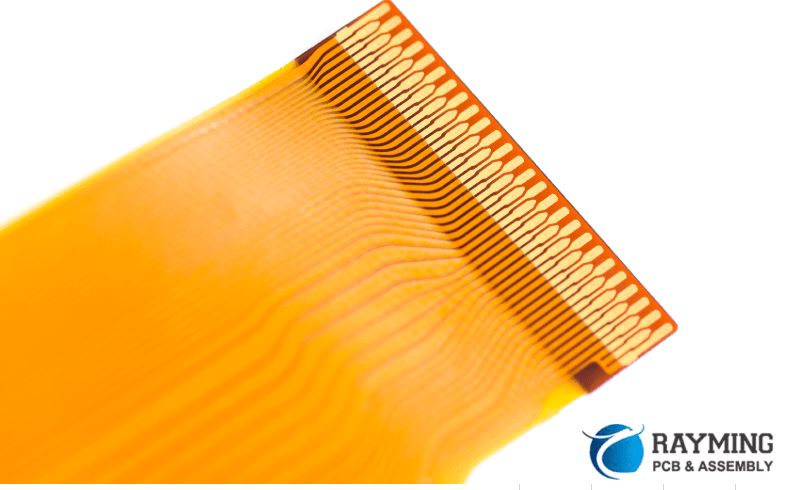
The copper thickness used in PCBs is generally measured in ounces per square foot or micrometers. Some common copper weights include:
1 oz Copper (35 μm)
- The thinnest and most common copper thickness used.
- Provides moderate current capacity.
- Used for simple circuits and cost-sensitive applications.
2 oz Copper (70 μm)
- Allows higher current capacity than 1 oz.
- Used for more complex circuit designs.
3 oz Copper (105 μm)
- Can handle significantly higher currents.
- Used when high power is needed.
- Heavier and more expensive than thinner copper.
4 oz Copper (140 μm)
- Very heavy copper for high current uses.
- Significantly more expensive than thinner copper.
- Mainly used for special applications like power circuits.
What is the Thickest Copper Available?
The thickest copper foils used in PCB fabrication can be up to 6 oz (210 μm) or even 8 oz (280 μm). However, these ultra-thick coppers are rare and used only for specialized high power applications.
6 oz Copper (210 μm)
- Extremely heavy copper for very high current capacity.
- Much more expensive than 2-4 oz copper.
- Significantly increases PCB thickness and weight.
- Used for high power devices like motor controllers.
8 oz Copper (280 μm)
- The maximum thickness copper available for PCBs.
- Restricted for extremely demanding high power uses.
- Very costly.
- Results in an extremely thick and heavy PCB.
- Mainly for niche applications like power distribution.
Here is a summary table of common PCB copper thicknesses:
Copper Thickness | Ounces per sq. ft | Micrometers | Typical Uses |
---|---|---|---|
1 oz | 35 μm | Simple circuits, cost-sensitive designs | |
2 oz | 70 μm | More complex circuits | |
3 oz | 105 μm | High current capacity | |
4 oz | 140 μm | Very high current, specialty uses | |
6 oz | 210 μm | Extremely high current, motor controllers | |
8 oz | 280 μm | Maximum thickness, power distribution |
When is Thick Copper Needed in a PCB?
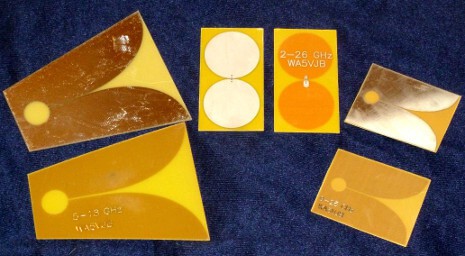
Using the thickest copper like 6 oz or 8 oz is not always ideal, even for high power designs. Here are some factors to consider when choosing PCB copper thickness:
- Current Requirements – Thicker copper is needed for traces carrying higher amperage. Calculate expected currents to determine minimum thickness.
- Thermal Loads – Thick copper helps conduct heat away from hot components. Useful for devices with high power dissipation.
- Number of Layers – A 6-8 layer PCB with 2 oz copper may handle power better than a 2 layer board with 6 oz copper.
- Component Density – More space between components allows trace widths to increase, reducing need for thick copper.
- Budget/Cost – Thick copper PCBs become exponentially more expensive. Determine if benefits outweigh costs.
- Board Thickness – Ultra-thick copper significantly increases board thickness. Ensure mechanical clearances are adequate.
- Board Weight – A PCB with 6-8 oz copper can be 2-3 times heavier than one with 1-2 oz. Account for increased weight in product design.
- Fabrication Factors – Thicker copper requires specialized PCB fabrication processes. Verify manufacturer capabilities and lead times.
Pros and Cons of Using Thick Copper PCBs
Below are some key advantages and disadvantages of using thick copper PCBs:
Advantages
- Handles very high currents and power levels
- Provides excellent thermal performance
- Allows for thinner PCB stacks in some cases
- Removes need for wide copper areas or gold plating to manage current
- Reduces impedance for high frequency applications
Disadvantages
- Much higher cost than standard 1-2 oz copper PCBs
- Increases PCB thickness and weight
- May require special fabrication processes
- Can cause measurability issues during manufacturing
- Excessive thickness can negatively impact soldering, drilling
- Thicker copper layers limit number of trace layers for a given thickness PCB stackup
Key Takeaways on Maximum Copper Thickness
- Standard PCB copper weights are 1, 2, and 3 oz per square foot or approximately 35, 70, and 105 μm respectively.
- The thickest copper foils used for PCB fabrication are 6 oz (210 μm) and 8 oz (280 μm).
- Ultra-thick copper like 6-8 oz is restricted to specialized, high power applications due to expense and manufacturing challenges.
- Multiple factors like current, thermal loads, layer count, and cost impact the decision to use thick copper PCBs.
- Thick copper PCBs handle extremely high power but also increase weight, cost, and fabrication difficulty significantly.
Frequently Asked Questions
What is the thickest copper that can be etched on a PCB?
The thickest copper foil that PCB fabricators can reliably etch is around 6 oz (210 μm). 8 oz copper is very difficult to etch and only used in specialized cases. The thickness that can be etched is also dependent on the PCB manufacturer’s capabilities.
Is there a performance benefit to using thicker copper?
Yes, thicker copper provides substantially improved electrical and thermal performance. It can handle higher currents and power levels. And it conducts heat away from components more effectively. This improves PCB reliability under high power loads.
Does thicker copper increase PCB cost?
Yes, copper PCB cost increases exponentially with thickness. A 2 oz copper PCB may cost 20% more than 1 oz, while 6 oz copper may cost 5-10x times the cost of 1 oz. Thick copper PCBs also often require longer lead times.
Can you solder components on 8 oz copper PCBs?
Soldering on ultra-thick 8 oz copper is possible but more challenging. The thick copper acts as a heat sink making it harder for the solder to reflow. Thicker PCBs may require adjustments to soldering process parameters or pre-heating to ensure good solder joints.
Is there a downside to using thick copper PCBs?
Thick copper PCBs are harder to manufacture and can cause issues like drilling smear if not done properly. They are also much heavier and thicker than standard PCBs. Board handling, connectors, clearances need consideration. And thermal expansion differences between thick copper and the dielectric material can induce mechanical stresses.
Leave a Reply