Introduction to PCB Current Calculators
A printed circuit board (PCB) is a fundamental component in most modern electronic devices. It mechanically supports and electrically connects electronic components using conductive tracks, pads, and other features etched from one or more sheet layers of copper laminated onto and/or between sheet layers of a non-conductive substrate.
One critical aspect of PCB design is ensuring that the traces on the board can handle the required current without overheating or failing. This is where a PCB current calculator comes into play. A PCB current calculator is a tool that helps designers determine the appropriate trace width for a given current, taking into account factors such as copper thickness, temperature rise, and trace length.
Why Use a PCB Current Calculator?
Using a PCB current calculator is essential for several reasons:
-
Ensuring reliability: By selecting the appropriate trace width, designers can ensure that the PCB will function reliably over its intended lifespan, without traces overheating or failing due to excessive current.
-
Optimizing space: PCBs often have limited space, and using a current calculator allows designers to select the minimum trace width required, thus saving space for other components or features.
-
Meeting safety standards: Many industries have specific safety standards that dictate the maximum allowable current for a given trace width. Using a current calculator helps designers ensure compliance with these standards.
-
Saving time and resources: Without a current calculator, designers would need to manually calculate trace widths or rely on trial and error, which can be time-consuming and waste resources.
How PCB Current Calculators Work
PCB current calculators work by taking into account several key factors that affect a trace’s ability to handle current:
Factors Affecting Current Capacity
-
Trace width: Wider traces can handle more current than narrower traces, as they have lower resistance and can dissipate heat more effectively.
-
Copper thickness: PCBs use copper foil of varying thicknesses, typically measured in ounces per square foot (oz/ft²). Thicker copper can handle more current than thinner copper.
-
Temperature rise: As current flows through a trace, it generates heat. The maximum allowable temperature rise depends on the PCB material, components, and operating environment.
-
Trace length: Longer traces have higher resistance than shorter traces, which can affect their current-carrying capacity.
-
Ambient temperature: The temperature of the environment in which the PCB will operate affects its ability to dissipate heat and, thus, its current-carrying capacity.
Calculation Methods
PCB current calculators use various methods to determine the appropriate trace width for a given current. The most common methods are:
-
IPC-2221 standard: The IPC (Institute for Printed Circuits) provides a set of standards for PCB design, including a method for calculating trace widths based on current, copper thickness, and temperature rise.
-
Ohm’s Law: Some calculators use Ohm’s Law (I = V / R) to determine the resistance of a trace based on its width, thickness, and length, and then calculate the maximum current based on the allowable temperature rise.
-
Empirical data: Some calculators use empirical data from real-world tests to determine the current-carrying capacity of traces under various conditions.
Using a PCB Current Calculator
To use a PCB current calculator, designers typically need to input the following information:
-
Current: The maximum current the trace is expected to carry, in amps (A).
-
Copper thickness: The thickness of the copper foil used in the PCB, typically in ounces per square foot (oz/ft²) or millimeters (mm).
-
Temperature rise: The maximum allowable temperature rise above ambient, in degrees Celsius (°C) or Fahrenheit (°F).
-
Trace length (optional): Some calculators take into account the length of the trace, as longer traces have higher resistance.
-
Ambient temperature (optional): Some calculators factor in the ambient temperature of the PCB’s operating environment.
Once this information is entered, the calculator will output the minimum trace width required to safely carry the specified current under the given conditions. Designers can then use this information to create traces that meet or exceed the minimum width.
Example Calculation
Let’s walk through an example calculation using a hypothetical PCB current calculator:
- Current: 2 A
- Copper thickness: 1 oz/ft²
- Temperature rise: 10 °C
- Trace length: 50 mm
- Ambient temperature: 25 °C
After inputting this information, the calculator might output a minimum trace width of 0.8 mm. This means that to safely carry 2 A of current under these conditions, the trace must be at least 0.8 mm wide.
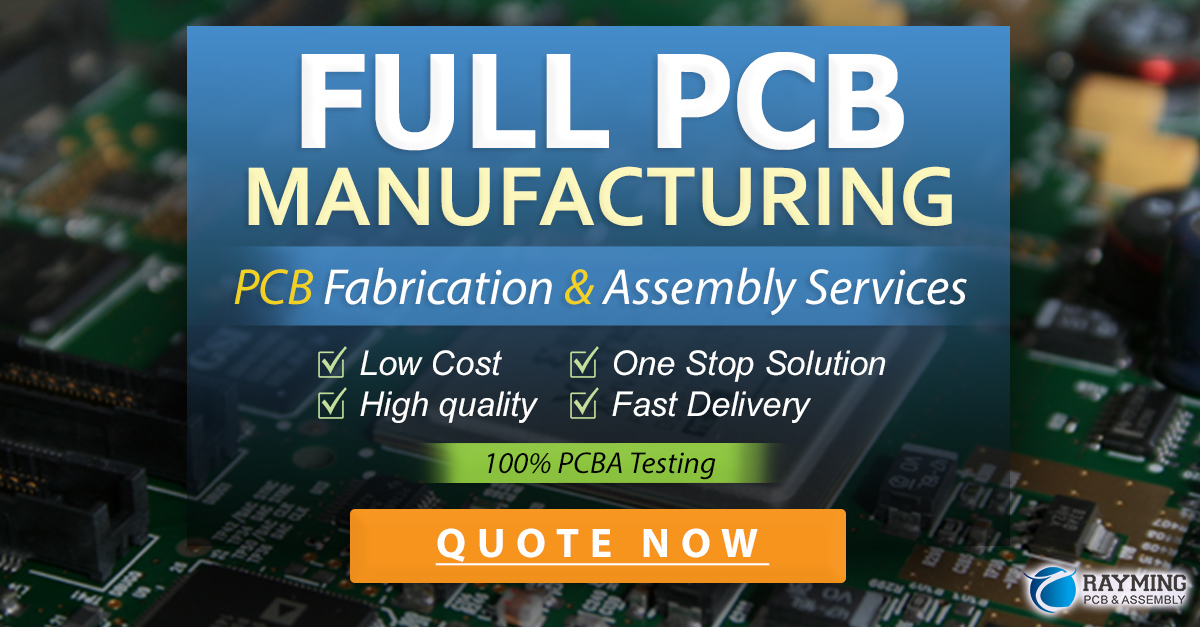
PCB Current Calculator Tables
Many PCB current calculators also provide tables that show the current-carrying capacity of traces at various widths and copper thicknesses. These tables can be a useful reference for designers, as they allow for quick lookup of trace width requirements without the need for manual calculations.
Here’s an example table showing the current-carrying capacity of traces at different widths and copper thicknesses, assuming a 10 °C temperature rise:
Trace Width (mm) | 0.5 oz/ft² | 1 oz/ft² | 2 oz/ft² | 3 oz/ft² |
---|---|---|---|---|
0.25 | 0.5 A | 0.7 A | 1.0 A | 1.2 A |
0.50 | 1.0 A | 1.4 A | 2.0 A | 2.4 A |
0.75 | 1.5 A | 2.1 A | 3.0 A | 3.6 A |
1.00 | 2.0 A | 2.8 A | 4.0 A | 4.8 A |
1.25 | 2.5 A | 3.5 A | 5.0 A | 6.0 A |
1.50 | 3.0 A | 4.2 A | 6.0 A | 7.2 A |
Designers can use tables like this to quickly determine the minimum trace width required for a given current and copper thickness, without the need for manual calculations.
Factors to Consider When Using a PCB Current Calculator
While PCB current calculators are a valuable tool for designers, there are several factors to consider when using them:
-
Safety margins: It’s generally a good idea to design traces with some safety margin, rather than using the absolute minimum width required. This provides a buffer against unexpected current spikes or environmental conditions.
-
High-frequency signals: Traces carrying high-frequency signals may require wider widths to minimize signal integrity issues, even if the current is relatively low.
-
Thermal management: In some cases, traces may need to be wider than the minimum required for current-carrying capacity in order to effectively dissipate heat from components.
-
Manufacturing limitations: Some PCB fabrication processes may have minimum trace width limitations that need to be taken into account.
-
Cost: Using wider traces than necessary can increase the overall size and cost of the PCB.
By considering these factors in addition to the results of a PCB current calculator, designers can create traces that are optimized for reliability, performance, and cost-effectiveness.
FAQ
1. How accurate are PCB current calculators?
PCB current calculators are generally quite accurate, as they are based on established standards and empirical data. However, they should be used as a starting point for design, and the results should be verified through testing and simulation.
2. Can I use a PCB current calculator for flexible PCBs?
Yes, most PCB current calculators can be used for both rigid and flexible PCBs. However, flexible PCBs may have additional design considerations, such as the need for strain relief and the effects of bending on trace resistance.
3. What happens if I use a trace that is too narrow for the current?
Using a trace that is too narrow for the current it needs to carry can lead to several problems, including:
- Overheating: The trace may overheat and cause damage to the PCB, components, or surrounding materials.
- Voltage drop: The increased resistance of a narrow trace can cause a voltage drop, which may affect the performance of connected components.
- Failure: In extreme cases, the trace may fail entirely, causing an open circuit and potentially rendering the PCB non-functional.
4. Can I use a PCB current calculator for traces on inner layers?
Yes, PCB current calculators can be used for traces on any layer of a multi-layer PCB. However, inner layers may have different thermal characteristics than outer layers, which should be taken into account when interpreting the results.
5. Are there any limitations to using a PCB current calculator?
While PCB current calculators are a valuable tool, they do have some limitations:
- They do not account for all possible design factors, such as high-frequency effects or thermal management.
- They may not take into account the specific requirements of certain industries or applications, such as aerospace or medical devices.
- They should be used as a starting point for design, but the results should always be verified through testing and simulation.
Despite these limitations, PCB current calculators remain an essential tool for any PCB designer looking to create reliable, high-performance circuit boards.
Conclusion
PCB current calculators are a valuable tool for designers looking to create reliable, high-performance circuit boards. By taking into account factors such as trace width, copper thickness, temperature rise, and trace length, these calculators help designers determine the appropriate trace dimensions for a given current, ensuring that the PCB will function safely and reliably over its intended lifespan.
When using a PCB current calculator, designers should consider factors such as safety margins, high-frequency effects, thermal management, manufacturing limitations, and cost. By combining the results of a current calculator with good design practices and thorough testing, designers can create PCBs that are optimized for reliability, performance, and cost-effectiveness.
As PCB design continues to evolve, with ever-increasing demands for higher speeds, smaller sizes, and greater reliability, tools like PCB current calculators will remain essential for designers looking to stay ahead of the curve. By understanding how these calculators work and how to use them effectively, designers can create PCBs that meet the needs of even the most demanding applications.
Leave a Reply