Introduction to the PCB Current Calculator
A printed circuit board (PCB) is a essential component in most modern electronic devices. It mechanically supports and electrically connects electronic components using conductive tracks, pads and other features etched from one or more sheet layers of copper laminated onto and/or between sheet layers of a non-conductive substrate.
One of the most important aspects of PCB design is ensuring the copper traces that carry signals between components can handle the required current without overheating or failing over time. This is where a PCB current calculator comes in. A PCB current calculator allows designers to input key parameters and calculate the maximum allowable current for a given copper trace width and thickness.
In this article, we’ll take an in-depth look at what a PCB current calculator is, how it works, and provide some examples of using one for PCB design. We’ll also answer some frequently asked questions about PCB current capacity and using these handy calculators.
How Much Current Can a PCB Trace Handle?
Before diving into the details of a PCB current calculator, it’s important to understand the factors that determine how much current a copper trace on a PCB can safely carry. The current carrying capacity of a PCB trace depends on:
- The cross-sectional area of the trace (width and thickness)
- The allowable temperature rise
- The thermal conductivity of the copper and PCB substrate material
- Environmental factors like ambient temperature
In general, wider and thicker traces can handle more current than narrower and thinner ones. This is because they have lower resistance and more area to dissipate heat. The resistance of a conductor is inversely proportional to its cross-sectional area.
The allowable temperature rise is how much hotter the trace can get compared to the ambient temperature before it starts to degrade or damage the PCB. For standard FR-4 PCB material, the temperature rise is usually limited to 10-20°C above ambient. Beyond that, the substrate material may start to break down or delaminate.
Copper is an excellent conductor of both electricity and heat. The more thermally conductive the PCB substrate material is, the more efficiently it can spread and dissipate the heat generated by current flowing through the copper traces. FR-4 is the most common PCB material and has decent thermal properties, but high performance substrates like ceramic or metal core PCBs are sometimes used for high current applications.
Finally, the environment the PCB will be used in makes a difference. In hot environments, there is less “thermal headroom” for a temperature rise in the traces before hitting the safe limit. Copper traces can handle more current in cooler environments.
What is a PCB Current Calculator?
A PCB current calculator is a tool that takes in the relevant parameters and calculates the maximum current a PCB trace can handle. The simplest calculators take the trace width and thickness as inputs and output a maximum current based on empirical data or rules of thumb.
More advanced calculators may allow you to specify the copper weight (thickness), ambient temperature, allowable temp rise, and number of layers the trace is on (inner vs outer layers). Some also calculate voltage drop along the length of the trace and power loss.
The IPC, the global trade association representing the printed board and electronics assembly industries, publishes current carrying capacity tables in standard IPC-2221. Many PCB current calculators implement these tables. However, the IPC specs are conservative, and some more aggressive designers use calculators based on real-world testing data that allows for higher currents.
Some PCB design software, like EagleCAD, has built-in trace current calculators. There are also many online calculators available for free. We’ll provide links to some popular ones at the end of this article.
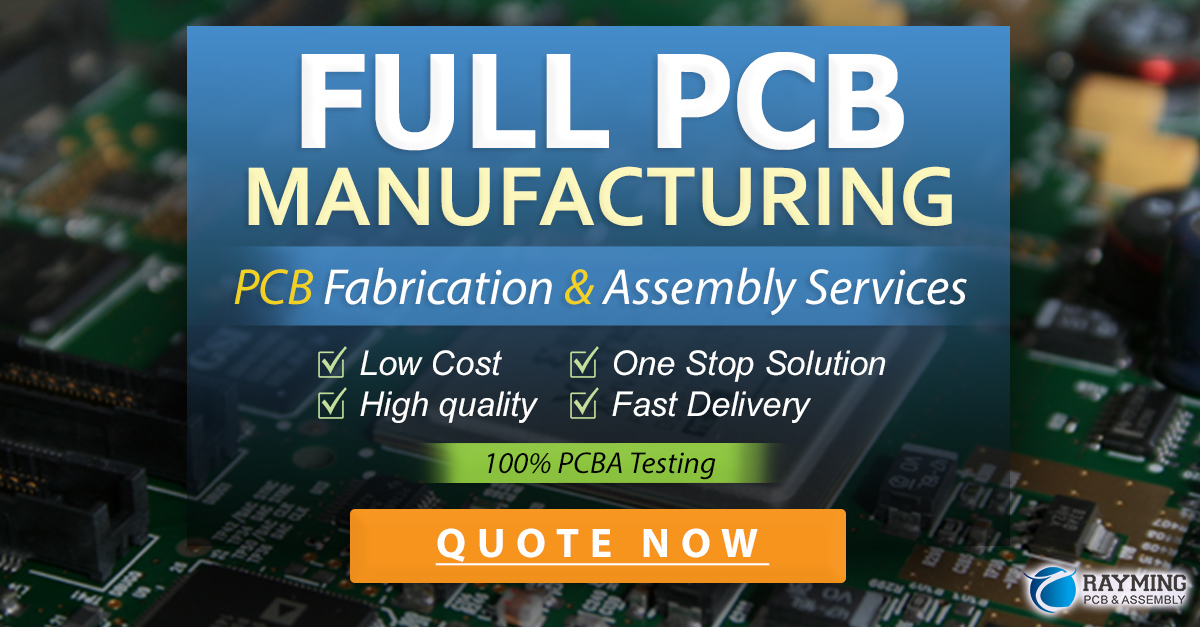
How to Use a PCB Current Calculator
Using a PCB current calculator is fairly straightforward. The exact inputs will vary based on the particular calculator, but in general you need to provide:
- Trace width (usually in mils or mm)
- Copper weight or thickness (in ounces per square foot or microns)
- Ambient temperature (°C or °F)
- Allowable temperature rise (°C or °F)
- Whether the trace is on an internal or external layer
Some calculators will have additional options, like the ability to select the substrate material if it’s not the standard FR-4.
Once you input these parameters, the calculator will give you a maximum current value in amps. It’s important to note that this is a theoretical maximum based on a steady state current. In reality, you should derate this value by 20% or more for safety margin, especially if the current is not steady or the PCB will be subject to vibrations or physical stress.
Many calculators will also show you the resistance and voltage drop of the trace at the maximum current. This can be useful for ensuring your power supply can maintain the required voltage at the load.
PCB Current Calculator Example
Let’s walk through an example of using a PCB current calculator. We’ll use the free online calculator at 4PCB.com.
Suppose we need to power an LED strip that draws 5A at 12V. We want to know what size trace we need on a 2-layer PCB. The ambient temperature inside the device enclosure will be around 40°C, and we’ll allow a 15°C temperature rise. The PCB will use standard 1oz copper on FR-4.
Plugging these values into the calculator, with a trace length of 50mm, we get the following result:
Copper Weight | Trace Width | Trace Thickness | Current Capacity |
---|---|---|---|
1 oz | 50 mil | 1.37 mil | 5.8 A |
The calculator recommends a 50mil (1.27mm) wide trace for our 5A current. It also shows that this trace will have a resistance of 1.67mΩ and a 0.01V drop at 5A.
If space is tight on our PCB, we could consider using 2oz copper instead. Punching in the same numbers but with 2oz copper gives us:
Copper Weight | Trace Width | Trace Thickness | Current Capacity |
---|---|---|---|
2 oz | 25 mil | 2.74 mil | 6.2 A |
With 2oz copper, we can use a much narrower 25mil (0.64mm) trace for our 5A current. The tradeoff is higher cost for the thicker copper PCB.
Frequently Asked Questions about PCB Current Calculators
How accurate are PCB current calculators?
PCB current calculators give a theoretical maximum based on simplified models and empirical data. They don’t take into account all real-world factors. Always derate the calculated current by at least 20% for safety margin.
What happens if I exceed the maximum current spec for a trace?
Putting too much current through a trace will cause it to heat up. Minor overloading may just cause a voltage drop and reduced efficiency. Significant overloading will cause the trace to overheat and either burn up like a fuse or delaminate from the PCB substrate. In extreme cases it could cause a fire.
Why are the external layer traces rated for more current than internal?
Traces on the outer layers of a PCB can dissipate heat better than inner layer traces which are sandwiched between layers of FR-4. The outer layer traces have more area exposed to air.
What if my PCB current calculator doesn’t have my substrate material listed?
The substrate material affects the current capacity through its thermal conductivity and maximum temperature spec. If using an exotic substrate not listed in the calculator, your best bet is to find its datasheet and look up the thermal properties, then choose the available material that is the closest match.
Can I just use the widest possible traces everywhere to be safe?
Using oversized traces is inefficient and can actually cause signal integrity issues at high frequencies. It’s best to size each trace for the current it needs to carry, with an appropriate safety margin. Also at some point wider traces don’t help, as the current capacity is limited by the thickness of the copper.
Conclusion
Sizing the traces on a PCB correctly is critical for both performance and long-term reliability. A PCB current calculator makes this complex task quicker and easier. By entering just a few key parameters about your PCB stackup and operating conditions, you can ensure your copper traces will be robust enough to handle the current your circuit demands.
Always remember to be conservative and leave margin for real-world conditions that may not be modeled by the calculator. When in doubt, it’s best to prototype your design and test it under the expected operating conditions to validate the trace sizing.
Further Reading
To learn more about PCB current capacity and using these calculators, check out these resources:
- IPC-2221 Generic Standard on Printed Board Design
- Saturn PCB Toolkit Current Carrying Capacity Calculator
- EEVblog #1176 – PCB Trace Current Capacity
- Altium PCB Design Tutorial – Current Carrying Capacity
Leave a Reply