Overview of Rogers and Teflon PCB Materials
Rogers PCB Materials
Rogers Corporation is a leading manufacturer of high-frequency laminate materials for PCBs. Their products are known for their exceptional electrical properties, low dielectric loss, and stable performance over a wide range of frequencies and temperatures. Rogers materials are commonly used in applications such as:
- Wireless communication systems
- Radar and satellite technology
- Automotive electronics
- Medical devices
- Aerospace and defense systems
Some popular Rogers PCB materials include:
- RO4000 Series: A hydrocarbon ceramic laminate with low dielectric constant and loss, suitable for high-frequency applications up to 18 GHz.
- RO3000 Series: A ceramic-filled PTFE composite with excellent thermal stability and low moisture absorption, ideal for microwave and RF applications.
- RT/duroid Series: A PTFE-based laminate with low dielectric constant and loss, offering superior high-frequency performance and dimensional stability.
Teflon PCB Materials
Teflon, or polytetrafluoroethylene (PTFE), is a synthetic fluoropolymer known for its excellent chemical resistance, low friction, and high-temperature stability. Teflon PCB materials offer several advantages, including:
- High dielectric strength and low dissipation factor
- Excellent moisture resistance and hydrophobicity
- Wide operating temperature range (-200°C to +260°C)
- Low flammability and smoke generation
- Good mechanical strength and flexibility
Teflon PCBs are commonly used in applications such as:
- Aerospace and military systems
- Medical devices and equipment
- Industrial control and automation
- High-frequency communication systems
Key Differences Between Rogers and Teflon PCBs
Dielectric Properties
One of the primary differences between Rogers and Teflon PCBs lies in their dielectric properties. Dielectric constant (Dk) and dissipation factor (Df) are two essential parameters that affect the electrical performance of a PCB.
- Rogers materials generally have lower dielectric constants (2.2 to 10.2) compared to Teflon (2.1 to 2.6), which allows for better signal integrity and lower signal attenuation at high frequencies.
- Rogers materials also exhibit lower dissipation factors (0.0009 to 0.0030) than Teflon (0.0002 to 0.0005), meaning they have lower dielectric loss and better power handling capabilities.
The following table compares the dielectric properties of some popular Rogers and Teflon PCB materials:
Material | Dielectric Constant (Dk) | Dissipation Factor (Df) |
---|---|---|
Rogers RO4350B | 3.48 | 0.0037 |
Rogers RO3003 | 3.00 | 0.0013 |
Rogers RT/duroid 5880 | 2.20 | 0.0009 |
Teflon PTFE | 2.1 | 0.0002 |
Thermal Properties
Thermal management is crucial for PCBs operating in high-temperature environments or handling high-power applications. Rogers and Teflon materials differ in their thermal properties, which can impact their suitability for specific applications.
- Rogers materials generally have higher thermal conductivity (0.6 to 1.7 W/mK) compared to Teflon (0.25 to 0.30 W/mK), allowing for better heat dissipation and thermal management.
- Teflon materials have a wider operating temperature range (-200°C to +260°C) than Rogers materials (-50°C to +260°C), making them suitable for extreme temperature environments.
The table below compares the thermal properties of Rogers and Teflon PCB materials:
Material | Thermal Conductivity (W/mK) | Operating Temperature Range (°C) |
---|---|---|
Rogers RO4350B | 0.62 | -55 to +280 |
Rogers RO3003 | 0.50 | -55 to +150 |
Rogers RT/duroid 5880 | 0.20 | -55 to +125 |
Teflon PTFE | 0.25 | -200 to +260 |
Mechanical Properties
The mechanical properties of PCB materials determine their durability, flexibility, and ease of fabrication. Rogers and Teflon materials exhibit different mechanical characteristics that can influence their application suitability.
- Teflon materials have lower moisture absorption (0.01% to 0.02%) compared to Rogers materials (0.02% to 0.07%), making them more resistant to environmental humidity and ensuring stable performance over time.
- Rogers materials generally have higher flexural strength (140 to 450 MPa) than Teflon (20 to 40 MPa), which makes them more resistant to bending and mechanical stress.
- Teflon materials have lower coefficient of friction and better surface lubricity compared to Rogers materials, which can be advantageous in applications requiring smooth movement or low wear.
The following table compares the mechanical properties of Rogers and Teflon PCB materials:
Material | Moisture Absorption (%) | Flexural Strength (MPa) | Coefficient of Friction |
---|---|---|---|
Rogers RO4350B | 0.05 | 390 | 0.20 |
Rogers RO3003 | 0.04 | 280 | 0.18 |
Rogers RT/duroid 5880 | 0.02 | 140 | 0.15 |
Teflon PTFE | 0.01 | 20 | 0.05 |
Cost and Availability
Cost and availability are important factors to consider when selecting PCB materials for your project. In general, Rogers materials are more expensive than Teflon due to their advanced composite formulations and superior electrical performance.
- Rogers materials are typically priced 20% to 50% higher than Teflon materials, depending on the specific grade and volume of purchase.
- Teflon materials are more readily available from various suppliers, while Rogers materials may have longer lead times and minimum order quantities.
It’s essential to balance the cost and availability factors with the performance requirements of your application to make an informed decision.
Choosing Between Rogers and Teflon PCBs
When deciding between Rogers and Teflon PCB materials, consider the following factors:
-
Frequency and electrical requirements: If your application operates at high frequencies (above 10 GHz) and demands low dielectric loss, Rogers materials may be the better choice.
-
Temperature and environmental conditions: For extreme temperature environments or applications with strict moisture resistance requirements, Teflon materials may be more suitable.
-
Mechanical requirements: If your PCB will be subject to bending, flexing, or mechanical stress, Rogers materials with higher flexural strength may be preferable.
-
Cost and availability: Evaluate the cost implications and availability of the materials based on your project budget and timeline.
It’s recommended to consult with experienced PCB designers and manufacturers to determine the most appropriate material for your specific application.
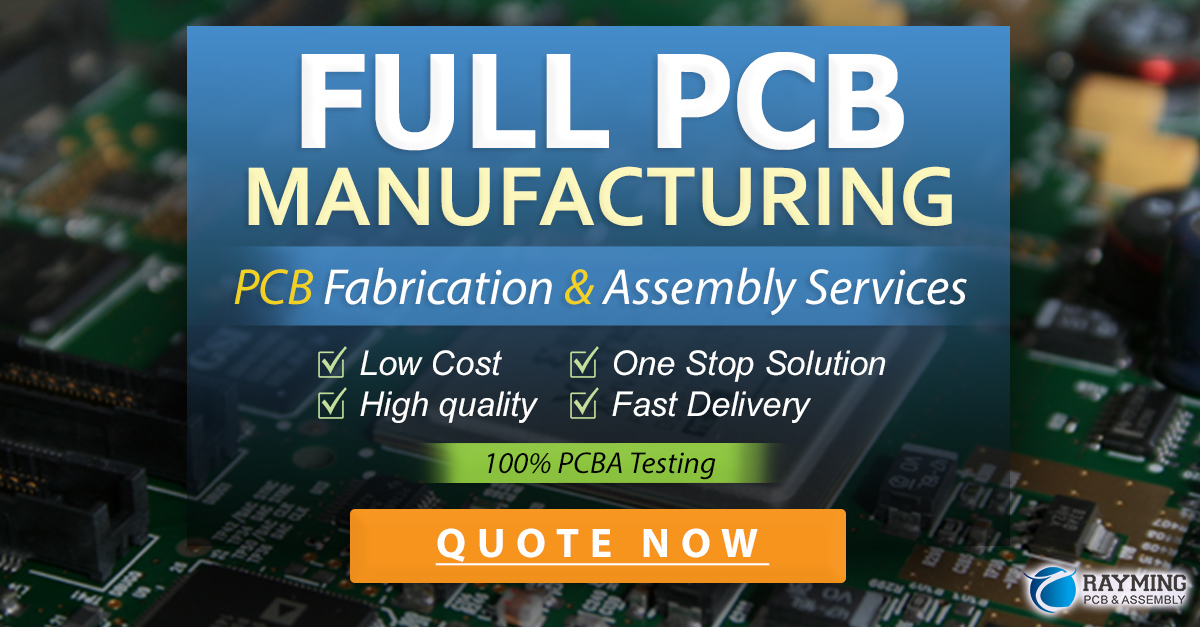
FAQ
-
Q: Can Rogers and Teflon PCB materials be used together in the same PCB stack-up?
A: Yes, Rogers and Teflon materials can be used together in a hybrid PCB stack-up to leverage the unique advantages of each material for different layers or sections of the board. -
Q: Are Rogers and Teflon PCBs suitable for high-power applications?
A: Both Rogers and Teflon materials have good power handling capabilities due to their low dielectric loss and high thermal stability. However, Rogers materials generally have better thermal conductivity, which can be advantageous for high-power applications. -
Q: How do Rogers and Teflon materials compare in terms of signal integrity?
A: Rogers materials typically offer better signal integrity performance due to their lower dielectric constant and dissipation factor, which results in lower signal attenuation and distortion at high frequencies. -
Q: Are there any special considerations for fabricating PCBs with Rogers or Teflon materials?
A: Yes, both Rogers and Teflon materials require specialized fabrication processes and equipment due to their unique properties. It’s essential to work with experienced PCB manufacturers who have the knowledge and capabilities to handle these materials effectively. -
Q: Can Rogers and Teflon PCBs be used for flexible or rigid-flex applications?
A: Teflon materials are more suitable for flexible and rigid-flex PCBs due to their lower flexural modulus and better mechanical flexibility. Rogers materials are generally used for rigid PCB applications where mechanical stability and strength are prioritized.
Conclusion
Rogers and Teflon PCB materials offer distinct advantages for high-performance applications requiring excellent electrical, thermal, and mechanical properties. While Rogers materials excel in high-frequency and low-loss applications, Teflon materials are known for their exceptional chemical resistance, wide temperature range, and moisture resistance.
When selecting between Rogers and Teflon PCBs, it’s crucial to carefully consider your application requirements, performance targets, and budget constraints. Engaging with experienced PCB design and manufacturing partners can help you make an informed decision and ensure the successful realization of your project.
As technology continues to advance, both Rogers and Teflon materials will play a vital role in enabling the next generation of electronic devices and systems across various industries.
Leave a Reply