What is Rogers PCB?
Rogers PCB, also known as Rogers Printed Circuit Board, is a high-performance substrate material used in the manufacturing of printed circuit boards (PCBs). These PCBs are specifically designed to cater to high-frequency and high-speed applications, such as telecommunications, aerospace, defense, and medical industries.
Rogers Corporation, the company behind Rogers PCB, has been a leading manufacturer of advanced materials for over 180 years. They offer a wide range of PCB materials, including high-frequency laminates, bondplys, and prepregs, which are used to fabricate reliable and high-quality PCBs.
Advantages of Rogers PCB
-
Low Dielectric Loss: Rogers PCB materials have a low dielectric constant (Dk) and low dissipation factor (Df), which minimizes signal loss and ensures excellent signal integrity at high frequencies.
-
High Thermal Conductivity: The high thermal conductivity of Rogers PCB materials allows for efficient heat dissipation, preventing overheating and ensuring the long-term reliability of the circuit board.
-
Dimensional Stability: Rogers PCB materials maintain their dimensions and properties over a wide range of temperatures and humidity levels, ensuring consistent performance in various environmental conditions.
-
Excellent Mechanical Properties: Rogers PCB materials offer superior mechanical strength, flexibility, and durability, making them suitable for applications that require high reliability and long-term performance.
-
Wide Range of Materials: Rogers Corporation offers a diverse portfolio of PCB materials, allowing designers to select the most suitable material for their specific application requirements.
Common Rogers PCB Materials
Rogers Corporation offers several popular PCB materials, each with unique properties and benefits. Some of the most widely used Rogers PCB materials include:
-
RT/duroid®: This series of high-frequency laminates is known for its low dielectric loss, excellent thermal stability, and consistent mechanical properties. RT/duroid® is commonly used in applications such as wireless communication, satellite systems, and radar equipment.
-
RO4000®: The RO4000® series is a glass-reinforced hydrocarbon and ceramic laminate with low dielectric loss and a stable dielectric constant. It is suitable for high-frequency applications, such as automotive radar, aerospace, and defense systems.
-
RO3000®: This series of ceramic-filled PTFE composites offers a low dielectric constant and low loss tangent, making it ideal for high-speed digital and RF/microwave applications. RO3000® is often used in wireless communication, automotive, and medical devices.
-
ULTRALAM®: ULTRALAM® is a series of high-performance, liquid crystalline polymer (LCP) based laminates and bondplys. These materials offer excellent electrical and mechanical properties, making them suitable for high-frequency, high-speed, and flexible circuit applications.
Comparison of Rogers PCB Materials
Material | Dielectric Constant (Dk) | Dissipation Factor (Df) | Thermal Conductivity (W/m·K) | Applications |
---|---|---|---|---|
RT/duroid® | 2.2 – 10.2 | 0.0009 – 0.0025 | 0.2 – 0.7 | Wireless communication, radar, satellite |
RO4000® | 3.3 – 3.7 | 0.0027 – 0.0037 | 0.4 – 0.7 | Automotive radar, aerospace, defense |
RO3000® | 3.0 – 10.2 | 0.0010 – 0.0025 | 0.4 – 0.6 | Wireless communication, automotive, medical |
ULTRALAM® | 2.9 – 3.2 | 0.0020 – 0.0050 | 0.2 – 0.4 | High-frequency, high-speed, flexible circuits |
Designing with Rogers PCB
When designing a PCB using Rogers materials, there are several factors to consider to ensure optimal performance and reliability.
Material Selection
Selecting the appropriate Rogers PCB material is crucial for achieving the desired electrical, thermal, and mechanical properties. Designers should consider factors such as the operating frequency, signal integrity requirements, thermal management needs, and environmental conditions when choosing a suitable material.
Stackup Design
The PCB stackup design plays a significant role in determining the electrical performance and signal integrity of the circuit board. When designing with Rogers PCB materials, it is essential to consider the layer arrangement, dielectric thickness, and copper weight to achieve the desired impedance and minimize signal loss.
Thermal Management
Proper thermal management is critical for maintaining the long-term reliability and performance of the PCB. Rogers PCB materials with high thermal conductivity should be selected for applications that generate significant heat. Additionally, designers should incorporate appropriate thermal management techniques, such as the use of thermal vias, heat sinks, and fans, to ensure efficient heat dissipation.
Manufacturing Considerations
Manufacturing PCBs with Rogers materials requires specialized processes and expertise. Designers should collaborate closely with experienced PCB manufacturers who have the necessary knowledge and equipment to handle Rogers materials. Factors such as drilling, plating, and lamination processes should be carefully considered to ensure the quality and reliability of the final product.
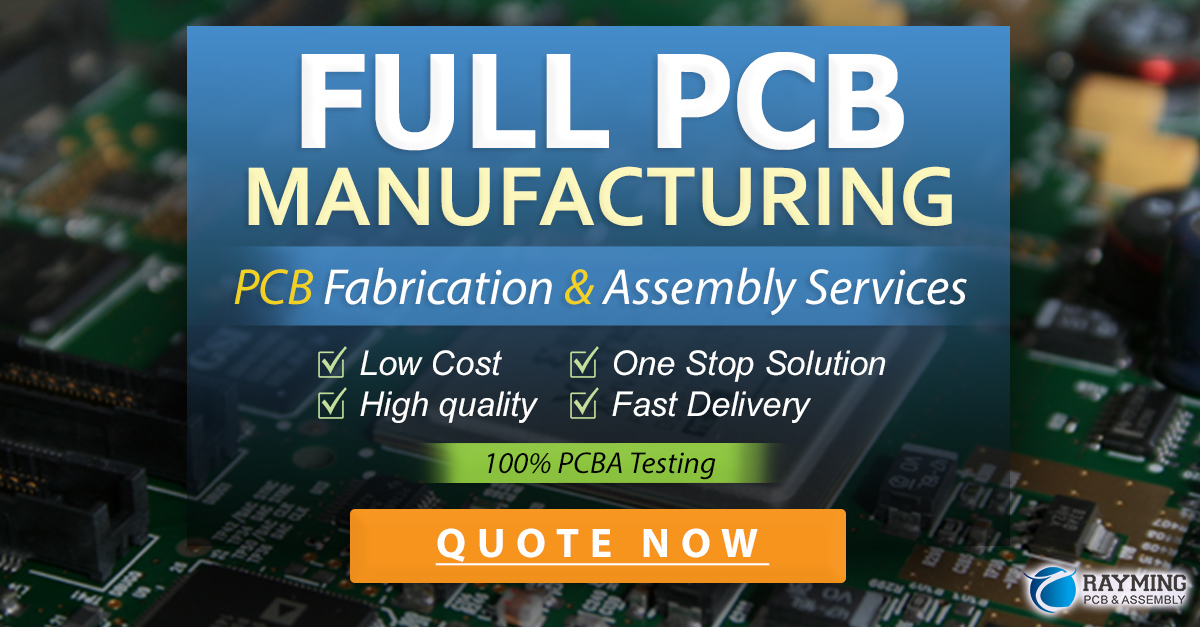
Applications of Rogers PCB
Rogers PCBs are widely used in various industries and applications that demand high-performance, reliability, and signal integrity. Some of the most common applications of Rogers PCB include:
-
Wireless Communication: Rogers PCBs are extensively used in wireless communication systems, such as 5G networks, cellular base stations, and satellite communication equipment, due to their low dielectric loss and excellent high-frequency performance.
-
Automotive: With the increasing adoption of advanced driver assistance systems (ADAS) and autonomous vehicles, Rogers PCBs are used in automotive radar systems, vehicle-to-vehicle (V2V) communication, and vehicle-to-infrastructure (V2I) communication applications.
-
Aerospace and Defense: Rogers PCBs are employed in various aerospace and defense applications, such as avionics, radar systems, missile guidance, and satellite communication, owing to their high reliability, thermal stability, and resistance to harsh environmental conditions.
-
Medical Devices: The low dielectric loss and high-frequency capabilities of Rogers PCBs make them suitable for medical applications, such as MRI systems, high-frequency ultrasound devices, and medical implants.
-
Industrial: Rogers PCBs are used in industrial applications that require high-speed data transmission, such as industrial automation, process control, and test and measurement equipment.
FAQ
-
Q: What is the difference between Rogers PCB and standard FR-4 PCB?
A: Rogers PCB materials offer superior high-frequency performance, lower dielectric loss, and better thermal conductivity compared to standard FR-4 PCB materials. Rogers PCBs are specifically designed for applications that require excellent signal integrity and reliability at high frequencies. -
Q: Can Rogers PCB materials be used for multilayer PCBs?
A: Yes, Rogers PCB materials can be used to fabricate multilayer PCBs. Rogers Corporation offers a range of bonding materials and prepregs that are compatible with their laminates, enabling the construction of high-performance multilayer PCBs. -
Q: Are Rogers PCBs more expensive than standard PCBs?
A: Yes, Rogers PCBs are generally more expensive than standard PCBs due to the advanced materials and specialized manufacturing processes involved. However, the superior performance and reliability offered by Rogers PCBs justify the higher cost for applications that demand high signal integrity and long-term reliability. -
Q: How do I select the right Rogers PCB material for my application?
A: Selecting the appropriate Rogers PCB material depends on various factors, such as the operating frequency, dielectric constant, dissipation factor, thermal conductivity, and mechanical requirements of your application. It is recommended to consult with Rogers Corporation’s technical support team or an experienced PCB designer to determine the most suitable material for your specific needs. -
Q: Can Rogers PCBs be manufactured using standard PCB fabrication processes?
A: While Rogers PCBs can be manufactured using standard PCB fabrication processes, they require specialized expertise and equipment to ensure optimal results. It is essential to work with a PCB manufacturer who has experience in handling Rogers materials and can provide the necessary support and guidance throughout the fabrication process.
Conclusion
Rogers PCBs are high-performance substrate materials that offer excellent electrical, thermal, and mechanical properties for demanding applications in various industries. With their low dielectric loss, high thermal conductivity, and dimensional stability, Rogers PCBs enable the design and fabrication of reliable, high-speed, and high-frequency circuits.
When designing with Rogers PCB materials, it is crucial to consider factors such as material selection, stackup design, thermal management, and manufacturing processes to ensure optimal performance and reliability. By collaborating with experienced PCB manufacturers and leveraging the extensive portfolio of Rogers PCB materials, designers can create cutting-edge solutions for a wide range of applications, including wireless communication, automotive, aerospace, defense, and medical devices.
As technology continues to advance and the demand for high-performance electronics grows, Rogers PCBs will remain a critical component in enabling the development of innovative and reliable products that push the boundaries of performance and functionality.
Leave a Reply