Introduction
When it comes to choosing materials for printed circuit boards (PCBs), two of the most popular options are FR-4 and Rogers materials. While both materials have their advantages and applications, there are significant differences between them that make each suitable for specific types of projects. In this article, we will explore the key differences between FR-4 and Rogers materials, their properties, and their applications in various industries.
What is FR-4 Material?
FR-4 (Flame Retardant 4) is a composite material made from woven fiberglass cloth with an epoxy resin binder. It is the most commonly used material for PCBs due to its excellent mechanical and electrical properties, as well as its affordability.
Properties of FR-4 Material
- Dielectric Constant: FR-4 has a dielectric constant of 4.3 to 4.7 at 1 MHz, which is relatively high compared to other PCB Materials.
- Dissipation Factor: The dissipation factor of FR-4 is around 0.02 at 1 MHz, which is considered good for most applications.
- Thermal Conductivity: FR-4 has a thermal conductivity of 0.3 W/mK, which is relatively low compared to other materials like aluminum or copper.
- Tg (Glass Transition Temperature): The Tg of FR-4 is around 130°C to 140°C, which means it can withstand high temperatures during soldering and other manufacturing processes.
- CTE (Coefficient of Thermal Expansion): FR-4 has a CTE of 13 to 16 ppm/°C in the X and Y axes, and 50 to 70 ppm/°C in the Z axis.
Applications of FR-4 Material
FR-4 is widely used in various industries for its versatility and reliability. Some common applications include:
- Consumer electronics (e.g., smartphones, laptops, televisions)
- Automotive electronics
- Industrial control systems
- Medical devices
- Telecommunications equipment
What is Rogers Material?
Rogers materials are a family of high-performance, engineered materials designed for demanding applications that require superior electrical, thermal, and mechanical properties. These materials are often used in high-frequency and high-speed applications where low dielectric loss and stable dielectric constant are critical.
Types of Rogers Materials
There are several types of Rogers materials, each with its own unique properties and applications. Some of the most common Rogers materials include:
- RO3000 Series: This series is designed for high-frequency applications up to 77 GHz. It offers low dielectric loss, stable dielectric constant, and excellent thermal conductivity.
- RO4000 Series: The RO4000 series is suitable for applications up to 30 GHz and offers low dielectric loss, stable dielectric constant, and good thermal conductivity.
- RT/duroid: RT/duroid materials are PTFE-based composites that offer excellent electrical and mechanical properties for high-frequency applications.
- TMM: TMM (Thermoset Microwave Materials) are ceramic-filled thermoset polymers that provide a low dielectric constant and low loss for high-frequency applications.
Properties of Rogers Materials
The properties of Rogers materials vary depending on the specific type, but in general, they offer:
- Low Dielectric Constant: Rogers materials typically have a dielectric constant ranging from 2.2 to 10.2, depending on the specific material.
- Low Dissipation Factor: The dissipation factor of Rogers materials is generally lower than FR-4, ranging from 0.0009 to 0.003 at 10 GHz.
- High Thermal Conductivity: Some Rogers materials, such as the RO3000 series, have a thermal conductivity of up to 1.44 W/mK, which is significantly higher than FR-4.
- Stable Dielectric Constant: Rogers materials maintain a stable dielectric constant over a wide range of frequencies and temperatures.
- Low CTE: Rogers materials have a lower CTE compared to FR-4, which makes them more suitable for high-reliability applications.
Applications of Rogers Materials
Rogers materials are used in various high-performance applications, such as:
- 5G wireless communication systems
- Automotive radar systems
- Aerospace and defense electronics
- Satellite communications
- High-speed digital circuits
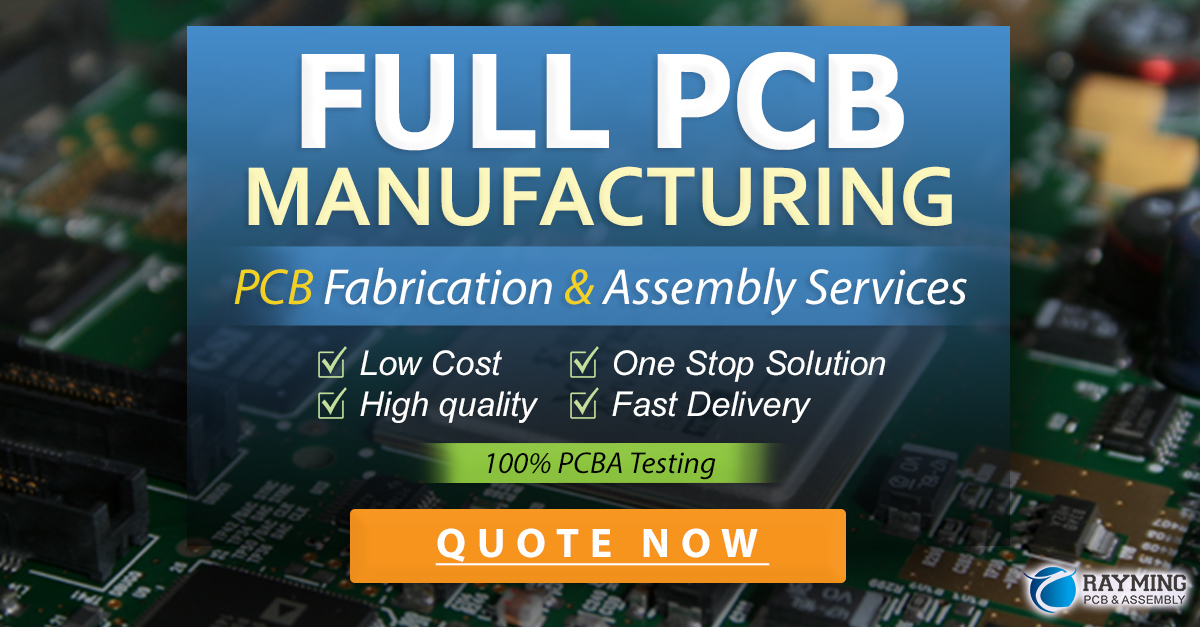
FR4 vs Rogers: Key Differences
Now that we have a better understanding of FR-4 and Rogers materials, let’s compare their key differences in terms of properties and applications.
Dielectric Constant and Dissipation Factor
The dielectric constant and dissipation factor are two crucial properties that determine a material’s suitability for high-frequency applications. FR-4 has a relatively high dielectric constant (4.3 to 4.7) and dissipation factor (0.02) compared to Rogers materials, which typically have lower values for both properties.
Material | Dielectric Constant | Dissipation Factor |
---|---|---|
FR-4 | 4.3 to 4.7 (at 1 MHz) | 0.02 (at 1 MHz) |
RO3000 Series | 3.0 to 3.5 (at 10 GHz) | 0.0009 to 0.0025 (at 10 GHz) |
RO4000 Series | 3.3 to 3.7 (at 10 GHz) | 0.0027 to 0.0037 (at 10 GHz) |
RT/duroid | 2.2 to 10.2 (at 10 GHz) | 0.0009 to 0.003 (at 10 GHz) |
The lower dielectric constant and dissipation factor of Rogers materials make them more suitable for high-frequency applications, as they result in lower signal loss and better signal integrity.
Thermal Conductivity
Thermal conductivity is essential for managing heat dissipation in PCBs. Rogers materials generally have higher thermal conductivity than FR-4, which allows for better heat dissipation and improved reliability in high-power applications.
Material | Thermal Conductivity (W/mK) |
---|---|
FR-4 | 0.3 |
RO3000 Series | Up to 1.44 |
RO4000 Series | 0.6 to 0.7 |
Cost
One of the main reasons for the widespread use of FR-4 is its affordability compared to Rogers materials. Rogers materials are generally more expensive due to their advanced properties and specialized manufacturing processes.
Material | Relative Cost |
---|---|
FR-4 | Low |
Rogers Materials | High |
The higher cost of Rogers materials may be justified in applications where their superior properties are necessary, such as in high-frequency or high-reliability systems.
FAQ
-
Q: Can FR-4 be used for high-frequency applications?
A: While FR-4 can be used for some high-frequency applications, it is generally not the best choice due to its relatively high dielectric constant and dissipation factor. These properties can lead to signal loss and reduced performance at higher frequencies. -
Q: Are Rogers materials compatible with standard PCB manufacturing processes?
A: Yes, most Rogers materials are compatible with standard PCB manufacturing processes, such as etching, drilling, and plating. However, due to their unique properties, some adjustments to the manufacturing process may be necessary to achieve optimal results. -
Q: Can Rogers materials be used for low-frequency applications?
A: While Rogers materials are primarily designed for high-frequency applications, they can also be used for low-frequency applications where their superior properties, such as low dielectric loss and stable dielectric constant, are advantageous. -
Q: How do I choose between FR-4 and Rogers materials for my project?
A: The choice between FR-4 and Rogers materials depends on your project’s specific requirements. Consider factors such as the operating frequency, required signal integrity, thermal management needs, and budget when making your decision. Consult with PCB Manufacturers and material suppliers to determine the best material for your application. -
Q: Are there any environmental concerns with using FR-4 or Rogers materials?
A: Both FR-4 and Rogers materials are compliant with various environmental regulations, such as RoHS (Restriction of Hazardous Substances) and REACH (Registration, Evaluation, Authorization, and Restriction of Chemicals). However, it is always important to consider the environmental impact of your project and choose materials that align with your sustainability goals.
Conclusion
FR-4 and Rogers materials are two popular choices for PCB Substrates, each with its own set of advantages and applications. FR-4 is widely used for its affordability, versatility, and reliability in a broad range of industries, while Rogers materials are preferred for high-frequency and high-performance applications due to their superior electrical, thermal, and mechanical properties.
When deciding between FR-4 and Rogers materials, it is essential to consider your project’s specific requirements, such as operating frequency, signal integrity, thermal management, and budget. By understanding the key differences between these materials and their properties, you can make an informed decision that ensures the optimal performance and reliability of your PCB Design.
Leave a Reply