Table of Contents
- Introduction to PCB Materials
- Substrate Materials
- FR-4
- High Tg FR-4
- Polyimide
- PTFE
- Ceramic
- Metal Core
- Copper Foil
- Electrodeposited Copper Foil
- Rolled Copper Foil
- Solder Mask
- Silkscreen
- Surface Finish
- HASL
- ENIG
- Immersion Tin
- Immersion Silver
- OSP
- Choosing the Right PCB Materials
- FAQ
- Conclusion
Introduction to PCB Materials
PCB materials are the building blocks of printed circuit boards. They consist of a substrate, copper foil, solder mask, silkscreen, and surface finish. Each component plays a specific role in the PCB’s functionality and manufacturability.
The substrate is the base material that provides mechanical support and electrical insulation. Copper foil is laminated onto the substrate to create conductive traces and pads. Solder mask is applied over the copper to protect it from oxidation and prevent solder bridges during assembly. Silkscreen is used for text and symbols on the PCB surface, while the surface finish protects the exposed copper and enhances solderability.
Substrate Materials
The substrate is the foundation of the PCB, and its properties significantly influence the board’s performance. Here are some common substrate materials used in PCB manufacturing:
FR-4
FR-4 (Flame Retardant 4) is the most widely used substrate material for PCBs. It is a composite material made of woven fiberglass cloth impregnated with an epoxy resin. FR-4 offers good mechanical strength, electrical insulation, and thermal stability. It is suitable for most general-purpose applications and is cost-effective.
High Tg FR-4
High Tg (glass transition temperature) FR-4 is a variant of the standard FR-4 material. It has a higher glass transition temperature, typically above 170°C, compared to around 130°C for standard FR-4. High Tg FR-4 offers improved thermal stability and is suitable for applications that require higher operating temperatures or lead-free soldering processes.
Polyimide
Polyimide is a high-performance substrate material known for its excellent thermal stability, chemical resistance, and mechanical strength. It can withstand temperatures up to 260°C and is often used in aerospace, military, and high-reliability applications. Polyimide is more expensive than FR-4 and requires specialized processing techniques.
PTFE
PTFE (Polytetrafluoroethylene), also known as Teflon, is a low-loss dielectric material used in high-frequency and microwave applications. It offers excellent electrical properties, including low dielectric constant and dissipation factor. PTFE is also highly resistant to chemicals and has a wide operating temperature range. However, it is more expensive and challenging to process compared to FR-4.
Ceramic
Ceramic substrates, such as alumina (Al2O3) and aluminum nitride (AlN), are used in high-power and high-frequency applications. They provide excellent thermal conductivity, electrical insulation, and dimensional stability. Ceramic substrates are often used in RF and microwave circuits, power electronics, and LED packaging.
Metal Core
Metal core substrates, such as aluminum and copper, are used in applications that require efficient heat dissipation. They consist of a metal core covered with a thin dielectric layer and copper foil. Metal core PCBs are commonly used in high-power LEDs, automotive electronics, and power converters.
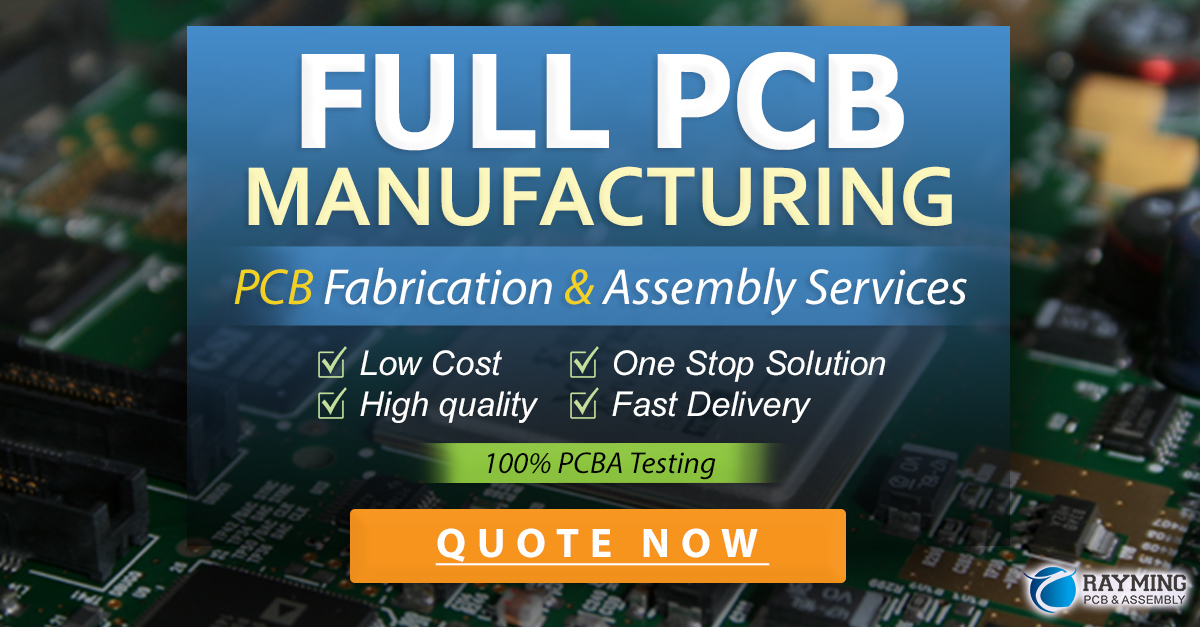
Copper Foil
Copper foil is the conductive layer laminated onto the substrate to create circuit traces and pads. There are two main types of copper foil used in PCB manufacturing:
Electrodeposited Copper Foil
Electrodeposited copper foil is produced by electroplating copper onto a rotating drum. It has a matte side (drum side) and a shiny side (copper side). The matte side has a rougher surface that promotes better adhesion to the substrate. Electrodeposited copper foil is widely used in PCB manufacturing due to its good adhesion properties and lower cost compared to rolled copper foil.
Rolled Copper Foil
Rolled copper foil is produced by mechanically rolling copper into thin sheets. It has a smoother surface on both sides compared to electrodeposited copper foil. Rolled copper foil offers better electrical conductivity and is preferred for high-frequency and high-current applications. However, it is more expensive than electrodeposited copper foil.
Copper Foil Type | Advantages | Disadvantages |
---|---|---|
Electrodeposited | – Good adhesion to substrate – Lower cost |
– Rougher surface – Lower conductivity |
Rolled | – Smoother surface – Better conductivity |
– More expensive – Reduced adhesion to substrate |
Solder Mask
Solder mask, also known as solder resist, is a polymer coating applied over the copper traces on the PCB. Its primary functions are to protect the copper from oxidation, prevent solder bridges during assembly, and provide electrical insulation between adjacent traces.
Solder mask is typically applied using screen printing or photoimaging techniques. It is available in various colors, with green being the most common. Other colors, such as blue, red, yellow, and black, are used for specific applications or for visual identification.
Solder Mask Color | Application |
---|---|
Green | Most common, general-purpose |
Blue | High-contrast, military and aerospace |
Red | High-visibility, automotive and industrial |
Yellow | High-visibility, safety-critical applications |
Black | Aesthetics, high-end consumer electronics |
Silkscreen
Silkscreen, also known as legend or nomenclature, is the text and symbols printed on the PCB surface. It provides information such as component designators, polarity markings, and company logos. Silkscreen is typically printed using a screen printing process and is available in various colors, with white being the most common.
Silkscreen should be legible and durable to withstand the PCB assembly process and the end-use environment. It is important to ensure that the silkscreen does not interfere with the solder mask openings or the component placement.
Surface Finish
Surface finish is the coating applied to the exposed copper on the PCB to protect it from oxidation and enhance solderability. There are several types of surface finishes used in PCB manufacturing, each with its own advantages and limitations.
HASL
HASL (Hot Air Solder Leveling) is a traditional surface finish where the PCB is dipped in molten solder and then leveled using hot air knives. HASL provides good solderability and is cost-effective. However, it can result in uneven surface due to the solder’s meniscus effect and is not suitable for fine-pitch components.
ENIG
ENIG (Electroless Nickel Immersion Gold) is a two-layer surface finish consisting of a nickel layer followed by a thin gold layer. The nickel provides a barrier against copper diffusion, while the gold protects the nickel from oxidation and enhances solderability. ENIG offers excellent surface planarity, making it suitable for fine-pitch components and wire bonding. However, it is more expensive than HASL.
Immersion Tin
Immersion tin is a single-layer surface finish where the exposed copper is coated with a thin layer of tin. It provides good solderability and is less expensive than ENIG. However, immersion tin has a limited shelf life due to the formation of tin whiskers, which can cause short circuits.
Immersion Silver
Immersion silver is another single-layer surface finish that coats the exposed copper with a thin layer of silver. It offers excellent solderability and conductivity. Immersion silver is compatible with aluminum wire bonding and is suitable for high-frequency applications. However, it is prone to tarnishing over time.
OSP
OSP (Organic Solderability Preservative) is a thin, organic coating applied to the exposed copper to protect it from oxidation. OSP is cost-effective and provides good solderability. However, it has a limited shelf life and may require special handling during assembly.
Surface Finish | Advantages | Disadvantages |
---|---|---|
HASL | – Cost-effective – Good solderability |
– Uneven surface – Not suitable for fine-pitch |
ENIG | – Excellent surface planarity – Suitable for fine-pitch and wire bonding |
– More expensive than HASL |
Immersion Tin | – Good solderability – Less expensive than ENIG |
– Limited shelf life – Tin whisker formation |
Immersion Silver | – Excellent solderability and conductivity – Compatible with aluminum wire bonding |
– Prone to tarnishing over time |
OSP | – Cost-effective – Good solderability |
– Limited shelf life – May require special handling |
Choosing the Right PCB Materials
Selecting the appropriate PCB materials depends on several factors, including:
- Application requirements (electrical, thermal, mechanical)
- Operating environment (temperature, humidity, chemical exposure)
- Frequency and signal integrity considerations
- Manufacturing process (soldering, assembly, rework)
- Cost and availability
It is essential to consult with the PCB manufacturer and consider the trade-offs between performance, cost, and manufacturability when choosing PCB materials.
FAQ
Q1: What is the most common substrate material used in PCB manufacturing?
A1: FR-4 is the most widely used substrate material for PCBs due to its good mechanical, electrical, and thermal properties, as well as its cost-effectiveness.
Q2: What are the advantages of using ENIG surface finish?
A2: ENIG (Electroless Nickel Immersion Gold) offers excellent surface planarity, making it suitable for fine-pitch components and wire bonding. It also provides good solderability and protection against oxidation.
Q3: What is the purpose of solder mask on a PCB?
A3: Solder mask is a polymer coating applied over the copper traces on the PCB to protect the copper from oxidation, prevent solder bridges during assembly, and provide electrical insulation between adjacent traces.
Q4: What are the considerations when choosing PCB materials?
A4: When choosing PCB materials, it is important to consider the application requirements (electrical, thermal, mechanical), operating environment, frequency and signal integrity considerations, manufacturing process, cost, and availability.
Q5: What is the difference between electrodeposited and rolled copper foil?
A5: Electrodeposited copper foil is produced by electroplating and has a rougher surface that promotes better adhesion to the substrate. Rolled copper foil is produced by mechanical rolling and has a smoother surface, offering better electrical conductivity. Electrodeposited copper foil is more common and less expensive than rolled copper foil.
Conclusion
PCB materials play a critical role in the performance, reliability, and manufacturability of electronic devices. Understanding the properties and applications of different substrate materials, copper foils, solder masks, silkscreens, and surface finishes is essential for designing and manufacturing high-quality PCBs.
Choosing the right PCB materials involves considering the application requirements, operating environment, signal integrity, manufacturing process, and cost. Working closely with the PCB manufacturer and carefully evaluating the trade-offs between performance and manufacturability will help ensure the success of your PCB project.
By selecting the appropriate materials and following best design and manufacturing practices, you can create PCBs that meet your specific needs and deliver optimal performance in your electronic devices.
Leave a Reply