Introduction to Popcorn Effect
The popcorn effect, also known as the popcorning effect or moisture-induced delamination, is a serious defect that can occur during the printed circuit board assembly (PCBA) process. It is characterized by the formation of small blisters or “popped” areas on the surface of the PCB laminate or component packaging.
This defect gets its name from its resemblance to popped popcorn kernels. When moisture trapped within the PCB or component packaging vaporizes and expands rapidly due to exposure to high temperatures during reflow soldering, it causes localized delamination between layers. This can lead to a host of reliability issues and even catastrophic failure of the assembLED PCB.
Understanding the causes, prevention methods, and detection techniques for popcorn effect is critical for ensuring the quality and reliability of electronic assemblies. In this comprehensive article, we will delve into the details of this important topic.
Causes of Popcorn Effect
Moisture Absorption
The primary cause of popcorn effect is moisture absorption by the PCB laminate or component packaging materials. Both PCBs and electronic components are hygroscopic, meaning they tend to absorb moisture from the surrounding environment.
PCB Laminates are typically made from materials like FR-4, which is a composite of woven fiberglass cloth impregnated with an epoxy resin. The epoxy resin can absorb moisture, especially in humid environments. Similarly, plastic IC packages and other component encapsulation materials can also absorb moisture over time.
The rate and extent of moisture absorption depend on several factors:
-
Material properties: Some materials are more hygroscopic than others. For example, FR-4 laminates with higher resin content tend to absorb more moisture compared to those with higher glass content.
-
Environmental conditions: High humidity and temperature accelerate moisture absorption. PCBs and components stored in humid environments for extended periods are more susceptible to popcorn effect.
-
Exposure time: The longer a PCB or component is exposed to moisture, the more moisture it will absorb until it reaches an equilibrium with the surrounding environment.
Rapid Heating During Reflow
The absorbed moisture itself does not cause popcorn effect. The defect occurs when the moisture-laden PCB or component is subjected to rapid heating, typically during the reflow soldering process.
In reflow soldering, the PCB Assembly is passed through a carefully controlled temperature profile in a reflow oven. The temperature is gradually raised to activate the flux, melt the solder paste, and form reliable solder joints between components and pads. The peak temperature in a typical lead-free reflow profile can exceed 240°C.
When the moisture trapped within the PCB or component packaging is exposed to these high temperatures, it vaporizes and expands rapidly. If the vapor pressure exceeds the strength of the material, it can cause localized delamination or blistering, resulting in the characteristic “popped” appearance.
The risk of popcorn effect is highest during the initial ramp-up phase of the reflow profile, where the rate of temperature change is the greatest. If the moisture cannot escape quickly enough through the material’s natural porosity, it can build up sufficient pressure to cause delamination.
Impact of Popcorn Effect
Popcorn effect can have serious consequences for the reliability and functionality of electronic assemblies. Some of the potential impacts include:
Delamination and Cracking
The most direct result of popcorn effect is localized delamination or separation between layers of the PCB laminate or component packaging. This can manifest as blisters, cracks, or voids on the surface or within the material.
Delamination can compromise the structural integrity of the PCB, reducing its ability to withstand mechanical stresses during handling, assembly, or operation. It can also create pathways for moisture ingress, leading to further degradation over time.
In severe cases, the delamination can extend to the copper traces or planes within the PCB, causing open circuits or intermittent connections. This can lead to electrical failures or erratic performance of the assembled device.
Component Damage
Popcorn effect can also damage electronic components, particularly those with plastic packages like QFP, BGA, or CSP. The rapid expansion of moisture within the component package can cause cracking, delamination, or lifting of the package from the PCB.
Damage to component packages can result in a range of issues:
-
Broken bond wires: The sudden movement or deformation of the package during popcorning can break the delicate bond wires that connect the die to the package leads.
-
Die cracking: In extreme cases, the stress from popcorning can propagate to the silicon die itself, causing cracks or fractures that render the component non-functional.
-
Parametric shifts: Even if the component survives the initial popcorning event, the moisture intrusion and mechanical stress can cause shifts in electrical parameters like leakage current, threshold voltage, or signal integrity.
Solder Joint Reliability
Popcorn effect can also impact the reliability of solder joints. The localized delamination and movement of the PCB or component during reflow can disrupt the formation of proper solder joints.
Some potential solder joint defects related to popcorn effect include:
-
Voids: The rapid outgassing of moisture can create large voids within the solder joint, reducing its mechanical strength and current-carrying capacity.
-
Dewetting: The delamination can interfere with the wetting and spreading of molten solder on the pads or component leads, resulting in poor or inconsistent solder coverage.
-
Bridging: In severe cases, the movement of components due to popcorning can cause them to shift out of alignment, leading to solder bridges between adjacent pins or pads.
These solder joint defects can lead to premature failures or intermittent connections, compromising the overall reliability of the assembled PCB.
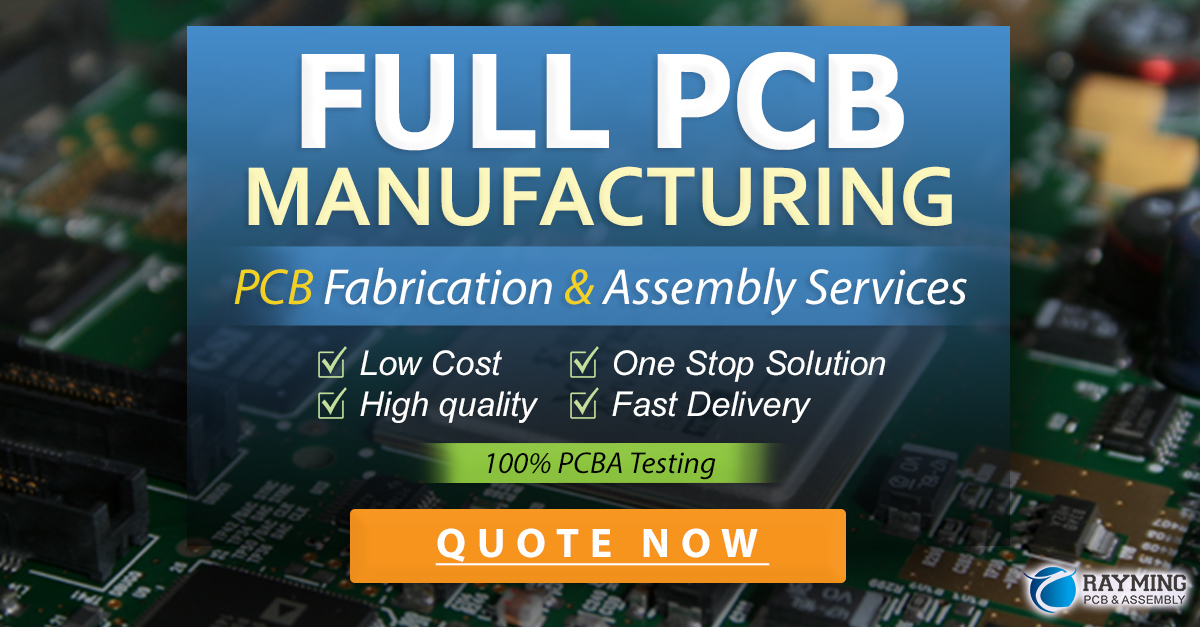
Prevention of Popcorn Effect
Given the serious consequences of popcorn effect, it is essential to take proactive measures to prevent its occurrence. The key strategies for preventing popcorn effect focus on controlling moisture levels in PCBs and components prior to reflow soldering.
Moisture Sensitivity Level (MSL) Classification
One of the most important tools for managing moisture sensitivity is the Moisture Sensitivity Level (MSL) classification system. MSL is a standardized rating that indicates a component’s susceptibility to moisture-induced damage during reflow soldering.
The MSL system is defined by the IPC/JEDEC J-STD-020 standard, which specifies the following levels:
MSL | Floor Life at 30°C/85% RH |
---|---|
1 | Unlimited |
2 | 1 year |
2a | 4 weeks |
3 | 168 hours |
4 | 72 hours |
5 | 48 hours |
5a | 24 hours |
6 | Time on Label (TOL) |
The floor life indicates how long a component can be exposed to ambient conditions (30°C/85% RH) after removal from its moisture-barrier packaging before it needs to be mounted and reflowed. Components with higher MSL ratings are more susceptible to moisture absorption and require stricter handling and storage controls.
Dry Storage and Handling
To prevent moisture absorption, PCBs and components should be stored in a dry environment with controlled temperature and humidity. The specific storage conditions depend on the MSL of the components and the duration of storage.
For MSL 1 components, no special storage conditions are required. However, for MSL 2 and above, components should be stored in moisture-barrier bags (MBBs) with desiccants and humidity indicator cards (HICs). The MBBs should be sealed and stored in a dry cabinet or nitrogen-purged storage area.
When components are removed from the MBB for assembly, they should be mounted and reflowed within the specified floor life for their MSL rating. If the floor life is exceeded, the components need to be baked to remove excess moisture before reflow.
Bake-out Procedures
Baking is a process of removing moisture from PCBs or components by exposing them to elevated temperatures in a controlled environment. The baking temperature and duration are specified based on the MSL and the thickness of the component package.
For example, the typical baking conditions for MSL 3 components are:
Package Thickness | Baking Temperature | Baking Time |
---|---|---|
≤ 1.4mm | 125°C | 4-6 hours |
> 1.4mm to 2.0mm | 125°C | 6-8 hours |
> 2.0mm | 125°C | 8-10 hours |
It is important to follow the recommended baking procedures carefully, as excessive baking can degrade the solderability of component leads or cause oxidation. After baking, components should be stored in a dry environment and reflowed within the specified time limit to prevent re-absorption of moisture.
Moisture-Sensitive PCB Design
In addition to handling and storage controls, PCB design can also play a role in reducing the risk of popcorn effect. Some design considerations include:
-
Material selection: Choose PCB laminate materials with lower moisture absorption properties, such as high-Tg or low-CTE materials. Avoid using hygroscopic materials in critical applications.
-
Minimize exposed copper: Reduce the area of exposed copper on the PCB surface, as it can act as a pathway for moisture ingress. Use solder mask or other protective coatings to cover exposed copper where possible.
-
Optimize via design: Ensure that vias are properly plugged or filled to prevent moisture from penetrating into the inner layers of the PCB. Avoid placing vias under moisture-sensitive components where possible.
-
Conformal coating: Apply conformal coating to the assembled PCB to provide an additional barrier against moisture ingress. Choose a coating material that is compatible with the PCB and components.
Detection of Popcorn Effect
Despite best efforts to prevent popcorn effect, it is important to have reliable methods for detecting its occurrence. Early detection of popcorn defects can help prevent affected assemblies from reaching the field and causing failures.
Visual Inspection
The most straightforward method for detecting popcorn effect is visual inspection. Popcorning often leaves visible signs on the surface of the PCB or component package, such as:
- Blisters or bubbles on the surface
- Cracks or delamination
- Lifting or separation of components from the PCB
- Solder joint anomalies (voids, dewetting, bridging)
Visual inspection can be performed manually by trained operators or using automated optical inspection (AOI) systems. AOI systems can rapidly scan the PCB surface and compare it against a reference image to detect anomalies.
However, visual inspection has some limitations. It can only detect defects that are visible on the surface, while some popcorn-related damage may be hidden within the layers of the PCB or component package.
X-Ray Inspection
For detecting internal defects related to popcorn effect, X-ray inspection is a valuable tool. X-ray systems can generate high-resolution images of the internal structure of the PCB and components, revealing defects such as:
- Delamination or voids within the PCB laminate
- Cracks or delamination within component packages
- Broken bond wires or die cracks
- Large voids or inconsistencies in solder joints
X-ray inspection can be performed using 2D or 3D X-ray systems, depending on the level of detail required. 3D X-ray systems can generate cross-sectional images or tomographic reconstructions, providing a more comprehensive view of the internal structure.
Acoustic Microscopy
Another technique for detecting internal popcorn defects is acoustic microscopy. This method uses high-frequency ultrasound waves to generate images of the internal structure of the PCB or component.
In acoustic microscopy, an ultrasonic transducer scans the surface of the sample, sending sound waves into the material. The waves are reflected back from internal interfaces and defects, creating an acoustic signature that can be analyzed to detect anomalies.
Acoustic microscopy can detect delamination, voids, and cracks within the PCB or component package with high sensitivity. It is particularly useful for inspecting components with complex internal structures, such as flip-chip or stacked-die packages.
Electrical Testing
Electrical testing can also help detect popcorn-related defects that affect the functionality of the assembled PCB. Some common electrical tests include:
-
In-circuit testing (ICT): Measures the electrical properties of individual components and connections on the PCB to detect opens, shorts, or parametric failures.
-
Functional Testing: Verifies the overall functionality of the assembled PCB under various operating conditions to detect performance anomalies or intermittent failures.
-
Boundary scan testing: Uses built-in test access ports (TAPs) on components to test the interconnections and functionality of the PCB assembly.
Electrical testing can help identify defects that may not be visually apparent, such as broken bond wires, parametric shifts, or intermittent connections caused by popcorn effect.
FAQs
Q1: What is the main cause of popcorn effect in PCBs and components?
A1: The main cause of popcorn effect is moisture absorption by the PCB laminate or component packaging materials, followed by rapid vaporization of the absorbed moisture during high-temperature reflow soldering.
Q2: How can I prevent popcorn effect in my PCB assemblies?
A2: To prevent popcorn effect, follow proper storage and handling procedures for moisture-sensitive components, including dry storage, moisture-barrier packaging, and bake-out before reflow. Also, consider moisture-resistant PCB design practices and materials.
Q3: What are the consequences of popcorn effect?
A3: Popcorn effect can cause delamination, cracking, or voiding in the PCB laminate or component packages, leading to structural damage, broken connections, or component failures. It can also impact the reliability of solder joints.
Q4: How can I detect popcorn effect in PCB assemblies?
A4: Popcorn effect can be detected through visual inspection (manual or automated), X-ray inspection, acoustic microscopy, and electrical testing methods like in-circuit testing or functional testing.
Q5: What should I do if I suspect popcorn effect in my PCB assemblies?
A5: If you suspect popcorn effect, quarantine the affected assemblies and perform a thorough inspection using visual, X-ray, or acoustic methods to assess the extent of the damage. Rework or scrap the affected boards based on the severity of the defects and the rework feasibility. Review your moisture control procedures to prevent future occurrences.
Conclusion
Popcorn effect is a serious defect that can occur during the PCBA process, leading to structural damage, component failures, and reliability issues. It is caused by the rapid vaporization of moisture absorbed by the PCB laminate or component packaging materials during high-temperature reflow soldering.
To prevent popcorn effect, it is essential to follow proper storage and handling procedures for moisture-sensitive components, including dry storage, moisture-barrier packaging, and bake-out before reflow. Moisture-resistant PCB design practices and materials can also help reduce the risk of popcorn effect.
Detection of popcorn effect can be achieved through visual inspection, X-ray inspection, acoustic microscopy, and electrical testing methods. Early detection and remediation of popcorn defects are critical for ensuring the quality and reliability of electronic assemblies.
By understanding the causes, prevention methods, and detection techniques for popcorn effect, PCB manufacturers and assemblers can effectively mitigate this defect and produce high-quality, reliable electronic products.
Leave a Reply