Understanding PCBs and PCBA
A printed circuit board (PCB) mechanically supports and electrically connects electronic components using conductive tracks, pads and other features etched from one or more sheet layers of copper laminated onto and/or between sheet layers of a non-conductive substrate. Components are generally soldered onto the PCB to both electrically connect and mechanically fasten them to it.
PCB Assembly, or PCBA, is the process of soldering or assembly of electronic components to a PCB. It is used in the vast majority of commercially produced electronic devices, such as computers, smartphones, tablets, and TVs.
The key steps involved in PCBA are:
-
Solder Paste Application: Solder paste is applied to the PCB pads where the components will be placed. This is typically done using a solder paste stencil and a squeegee.
-
Component Placement: The electronic components are then placed onto the PCB. This is usually done by a Pick-and-place machine, which picks up the components and places them in their designated locations with great speed and accuracy.
-
Reflow Soldering: After the components are placed, the PCB goes through a reflow oven. The solder paste melts in the high temperature, forming permanent electrical connections between the components and the PCB.
-
Inspection and Testing: After soldering, the PCBs are inspected and tested to ensure all connections are properly made and the board functions as intended.
Types of PCBs
PCBs can be categorized based on the number of layers:
-
Single Layer PCB: These have only one layer of base material or substrate. The electronic components are soldered on one side and the copper traces are on the other side.
-
Double Layer PCB: These have two layers of substrate. The components and copper traces are on both sides of the board.
-
Multi-Layer PCB: These have more than two layers of substrate. They are used for more complex circuits and offer better performance and durability.
PCB Type | Layers | Complexity | Cost |
---|---|---|---|
Single Layer | 1 | Low | Low |
Double Layer | 2 | Medium | Medium |
Multi-Layer | >2 | High | High |
Advantages of Custom PCBA
Custom PCBA offers several advantages over off-the-shelf PCBs:
Tailored to Specific Needs
Custom PCBs are designed and manufactured to meet the specific requirements of a project. This includes the size, shape, number of layers, type of components, and any special features needed.
Improved Reliability
Custom PCBs can be designed with higher quality materials and more rigorous manufacturing standards, resulting in a more reliable product. Additionally, custom designs can incorporate redundancy and other features to improve reliability.
Reduced Size and Weight
Custom PCBs can be optimized for size and weight, which is crucial for applications where space and weight are at a premium, such as in mobile devices or aerospace applications.
Intellectual Property Protection
Custom PCBs provide a level of intellectual property protection as the design is unique and not readily available to competitors.
Cost Savings in High Volumes
While custom PCBs have higher upfront design and setup costs, they can offer significant cost savings in high volume production due to optimized design and streamlined manufacturing.
The Custom PCBA Process
The process of creating a custom PCBA involves several steps:
1. Design
The first step is to design the PCB. This involves creating a schematic, which is a diagram that shows how all the components are connected, and a layout, which shows the physical arrangement of the components on the board. PCB design software, such as Altium Designer or KiCad, is used for this process.
2. Prototyping
Once the design is complete, a prototype is usually made. This allows for testing and verification of the design before mass production. Prototypes can be made in-house or by a PCB Prototyping service.
3. Manufacturing
After the prototype is verified, the PCB is ready for manufacturing. This involves several steps, including PCB fabrication, PCBA, and testing.
4. Testing and Quality Control
Rigorous testing and quality control measures are implemented throughout the manufacturing process to ensure the PCBs meet the required specifications and are free of defects.
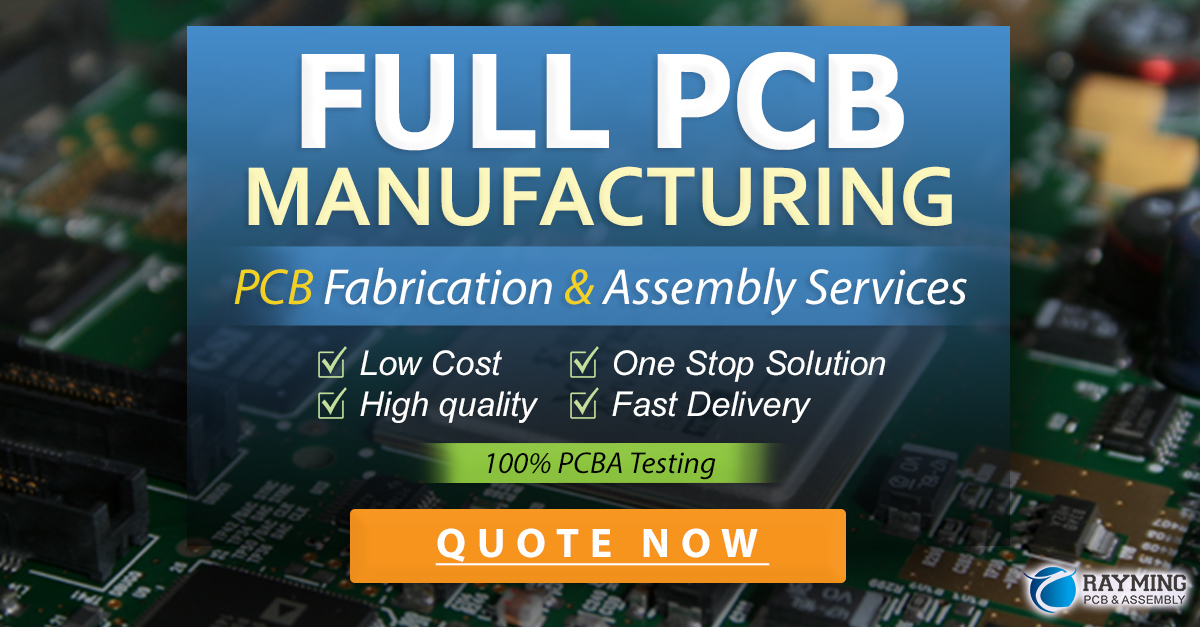
Choosing a PCBA Partner
Choosing the right PCBA partner is crucial for the success of your project. Here are some key factors to consider:
Technical Capabilities
Ensure the PCBA partner has the technical capabilities and equipment to handle your specific requirements. This includes the ability to work with the required materials, components, and PCB features.
Quality Standards
Check the quality standards and certifications held by the PCBA partner. Common standards include ISO 9001, IPC-A-610, and UL.
Experience and Expertise
Look for a PCBA partner with experience and expertise in your industry or application. They should understand your specific needs and requirements.
Capacity and Lead Time
Ensure the PCBA partner has the production capacity to meet your volume requirements and can deliver within your required lead time.
Communication and Support
Good communication and support are essential. Look for a PCBA partner that is responsive, communicative, and provides good technical support.
FAQs
1. What is the difference between PCB and PCBA?
PCB (Printed Circuit Board) refers to the Bare Board, while PCBA (Printed Circuit Board Assembly) refers to the board with components soldered onto it.
2. How long does custom PCBA take?
The lead time for custom PCBA depends on the complexity of the design and the quantity required. Prototype quantities can usually be produced in 1-2 weeks, while larger production runs may take several weeks.
3. What information do I need to provide for custom PCBA?
You will need to provide the Gerber files for the PCB design, the bill of materials (BOM) listing all the required components, and the assembly drawings or instructions.
4. What are the minimum quantities for custom PCBA?
Minimum quantities vary by manufacturer. Some offer low volume production with no minimum order quantity, while others may have minimum quantities of 100 or more.
5. How much does custom PCBA cost?
The cost of custom PCBA depends on the complexity of the design, the quantity required, and the components used. In general, larger quantities will have a lower per-unit cost. It’s best to get a quote from the PCBA manufacturer based on your specific requirements.
Conclusion
Custom PCBA offers numerous advantages for electronic projects, including tailored design, improved reliability, reduced size and weight, intellectual property protection, and potential cost savings in high volumes. The process involves design, prototyping, manufacturing, and thorough testing and quality control.
When choosing a PCBA partner, consider their technical capabilities, quality standards, experience and expertise, capacity and lead time, and communication and support. With the right partner, custom PCBA can help bring your electronic product to life efficiently and effectively.
Leave a Reply