Introduction to OSP Finish on PCB
Organic Solderability Preservatives (OSP) is a surface finish commonly used in the manufacturing of printed circuit boards (PCBs). OSP-PCB is a cost-effective and environmentally friendly alternative to other surface finishes such as Hot Air Solder Leveling (HASL), Electroless Nickel Immersion Gold (ENIG), and Immersion Silver. In this article, we will explore what OSP finish is, how it is applied, and the advantages and disadvantages of using OSP on PCBs.
What is OSP Finish?
OSP is a chemical coating that is applied to the copper pads on a PCB to prevent oxidation and maintain solderability. The coating is a clear, thin, and organic compound that is typically composed of benzimidazole or benzotriazole. OSP acts as a barrier between the copper and the environment, preventing the formation of copper oxide, which can degrade the solderability of the PCB.
How is OSP Applied to PCBs?
The OSP finish is applied to the PCB through a series of steps:
-
Cleaning: The PCB is thoroughly cleaned to remove any contaminants or debris that may affect the adhesion of the OSP coating.
-
Microetching: The copper pads are microetched to create a uniform surface texture and improve the adhesion of the OSP coating.
-
OSP Application: The OSP coating is applied to the PCB through either spraying or immersion. The PCB is then dried to remove any excess moisture.
-
Curing: The OSP coating is cured using heat to ensure proper adhesion and coverage.
Advantages of OSP Finish on PCBs
OSP finish offers several advantages over other surface finishes:
Cost-effective
OSP is one of the most cost-effective surface finishes available. It requires fewer processing steps and materials compared to other finishes, resulting in lower production costs. This makes OSP an attractive option for high-volume, Low-Cost PCB manufacturing.
Environmentally Friendly
OSP is an environmentally friendly surface finish as it does not contain any heavy metals or hazardous chemicals. This reduces the environmental impact of PCB manufacturing and makes OSP a more sustainable choice.
Good Solderability
OSP provides good solderability by preventing the formation of copper oxide on the PCB pads. This ensures reliable solder joints and reduces the risk of soldering defects.
Flat Surface
OSP finish results in a flat surface, which is essential for fine-pitch components and high-density PCB Designs. The flat surface allows for better placement accuracy and reduces the risk of component tilting or tombstoning.
Suitable for Multiple Assembly Processes
OSP finish is compatible with various assembly processes, including Reflow Soldering, wave soldering, and pin-through-hole assembly. This versatility makes OSP a suitable choice for a wide range of PCB applications.
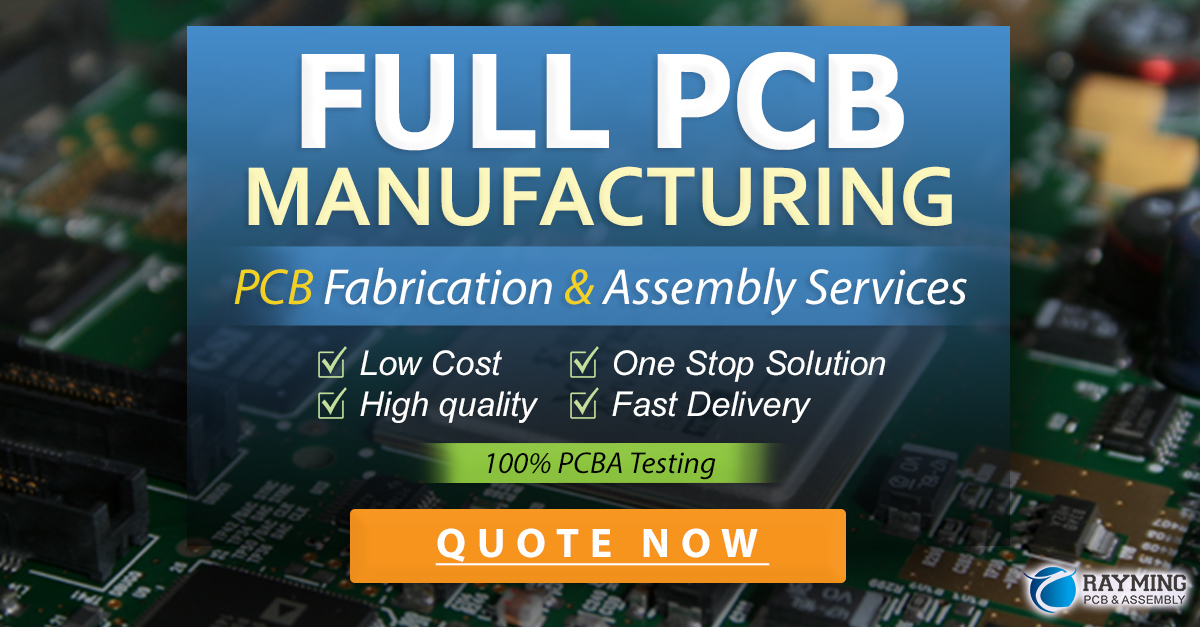
Disadvantages of OSP Finish on PCBs
Despite its many advantages, OSP finish also has some limitations:
Limited Shelf Life
One of the main drawbacks of OSP finish is its limited shelf life. The organic coating can degrade over time, especially when exposed to high temperatures and humidity. This can lead to a loss of solderability and an increased risk of assembly defects. Typically, OSP-coated PCBs have a shelf life of 6 to 12 months, depending on the storage conditions.
Susceptible to Contamination
OSP finish is more susceptible to contamination compared to other surface finishes. Contaminants such as dust, dirt, and oils can easily adhere to the organic coating, affecting its solderability. Proper handling and storage of OSP-coated PCBs are crucial to maintain their integrity.
Not Suitable for Multiple Reflow Cycles
OSP finish is not recommended for PCBs that require multiple reflow cycles. The organic coating can degrade with each reflow cycle, leading to a loss of solderability and an increased risk of defects. For applications that require multiple reflow cycles, other surface finishes such as ENIG or Immersion Silver are more suitable.
Difficult to Inspect
OSP finish can be difficult to inspect visually as the coating is clear and thin. This can make it challenging to detect defects or inconsistencies in the coating. Specialized inspection techniques, such as X-ray fluorescence (XRF) or Fourier-transform infrared spectroscopy (FTIR), may be required to ensure the quality of the OSP finish.
Comparison of OSP with Other Surface Finishes
To help you make an informed decision, here’s a comparison of OSP with other common surface finishes:
Surface Finish | Advantages | Disadvantages |
---|---|---|
OSP | – Cost-effective – Environmentally friendly – Good solderability – Flat surface – Suitable for multiple assembly processes |
– Limited shelf life – Susceptible to contamination – Not suitable for multiple reflow cycles – Difficult to inspect |
HASL | – Excellent solderability – Long shelf life – Suitable for multiple reflow cycles |
– Not suitable for fine-pitch components – Uneven surface – Contains lead (in some cases) |
ENIG | – Excellent solderability – Long shelf life – Suitable for fine-pitch components – Flat surface |
– More expensive than OSP – Contains nickel (allergenic) – Can be prone to “black pad” defect |
Immersion Silver | – Good solderability – Suitable for fine-pitch components – Flat surface – Suitable for multiple reflow cycles |
– More expensive than OSP – Limited shelf life – Can tarnish over time |
Applications of OSP Finish on PCBs
OSP finish is widely used in various PCB applications, including:
- Consumer electronics
- Automotive electronics
- Industrial control systems
- Medical devices
- Telecommunications equipment
OSP’s cost-effectiveness, good solderability, and compatibility with multiple assembly processes make it a popular choice for these applications. However, it is essential to consider the specific requirements of each application, such as shelf life, reflow cycles, and environmental conditions, to determine if OSP is the most suitable surface finish.
Frequently Asked Questions
-
What does OSP stand for?
OSP stands for Organic Solderability Preservatives. It is a clear, thin, and organic coating applied to the copper pads on a PCB to prevent oxidation and maintain solderability. -
How long does OSP finish last?
OSP finish typically has a shelf life of 6 to 12 months, depending on the storage conditions. The organic coating can degrade over time, especially when exposed to high temperatures and humidity. -
Is OSP finish environmentally friendly?
Yes, OSP finish is an environmentally friendly surface finish as it does not contain any heavy metals or hazardous chemicals. This reduces the environmental impact of PCB manufacturing and makes OSP a more sustainable choice. -
Can OSP-coated PCBs be reworked?
Yes, OSP-coated PCBs can be reworked. However, the rework process may damage the OSP coating, affecting its solderability. It is essential to follow proper rework procedures and reapply OSP coating if necessary. -
Is OSP finish suitable for all PCB applications?
While OSP finish is suitable for a wide range of PCB applications, it may not be the best choice for every situation. Factors such as shelf life requirements, multiple reflow cycles, and environmental conditions should be considered when selecting a surface finish. In some cases, other surface finishes like ENIG or Immersion Silver may be more appropriate.
Conclusion
OSP finish is a cost-effective, environmentally friendly, and widely used surface finish in the PCB industry. Its good solderability, flat surface, and compatibility with multiple assembly processes make it an attractive choice for many applications. However, it is essential to consider its limitations, such as limited shelf life and susceptibility to contamination, when deciding if OSP is the right surface finish for your PCB application.
By understanding the advantages and disadvantages of OSP and comparing it with other surface finishes, you can make an informed decision that meets the specific requirements of your PCB design and manufacturing process. As with any surface finish, proper handling, storage, and processing are crucial to ensure the quality and reliability of your OSP-coated PCBs.
Leave a Reply