Introduction to Gold Fingers
Gold fingers, also known as edge connectors, are a type of electrical connector commonly found on printed circuit boards (PCBs) and various electronic devices. These connectors are named “gold fingers” due to the gold-plated contacts that protrude from the edge of the PCB, resembling fingers. Gold fingers play a crucial role in establishing reliable electrical connections between different components or modules in electronic systems.
What are Gold Fingers Used For?
Gold fingers are used in a wide range of applications, including:
- Computer hardware: Gold fingers are found on computer peripherals such as graphics cards, sound cards, and memory modules (e.g., RAM).
- Consumer electronics: Many electronic devices, such as smartphones, tablets, and digital cameras, utilize gold fingers for connecting various components.
- Industrial equipment: Gold fingers are used in industrial control systems, automation devices, and test and measurement equipment.
- Automotive electronics: Gold fingers are used in automotive electronic systems, such as infotainment systems and engine control modules.
Advantages of Gold Fingers
Gold fingers offer several advantages over other types of connectors:
Excellent Conductivity
Gold is an excellent conductor of electricity, which makes it an ideal material for electrical contacts. The gold plating on the fingers ensures low contact resistance and minimizes signal loss, resulting in reliable and efficient electrical connections.
Corrosion Resistance
Gold is highly resistant to corrosion and oxidation, which helps maintain the integrity of the electrical contacts over time. This is particularly important in harsh environments where the connectors may be exposed to moisture, humidity, or other corrosive elements.
Durability
Gold fingers are designed to withstand repeated insertions and removals without significant wear and tear. The gold plating on the contacts helps reduce friction and prevents the build-up of debris, ensuring a long lifespan for the connector.
Compatibility
Gold fingers are widely used and compatible with various industry standards, such as PCI, PCIe, and DIMM. This standardization allows for easy integration of components from different manufacturers, promoting interoperability and flexibility in system design.
Manufacturing Process of Gold Fingers
The manufacturing process of gold fingers involves several steps to ensure high-quality and reliable connectors:
-
PCB Fabrication: The PCB is designed and manufactured according to the specific requirements of the application. The edge of the PCB where the gold fingers will be located is carefully designed to ensure proper dimensions and spacing.
-
Nickel plating: Before applying the gold plating, a layer of nickel is deposited on the copper contacts. Nickel acts as a barrier layer, preventing the diffusion of copper into the gold layer and improving the adhesion of the gold plating.
-
Gold plating: The nickel-plated contacts are then coated with a thin layer of gold using electroplating or immersion plating techniques. The thickness of the gold layer typically ranges from 0.05 to 2.0 micrometers, depending on the application requirements.
-
Surface finish: After gold plating, the surface of the gold fingers may undergo additional treatments, such as selective plating or surface roughening, to enhance the contact properties and improve the reliability of the electrical connection.
-
Quality control: Stringent quality control measures are implemented throughout the manufacturing process to ensure the consistency and reliability of the gold fingers. This includes visual inspections, thickness measurements, and electrical testing to verify the performance of the connectors.
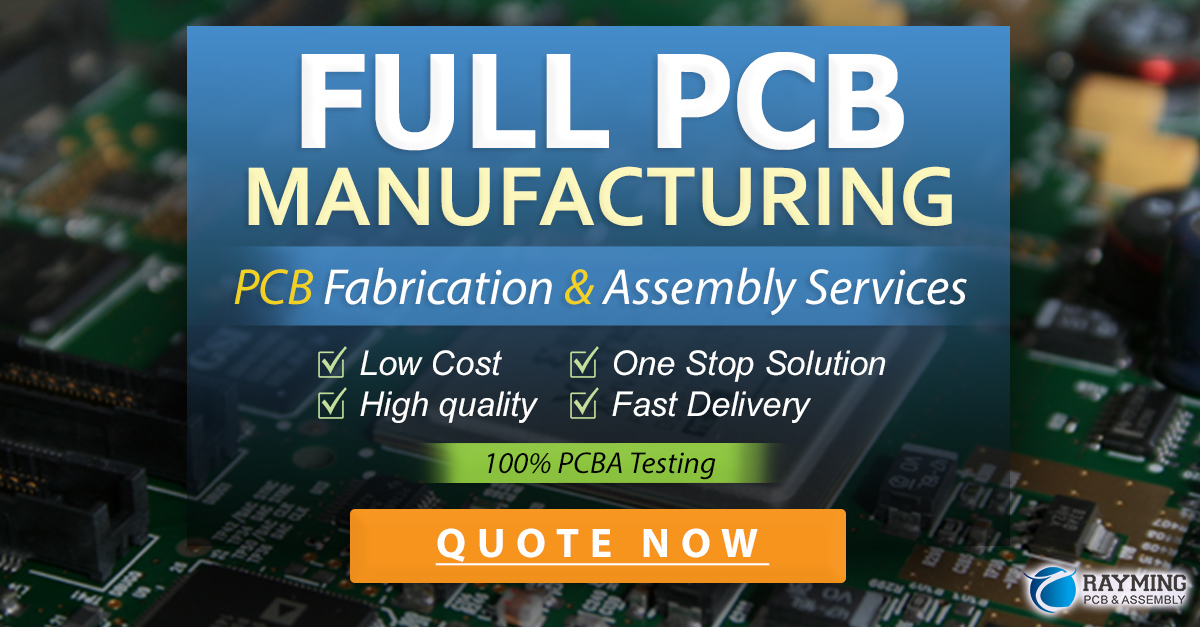
Gold Finger Design Considerations
When designing gold fingers for a specific application, several key factors must be considered:
Contact Pitch
The contact pitch refers to the distance between the centers of adjacent gold fingers. The pitch is determined by the specific standard or application requirements and can range from 0.5mm to 2.54mm or more. Smaller pitch sizes allow for higher density connections but may require more precise manufacturing processes.
Contact Thickness
The thickness of the gold fingers is another important design consideration. Thicker gold fingers offer better mechanical stability and current-carrying capacity but may increase the overall cost of the connector. The thickness is typically specified in terms of the copper thickness and the gold plating thickness.
Contact Length
The length of the gold fingers determines the mating depth of the connector and affects the overall mechanical stability of the connection. Longer gold fingers provide a more secure and reliable connection but may require more space on the PCB.
Contact Shape
Gold fingers can have various shapes, such as rectangular, chamfered, or rounded edges. The shape of the contacts can affect the ease of insertion and removal, as well as the contact pressure and reliability of the electrical connection.
Testing and Reliability of Gold Fingers
To ensure the reliability and performance of gold fingers, various testing methods are employed:
Contact Resistance Testing
Contact resistance testing measures the electrical resistance between the gold fingers and the mating connector. Low contact resistance is essential for maintaining signal integrity and minimizing power loss. The contact resistance is typically measured using a four-wire Kelvin method to eliminate the influence of lead resistance.
Insertion and Withdrawal Force Testing
Insertion and withdrawal force testing evaluates the mechanical properties of the gold fingers and the mating connector. The force required to insert and remove the connector is measured to ensure that it meets the specified requirements. Excessive insertion or withdrawal force can lead to damage or deformation of the gold fingers, while insufficient force may result in a poor electrical connection.
Environmental Testing
Gold fingers are often subjected to environmental testing to assess their performance under various conditions. This may include temperature cycling, humidity exposure, and vibration testing. These tests help determine the reliability and durability of the gold fingers in real-world applications.
Gold Finger Standards and Specifications
Several industry standards and specifications govern the design and manufacturing of gold fingers:
PCI (Peripheral Component Interconnect)
The PCI standard defines the requirements for gold fingers used in PCI expansion cards. It specifies the dimensions, pitch, and electrical characteristics of the connectors.
PCIe (PCI Express)
PCIe is an evolution of the PCI standard and defines the requirements for gold fingers used in PCIe expansion cards. It offers higher bandwidth and improved performance compared to PCI.
DIMM (Dual Inline Memory Module)
The DIMM standard specifies the requirements for gold fingers used in memory modules, such as DDR RAM. It defines the dimensions, pitch, and electrical characteristics of the connectors.
Custom Specifications
In some cases, custom gold finger specifications may be developed for specific applications or devices. These specifications are tailored to meet the unique requirements of the application, such as higher current-carrying capacity or enhanced mechanical stability.
Frequently Asked Questions (FAQ)
1. Can gold fingers be repaired if damaged?
In most cases, damaged gold fingers cannot be easily repaired. If the gold plating is worn off or the contacts are physically damaged, the entire PCB or component may need to be replaced. However, in some instances, specialized repair services may be able to restore the gold fingers using techniques such as gold plating or contact replacement.
2. Are gold fingers necessary for all electronic devices?
No, gold fingers are not necessary for all electronic devices. The choice of connector type depends on the specific requirements of the application, such as signal integrity, current-carrying capacity, and environmental conditions. In some cases, alternative connector types, such as pin headers or edge connectors with other plating materials, may be more suitable.
3. How does the thickness of the gold plating affect the performance of gold fingers?
The thickness of the gold plating on gold fingers can affect their performance in several ways:
Gold Plating Thickness | Effects |
---|---|
Thinner (e.g., 0.05 – 0.5 micrometers) | – Lower cost – Suitable for low-current applications – May have higher contact resistance |
Thicker (e.g., 0.5 – 2.0 micrometers) | – Higher cost – Better wear resistance – Lower contact resistance – Suitable for high-current applications |
The choice of gold plating thickness depends on the specific requirements of the application, such as the expected number of mating cycles, the current-carrying capacity, and the environmental conditions.
4. Can gold fingers be used in high-temperature applications?
Yes, gold fingers can be used in high-temperature applications, as gold has a relatively high melting point (1064°C) and good thermal conductivity. However, the maximum operating temperature of gold fingers is limited by the thermal properties of the PCB Substrate material and other components used in the assembly. In extreme high-temperature applications, alternative connector types or specialized high-temperature materials may be required.
5. How do gold fingers compare to other types of connectors in terms of cost?
Gold fingers are generally more expensive than other types of connectors, such as pin headers or edge connectors with tin or nickel plating. The higher cost is primarily due to the use of gold, which is a precious metal with excellent electrical and chemical properties. However, the increased cost of gold fingers is often justified by their superior performance, reliability, and durability in demanding applications.
Conclusion
Gold fingers are a crucial component in many electronic devices, providing reliable and efficient electrical connections between PCBs and other modules. The gold plating on the contacts ensures excellent conductivity, corrosion resistance, and durability, making gold fingers suitable for a wide range of applications, from consumer electronics to industrial equipment.
When designing and manufacturing gold fingers, several factors must be considered, such as contact pitch, thickness, length, and shape. Industry standards and specifications provide guidelines for ensuring compatibility and interoperability between different components and systems.
Rigorous testing and quality control measures are implemented to verify the performance and reliability of gold fingers under various conditions. Contact resistance testing, insertion and withdrawal force testing, and environmental testing are common methods used to assess the quality and durability of gold fingers.
As electronic devices continue to advance and become more complex, the importance of reliable and high-performance connectors like gold fingers will only continue to grow. By understanding the characteristics, manufacturing processes, and design considerations of gold fingers, engineers and designers can create more robust and efficient electronic systems that meet the demands of today’s increasingly connected world.
Leave a Reply