Introduction to EMC PCB Design
Electromagnetic Compatibility (EMC) is a critical aspect of Printed Circuit Board (PCB) design that ensures electronic devices function properly in their intended electromagnetic environment without causing or being susceptible to electromagnetic interference. EMC PCB Design involves implementing various techniques and adhering to EMC standards to minimize electromagnetic interference (EMI) and ensure the device’s compliance with regulatory requirements.
In this comprehensive guide, we will delve into the world of EMC PCB design, covering the fundamentals, key techniques, and relevant EMC standards. Whether you are a seasoned PCB designer or just starting, this guide will provide you with the knowledge and best practices to create EMC-compliant PCBs.
Understanding Electromagnetic Interference (EMI)
Electromagnetic Interference (EMI) refers to the unwanted disturbances caused by electromagnetic energy from one electronic device to another. EMI can disrupt the normal operation of electronic devices, leading to performance degradation, data corruption, or even complete system failure.
EMI can be classified into two main categories:
- Conducted EMI: Interference that propagates through conductive paths such as power lines, signal traces, or ground planes.
- Radiated EMI: Interference that propagates through the air as electromagnetic waves, generated by electronic components or traces acting as antennas.
To achieve EMC compliance, PCB designers must address both conducted and radiated EMI through proper design techniques and adherence to EMC standards.
Key Techniques for EMC PCB Design
1. Proper Grounding
Grounding is a fundamental aspect of EMC PCB design. Proper grounding helps to minimize EMI by providing a low-impedance path for electromagnetic energy to return to its source. Some key grounding techniques include:
- Using a solid ground plane to provide a low-impedance return path for high-frequency signals.
- Implementing a star grounding topology to minimize ground loops and reduce ground bounce.
- Connecting all ground points to the main ground plane using short and wide traces or vias.
2. Power Supply Decoupling
Power supply decoupling is crucial for reducing conducted EMI. Decoupling capacitors are placed close to the power pins of integrated circuits (ICs) to provide a local, low-impedance source of energy and filter out high-frequency noise. Consider the following:
- Use a combination of bulk, ceramic, and small-value capacitors to cover a wide frequency range.
- Place decoupling capacitors as close as possible to the IC power pins.
- Use low-inductance capacitors and minimize the loop area between the capacitor and the IC.
3. Signal Integrity
Maintaining signal integrity is essential for minimizing radiated EMI. High-speed digital signals can generate significant electromagnetic energy if not properly managed. Some signal integrity techniques include:
- Matching the impedance of transmission lines to minimize reflections and ringing.
- Using Controlled Impedance traces for critical high-speed signals.
- Minimizing the length of high-speed traces to reduce the antenna effect.
- Implementing termination resistors to prevent signal reflections.
4. Shielding
Shielding is an effective method to contain electromagnetic energy within a specific area and prevent it from interfering with other devices. Shielding techniques include:
- Using metal enclosures or conductive coatings to create a Faraday cage around sensitive components.
- Implementing shielding gaskets or conductive adhesives to ensure proper electrical contact between the shield and the PCB.
- Placing sensitive components away from potential sources of EMI.
5. Filtering
Filtering is used to suppress conducted EMI by attenuating unwanted high-frequency signals. Common filtering techniques include:
- Implementing EMI filters at the power input stage to attenuate conducted emissions.
- Using ferrite beads or common mode chokes to suppress high-frequency noise on signal lines.
- Placing filters close to the noise source to minimize the propagation of EMI.
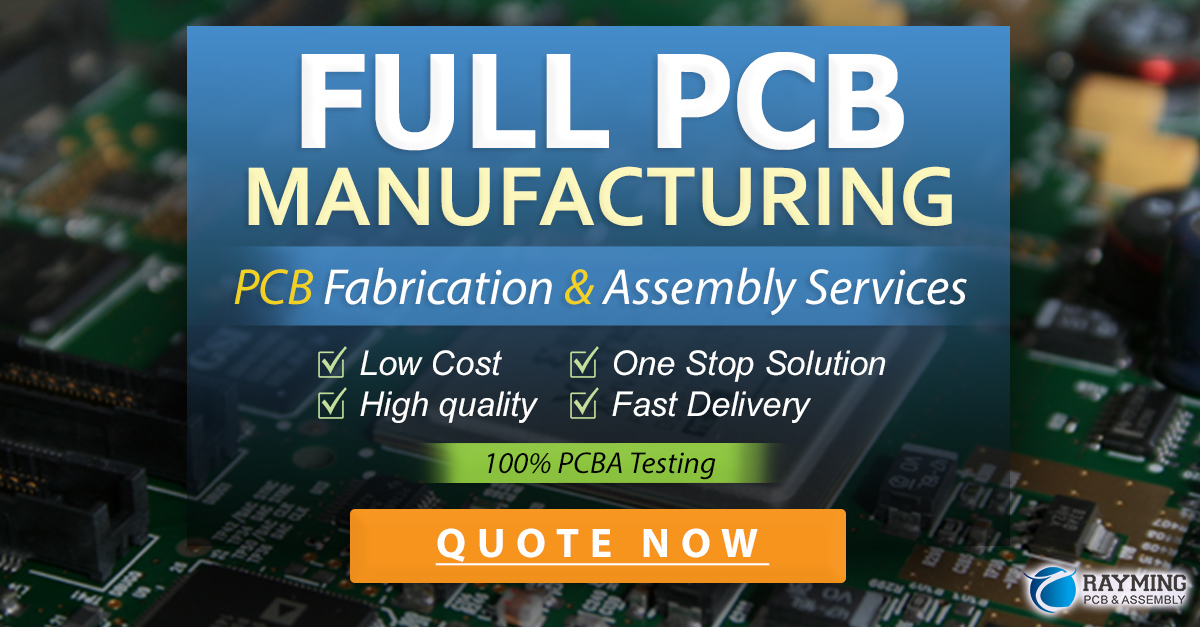
EMC Standards and Regulations
To ensure the electromagnetic compatibility of electronic devices, various EMC standards and regulations have been established by international organizations and regulatory bodies. Some of the key EMC standards include:
Standard | Description |
---|---|
FCC Part 15 | Rules and regulations for electromagnetic compatibility in the United States |
CISPR 22 | International standard for information technology equipment |
IEC 61000-4-2 | Electrostatic discharge (ESD) immunity test |
IEC 61000-4-3 | Radiated, radio-frequency, electromagnetic field immunity test |
IEC 61000-4-4 | Electrical fast transient/burst immunity test |
IEC 61000-4-5 | Surge immunity test |
IEC 61000-4-6 | Immunity to conducted disturbances, induced by radio-frequency fields |
PCB designers must be aware of the applicable EMC standards based on the target market and the specific industry requirements. Compliance with these standards ensures that the electronic device can operate reliably in its intended electromagnetic environment.
EMC Testing and Certification
To validate the EMC performance of a PCB and ensure compliance with relevant standards, EMC testing and certification are essential. EMC testing involves subjecting the device to various electromagnetic disturbances and measuring its emissions and immunity levels.
Common EMC tests include:
- Conducted Emissions Test: Measures the electromagnetic energy conducted through power lines or signal cables.
- Radiated Emissions Test: Measures the electromagnetic energy radiated by the device into the surrounding environment.
- Conducted Immunity Test: Evaluates the device’s ability to withstand conducted electromagnetic disturbances.
- Radiated Immunity Test: Assesses the device’s immunity to radiated electromagnetic fields.
After successfully passing the required EMC tests, the device can be certified as compliant with the relevant EMC standards. Certification marks, such as the FCC mark or CE mark, indicate that the device has met the necessary EMC requirements and can be legally sold in the target market.
Best Practices for EMC PCB Design
To achieve optimal EMC performance and streamline the design process, consider the following best practices:
- Plan for EMC early in the design process: Incorporate EMC considerations from the initial stages of PCB design to avoid costly redesigns later.
- Identify potential sources of EMI: Analyze the PCB layout and identify components or traces that may generate or be susceptible to EMI.
- Minimize loop areas: Keep signal traces and Return Paths as close together as possible to minimize loop areas and reduce radiated emissions.
- Use proper layer stacking: Arrange the PCB Layers strategically, with power and ground planes shielding sensitive signal layers.
- Route signals carefully: Avoid routing high-speed signals near potential sources of EMI or parallel to other sensitive traces.
- Implement good design practices: Follow established design guidelines, such as using ground planes, proper trace widths, and avoiding sharp corners or sudden impedance changes.
- Collaborate with experienced EMC engineers: Work closely with EMC experts to review the design, identify potential issues, and implement necessary mitigation techniques.
- Perform pre-compliance testing: Conduct in-house pre-compliance testing to identify and address EMC issues early in the design process.
- Document EMC design decisions: Maintain clear documentation of EMC design choices, test results, and any modifications made for future reference and troubleshooting.
By following these best practices and staying up to date with the latest EMC standards and techniques, PCB designers can create robust and EMC-compliant designs that meet the requirements of the target market.
Frequently Asked Questions (FAQ)
- What is the difference between EMI and EMC?
-
EMI (Electromagnetic Interference) refers to the unwanted disturbances caused by electromagnetic energy from one device to another. EMC (Electromagnetic Compatibility) is the ability of a device to function properly in its intended electromagnetic environment without causing or being susceptible to EMI.
-
Why is EMC important in PCB design?
-
EMC is crucial in PCB design to ensure that electronic devices can operate reliably and safely in their intended electromagnetic environment. Proper EMC design helps to minimize electromagnetic interference, prevent malfunctions, and ensure compliance with regulatory standards.
-
What are the main sources of EMI in a PCB?
-
The main sources of EMI in a PCB include high-speed digital signals, switching power supplies, clock signals, and interconnects acting as antennas. Improper grounding, poor shielding, and inadequate filtering can also contribute to EMI.
-
How can I minimize radiated EMI in my PCB design?
-
To minimize radiated EMI, you can use techniques such as proper grounding, shielding sensitive components, minimizing loop areas, maintaining signal integrity, and implementing filters. Routing high-speed signals away from potential EMI sources and using controlled impedance traces can also help reduce radiated emissions.
-
What are the consequences of not complying with EMC standards?
- Non-compliance with EMC standards can result in legal and financial consequences. Devices that do not meet the required EMC standards may not be allowed to be sold in certain markets, leading to product recalls, fines, and damage to the company’s reputation. Additionally, non-compliant devices may cause electromagnetic interference that can disrupt the operation of other electronic devices, potentially leading to safety hazards or malfunctions.
Conclusion
EMC PCB design is a critical aspect of creating reliable and compliant electronic devices. By understanding the fundamentals of EMI, implementing key techniques such as proper grounding, power supply decoupling, signal integrity, shielding, and filtering, and adhering to relevant EMC standards, PCB designers can effectively mitigate electromagnetic interference and ensure the proper functioning of their devices.
Staying up to date with the latest EMC standards, collaborating with experienced EMC engineers, and following best practices throughout the design process are essential for achieving optimal EMC performance. By prioritizing EMC considerations from the early stages of PCB design, designers can avoid costly redesigns, streamline the certification process, and deliver high-quality, EMC-compliant products to the market.
Leave a Reply