What is PCB Solder Mask Opening (SMO)?
PCB Solder Mask Opening (SMO) refers to the openings or exposed areas in the solder mask layer of a printed circuit board (PCB) where components are soldered. The solder mask is a thin lacquer-like layer applied over the copper traces of a PCB, leaving only the areas that need to be soldered exposed. SMOs are created to allow the solder to form a reliable electrical and mechanical connection between the component leads and the PCB pads.
Functions of Solder Mask Opening
The primary functions of SMO include:
-
Solder Application: SMOs provide access for the molten solder to bond with the exposed copper pads and component leads during the soldering process.
-
Insulation: The solder mask acts as an insulating layer, preventing short circuits and protecting the copper traces from oxidation and damage.
-
Aesthetics: SMOs contribute to the overall appearance of the PCB, providing a clean and professional look.
Types of Solder Mask Opening
There are two main types of SMOs:
-
Non-Solder Mask Defined (NSMD): In this type, the copper pad is larger than the opening in the solder mask. The solder mask overlaps the edges of the copper pad, and the opening is smaller than the pad itself. NSMD is the most common type of SMO.
-
Solder Mask Defined (SMD): In SMD, the opening in the solder mask is larger than the copper pad. The solder mask does not overlap the edges of the pad, and the copper is exposed only within the opening. SMD is used in applications that require higher precision and smaller pad sizes.
Designing Solder Mask Openings
SMO Design Guidelines
When designing SMOs, consider the following guidelines:
-
Pad Size: Ensure that the pad size is appropriate for the component lead size and the soldering process. The pad should be large enough to accommodate the lead and allow for proper solder fillets.
-
SMO Size: The size of the SMO should be slightly larger than the pad size to allow for proper solder coverage and to account for any misalignment during the solder mask application process.
-
Spacing: Maintain adequate spacing between SMOs to prevent solder bridging and short circuits. The spacing should be based on the PCB manufacturing capabilities and the soldering process requirements.
-
Solder Mask Clearance: Provide sufficient clearance between the solder mask and the component body to avoid any interference during assembly.
SMO Size and Spacing
The size and spacing of SMOs depend on various factors, such as the component package, PCB manufacturing capabilities, and the soldering process. The following table provides general guidelines for SMO size and spacing based on common component packages:
Component Package | Pad Size (mm) | SMO Size (mm) | Spacing (mm) |
---|---|---|---|
0201 | 0.25 x 0.125 | 0.35 x 0.225 | 0.2 |
0402 | 0.5 x 0.25 | 0.6 x 0.35 | 0.3 |
0603 | 0.8 x 0.4 | 0.9 x 0.5 | 0.4 |
0805 | 1.25 x 0.75 | 1.35 x 0.85 | 0.5 |
1206 | 1.6 x 0.8 | 1.7 x 0.9 | 0.6 |
SOIC | 1.27 x 0.6 | 1.47 x 0.8 | 0.5 |
TQFP | 0.5 x 0.3 | 0.6 x 0.4 | 0.3 |
BGA | 0.5 (ball diameter) | 0.6 (ball diameter) | 0.5 (pitch) |
Note that these are general guidelines, and the actual dimensions may vary based on specific design requirements and manufacturing capabilities.
Solder Mask Clearance
Solder mask clearance is the distance between the edge of the SMO and the component body. Adequate clearance is essential to ensure proper component placement and to avoid any interference between the solder mask and the component during assembly. The following table provides recommended solder mask clearance values for various Component Types:
Component Type | Solder Mask Clearance (mm) |
---|---|
Chip Components | 0.05 – 0.1 |
Gull Wing Leads (QFP, SOP) | 0.1 – 0.15 |
J-Lead Components (SOJ, PLCC) | 0.1 – 0.15 |
BGAs | 0.1 – 0.15 |
Connectors | 0.15 – 0.3 |
These clearance values are general recommendations, and designers should consult the component manufacturer’s datasheets and the PCB Fabrication vendor’s guidelines for specific requirements.
SMO Manufacturing Process
Solder Mask Application Methods
There are two primary methods for applying solder mask to a PCB:
-
Silk Screen Printing: In this method, a fine mesh screen is used to apply the liquid solder mask onto the PCB surface. The screen has openings that correspond to the areas where the solder mask should be applied. The PCB is placed under the screen, and the solder mask is forced through the openings using a squeegee. This method is suitable for low-volume production and prototype boards.
-
Liquid Photo Imaging (LPI): LPI is a photolithographic process that uses a photosensitive solder mask. The liquid solder mask is applied uniformly over the entire PCB surface, and then it is exposed to UV light through a photomask. The photomask contains the negative image of the desired solder mask pattern. The exposed areas of the solder mask become hardened, while the unexposed areas remain liquid and are later removed in the developing process. LPI is the preferred method for high-volume production due to its precision and consistency.
Solder Mask Materials
Solder mask materials are typically epoxy-based or acrylic-based polymers that are formulated to provide excellent insulation, chemical resistance, and thermal stability. Some common solder mask materials include:
-
Liquid Photoimageable Solder Mask (LPSM): LPSM is the most widely used solder mask material for high-volume PCB production. It is a photosensitive polymer that can be applied using the LPI process, resulting in high-resolution and precise SMOs.
-
Dry Film Solder Mask (DFSM): DFSM is a solid photosensitive film that is laminated onto the PCB surface using heat and pressure. It is then exposed to UV light through a photomask and developed to create the SMOs. DFSM is suitable for applications that require high thickness and better chemical resistance.
-
Liquid Screen Printable Solder Mask (LSPSM): LSPSM is a non-photosensitive liquid solder mask that is applied using the silk screen printing method. It is cured using heat or UV light after application. LSPSM is ideal for low-volume production and prototype boards.
Solder Mask Colors
Solder mask is available in various colors, with green being the most common. Other popular colors include:
- Blue
- Red
- Yellow
- Black
- White
The choice of solder mask color is usually a matter of aesthetic preference, but in some cases, specific colors may be chosen for functional reasons, such as improved visibility for optical inspection or color-coding for different board types.
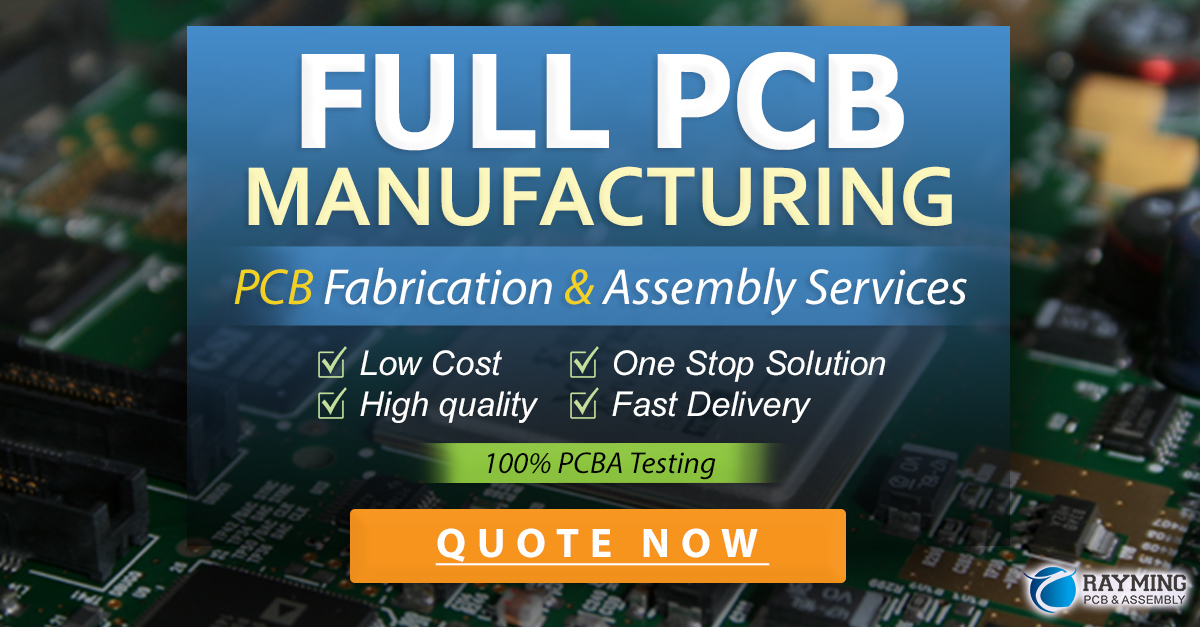
SMO Quality Control
Visual Inspection
Visual inspection is the first step in ensuring the quality of SMOs. Inspectors check for various defects, such as:
-
Solder Mask Misalignment: Misaligned solder mask can lead to exposed copper traces or partially covered pads, which can cause short circuits or poor solderability.
-
Solder Mask Bridging: Solder mask bridges occur when the solder mask inadvertently covers the space between two adjacent pads, causing them to be electrically connected.
-
Solder Mask Voids: Voids are small holes or gaps in the solder mask that expose the underlying copper. They can be caused by air bubbles, contamination, or improper curing of the solder mask.
-
Solder Mask Peeling: Peeling or lifting of the solder mask can occur due to poor adhesion, mechanical stress, or exposure to harsh chemicals.
Visual inspection is performed using magnification tools, such as magnifying lenses or microscopes, and is often aided by automated optical inspection (AOI) systems.
Automated Optical Inspection (AOI)
AOI systems use high-resolution cameras and advanced image processing algorithms to detect and classify SMO defects. These systems can quickly scan the entire PCB surface and compare the captured images to a reference image or CAD data. AOI systems can detect defects such as:
- Solder mask misalignment
- Solder mask bridging
- Solder mask voids
- Insufficient or excessive solder mask coverage
AOI systems provide fast and consistent inspection results, reducing the reliance on manual visual inspection and improving the overall quality control process.
Electrical Testing
Electrical testing is performed to ensure that the SMOs provide the necessary insulation and do not cause any short circuits or open connections. Some common electrical tests include:
-
Continuity Test: This test verifies that the intended electrical connections are present and that there are no unintended short circuits between adjacent pads or traces.
-
Insulation Resistance Test: This test measures the resistance between adjacent pads or traces to ensure that the solder mask provides adequate electrical insulation.
-
High-Voltage Test: This test applies a high voltage between the conductors and the substrate to detect any weaknesses in the solder mask’s insulating properties.
Electrical testing is typically performed using automated test equipment (ATE) or dedicated PCB test fixtures.
Frequently Asked Questions (FAQ)
-
What is the purpose of solder mask on a PCB?
The solder mask serves as an insulating layer that protects the copper traces from oxidation, prevents short circuits, and provides a surface for applying solder to the exposed pads during the assembly process. -
What is the difference between NSMD and SMD solder mask openings?
In NSMD (Non-Solder Mask Defined) openings, the copper pad is larger than the opening in the solder mask, and the mask overlaps the edges of the pad. In SMD (Solder Mask Defined) openings, the solder mask opening is larger than the copper pad, and the copper is exposed only within the opening. -
How do I choose the right solder mask color for my PCB?
The choice of solder mask color is usually a matter of aesthetic preference. Green is the most common color, but other colors like blue, red, yellow, black, and white are also available. In some cases, specific colors may be chosen for functional reasons, such as improved visibility for optical inspection or color-coding for different board types. -
What are the most common defects associated with solder mask openings?
The most common SMO defects include solder mask misalignment, bridging, voids, and peeling. These defects can lead to short circuits, poor solderability, and reduced insulation properties. -
How can I ensure the quality of solder mask openings on my PCB?
To ensure the quality of SMOs, use a combination of visual inspection, automated optical inspection (AOI), and electrical testing. Adhere to the recommended design guidelines for SMO size, spacing, and clearance, and work closely with your PCB fabrication vendor to establish clear quality control specifications.
Leave a Reply