Introduction to BGA Components
BGA (Ball Grid Array) components are a type of surface-mount packaging used for integrated circuits (ICs) and other electronic components. They are characterized by a grid of solder balls on the bottom of the package, which are used to attach the component to a printed circuit board (PCB). BGA components offer several advantages over other packaging types, including higher pin count, smaller footprint, and better thermal and electrical performance.
Advantages of BGA Components
- Higher pin count: BGA packages can accommodate a large number of pins in a small area, making them ideal for complex ICs with many input/output (I/O) connections.
- Smaller footprint: The grid array layout of BGA packages allows for a more compact design compared to other packaging types, such as quad flat pack (QFP) or thin small outline package (TSOP).
- Better thermal performance: The solder balls on the bottom of the BGA package provide a direct thermal path from the IC to the PCB, improving heat dissipation.
- Improved electrical performance: The shorter lead lengths and lower inductance of BGA packages result in better signal integrity and reduced noise.
Types of BGA Components
There are several types of BGA components, each with its own characteristics and applications. Some of the most common types include:
1. Plastic BGA (PBGA)
Plastic BGA (PBGA) components are the most common type of BGA package. They consist of a plastic substrate with the IC mounted on top and the solder balls attached to the bottom. PBGA packages are cost-effective and suitable for a wide range of applications, including:
- Consumer electronics
- Telecommunications
- Industrial control systems
Advantages of PBGA
- Lower cost compared to ceramic BGA packages
- Good thermal and electrical performance
- Available in a wide range of sizes and pin counts
Disadvantages of PBGA
- Limited thermal dissipation compared to ceramic BGA packages
- Susceptible to moisture absorption, which can lead to package cracking during reflow soldering
2. Ceramic BGA (CBGA)
Ceramic BGA (CBGA) components use a ceramic substrate instead of a plastic one. The IC is mounted on the ceramic substrate, and the solder balls are attached to the bottom. CBGA packages offer better thermal and mechanical performance than PBGA packages, making them suitable for applications that require high reliability, such as:
- Aerospace and defense
- High-performance computing
- Medical devices
Advantages of CBGA
- Excellent thermal conductivity and dissipation
- High mechanical strength and stability
- Low moisture absorption, reducing the risk of package cracking
Disadvantages of CBGA
- Higher cost compared to PBGA packages
- Limited availability and longer lead times
3. Tape BGA (TBGA)
Tape BGA (TBGA) components use a flexible tape substrate, typically made of polyimide, with the IC mounted on top and the solder balls attached to the bottom. TBGA packages are thinner and lighter than PBGA and CBGA packages, making them suitable for applications that require a low profile, such as:
- Mobile devices
- Wearable electronics
- Smartcards
Advantages of TBGA
- Ultra-thin profile (as low as 0.3 mm)
- Lightweight
- Flexible substrate allows for bending and folding
Disadvantages of TBGA
- Limited thermal dissipation due to thin substrate
- Susceptible to mechanical damage during handling and assembly
4. Cavity Down BGA (CDBGA)
Cavity Down BGA (CDBGA) components have the IC mounted in a cavity on the bottom of the substrate, with the solder balls surrounding the cavity. This configuration allows for better thermal dissipation and protection of the IC. CDBGA packages are commonly used in applications that require high performance and reliability, such as:
- High-end networking equipment
- Server and storage systems
- Automotive electronics
Advantages of CDBGA
- Excellent thermal dissipation due to direct contact between the IC and the PCB
- Enhanced mechanical protection for the IC
- Improved signal integrity due to shorter lead lengths
Disadvantages of CDBGA
- Higher cost compared to standard BGA packages
- More complex assembly process
5. Package on Package (PoP)
Package on Package (PoP) is a stacking technology that combines two or more BGA packages on top of each other. The bottom package typically contains a processor or baseband IC, while the top package contains memory or other components. PoP allows for high-density packaging and is commonly used in applications that require a small form factor, such as:
- Smartphones
- Tablets
- Wearable devices
Advantages of PoP
- High-density packaging
- Reduced footprint compared to side-by-side placement of components
- Improved electrical performance due to shorter interconnects
Disadvantages of PoP
- Higher assembly complexity and cost
- Thermal management challenges due to stacked configuration
- Limited flexibility in component selection and placement
Comparison of BGA Component Types
BGA Type | Substrate Material | Thermal Performance | Mechanical Strength | Moisture Sensitivity | Common Applications |
---|---|---|---|---|---|
PBGA | Plastic | Good | Good | High | Consumer electronics, telecommunications, industrial control |
CBGA | Ceramic | Excellent | Excellent | Low | Aerospace, defense, high-performance computing, medical devices |
TBGA | Polyimide tape | Limited | Limited | High | Mobile devices, wearable electronics, smartcards |
CDBGA | Plastic or ceramic | Excellent | Good | Low | Networking equipment, server and storage systems, automotive electronics |
PoP | Varies | Varies | Varies | Varies | Smartphones, tablets, wearable devices |
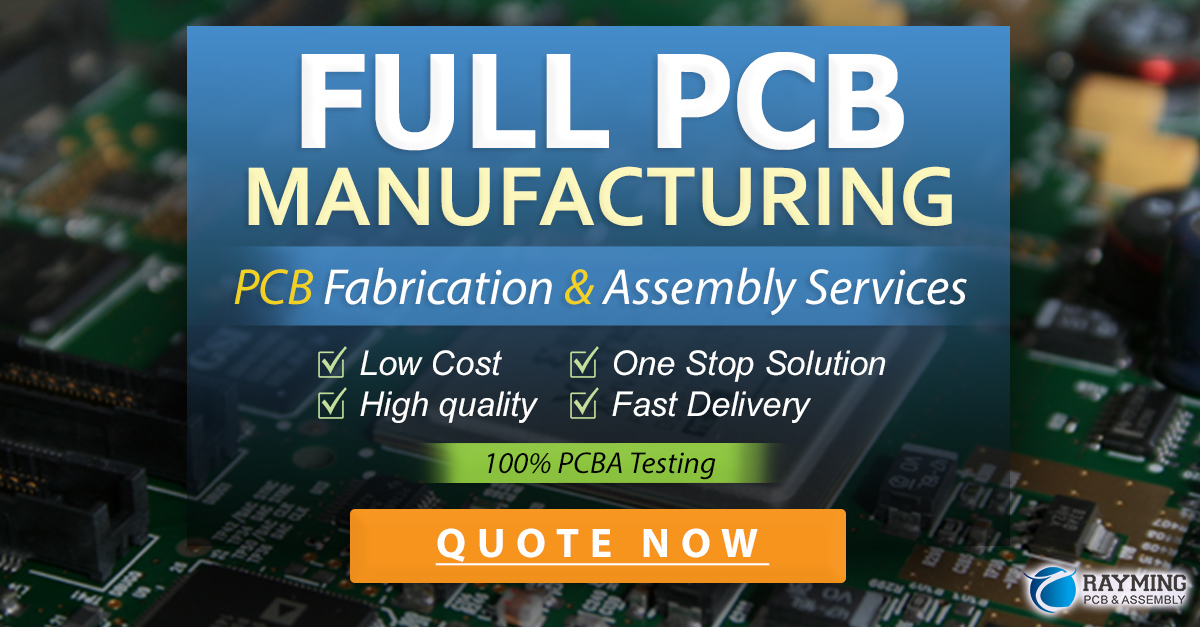
Selecting the Right BGA Component
When choosing a BGA component for your application, consider the following factors:
- Pin count and package size: Ensure that the BGA package has enough pins to accommodate your design and fits within the available space on the PCB.
- Thermal requirements: Consider the power dissipation of the IC and choose a BGA package with adequate thermal performance.
- Mechanical requirements: Evaluate the mechanical stress and strain that the BGA package will be subjected to and select a package with sufficient strength and stability.
- Moisture sensitivity: Assess the exposure to moisture during storage and assembly, and choose a BGA package with an appropriate moisture sensitivity level (MSL) rating.
- Cost and availability: Consider the cost and lead time of the BGA package, as well as any additional assembly or testing requirements.
Assembly and Rework Considerations
Assembling and reworking BGA components requires specialized equipment and processes due to the fine pitch and hidden solder joints. Some key considerations include:
- Solder paste printing: Use a stencil with the appropriate aperture size and shape to ensure proper solder paste deposition on the PCB pads.
- Component placement: Use a pick-and-place machine with high accuracy and precision to place the BGA component on the PCB.
- Reflow soldering: Follow the recommended reflow profile for the specific BGA package and PCB material to achieve reliable solder joints.
- Inspection: Use X-ray or 3D automated optical inspection (AOI) to verify the integrity of the solder joints, as they are hidden under the package.
- Rework: If a BGA component needs to be replaced, use a dedicated BGA Rework station with precise temperature control and component alignment capabilities.
Frequently Asked Questions (FAQ)
1. What is the difference between a BGA and a QFP package?
A BGA package has a grid array of solder balls on the bottom, while a QFP package has leads extending from the sides of the package. BGA packages offer higher pin count density and better thermal and electrical performance compared to QFP packages.
2. Can BGA components be soldered using a manual soldering iron?
No, BGA components require specialized reflow soldering equipment due to the fine pitch and hidden solder joints. Manual soldering is not recommended, as it can result in poor solder joint quality and damage to the component or PCB.
3. How can I inspect the solder joints of a BGA component?
Solder joints of BGA components are hidden under the package, making visual inspection impossible. X-ray or 3D automated optical inspection (AOI) techniques are used to verify the integrity of the solder joints.
4. What is the difference between a PBGA and a CBGA package?
PBGA packages use a plastic substrate, while CBGA packages use a ceramic substrate. Ceramic substrates offer better thermal conductivity and mechanical stability compared to plastic substrates, but they are also more expensive.
5. Are BGA components more expensive than other package types?
BGA components can be more expensive than other package types due to the higher pin count and more complex assembly process. However, the cost difference varies depending on the specific component and the volume of production. In some cases, the improved performance and smaller footprint of BGA components can justify the higher cost.
Conclusion
BGA components are a popular choice for a wide range of electronic applications due to their high pin count density, small footprint, and excellent thermal and electrical performance. Understanding the different types of BGA packages and their characteristics is crucial for selecting the right component for your design. When working with BGA components, it is essential to follow best practices for assembly and rework to ensure reliable and high-quality solder joints. By considering factors such as thermal requirements, mechanical stability, and moisture sensitivity, you can choose the most suitable BGA component for your application and achieve optimal performance and reliability.
Leave a Reply