What is a BGA Rework Station?
A BGA rework station is a specialized machine used for removing and replacing BGA components on printed circuit boards (PCBs). BGA components have an array of solder balls on their underside instead of pins, which allows for a high density of connections in a small package. However, this also makes BGAs more challenging to work with compared to traditional through-hole or surface mount components.
A typical BGA rework station consists of several key components:
- Heating system: Used to precisely heat the BGA component and surrounding area to melt the solder balls.
- Placement system: Allows for accurate alignment and placement of the BGA component on the PCB.
- Vision system: Provides magnification and assists with alignment, inspection, and process monitoring.
- Software and controls: Enable the operator to fine-tune and monitor the rework process.
Why Use a BGA Rework Station?
There are several reasons why a dedicated BGA rework station is essential:
- Precision: BGAs require very precise control over heating and placement due to their small size and high pin count. Manual methods are inadequate.
- Reliability: Proper BGA rework ensures reliable solder joints and prevents damage to the component and PCB.
- Efficiency: A rework station streamlines the process and reduces time and effort compared to manual techniques.
- Versatility: Advanced BGA rework stations can handle a wide range of component sizes and types.
Whether you are doing prototyping, small-scale production, or repair and refurbishment, a BGA rework station is an invaluable tool that will pay for itself in terms of improved results and efficiency.
Key Factors When Choosing a BGA Rework Station
With a wide range of BGA rework stations on the market, it’s important to carefully evaluate your options. Consider the following key factors:
Heating System
The heating system is the heart of a BGA rework station. Look for the following characteristics:
- Precision temperature control: The ability to accurately set and maintain temperatures is critical. Look for closed-loop temperature control and high-quality sensors.
- Heating zones: Multiple independent heating zones allow for precise control over the heating profile. This is especially important for large BGAs or temperature-sensitive components.
- Ramp rate control: The ability to control the speed of heating and cooling (ramp rate) is important for preventing thermal shock and ensuring proper solder reflow.
Heating System Feature | Importance |
---|---|
Precision temperature control | Essential for reliable soldering |
Multiple heating zones | Enables optimal profiling |
Ramp rate control | Prevents thermal damage |
Placement System
Accurate placement is essential for a successful BGA rework. The placement system should offer:
- High precision: Look for systems with high-resolution motion control and fine-pitch capability for the most challenging BGA components.
- Interchangeable heads: The ability to swap out placement heads allows for handling a wider range of component sizes and types.
- Adjustable force sensing: Controllable placement force helps prevent damage to delicate components.
A high-quality, versatile placement system will accommodate both your current and future BGA rework needs.
Vision System
A clear view of the work area is a must for precision BGA rework. Key aspects of the vision system include:
- Magnification: Adequate magnification is essential for inspecting solder joints and component alignment.
- Clarity and focal planes: The image should be crisp and clear, with the ability to focus on different planes (component top, solder balls, PCB pads).
- Integrated vs. separate: Some rework stations integrate the vision system into the machine, while others offer separate, standalone vision systems. Integrated systems offer convenience, while separate systems provide flexibility.
- Recording capability: The ability to record video of the rework process is valuable for process documentation and technician training.
Vision System Aspect | Optimal Characteristics |
---|---|
Magnification | 20X or greater |
Image quality | High resolution, adjustable focus |
Recording | Built-in HD video recording |
Software and Control System
The software and controls tie everything together and provide the interface for the operator. Important considerations include:
- User interface: The control software should be intuitive and easy to navigate. Look for clear displays and logical controls.
- Profile management: Pre-programmed profiles for common BGA components save time. The ability to store, edit, and share custom profiles is also valuable.
- Real-time monitoring: Real-time display of key process parameters (temperatures, times, placement force) allows the operator to monitor the rework process and make adjustments as needed.
- Data logging: Automatic logging of process data enables traceability and aids in troubleshooting and process optimization.
Well-designed software and controls can greatly enhance the usability of the rework station and make the operator’s job easier.
Thermal Capability and Component Range
Consider the range of component sizes and types that you will be working with, both now and in the future. The rework station should be able to handle your largest and most challenging BGAs. Key specifications to look for include:
- Temperature range: The heating system should accommodate the reflow profiles of your BGA components. Common peak temperatures range from 240-260°C.
- Component size range: The placement system should be able to handle your smallest and largest BGA packages.
- PCB size capacity: The machine should accommodate the PCB sizes that you work with. Some machines offer extendable PCB supports for larger boards.
Select a machine that offers some headroom beyond your current needs to futureproof your investment.
Ease of Use and Maintenance
The best BGA rework station is one that your technicians can operate confidently and efficiently. Ease of use considerations include:
- Intuitive controls: Well-labeled buttons, knobs, and touchscreens make for a shallower learning curve.
- Quick changeover: Look for features like quick-change nozzles and placement heads to streamline setup between different jobs.
- Ergonomics: A comfortable working height, good lighting, and an adjustable monitor position can make a big difference in operator comfort and productivity over long shifts.
- Accessibility for maintenance: Regular maintenance is essential for keeping the machine in top operating condition. Easily accessible parts and modular components simplify maintenance tasks.
Don’t overlook the importance of ergonomics and ease of maintenance, as these factors have a significant impact on productivity and long-term cost of ownership.
Budget and Return on Investment
Expect to spend a few thousand dollars for an entry-level BGA rework station, with high-end machines costing upwards of $30,000 or more. When setting your budget, consider both upfront costs and total cost of ownership:
- Upfront cost: This includes the base price of the machine plus any necessary accessories, options, and facilities modifications.
- Consumables: Include the cost of solder paste, flux, nozzles, etc.
- Maintenance: Budget for annual calibration, preventive maintenance, and occasional repairs.
- Training: Account for any necessary operator training and certification.
Also consider the return on investment (ROI) in terms of improved quality, efficiency, and capabilities. Estimate how many BGA repairs or rework operations you will perform annually to gauge how quickly the machine will pay for itself.
Cost Consideration | Example |
---|---|
Upfront machine cost | $15,000 |
Consumables (annual) | $2,000 |
Maintenance and calibration (annual) | $1,500 |
Operator training | $1,000 |
Total cost of ownership (5 years) | $32,500 |
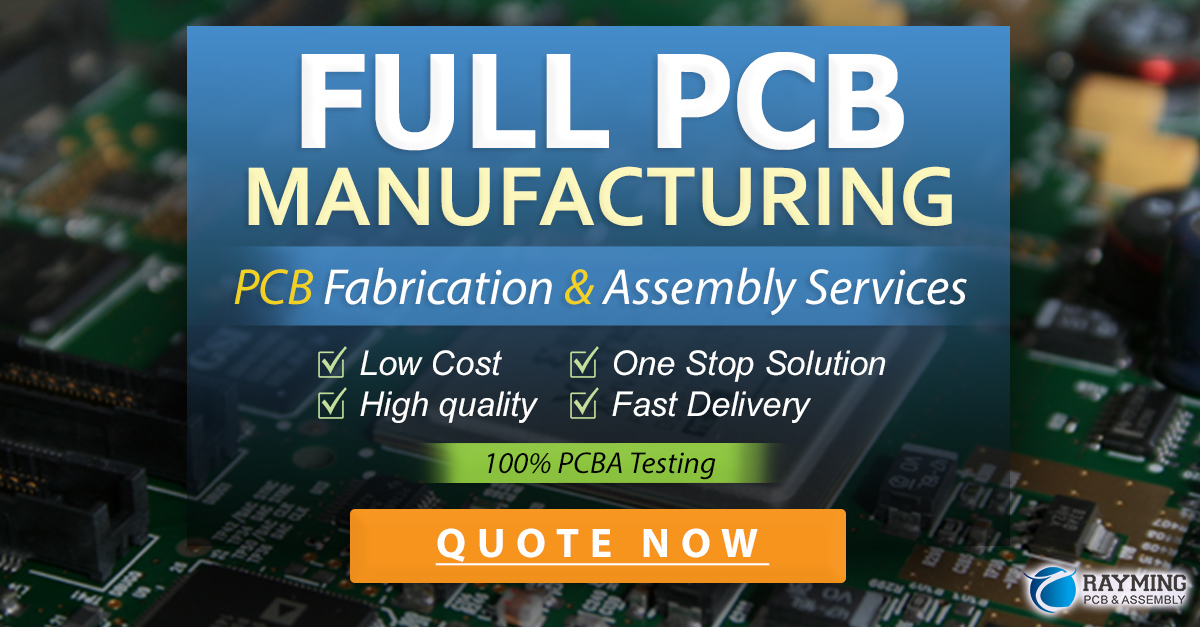
BGA Rework Station Comparison
To help narrow down your options, here is a comparison of three popular BGA rework stations:
Model | Heating System | Placement System | Vision System | Price Range |
---|---|---|---|---|
A | 3 zones, 2500W | +/- 0.025 mm | 40X, integrated | $15,000-$20,000 |
B | 4 zones, 3000W | +/- 0.01 mm | 50X, separate | $25,000-$30,000 |
C | 2 zones, 1800W | +/- 0.05 mm | 30X, integrated | $10,000-$15,000 |
Each model offers a different balance of capabilities and price points to suit different needs and budgets. Be sure to do a hands-on demo if possible to see which machine best fits your requirements and preferences.
BGA Rework Station Setup and Operation
Once you’ve chosen a BGA rework station, proper setup and operation are key to achieving the best results. Here are the basic steps:
- Prepare the PCB: Clean the site, apply flux, and preheat if needed.
- Program the profile: Select or create a thermal profile to match the BGA component and PCB.
- Align and place: Use the vision system and placement system to accurately align and place the component.
- Reflow soldering: Run the thermal profile to reflow the solder, forming a proper joint between the BGA and PCB.
- Inspect and clean: Verify joint quality with visual or X-ray inspection. Clean off flux residue.
Following proper procedures and using quality consumables will help ensure reliable BGA joints and prevent costly rework.
Frequently Asked Questions
What is a typical ROI for a BGA rework station?
The return on investment depends on the volume and value of the BGA rework operations. As an example, if the machine enables 500 repairs annually with an average value of $100 each, that’s $50,000 in annual revenue. A $20,000 machine would pay for itself in less than 6 months in this scenario.
How do I choose the right nozzle for my BGA components?
Nozzle selection depends on the size and shape of the BGA package. The nozzle should be slightly larger than the component to allow for proper air flow around the perimeter. Many machines come with a selection of standard nozzles, with custom nozzles available for unusual package sizes. Consult your machine’s documentation or supplier for specific recommendations.
What regular maintenance is required for a BGA rework station?
Regular calibration of the heating system and placement system is important for maintaining accuracy. Nozzles and placement heads should be cleaned periodically to prevent flux buildup. Filters and cooling fans should be cleaned or replaced as needed. Follow the manufacturer’s recommended maintenance schedule and procedures.
Can I use a BGA rework station for repairing PCBs with lead-free solder?
Yes, but lead-free solder requires higher reflow temperatures compared to traditional tin-lead solder. Make sure your rework station can achieve the necessary peak temperature for lead-free profiles (usually around 260°C). You may also need different nozzles and consumables optimized for lead-free soldering.
How long does it take to learn to use a BGA rework station?
The learning curve depends on the complexity of the machine and the operator’s prior experience. Most technicians can become proficient with a new machine within a few days to a week of hands-on practice. Look for a supplier that offers training resources such as online courses, application notes, and tech support to shorten the learning curve.
Conclusion
Choosing the right BGA rework station is a critical decision for any electronics manufacturing or repair operation. By carefully evaluating your requirements and comparing the available options, you can select a machine that will deliver reliable results, streamline your processes, and provide a rapid return on investment. Remember to prioritize precision, versatility, and ease of use to get the most value from your BGA rework station.
Leave a Reply