Introduction to PCB Reflow Soldering
Reflow Soldering is a process used in the manufacturing of printed circuit boards (PCBs) to attach surface mount components to the board. This process involves applying solder paste to the PCB, placing the components on the board, and then heating the entire assembly to melt the solder and form a permanent connection between the components and the PCB. Reflow soldering is a critical step in the PCB manufacturing process, as it ensures the reliability and functionality of the finished product.
Advantages of Reflow Soldering
- High-quality solder joints
- Consistent and repeatable process
- Suitable for high-volume production
- Allows for the use of smaller components and higher component density
Understanding the Reflow Soldering Process
The reflow soldering process consists of several stages, each of which plays a crucial role in achieving a successful outcome.
Solder Paste Application
The first step in the reflow soldering process is the application of solder paste to the PCB. Solder paste is a mixture of tiny solder particles suspended in a flux medium. The paste is applied to the PCB using a stencil printing process, which ensures that the correct amount of solder is deposited on each pad.
Component Placement
Once the solder paste has been applied, the surface mount components are placed on the PCB using a Pick-and-place machine. This machine uses vacuum nozzles to pick up the components and place them accurately on the pads.
Reflow Oven Heating
After the components have been placed, the PCB is sent through a reflow oven. The oven heats the PCB and the components, causing the solder paste to melt and form a permanent connection between the components and the pads. The heating process follows a specific temperature profile, which is designed to ensure that the solder melts and flows properly without damaging the components or the PCB.
Cooling and Inspection
Once the PCB has passed through the reflow oven, it is allowed to cool. During this stage, the molten solder solidifies, forming a strong and reliable connection between the components and the PCB. After cooling, the PCB is inspected to ensure that all solder joints are properly formed and that there are no defects or issues.
Reflow Soldering Temperature Profile
The temperature profile is a critical aspect of the reflow soldering process, as it determines the quality and reliability of the solder joints. A typical reflow soldering temperature profile consists of four stages:
- Preheat
- Soak
- Reflow
- Cooling
Stage | Temperature Range (°C) | Duration (seconds) |
---|---|---|
Preheat | 25-150 | 60-120 |
Soak | 150-180 | 60-120 |
Reflow | 220-250 | 30-60 |
Cooling | 250-25 | 60-120 |
Preheat Stage
During the preheat stage, the PCB and components are gradually heated to a temperature of around 150°C. This stage helps to evaporate any moisture on the PCB and components, which can cause defects during the reflow stage.
Soak Stage
In the soak stage, the temperature is maintained between 150°C and 180°C for a period of 60 to 120 seconds. This stage allows the temperature to equalize across the PCB and components, ensuring that all parts of the assembly reach the same temperature before entering the reflow stage.
Reflow Stage
The reflow stage is the most critical part of the process, as it is when the solder melts and forms a connection between the components and the PCB. The temperature is quickly raised to the melting point of the solder, which is typically between 220°C and 250°C. The assembly is kept at this temperature for 30 to 60 seconds to ensure that the solder has sufficient time to melt and flow properly.
Cooling Stage
After the reflow stage, the PCB and components are allowed to cool gradually. This stage is important because it allows the molten solder to solidify and form a strong, reliable connection. Rapid cooling can cause thermal stress and lead to defects in the solder joints.
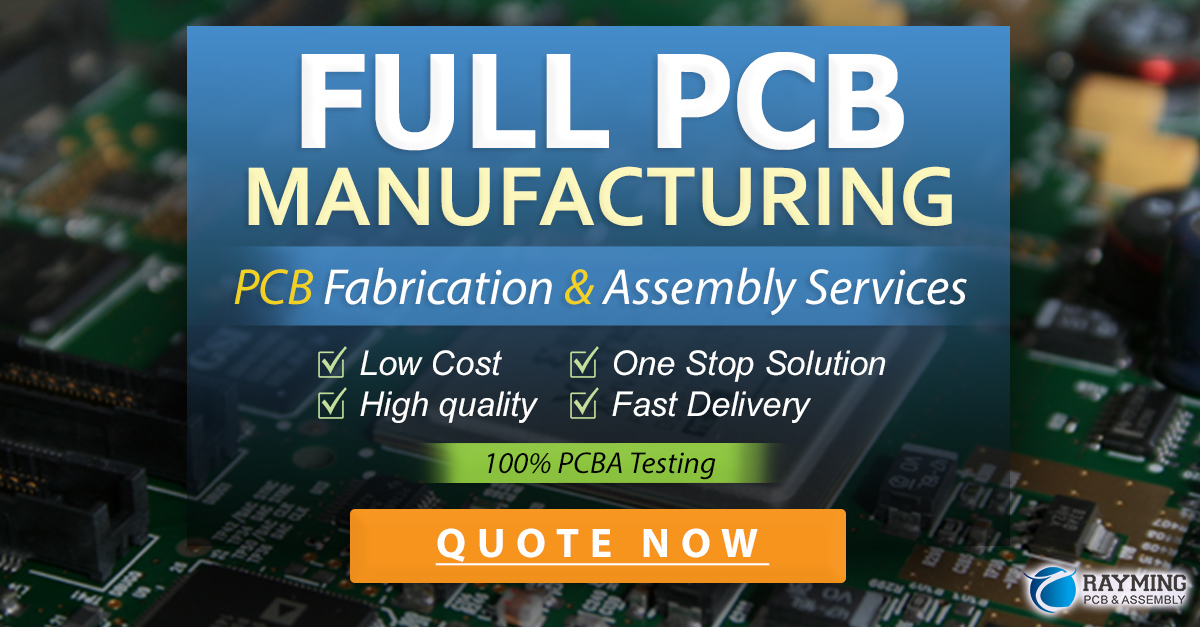
Common Reflow Soldering Defects and How to Prevent Them
Despite the many advantages of reflow soldering, several defects can occur during the process. Here are some of the most common defects and how to prevent them:
Tombstoning
Tombstoning occurs when a component stands up on one end, forming a tombstone-like shape. This defect is usually caused by an uneven heating of the component or an imbalance in the solder paste volume on the pads. To prevent tombstoning, ensure that the solder paste is applied evenly and that the component placement is accurate.
Bridging
Bridging occurs when solder forms a connection between two adjacent pads or components, creating a short circuit. This defect is often caused by excessive solder paste or incorrect component placement. To prevent bridging, use the correct solder paste stencil thickness and ensure that the components are placed accurately.
Insufficient Wetting
Insufficient wetting occurs when the solder does not flow properly, resulting in a weak or incomplete connection. This defect can be caused by contamination on the PCB or components, incorrect reflow temperature profile, or inadequate flux activity. To prevent insufficient wetting, ensure that the PCB and components are clean, use the correct reflow temperature profile, and select a suitable solder paste with adequate flux activity.
Solder Balling
Solder balling occurs when small spheres of solder form on the surface of the PCB or components. This defect is usually caused by excessive solder paste or incorrect reflow temperature profile. To prevent solder balling, use the correct solder paste stencil thickness and follow the recommended reflow temperature profile.
Best Practices for Successful PCB Reflow Soldering
To ensure a successful reflow soldering process and minimize the risk of defects, follow these best practices:
- Use high-quality solder paste with the appropriate particle size and flux activity for your application.
- Ensure that the PCB and components are clean and free from contamination.
- Use the correct solder paste stencil thickness and aperture size for your components.
- Ensure accurate component placement using a pick-and-place machine or manual placement with proper alignment.
- Follow the recommended reflow temperature profile for your solder paste and PCB Design.
- Regularly maintain and calibrate your reflow oven to ensure consistent and accurate temperature control.
- Conduct thorough inspections of the soldered PCBs to identify and address any defects or issues.
Frequently Asked Questions (FAQ)
1. What is the difference between reflow soldering and Wave Soldering?
Reflow soldering is used for surface mount components and involves applying solder paste, placing components, and heating the assembly in a reflow oven. Wave soldering is used for through-hole components and involves passing the PCB over a wave of molten solder.
2. Can I reflow solder without using a stencil?
While it is possible to apply solder paste without a stencil, using a stencil ensures a consistent and accurate solder paste deposition, which is crucial for achieving high-quality solder joints and minimizing defects.
3. How do I select the right solder paste for my application?
When selecting a solder paste, consider factors such as the solder alloy composition, particle size, flux activity, and the requirements of your specific application. Consult with your solder paste supplier or refer to industry guidelines for recommendations.
4. What is the shelf life of solder paste, and how should it be stored?
The shelf life of solder paste varies depending on the specific product but is typically around 6 months when stored under refrigeration (2-10°C). Always refer to the manufacturer’s guidelines for storage and handling instructions.
5. How often should I calibrate my reflow oven?
The frequency of reflow oven calibration depends on factors such as usage, environmental conditions, and the manufacturer’s recommendations. As a general guideline, consider calibrating your reflow oven at least once every 6 months or whenever you notice inconsistencies in the soldering process.
Conclusion
Reflow soldering is a critical process in the manufacturing of printed circuit boards, ensuring reliable and high-quality solder joints for surface mount components. By understanding the reflow soldering process, temperature profile, common defects, and best practices, you can optimize your PCB Assembly process and achieve consistent, successful results. Regular maintenance, calibration, and inspection are essential for maintaining the quality and reliability of your reflow soldering process.
Leave a Reply