What is Reflow Soldering?
Reflow soldering is a process in which solder paste, a mixture of tiny solder particles suspended in flux, is applied to the contact pads of a PCB. Electronic components are then placed on the solder paste, and the entire assembly is subjected to a controlled heating process. The heat melts the solder particles, which then cool and solidify, creating strong electrical and mechanical bonds between the components and the PCB.
Advantages of Reflow Soldering
Reflow soldering offers several advantages over other soldering methods, such as wave soldering or hand soldering:
- High precision: Reflow soldering allows for the precise placement of small components on dense PCBs, making it ideal for modern electronic devices.
- Consistency: The controlled heating process ensures uniform solder joint formation across the entire PCB, resulting in improved reliability and quality.
- Automation: Reflow soldering is easily automated, enabling high-volume production and reducing manual labor costs.
- Flexibility: The process is compatible with a wide range of component sizes and types, as well as various PCB materials and finishes.
The Reflow Soldering Process
The reflow soldering process consists of several stages, each with its own set of parameters and considerations.
1. Solder Paste Application
Solder paste is applied to the PCB using a stencil printing process. A stencil, typically made of stainless steel or polyimide, is aligned with the PCB and acts as a template for depositing solder paste onto the contact pads. The thickness of the stencil and the size of its apertures determine the amount of solder paste applied.
Solder Paste Composition
Solder paste is a homogeneous mixture of the following components:
Component | Typical Proportion |
---|---|
Solder alloy particles | 85-90% by weight |
Flux | 10-15% by weight |
The most common solder alloy used in reflow soldering is tin-silver-copper (SAC), with a typical composition of 96.5% tin, 3% silver, and 0.5% copper (SAC305). This lead-free alloy has a melting point of approximately 217°C.
2. Component Placement
After solder paste application, electronic components are placed on the PCB using pick-and-place machines or, in some cases, by hand. Accurate component placement is crucial for ensuring proper solder joint formation and preventing component shifting during the reflow process.
3. Reflow Soldering Profile
The reflow soldering profile is a critical aspect of the process, as it determines the quality and reliability of the solder joints. A typical reflow profile consists of four main stages:
- Preheat: The PCB Assembly is gradually heated to activate the flux and evaporate the solvents in the solder paste. This stage also helps minimize thermal shock to the components.
- Thermal soak: The temperature is maintained just below the melting point of the solder alloy to ensure even heat distribution across the PCB and allow the components to reach thermal equilibrium.
- Reflow: The temperature is rapidly increased above the melting point of the solder alloy, causing the solder particles to melt and form solder joints. The peak temperature and duration of the reflow stage are critical for achieving optimal results.
- Cooling: The PCB assembly is cooled at a controlled rate to allow the solder joints to solidify and prevent thermal stress on the components.
Here is an example of a typical lead-free reflow soldering profile:
Stage | Temperature Range | Duration |
---|---|---|
Preheat | 25°C to 150°C | 60-90 seconds |
Thermal soak | 150°C to 180°C | 60-120 seconds |
Reflow | 217°C to 260°C | 30-90 seconds |
Cooling | 260°C to 25°C | 60-120 seconds |
The specific parameters of a reflow profile depend on factors such as the PCB design, component types, and solder paste composition. Manufacturers often use thermal profiling tools to optimize the reflow process and ensure consistent results.
Reflow Soldering Equipment
Several types of equipment are used in the reflow soldering process, each with its own advantages and limitations.
Convection Reflow Ovens
Convection reflow ovens are the most common type of reflow soldering equipment. They use forced convection heating, where hot air is circulated throughout the oven chamber to heat the PCB assembly evenly. Convection reflow ovens can be further classified into two categories:
- Infrared (IR) convection ovens: These ovens combine infrared heating elements with convection heating to improve heat transfer and reduce the overall reflow time.
- Vapor Phase Reflow ovens: In these ovens, the PCB assembly is immersed in a vapor of a heat transfer fluid, which condenses on the surface of the PCB and components, providing uniform heating.
Conduction Reflow Systems
Conduction reflow systems use direct contact heating, where the PCB assembly is placed on a heated surface or between heated plates. This method offers more localized heating and is often used for smaller batch sizes or specialized applications.
Laser Reflow Systems
Laser reflow systems use focused laser beams to heat specific areas of the PCB assembly. This method is highly precise and can be used for selective soldering or rework processes.
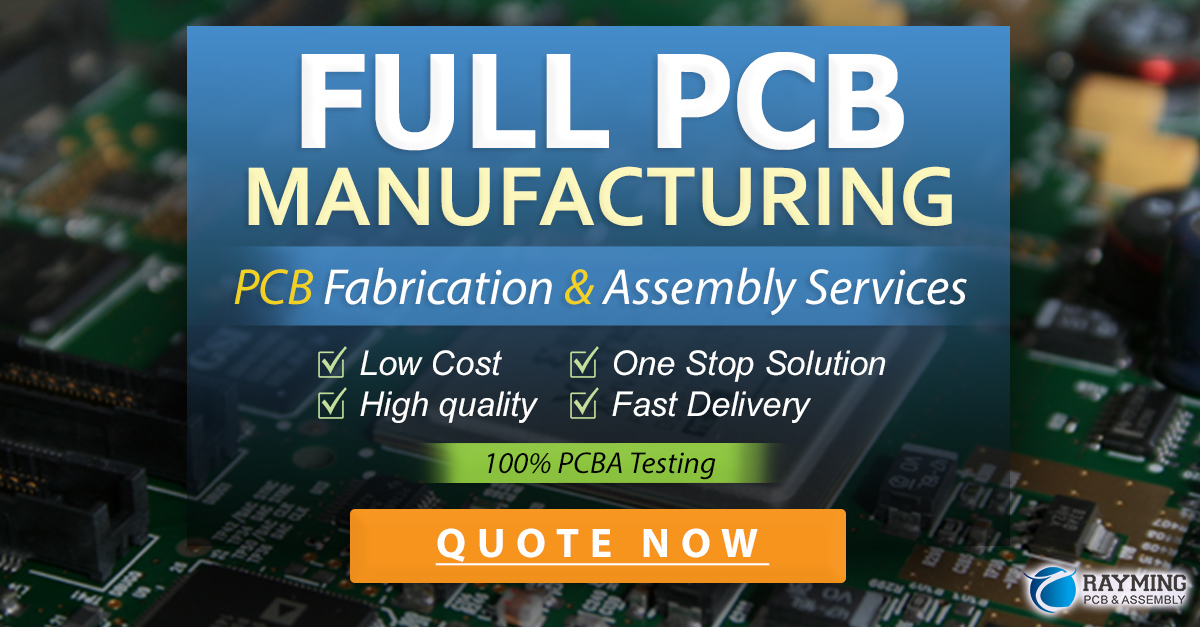
Best Practices for Reflow Soldering
To achieve optimal results in reflow soldering, consider the following best practices:
- PCB design: Ensure that the PCB design is compatible with the reflow soldering process, with appropriate pad sizes, component spacing, and thermal relief features.
- Solder paste selection: Choose a solder paste with the appropriate alloy composition, particle size, and flux activity for your specific application.
- Stencil design: Optimize the stencil design to ensure consistent solder paste deposition, considering factors such as aperture size, shape, and spacing.
- Component placement: Use pick-and-place machines or skilled operators to ensure accurate component placement and orientation.
- Reflow profile optimization: Develop and optimize the reflow profile based on the specific requirements of your PCB assembly, considering factors such as component thermal sensitivity and solder paste specifications.
- Process control: Implement process control measures, such as regular maintenance, calibration, and monitoring of the reflow soldering equipment to ensure consistent results.
- Inspection and testing: Conduct thorough visual inspection and electrical testing of the soldered PCB assemblies to identify and address any defects or quality issues.
Frequently Asked Questions (FAQ)
-
What is the difference between reflow soldering and wave soldering?
Reflow soldering is used for surface mount components and involves applying solder paste to the PCB, placing the components, and heating the entire assembly to melt the solder. Wave soldering, on the other hand, is used for through-hole components and involves passing the PCB over a molten solder wave to form solder joints. -
Can reflow soldering be used for through-hole components?
While reflow soldering is primarily used for surface mount components, it can be used for some through-hole components with appropriate design modifications, such as using pin-in-paste or intrusive reflow techniques. -
What are some common defects in reflow soldering?
Common defects in reflow soldering include bridging (unintended connections between adjacent pads), tombstoning (components standing on end due to uneven solder joint formation), insufficient or excessive solder, and solder balls or splatter. -
How can I troubleshoot issues with my reflow soldering process?
To troubleshoot reflow soldering issues, start by examining the solder joints and identifying the specific defects. Review the reflow profile, solder paste specifications, and PCB design to identify potential causes. Conduct process audits and implement corrective actions, such as adjusting the reflow profile, improving stencil design, or optimizing component placement. -
What safety precautions should be taken when performing reflow soldering?
Reflow soldering involves high temperatures and the use of chemicals, so safety precautions are essential. Always wear appropriate personal protective equipment (PPE), such as heat-resistant gloves and eye protection. Ensure adequate ventilation to minimize exposure to fumes and vapors. Follow proper handling and storage procedures for solder paste and other materials. Regularly inspect and maintain equipment to prevent electrical or fire hazards.
Conclusion
Reflow soldering is a critical process in the manufacturing of electronic devices, enabling the precise and reliable assembly of surface mount components on PCBs. By understanding the principles, equipment, and best practices involved in reflow soldering, manufacturers can optimize their processes to achieve high-quality, consistent results. As electronic devices continue to advance in complexity and miniaturization, the importance of reflow soldering will only continue to grow, making it an essential skill for professionals in the electronics industry.
Leave a Reply