What is Soldermask CTI?
Soldermask Comparative Tracking Index (CTI) is a measure of the electrical insulation properties and resistance to tracking (formation of conductive paths) of the soldermask material used on printed circuit boards (PCBs). It indicates the voltage at which the soldermask will fail and allow current to “track” between conductors, potentially causing a short circuit.
CTI is measured according to the IEC 60112 standard. In this test, electrodes are placed on the soldermask surface and a 50 Hz AC voltage is applied, which is increased in steps until tracking occurs. The CTI value is the maximum voltage withstood before failure, divided by 25.
IEC 60112 CTI Classes
CTI Range | Corresponding IEC 60112 Class | Typical Applications |
---|---|---|
≥ 600 | CTI 600 | Telecom, industrial control, power supplies |
400 – 599 | CTI 400 | Consumer electronics, household appliances |
175 – 399 | CTI 175 | Low-voltage, non-safety-critical applications |
100 – 174 | CTI 100 | Functional testing only, not for end products |
Most standard soldermasks have a CTI in the 175-399 range, suitable for typical consumer electronics operating at voltages under 250 VAC. For applications operating at higher voltages or requiring better insulation performance, high CTI soldermasks with ratings of 400 or 600 are used.
When are High CTI Soldermasks Required?
High CTI soldermasks are essential for PCBs in applications involving:
-
High voltages: Boards operating at voltages over 250 VAC need increased insulation to prevent tracking and short circuits.
-
Harsh environments: High humidity, condensation, dust, and other contaminants can degrade insulation and promote tracking at lower voltages. High CTI masks maintain safety margins in these conditions.
-
Safety-critical systems: Medical devices, automotive controls, aerospace equipment, and other systems where PCB failure would endanger users require the added reliability of high CTI soldermasks.
-
Compact layouts: As PCBs get smaller and more dense, conductor spacings shrink, making them more vulnerable to tracking. High CTI masks enable compact designs while preserving electrical spacing.
-
Regulatory standards: Some industries and applications are governed by safety standards that mandate the use of soldermasks with specific minimum CTI ratings:
Standard | Scope | Minimum CTI |
---|---|---|
IEC 60601-1 | Medical devices | CTI 400 |
IEC 60950-1 | IT equipment | CTI 175 |
IEC 60335-1 | Household appliances | CTI 175 |
IEC 61010-1 | Lab & measurement equip. | CTI 175 |
UL 796 | Printed wiring boards | CTI 175 |
Using soldermasks with CTI ratings above the specified minimums provides an extra margin of safety.
Choosing the Right High CTI Soldermask
When selecting a high CTI soldermask for an application, consider the following factors in addition to the CTI rating:
Voltage Rating
The soldermask’s dielectric withstand voltage should exceed the maximum voltage present on the board, with an ample safety margin (typically 2-3x). This ensures that the soldermask can handle voltage spikes and transients without breakdown.
Thickness
Soldermask thickness affects its insulation and mechanical properties. Thicker coatings generally have higher dielectric strength and CTI, but may impact soldering and fine-pitch component placement. Typical thicknesses range from 0.5 mil (13 μm) to 2.0 mil (50 μm), with high CTI masks usually on the thicker end.
Material
The base resin system and filler materials used in the soldermask influence its electrical and physical properties. Common high CTI mask materials include:
- Epoxy: Tough, heat-resistant, and compatible with lead-free soldering, but can be brittle and prone to cracking.
- Urethane: Flexible and resistant to cracking, but less heat-tolerant and more moisture-sensitive than epoxy.
- Silicone: Highly flexible and thermal shock resistant, but expensive and can interfere with soldering.
Additives such as silica, alumina, and ceramic fillers can boost the CTI of any base resin. The optimal material choice depends on the specific requirements and processing constraints of each application.
Color
Soldermask color is usually dictated by the PCB design and aesthetic requirements, but can also affect electrical properties. Darker masks (green, black) typically have higher CTI than lighter colors (white, red, blue) due to the carbon black pigments used. However, this can vary by manufacturer and should be verified in the mask’s datasheet.
Surface Finish
The soldermask surface finish – matte, semi-gloss, or glossy – does not directly impact CTI but can affect other PCB properties:
- Matte finishes are non-reflective, allowing easier automated inspection but can be harder to clean.
- Glossy finishes are smooth and easier to clean but may cause glare that interferes with inspection.
- Semi-gloss is a compromise between the two.
High CTI masks are available in all finishes, so the choice depends on downstream processing needs.
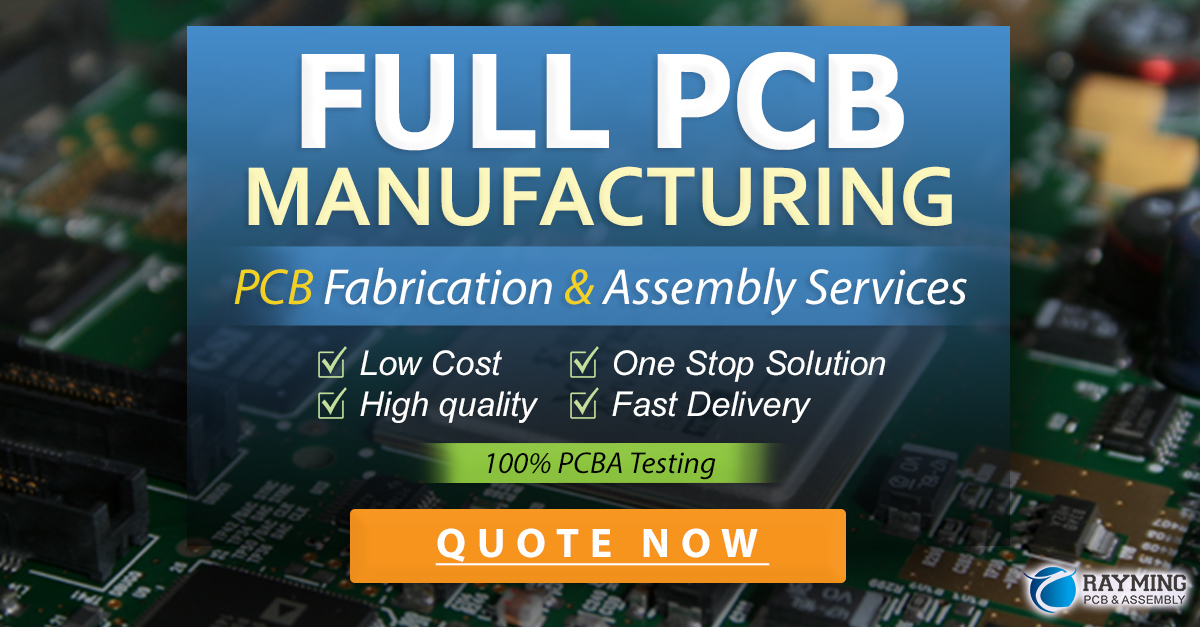
Applying High CTI Soldermasks
The process of applying high CTI soldermasks is similar to that of standard masks, but with some extra considerations:
-
Board preparation: Ensure the Bare PCB is clean and free of contaminants that could degrade adhesion or insulation. Plasma or chemical cleaning may be necessary.
-
Mask selection: Choose a soldermask that meets the CTI, voltage rating, thickness, material, color, and finish requirements for the application.
-
Application method: High CTI masks can be applied by screen printing, spraying, or curtain coating, depending on the PCB design and production volume. Electrostatic spray coating is often used for complex layouts.
-
Curing: Proper curing is critical for achieving the desired electrical and mechanical properties. Follow the manufacturer’s recommended cure schedule (time, temperature, UV intensity) closely. Undercuring can result in poor insulation, while overcuring makes the mask brittle.
-
Inspection: Visually inspect the cured soldermask for defects such as pinholes, bubbles, or thin spots that could compromise CTI. Electrical testing (hi-pot, insulation resistance) can verify insulation integrity.
-
Rework: If defects are found, the soldermask may need to be stripped and reapplied. High CTI masks can be more difficult to remove than standard masks, so prevention is key.
Following best practices and working closely with the soldermask supplier can help ensure a robust, high CTI soldermask process.
FAQ
1. What is the difference between CTI and dielectric withstand voltage?
CTI measures the soldermask’s resistance to tracking (formation of conductive paths) under high voltage stress, while dielectric withstand voltage measures the maximum voltage the mask can withstand before breakdown. Both are important for insulation performance, but CTI specifically addresses the problem of conductive contamination on the PCB surface.
2. Can high CTI soldermasks be used for lead-free soldering?
Yes, most high CTI soldermasks are compatible with lead-free soldering processes, which use higher temperatures than traditional tin-lead soldering. However, it’s important to select a mask material that can withstand the specific thermal profile of the lead-free process being used (e.g. SAC305, SN100C). The mask supplier can provide guidance on lead-free compatibility.
3. Are high CTI soldermasks always necessary for high voltage PCBs?
While high CTI masks provide added insulation and tracking resistance, they may not be necessary if other insulation methods (e.g. conformal coating, potting) are used, or if the high voltage areas are sufficiently spaced apart. However, using a high CTI mask is often the simplest and most cost-effective way to ensure electrical safety in high voltage designs.
4. How does the color of the soldermask affect its CTI?
The pigments used to color soldermasks can impact the CTI, with darker masks (green, black) generally having higher CTI than lighter colors (white, red, blue). This is due to the conductive carbon black pigments used in dark masks. However, the effect of color on CTI can vary by mask material and manufacturer, so it’s best to refer to the specific product datasheet for CTI ratings.
5. Can high CTI soldermasks be used in outdoor or harsh environment applications?
Yes, high CTI masks are often used in outdoor and harsh environment PCBs to maintain insulation performance in the presence of moisture, dust, and other contaminants. However, for the most demanding environments, additional protection such as conformal coating or encapsulation may be necessary on top of the soldermask. The choice of mask material (epoxy, urethane, silicone) should also consider the specific environmental stressors the PCB will face.
Leave a Reply