Introduction to PCB Prototyping
Printed Circuit Board (PCB) prototyping is an essential step in the electronic product development process. It allows engineers and designers to test and validate their designs before committing to large-scale production. Small batch PCB Assembly is ideal for creating prototypes and low-volume production runs, as it offers flexibility, cost-effectiveness, and quick turnaround times.
What is PCB Prototyping?
PCB prototyping is the process of creating a physical representation of a PCB design to test its functionality, performance, and compatibility with other components. This process involves designing the PCB layout, fabricating the board, and assembling the components onto the board. Prototyping helps identify and resolve any issues or errors in the design before mass production, saving time and money in the long run.
Benefits of Small Batch PCB Assembly
Small batch PCB assembly offers several advantages for prototyping and low-volume production:
- Cost-effectiveness: Small Batch assembly is more affordable than large-scale production, as it requires less material and setup costs.
- Flexibility: Small batch assembly allows for design changes and iterations without incurring significant costs or delays.
- Quick turnaround: Small batch assembly providers often offer faster turnaround times compared to large-scale manufacturers, allowing for quicker testing and validation.
- Quality control: Small batch assembly allows for more precise quality control, as each board can be inspected and tested individually.
PCB Design Considerations for Prototyping
Choosing the Right PCB Design Software
Selecting the appropriate PCB design software is crucial for creating accurate and efficient prototypes. Some popular options include:
- Autodesk Eagle
- KiCad
- Altium Designer
- OrCAD
- Cadence Allegro
When choosing a PCB design software, consider factors such as ease of use, feature set, compatibility with other tools, and cost.
PCB Layout Best Practices
To ensure optimal performance and manufacturability of your PCB Prototype, follow these best practices:
- Use appropriate trace widths and spacing to minimize signal interference and crosstalk.
- Proper grounding techniques to reduce noise and improve signal integrity.
- Minimize the use of vias and layer changes to simplify manufacturing and reduce costs.
- Use appropriate component placement and orientation for ease of assembly and thermal management.
- Adhere to the manufacturer’s design rules and guidelines for the specific fabrication process.
Component Selection and Sourcing
When selecting components for your PCB prototype, consider the following factors:
- Availability: Ensure that the chosen components are readily available and not obsolete.
- Cost: Select components that fit within your budget while meeting the required specifications.
- Packaging: Choose appropriate package sizes and types for ease of assembly and compatibility with the PCB layout.
- Reliability: Use components from reputable manufacturers to ensure quality and reliability.
PCB Fabrication Process
PCB Material Selection
The choice of PCB material depends on the specific requirements of your application, such as:
- Dielectric constant
- Thermal conductivity
- Mechanical strength
- Cost
Common PCB materials include:
Material | Dielectric Constant | Thermal Conductivity (W/mK) | Relative Cost |
---|---|---|---|
FR-4 | 4.3-4.7 | 0.3-0.4 | Low |
Rogers | 2.5-10.2 | 0.6-1.5 | High |
Polyimide | 3.4-3.5 | 0.1-0.2 | Medium |
Aluminum | – | 150-200 | Medium |
PCB Fabrication Methods
There are several methods for fabricating PCBs, each with its own advantages and limitations:
- Subtractive method: This involves removing unwanted copper from a pre-laminated board using etching techniques.
- Additive method: This method involves adding copper traces onto a non-conductive substrate using printing or plating techniques.
- Semi-additive method: This is a combination of subtractive and additive methods, where a thin layer of copper is etched away, and additional copper is plated onto the remaining traces.
The choice of fabrication method depends on factors such as design complexity, required features, and cost.
PCB Surface Finishes
The surface finish of a PCB serves to protect the copper traces from oxidation and enhance solderability. Common surface finishes include:
- Hot Air Solder Leveling (HASL)
- Electroless Nickel Immersion Gold (ENIG)
- Immersion Silver (IAg)
- Immersion Tin (ISn)
- Organic Solderability Preservative (OSP)
Each surface finish has its own advantages and disadvantages in terms of cost, durability, and compatibility with different assembly processes.
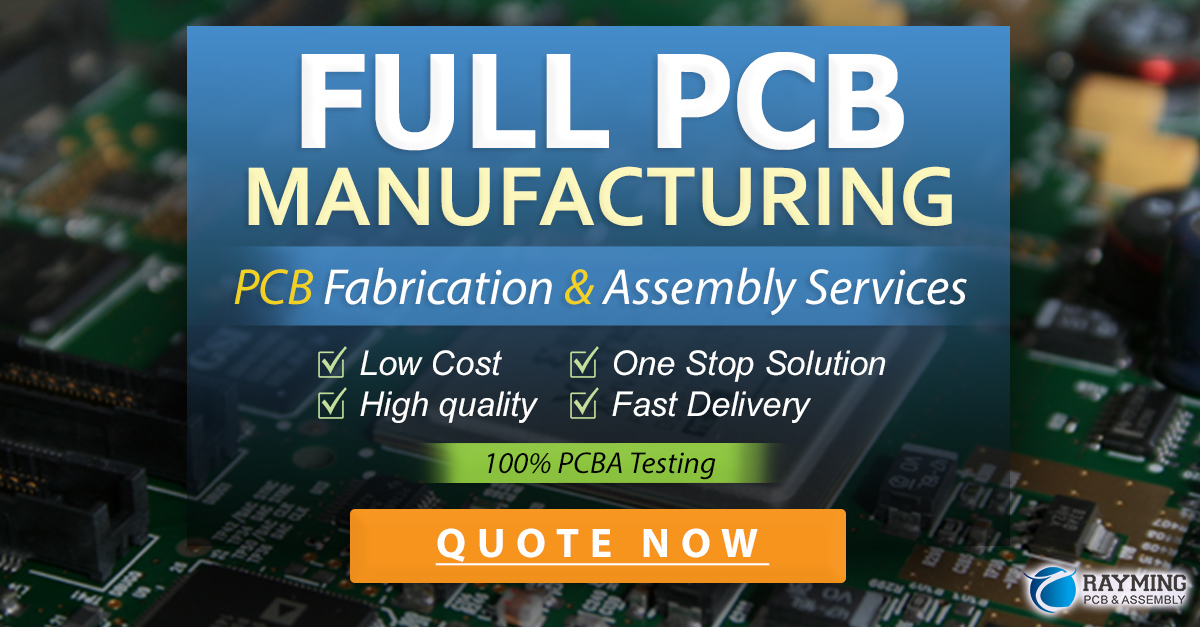
PCB Assembly Techniques
Through-Hole Assembly (THA)
Through-hole assembly involves inserting component leads through drilled holes in the PCB and soldering them to pads on the opposite side. THA is suitable for larger components and provides stronger mechanical connections compared to surface mount assembly. However, it is less space-efficient and requires more manual labor.
Surface Mount Assembly (SMA)
Surface mount assembly involves placing components directly onto pads on the surface of the PCB and soldering them in place. SMA allows for smaller component sizes and higher density layouts compared to THA. It is also more suitable for automated assembly processes, reducing labor costs and increasing production speed.
Mixed Assembly
Mixed assembly combines both through-hole and surface mount components on the same PCB. This approach is often used when certain components are not available in surface mount packages or when stronger mechanical connections are required for specific parts of the circuit.
Automated Assembly Processes
Solder Paste Printing
Solder paste printing is the process of applying solder paste onto the PCB pads using a stencil. The stencil is a thin metal sheet with openings that correspond to the pad locations on the PCB. Solder paste is dispensed onto the stencil and then transferred onto the PCB using a squeegee. Proper solder paste printing is crucial for ensuring reliable solder joints and preventing defects such as bridging or insufficient solder.
Pick and Place Machine
A pick and place machine is an automated system that picks up components from feeders and places them onto the PCB with high precision. Modern pick and place machines can place thousands of components per hour, significantly reducing assembly time and labor costs compared to manual placement. These machines use vision systems to ensure accurate component placement and can handle a wide range of component sizes and types.
Reflow Soldering
Reflow soldering is the process of heating the PCB and components to melt the solder paste and form permanent solder joints. This is typically done using a reflow oven, which heats the PCB in a controlled manner following a specific temperature profile. The temperature profile is designed to activate the flux, remove any oxides, and allow the solder to flow and form reliable connections. Proper reflow soldering is essential for ensuring the quality and reliability of the assembled PCB.
Quality Control and Testing
Visual Inspection
Visual inspection is the first step in quality control and involves examining the assembled PCB for any visible defects or issues. This can be done manually or using automated optical inspection (AOI) systems. Visual inspection checks for problems such as:
- Component placement accuracy
- Solder joint quality
- Bridging or short circuits
- Missing or damaged components
In-Circuit Testing (ICT)
In-circuit testing involves using a bed-of-nails fixture to make electrical contact with specific points on the PCB and test the functionality of individual components and circuits. ICT can detect issues such as:
- Open or short circuits
- Incorrect component values
- Missing or damaged components
- Incorrect polarity
ICT is an effective method for catching manufacturing defects and ensuring the basic functionality of the PCB.
Functional Testing
Functional testing involves testing the PCB in its intended operating environment to ensure that it performs as expected. This can include testing the PCB’s response to various inputs, measuring output signals, and verifying communication with other devices. Functional testing is essential for validating the overall design and ensuring that the PCB meets the required specifications.
Prototyping Services and Providers
Choosing a PCB Prototyping Service
When selecting a PCB prototyping service, consider the following factors:
- Capabilities: Ensure that the service provider can handle your specific requirements, such as PCB size, layer count, and material.
- Turnaround time: Look for providers that offer fast turnaround times to minimize delays in your development process.
- Cost: Compare prices from multiple providers to find the most cost-effective solution for your needs.
- Quality: Choose a provider with a proven track record of delivering high-quality PCBs and reliable customer support.
Popular PCB Prototyping Service Providers
Some popular PCB prototyping service providers include:
- PCBWay
- JLCPCB
- OSH Park
- Seeed Studio
- ExpressPCB
Each provider has its own strengths and weaknesses, so it’s essential to research and compare their offerings to find the best fit for your project.
Frequently Asked Questions (FAQ)
- What is the minimum order quantity for small batch PCB assembly?
-
The minimum order quantity for small batch PCB assembly varies among service providers but can be as low as one piece. However, the cost per unit is typically higher for smaller quantities.
-
How long does it take to receive a PCB prototype?
-
The turnaround time for PCB Prototypes depends on the complexity of the design and the service provider. Some providers offer turnaround times as fast as 24 hours, while others may take several days or weeks.
-
What is the cost of PCB prototyping?
-
The cost of PCB prototyping depends on factors such as the PCB size, layer count, material, and quantity. Prices can range from a few dollars to several hundred dollars per board, depending on the specific requirements.
-
Can I assemble my PCB prototype myself?
-
Yes, it is possible to assemble PCB prototypes manually, especially for simple designs with through-hole components. However, for more complex designs or surface mount components, it is often more efficient and cost-effective to use a professional assembly service.
-
What should I do if my PCB prototype doesn’t work as expected?
- If your PCB prototype doesn’t function as expected, first visually inspect the board for any obvious defects or issues. Then, use a multimeter to check for shorts, opens, or incorrect component values. If the problem persists, consider using more advanced testing methods such as in-circuit testing or functional testing to identify the issue. Once the problem is identified, modify your design and create a new prototype for further testing.
Conclusion
Small batch PCB assembly is a crucial aspect of electronic product development, enabling engineers and designers to create prototypes and low-volume production runs efficiently and cost-effectively. By understanding the various aspects of PCB design, fabrication, assembly, and testing, you can optimize your prototyping process and bring your products to market faster.
When selecting a PCB prototyping service, consider factors such as capabilities, turnaround time, cost, and quality to find the best solution for your needs. By partnering with a reliable service provider and following best practices for PCB design and assembly, you can ensure the success of your electronic product development endeavors.
Leave a Reply