FQA
Q1: What is a rigid flex PCB?
A rigid flex PCB is a printed circuit board that consists of rigid and flexible substrates laminated together. It provides solutions for applications that require dynamics movements and mechanical complexity while maintaining high durability and reliability. The rigid sections provide structural support and the flexible sections allow movement and decrease wiring between components.
Q2: What are the benefits of using rigid flex PCBs?
Some key benefits of rigid flex PCBs include:
- High reliability: The materials used are engineered for repeated flexing and are extremely durable. This makes them well-suited for dynamic applications.
- Space and weight savings: By combining rigid and flex, rigid flex PCBs require less space and weigh less than assemblies using connectors and cables.
- Increased functionality: Rigid flex allows for more compact product design with components placed on multiple rigid sections connected by flex.
- Simplified assembly: Components can be pre-assembled or populated on the rigid sections, reducing assembly time and cost.
- Reduced electrical noise: The short, continuous connections minimize noise and interference.
Q3: What types of products use rigid flex PCBs?
Rigid flex PCBs are used in a variety of industries and products including:
- Consumer electronics – Cell phones, wearables, tablets
- Medical devices – Hearing aids, insulin pumps, pain management devices
- Automotive – Cameras, sensors, control units
- Aerospace and defense – Avionics, radars, guidance systems
- Industrial – Robotics, instrumentation, control systems
Q4: What are some key considerations when selecting a rigid flex PCB supplier?
Some key factors to consider include:
- Capabilities: Evaluate the supplier’s design expertise, manufacturing capabilities, and services offered. Look for extensive experience with rigid flex technology.
- Quality: Choose a supplier with rigorous quality control standards, modern manufacturing facilities, and advanced testing capabilities. They should be ISO 9001 certified at a minimum.
- Reliability: Select a supplier with a proven track record of on-time delivery and responsive customer service. Check client references.
- Technical support: The supplier should provide design support and quickly respond to technical questions. Evaluate their engineering resources.
- Value: Balance costs with the factors above. Consider total value, not just lowest initial quote cost.
Q5: Who are some of the top rigid flex PCB suppliers?
Some of the leading global rigid flex PCB manufacturers include:
- Minco
- MFLEX
- Flexible Circuit Technologies (FCT)
- Flexible Circuit Technologies
- All Flex
- Tech-Etch
- Flex
- Compass Circuits
- Rigid-Flex Int.
- Summit Interconnect
- Samsung Electro-Mechanics
- Ibiden
Top Rigid Flex PCB Suppliers Comparison
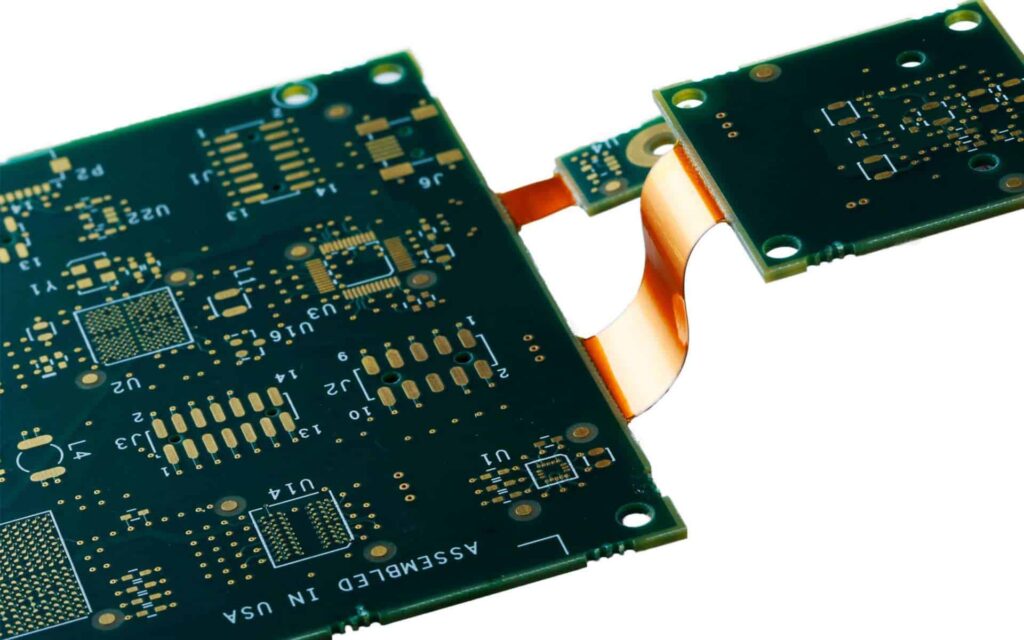
Here is a comparison table highlighting some of the key capabilities of top rigid flex PCB suppliers:
Supplier | Location | Capabilities | Certifications | Manufacturing Facilities |
---|---|---|---|---|
Minco | Minnesota, USA | Prototype to medium volume, 2-42 layers flex and rigid-flex, controlled impedance, HDI | ISO 9001, ISO 13485, AS9100D | Circuits facilities in China and Malaysia |
MFLEX | California, USA | High volume, 2-30 layers, rigid-flex, HDI, high speed digital | ISO 9001, ISO 13485, AS9100, Nadcap | Circuits facilities in China and India |
Flexible Circuit Technologies | Minnesota, USA | Quickturn protoype to medium volume, 2-12 layer rigid flex, controlled impedance | ISO 9001:2015, ISO 13485:2016 | Circuits facilities in Minnesota, USA |
All Flex | California, USA | Quickturn prototype to medium volume, 2-30 layers, rigid-flex, HDI, flex-on-glass | ISO 9001:2015, AS9100D, IPC 6013 | Circuits facilities in Minnesota and California, USA |
Tech-Etch | Massachusetts, USA | Prototype to medium volume, 2-30 layers rigid-flex, 4 mil line/space | ISO 9001:2015, ISO 13485:2016 | Circuits facilities in Massachusetts and New Hampshire, USA |
Flex | California, USA | High volume, 12-28 layer rigid-flex, HDI, advanced thermal management | ISO 9001, IATF 16949, AS9100 | Circuits facilities in Wisconsin, USA and globally |
Compass Circuits | Arizona, USA | Prototype to medium volume rigid-flex, microvias, controlled impedance, buried capacitance | ISO 9001:2015, AS9100D | Circuits facilities in Arizona and California, USA |
Rigid-Flex Int. | Wisconsin, USA | Quickturn prototype to medium volume, 2-30 layer rigid-flex | ISO 9001:2015 | Circuits facilities in Wisconsin, USA |
Summit Interconnect | Minnesota, USA | Prototype to medium volume, 2-30 layer rigid-flex, HDI | ISO 9001:2015, ISO 13485:2016 | Circuits facilities in Minnesota and Wisconsin, USA |
Samsung Electro-Mechanics | South Korea | High volume rigid-flex, HDI, highend packaging, flexible glass | ISO 9001, IATF 16949, AS9100 | Facilities worldwide, high volume Asia focus |
Ibiden | Japan | High volume, high layer count rigid-flex, fine line capabilities | ISO 9001, IATF 16949, ISO 14001 | Facilities in Japan, Malaysia, Philippines |
Rigid Flex PCB Design Considerations
When designing a rigid flex PCB, engineers must consider factors such as:
Layer stackup: Determine the layer count, stackup, and materials needed for traces, planes, and covers based on circuit density, impedance, and other requirements. Rigid layers are typically thicker FR-4, while flex layers use polyimide films.
Rigid-to-flex transitions: Manage differences in materials through controlled impedance interfaces and geometric transitions. Avoid sharp corners or angles.
Component placement: Position components to minimize traces crossing the rigid-flex boundary. Place high performance or dense circuitry on the rigid sections.
Flex fold areas: Account for neutral bend axis and leave sufficient keep-out around the fold. Add stiffeners or covers if needed.
Thermal management: Ensure proper heat dissipation through thermal reliefs, thermal cores, or other methods. Consider heat profiles during flexing.
Routing: Use conservative trace widths/spacing and corner radii. Allow for flexing cycles and dynamic motion.
Testability: Include test points, ports, and fixtures as needed to validate all sections. Account for limited access with enclosures.
Manufacturability: Work with manufacturer early in the design process to ensure design for manufacturing guidelines are met.
Proper design is critical for rigid flex PCB reliability. Experienced suppliers have rigid flex design expertise to support complex projects through the full product lifecycle.
Reasons to Use a Rigid Flex PCB Supplier
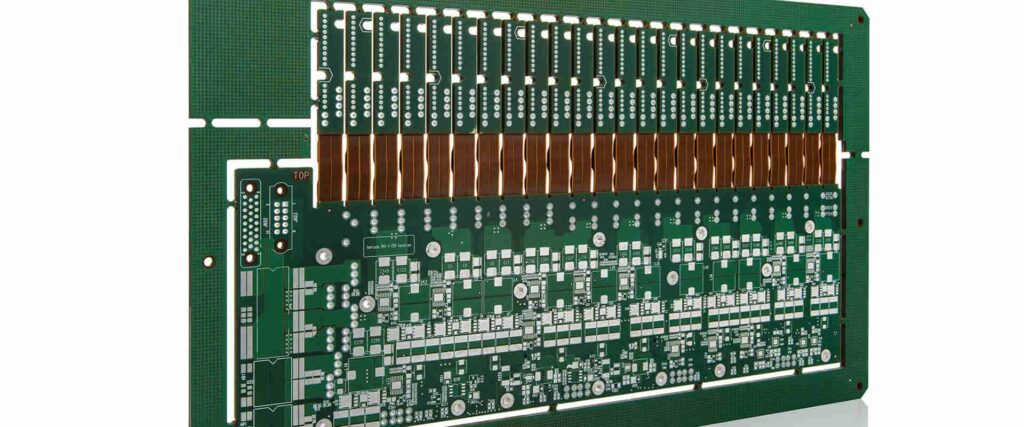
There are several key advantages to partnering with an established rigid flex PCB supplier:
Specialized expertise: Rigid flex suppliers specialize in the intricacies of this technology. They have extensive knowledge of materials, modeling, fabrication, and qualification testing that an end customer is unlikely to possess in house.
Design support: Suppliers provide valuable design reviews and recommendations early in the development process to avoid manufacturability issues. Their guidance can optimize the design for cost, quality, and reliability based on years of experience.
Process control: By controlling the complex process internally, suppliers can consistently produce quality boards and scale efficiently to higher volumes. Customers benefit through improved yields and dependable delivery.
Quality and reliability: Leading suppliers invest in advanced manufacturing and inspection equipment to build quality into the process. Their focus on continuous improvement provides customers with consistent, defect-free PCBs.
Economies of scale: Suppliers aggregate demand across customers to achieve favorable pricing on base materials. They can leverage investments across product volumes and offer competitive costs.
Fast time to market: Suppliers maintain inventory of base materials and can rapidly mobilize to meet quickturn prototyping or ramp up to full rate production. This accelerated time to market is critical for product launch success.
For products where performance, complexity, and reliability are vital, partnering with an expert rigid flex supplier reduces risk and speeds time to revenue.
Conclusion
Rigid flex PCBs provide the ideal solution for products requiring dynamic movements and tight interconnections. As products continue to shrink with higher densities, rigid flex allows designers to fit more functionality into smaller spaces without compromising reliability.
Selecting the right rigid flex PCB partner ensures you have the materials knowledge, engineering support, quality systems, and volume scalability needed to be successful. The above global and domestic suppliers offer proven expertise in prototyping to high volume production. Choosing a supplier with the right capabilities, experience, and resources for your specific project will lead to a smoother PCB design and development cycle.
Leave a Reply