Rigid flex printed circuit boards (PCBs) combine rigid and flexible circuitry into a single component, providing design flexibility and reliability for complex electronic devices. As demand for ever-smaller and more capable electronics grows, rigid flex PCBs have become essential for products from smartphones to medical devices. This guide explores leading rigid flex PCB manufacturers, considerations for choosing a manufacturer, rigid flex PCB design principles, and answers common questions about procuring high-quality rigid flex PCBs.
Key Capabilities of Leading Rigid Flex PCB Manufacturers
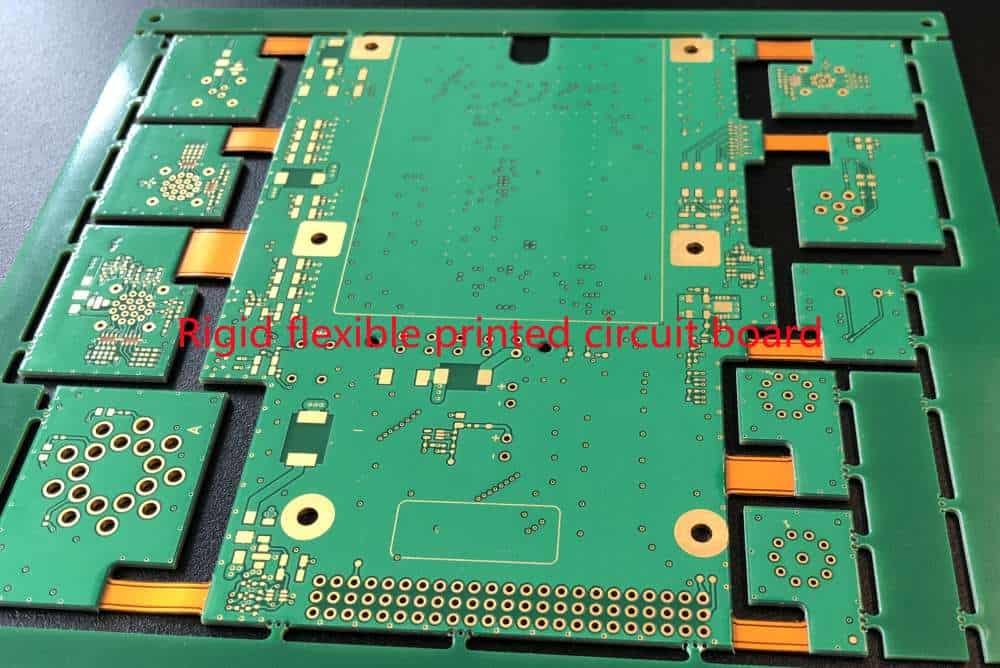
Choosing the right rigid flex PCB partner requires evaluating manufacturers’ capabilities across several key areas:
Experience and Expertise
Look for long experience manufacturing rigid flex PCBs. Leading manufacturers have high expertise across rigid flex materials, layer stacks, and fabrication processes. They stay ahead of emerging trends and can advise on optimal rigid flex design approaches.
Rigid Flex Materials and Constructions
The best manufacturers offer a wide range of flexible and rigid materials to meet application requirements, including:
- Flexible polyimide and polyester films
- Rigid FR-4 and high Tg substrates
- Adhesives for bonding layers
They also enable complex layer stacks with multiple rigid and flex zones in a single PCB.
Design and Simulation Services
Rigid flex PCB layout requires specialized design skills. Top manufacturers provide design support and simulation of flex stresses, thermal behavior, and other parameters to optimize designs.
Advanced Manufacturing Processes
Leading manufacturers use advanced fabrication processes ideal for rigid flex PCBs, such as:
- Fine line tracing and spacing
- Multiple layer HDI
- Tight tolerance alignment of rigid and flex areas
- Via protection at transitions
- Solder mask over bare copper (SMOBC)
Quality and Reliability
With expertise in rigid flex process control, inspection, and testing, reliable manufacturers deliver consistently high yields and defect-free products, even for challenging, high-mix designs.
Prototyping and Low Volume
Look for quick-turn prototyping services to test initial designs. Support for low volume production is also essential during product development and for niche applications.
Notable Rigid Flex PCB Manufacturers
Many PCB manufacturers offer some rigid flex services, but those focused on high-mix, advanced rigid flex have the best expertise. Here are some leading global rigid flex suppliers:
Flexible Circuit Technologies
Headquartered in the US, Flexible Circuit Technologies specializes in complex, high-performance rigid flex. Capabilities include:
- Stack-ups with 15+ flex layers
- Traces and spaces to 2 mils
- Tight 3 mil line width control
- Via in pad on 2 mil pitch
- 0201 chip components
They also provide extensive design, simulation, and prototyping services catered to rigid flex PCBs.
SigmaTron
SigmaTron has decades of experience with single, double, and multilayer rigid flex PCBs. They fabricate ultra-fine lines down to 0.5 mm and multilayer flex up to 6 layers. Services include electrical testing and conformal coating.
Compass Circuits
Compass Circuits focuses on quick-turn rigid flex PCB prototypes and low-to-medium volume production. They manufacture flex and rigid flex PCBs with line widths/spaces down to 1 mil, using advanced materials like polyimide flex layers.
Lenthor Engineering
Lenthor Engineering provides turnkey PCB solutions with a specialty in rigid flex designs. They manufacture complex rigid flex with up to 30 layers, Sophisticated rigid flex applications with high layer counts and fine features.blind and buried vias, and controlled impedance on flex layers.
ParaChem
ParaChem offers design, prototyping, and manufacturing services for rigid, flex, and rigid flex PCBs. They have particular expertise in high-frequency and controlled impedance rigid flex boards, including multilayer flex up to 6 layers.
Key Considerations for Choosing a Rigid Flex PCB Partner
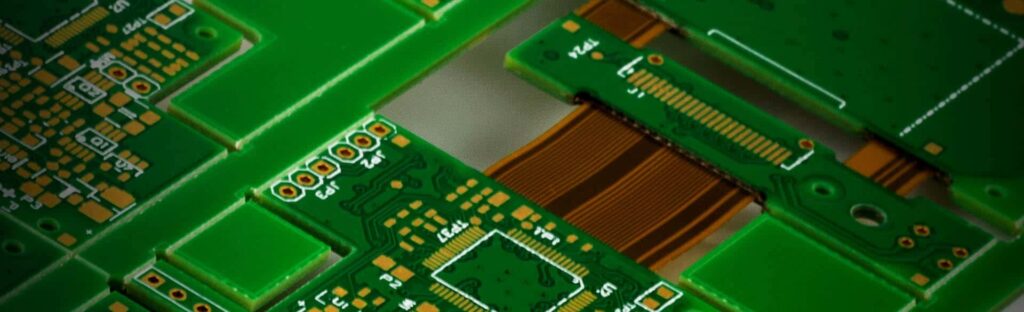
With many options on the market, here are key factors to consider when selecting a rigid flex PCB manufacturer:
Rigid Flex Design Experience
Look for manufacturers with extensive expertise in both the rigid and flex aspects of PCBs. They should demonstrate experience with designs similar to yours.
Quality Systems
Leading manufacturers have quality systems in place like ISO 9001 or AS 9100 certifications. They provide test reports and comply with defense and aerospace standards.
Production Capabilities
Assess production capabilities like layer count, line width/spacing, and via construction to ensure the manufacturer can achieve your technical requirements.
Materials and Constructions
Ask about available rigid and flexible materials, adhesives, and other innovations to choose the optimal construction.
Lead Times and Turnaround
Ask about typical lead times and options to expedite deliveries. Quick-turn prototyping services are ideal during the design process.
Customer Service
The manufacturer should assign dedicated account managers and engineering support. Clear communication is essential throughout the design and ordering processes.
Location and Logistics
For some applications, working with domestic manufacturers or those with warehouses in target markets simplifies logistics.
Design Principles for Optimized Rigid Flex PCBs
Proper design is critical to maximizing performance and reliability of rigid flex PCBs. Here are key design considerations:
Layer Stack Design
- Use thicker dielectrics for outer layers to prevent flex cracking
- Place control layers on outer rigid sections for stability
- Put signal layers in center of stack for protection
- Strategically place ground planes to isolate signals
Trace Routing
- Avoid sharp angles on traces in flex areas
- Include teardrops at solder pads on flex layers
- Cross hatched copper fills strengthen flex regions
- Ensure sufficient trace widths for current loads
Component Placement
- Avoid placing heavy components on flexible sections
- Anchor larger components to rigid areas
- Watch component clearance at flex bends
Rigid-Flex Transitions
- Include stress relief features like rounded corners
- Stagger layer transitions across rigid-flex boundary
- Avoid sudden layer drops
- Protect vias with solder mask at transitions
Flex and Fold Design
- Design bend radius to prevent metal fatigue
- Watch for clearance at fold lines
- Heat steel rule dies match intended bends
Following fundamental rigid flex design principles results in PCBs that meet reliability requirements over the product lifetime.
Table: Comparison of Rigid Flex and Multilayer PCB Characteristics
Property | Rigid Flex PCB | Multilayer PCB |
---|---|---|
Flexibility | Flexible and rigid sections | Rigid board |
Layer Count | Typically 2-6 layers | Can reach >20 layers |
Dielectric Materials | Polyimide, polyester films | FR-4, high Tg |
Traces/Spacing | To 5/5 mil | To 5/5 mil |
Folding | Can be folded and bent | Cannot be folded |
Thermal Issues | Generally less | More due to higher layer count |
EMI Control | Moderate | Excellent due to more ground planes |
Common Uses | Dynamic flexing applications | High density interconnect |
Frequently Asked Questions about Rigid Flex PCBs
What are the main benefits of using a rigid flex PCB?
Rigid flex PCBs provide:
- Flexibility to fit and dynamically flex in products
- Reliability with stress relief at bends
- Design flexibility to integrate rigid and flex circuits
- Reduced system interconnect vs. separate PCBs
- Miniaturization especially relative to wire harnesses
When should rigid flex PCBs be used vs. rigid PCBs?
Consider rigid flex when:
- Flexibility and dynamic bending are required
- 3D form factors are needed for compact devices
- Production volumes are lower
- Reducing layers and connectors vs. separate PCBs is beneficial
Rigid PCBs have advantages for:
- Very high layer counts and interconnect density
- Excellent thermal performance
- Higher production volumes and repeatability
How are rigid and flexible layers bonded in a rigid flex PCB?
Adhesive films typically bond the layers. Common adhesives include acrylic, modified acrylic, nitrile, and polyimide. Adhesive type is selected based on application requirements.
What are key considerations when routing traces in rigid flex PCBs?
Follow teardrop rules at pads, avoid 90 degree bends, watch trace widths for current capacity, and ensure adequate isolation between traces. Strategically place ground planes to shield signals.
How many bend cycles can a rigid flex PCB support?
The flex section can typically withstand 500-3000 bend cycles before traces may eventually crack. Careful design of bend radius and materials selection is key. Dynamic bend applications require testing.
In summary, rigid flex PCB technology enables electronics manufacturers to produce curved, compact, and reliable products. By partnering with a manufacturer experienced in advanced rigid flex materials, designs, and processes, companies can optimize rigid flex PCB performance while reducing risk. Considering the design principles and manufacturer capabilities covered in this guide will help identify the right rigid flex partner for your next product.
Leave a Reply