What is Press Fit?
Press fit, also known as interference fit or friction fit, is a fastening method that relies on friction and pressure to join two parts together without the use of additional fasteners like screws, bolts, or adhesives. In a press fit, the inner diameter of one part (the hole) is slightly smaller than the outer diameter of the mating part (the shaft or pin). When the two parts are forcefully pressed together, the interference between their surfaces creates a strong, tight fit that resists separation.
Press fitting is commonly used in various industries, including automotive, aerospace, electronics, and machinery manufacturing. It provides a cost-effective, efficient, and reliable method for assembling components, especially in high-volume production.
Advantages of Press Fit
Press fitting offers several advantages over other fastening methods:
-
Simplicity: Press fitting is a simple and straightforward assembly process that does not require additional fasteners or complex tooling.
-
Cost-effectiveness: By eliminating the need for separate fasteners, press fitting reduces material costs and assembly time, making it an economical choice for mass production.
-
Strength: The interference between the mating surfaces creates a strong, tight fit that can withstand high loads and vibrations.
-
Alignment: Press fitting ensures precise alignment between the assembled components, as the parts are forced into position during the assembly process.
-
Space efficiency: Press fit assemblies are compact and do not require additional space for fasteners, making them suitable for applications with limited space.
-
Electrical conductivity: In some cases, press fitting can provide electrical conductivity between the assembled parts, eliminating the need for separate electrical connections.
Types of Press Fits
There are three main types of press fits, each with its own characteristics and applications:
1. Clearance Fit
In a clearance fit, there is a small gap between the mating parts, allowing them to be easily assembled and disassembled. This type of fit is used when precise alignment or a tight fit is not required, such as in sliding or rotating components.
2. Transition Fit
A transition fit is a borderline case between clearance and interference fit. The dimensions of the mating parts are such that they may have either a slight clearance or a slight interference, depending on the actual sizes within the specified tolerances. Transition fits are used when a specific fit is not critical, but a certain degree of friction or resistance is desired.
3. Interference Fit
An interference fit, or press fit, is characterized by the inner diameter of the hole being smaller than the outer diameter of the shaft. The difference in diameters is called the interference, which can be further categorized based on the amount of interference:
-
Light press fit: A light press fit has a small amount of interference, typically ranging from 0.0001 to 0.0005 inches per inch of diameter. This type of fit is used for easy assembly and disassembly, and when a tight fit is not critical.
-
Medium press fit: A medium press fit has a moderate amount of interference, usually between 0.0005 and 0.0015 inches per inch of diameter. This fit provides a stronger hold than a light press fit and is used when a tighter fit and greater resistance to separation are required.
-
Heavy press fit: A heavy press fit has a large amount of interference, typically greater than 0.0015 inches per inch of diameter. This type of fit is used when a very strong, permanent assembly is needed, and disassembly is not expected.
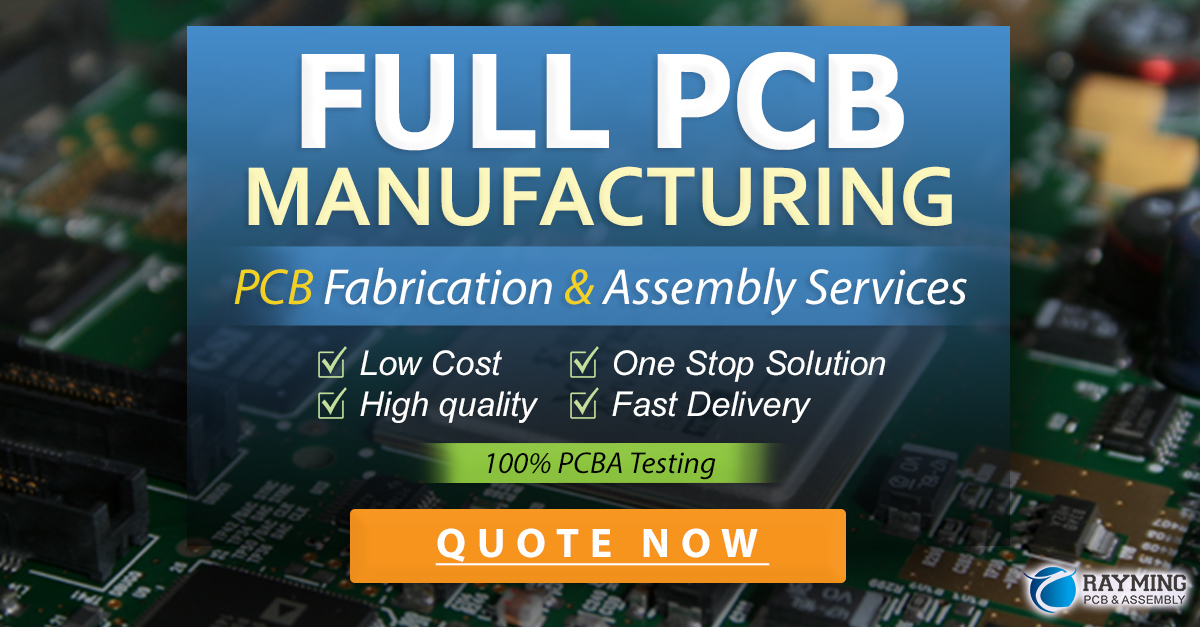
Factors Affecting Press Fit Performance
Several factors influence the strength and reliability of a press fit assembly:
1. Material Properties
The properties of the materials being joined, such as their hardness, elasticity, and thermal expansion coefficients, play a crucial role in the success of a press fit. Harder materials require higher assembly forces and provide a stronger hold, while softer materials may deform or yield under the assembly pressure.
2. Surface Finish
The surface finish of the mating parts affects the friction and the overall fit. Smoother surfaces generally require higher assembly forces but provide a more consistent fit, while rougher surfaces may have lower assembly forces but can result in a less predictable fit.
3. Geometry
The geometry of the mating parts, including their diameters, lengths, and chamfers or lead-ins, influences the assembly process and the resulting fit. Proper design of the lead-ins and chamfers can help align the parts and reduce assembly forces.
4. Tolerances
The dimensional tolerances of the mating parts directly affect the amount of interference and the resulting fit. Tighter tolerances ensure a more consistent and predictable fit, while looser tolerances may result in variations in the assembly force and the strength of the fit.
5. Assembly Process
The assembly process, including the press force, speed, and alignment, can impact the quality of the press fit. Insufficient or excessive press force may result in a weak fit or damage to the parts, while misalignment can cause uneven stress distribution and reduced strength.
Press Fit Design Considerations
When designing a press fit assembly, several factors must be considered to ensure a successful and reliable fit:
1. Interference Amount
The amount of interference between the mating parts should be carefully selected based on the desired strength, the materials involved, and the assembly process. Too little interference may result in a weak fit, while too much interference can cause excessive stress and damage to the parts.
2. Stress Analysis
A thorough stress analysis should be conducted to ensure that the press fit assembly can withstand the expected loads and operating conditions. This analysis should consider the material properties, geometry, and interference amount to predict the stress distribution and potential failure modes.
3. Material Selection
The materials for the mating parts should be selected based on their compatibility, strength, and thermal properties. In general, the shaft material should be harder than the hole material to prevent excessive deformation and ensure a strong fit.
4. Surface Treatment
Surface treatments, such as coatings or heat treatment, can be applied to the mating parts to improve their friction characteristics, corrosion resistance, or wear resistance. However, the effect of these treatments on the interference fit must be carefully considered.
5. Assembly Process Design
The assembly process should be designed to ensure consistent and reliable press fitting. This includes selecting the appropriate press equipment, determining the press force and speed, and designing fixtures or guides to maintain alignment during assembly.
Press Fit Assembly Methods
There are several methods for assembling press fit components, each with its own advantages and limitations:
1. Mechanical Press
A mechanical press uses a hydraulic or pneumatic cylinder to apply a controlled force to press the parts together. This method is suitable for high-volume production and can accommodate a wide range of part sizes and materials.
2. Arbor Press
An arbor press is a manual press that uses a lever and a screw mechanism to apply pressure to the parts. This method is suitable for low-volume production or prototyping, and it allows for more control and flexibility in the assembly process.
3. Thermal Assembly
Thermal assembly involves heating or cooling one of the mating parts to temporarily change its dimensions and allow for easier assembly. For example, the shaft can be cooled to shrink its diameter, while the hole can be heated to expand its diameter. After assembly, the parts return to their original dimensions, creating a tight fit.
4. Shrink Fitting
Shrink fitting is a specific type of thermal assembly where the outer part (usually the hole) is heated to expand its diameter, allowing the inner part (the shaft) to be inserted. As the outer part cools, it shrinks and creates a tight fit around the shaft.
5. Freeze Fitting
Freeze fitting is another type of thermal assembly where the inner part (the shaft) is cooled, typically using liquid nitrogen, to temporarily shrink its diameter. The shaft is then inserted into the hole, and as it warms up to room temperature, it expands and creates a press fit.
Press Fit Disassembly
Disassembling a press fit can be challenging, as the interference between the parts resists separation. However, there are several methods for disassembling press fit components:
1. Mechanical Disassembly
Mechanical disassembly involves applying a controlled force to separate the parts, using a press or a specialized tool. This method may require high forces and can potentially damage the parts, so it should be used with caution.
2. Thermal Disassembly
Thermal disassembly involves heating or cooling one of the parts to temporarily change its dimensions and allow for easier separation. For example, heating the outer part (the hole) can cause it to expand and release the inner part (the shaft).
3. Chemical Disassembly
Chemical disassembly involves using a solvent or a lubricant to break down the friction between the parts and facilitate separation. This method is less common and may not be suitable for all materials or applications.
Press Fit Troubleshooting
When issues arise with press fit assemblies, it is important to identify the root cause and take corrective action. Some common problems and their potential solutions include:
1. Excessive Assembly Force
If the assembly force is too high, it may indicate that the interference is too large or that there are issues with the surface finish or lubrication. Possible solutions include:
- Verifying the part dimensions and tolerances
- Checking the surface finish and applying appropriate lubrication
- Redesigning the assembly with a smaller interference or different materials
2. Insufficient Hold Strength
If the press fit assembly fails to hold under the expected loads, it may suggest that the interference is too small or that there are problems with the material properties or geometry. Possible solutions include:
- Increasing the interference amount
- Selecting materials with higher strength or hardness
- Modifying the geometry to improve stress distribution
3. Misalignment or Uneven Fit
Misalignment or an uneven fit can result in reduced strength and potential failure of the assembly. Possible causes and solutions include:
- Improving the alignment of the press equipment and fixtures
- Verifying the part geometry and lead-in design
- Ensuring consistent surface finish and cleanliness of the mating parts
Press Fit Standards and Guidelines
Several standards and guidelines provide recommendations for the design and implementation of press fit assemblies:
- ISO 286: Geometrical product specifications (GPS) – ISO code system for tolerances on linear sizes
- ANSI B4.1: Preferred Limits and Fits for Cylindrical Parts
- ASME B4.2: Preferred Metric Limits and Fits
- DIN 7190: Interference fits – Calculation and design rules
These standards offer guidance on tolerance classes, interference amounts, and design principles for various press fit applications.
Press Fit Applications
Press fitting is used in a wide range of industries and applications, including:
1. Automotive
- Assembling gears, bearings, and shafts in transmissions and engines
- Joining brake components, such as rotors and hubs
- Securing electrical connectors and terminals
2. Aerospace
- Assembling turbine blades and discs in jet engines
- Joining structural components in aircraft frames and wings
- Securing hydraulic and pneumatic fittings
3. Electronics
- Mounting electronic components on circuit boards
- Assembling connectors and sockets
- Securing heat sinks to electronic devices
4. Manufacturing and Machinery
- Assembling pulleys, sprockets, and gears on shafts
- Joining machine tool spindles and tool holders
- Securing bearings and bushings in housings
Frequently Asked Questions (FAQ)
1. What is the difference between a press fit and a shrink fit?
A press fit and a shrink fit are both types of interference fits, but they differ in the assembly method. In a press fit, the parts are forced together using mechanical pressure, while in a shrink fit, the outer part is heated to expand its diameter, allowing the inner part to be inserted before cooling and creating a tight fit.
2. How do I select the appropriate interference amount for my press fit assembly?
The selection of the interference amount depends on several factors, including the materials, geometry, and desired strength of the assembly. As a general rule, the interference should be between 0.0005 and 0.0030 inches per inch of diameter, depending on the specific application. Consulting design guidelines, standards, and performing stress analysis can help determine the optimal interference amount.
3. Can press fitting be used with dissimilar materials?
Yes, press fitting can be used with dissimilar materials, provided that the differences in their thermal expansion coefficients and mechanical properties are taken into account. In general, the shaft material should be harder than the hole material to prevent excessive deformation and ensure a strong fit. Special care should be taken when designing press fits with materials that have significantly different thermal expansion rates.
4. How do I prevent damage to the parts during press fit assembly?
To prevent damage during press fit assembly, consider the following:
- Ensure that the part dimensions and tolerances are within the specified range
- Use appropriate lubrication to reduce friction and assembly forces
- Design lead-ins and chamfers to help align the parts and reduce stress concentrations
- Control the press force and speed to avoid excessive stress or deformation
- Maintain proper alignment of the parts and the press equipment
5. What are the limitations of press fitting?
Press fitting has some limitations, including:
- Difficulty in disassembly, as the interference resists separation
- Potential for stress concentrations and fatigue failures if not designed properly
- Limited ability to accommodate misalignment or angular adjustments
- Sensitivity to variations in part dimensions and surface finish
- Potential for fretting or corrosion in certain environments
Despite these limitations, press fitting remains a widely used and reliable fastening method for many applications.
Conclusion
Press fitting is a versatile and cost-effective fastening method that relies on interference and friction to join two parts together. By carefully selecting the materials, geometry, and interference amount, designers can create strong and reliable press fit assemblies for a wide range of applications.
Understanding the factors that affect press fit performance, such as material properties, surface finish, and assembly process, is crucial for successful implementation. Proper design, stress analysis, and adherence to relevant standards and guidelines can help ensure the optimal performance and longevity of press fit assemblies.
While press fitting has its limitations and challenges, it remains an essential technique in various industries, offering simplicity, strength, and efficiency in joining components. As technology advances and new materials emerge, the principles of press fitting will continue to evolve and adapt to meet the ever-changing needs of modern manufacturing and engineering.
Leave a Reply