Introduction to PCBs and Their Versatility
Printed Circuit Boards (PCBs) have revolutionized the electronics industry since their inception in the 1940s. These thin, flat boards made of insulating materials with conductive copper traces have become the backbone of modern electronic devices. PCBs provide a stable and efficient platform for mounting and interconnecting electronic components, enabling the creation of complex circuits in a compact and organized manner.
One of the key reasons behind the widespread adoption of PCBs is their versatility. They can be designed and manufactured to suit a wide range of applications, from simple single-layer boards for basic projects to multi-layer, high-density interconnect (HDI) boards for advanced electronics. This versatility has made PCBs indispensable across various industries, including consumer electronics, telecommunications, automotive, aerospace, medical devices, and more.
In this article, we will explore 10 application areas where PCBs play a crucial role, highlighting their importance and the specific requirements they fulfill in each domain.
1. Consumer Electronics
1.1 Smartphones and Tablets
PCBs are the heart of modern smartphones and tablets. These devices require highly miniaturized and densely packed PCBs to accommodate the numerous components and features within their slim form factors. The PCBs in smartphones and tablets often feature multiple layers, HDI technology, and advanced materials to ensure high performance, reliability, and energy efficiency.
1.2 Laptops and Computers
Laptops and desktop computers rely on PCBs for their motherboards, graphics cards, memory modules, and other critical components. These PCBs must handle high-speed data transfer, heat dissipation, and complex power distribution while maintaining signal integrity. The use of multi-layer PCBs with fine-pitch components and advanced routing techniques enables the creation of powerful and compact computing devices.
1.3 Smart Home Devices
The growing popularity of smart home devices, such as smart speakers, thermostats, and security systems, has further expanded the application of PCBs in consumer electronics. These devices often require wireless connectivity, sensors, and power management features, all of which are facilitated by carefully designed PCBs. The use of flexible and rigid-flex PCBs has also enabled the creation of more ergonomic and space-efficient smart home devices.
2. Telecommunications
2.1 5G Infrastructure
The deployment of 5G networks has driven significant advancements in PCB technology. 5G infrastructure, including base stations and small cells, requires high-frequency, low-loss PCBs capable of handling millimeter-wave signals. These PCBs often incorporate advanced materials, such as low-loss dielectrics and high-performance laminates, to minimize signal attenuation and ensure reliable communication.
2.2 Networking Equipment
PCBs play a vital role in networking equipment, such as routers, switches, and modems. These devices demand high-speed data transfer, reliable power distribution, and effective heat management. Multi-layer PCBs with impedance control and differential pair routing are commonly used to maintain signal integrity and minimize crosstalk in high-speed networking applications.
2.3 Satellite Communication Systems
Satellite communication systems rely on PCBs that can withstand the harsh conditions of space, including extreme temperatures, radiation, and mechanical stresses. These PCBs must be designed with high reliability, using materials and components that can endure the challenging environment. Additionally, the PCBs used in satellite communication systems often require specialized shielding and grounding techniques to minimize electromagnetic interference (EMI) and ensure proper functioning.
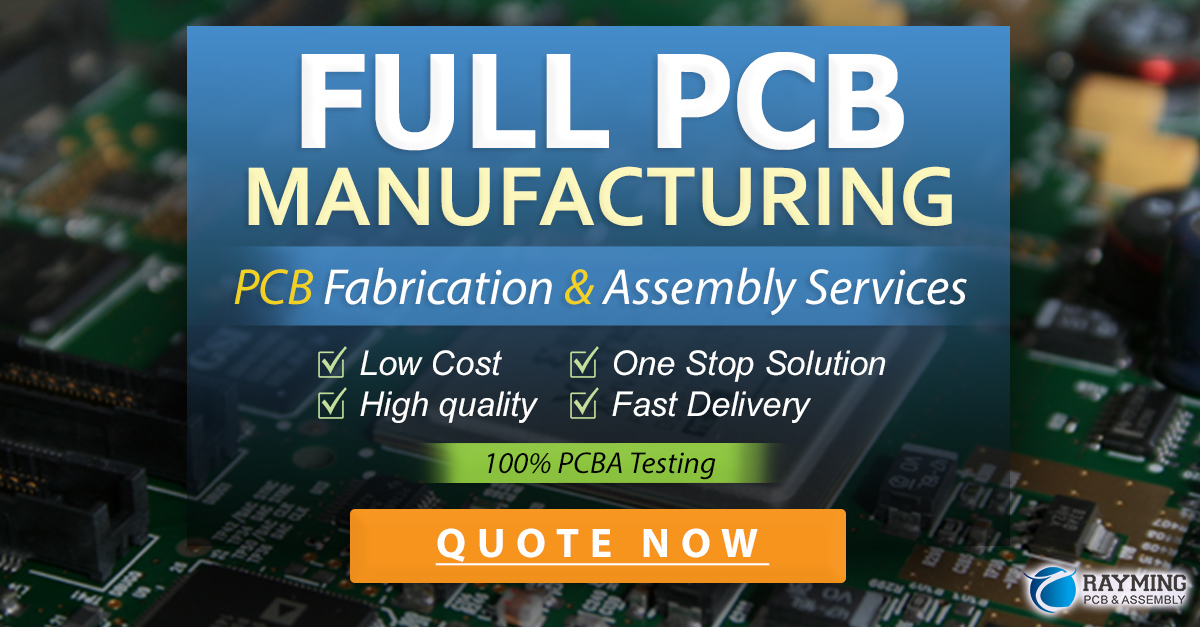
3. Automotive Electronics
3.1 Engine Control Units (ECUs)
Modern vehicles feature numerous electronic control units (ECUs) that manage various functions, such as engine control, transmission, braking, and suspension. These ECUs rely on robust and reliable PCBs that can operate in the harsh automotive environment, withstanding vibrations, temperature fluctuations, and exposure to chemicals. Automotive PCBs must also comply with stringent safety and reliability standards, such as AEC-Q100 and ISO 26262.
3.2 Infotainment Systems
In-vehicle infotainment systems have become increasingly sophisticated, offering features like touchscreens, navigation, audio/video playback, and smartphone integration. The PCBs used in these systems must support high-resolution displays, fast data processing, and seamless connectivity. They often incorporate high-speed interfaces, such as HDMI and USB, and require careful signal integrity management to ensure optimal performance.
3.3 Advanced Driver Assistance Systems (ADAS)
Advanced driver assistance systems (ADAS), such as lane departure warning, adaptive cruise control, and automatic emergency braking, rely on an array of sensors, cameras, and radar/lidar units. The PCBs used in these systems must process and analyze vast amounts of data in real-time, making high-performance computing and fast data transfer essential. Additionally, these PCBs must be designed with fail-safe mechanisms and redundancy to ensure the safety of the vehicle occupants.
4. Aerospace and Defense
4.1 Avionics
PCBs used in avionics systems, such as flight control, navigation, and communication equipment, must meet the highest standards of reliability and performance. These PCBs are subject to rigorous testing and certification processes to ensure they can withstand the extreme conditions encountered in aerospace applications, including high altitudes, rapid temperature changes, and intense vibrations. The use of high-reliability components, conformal coatings, and redundant circuits is common in avionics PCBs.
4.2 Radar and Surveillance Systems
Radar and surveillance systems employ PCBs that can handle high-frequency signals and provide precise timing control. These PCBs often feature high-speed digital interfaces, analog-to-digital converters (ADCs), and digital signal processors (DSPs) to enable real-time signal processing and target tracking. The use of low-loss materials and controlled impedance routing is crucial for maintaining signal integrity in these applications.
4.3 Unmanned Aerial Vehicles (UAVs)
Unmanned aerial vehicles (UAVs) or drones have gained prominence in both military and civilian applications. The PCBs used in UAVs must be lightweight, compact, and power-efficient to maximize flight time and payload capacity. They also need to support various sensors, communication modules, and flight control systems. Flexible and rigid-flex PCBs are often used in UAVs to accommodate the limited space and enable efficient integration of components.
5. Medical Devices
5.1 Diagnostic Equipment
PCBs are essential components in medical diagnostic equipment, such as MRI machines, CT scanners, and ultrasound devices. These PCBs must meet strict quality and reliability standards, as well as comply with regulatory requirements for medical devices. They often incorporate high-precision analog circuits, low-noise power supplies, and robust shielding to ensure accurate and reliable results.
5.2 Wearable Medical Devices
Wearable medical devices, such as fitness trackers, smartwatches, and continuous glucose monitors, have gained popularity in recent years. The PCBs used in these devices must be miniaturized, flexible, and low-power to ensure user comfort and long battery life. They often feature wireless connectivity, such as Bluetooth Low Energy (BLE) or Wi-Fi, to enable data transfer and remote monitoring.
5.3 Implantable Devices
Implantable medical devices, such as pacemakers, defibrillators, and neurostimulators, rely on highly reliable and biocompatible PCBs. These PCBs must be designed to withstand the harsh environment inside the human body, resisting moisture, chemicals, and mechanical stresses. They also need to be extremely power-efficient and feature fail-safe mechanisms to ensure patient safety.
6. Industrial Automation and Control
6.1 Programmable Logic Controllers (PLCs)
Programmable logic controllers (PLCs) are the backbone of industrial automation systems, controlling and monitoring various processes in manufacturing, energy, and infrastructure sectors. The PCBs used in PLCs must be rugged, reliable, and capable of operating in harsh industrial environments. They often feature robust power management, isolated interfaces, and industrial-grade components to ensure long-term reliability and performance.
6.2 Human-Machine Interfaces (HMIs)
Human-machine interfaces (HMIs) enable operators to interact with industrial automation systems, providing a user-friendly interface for monitoring and controlling processes. The PCBs used in HMIs must support high-resolution displays, touch input, and fast data processing. They often incorporate graphics processors, memory modules, and communication interfaces to enable seamless interaction and real-time data visualization.
6.3 Industrial Sensors and Actuators
Industrial sensors and actuators play a crucial role in automating and optimizing various processes. The PCBs used in these devices must be designed to interface with a wide range of sensors (e.g., temperature, pressure, flow) and actuators (e.g., valves, motors, solenoids). They often feature analog signal conditioning, digital-to-analog converters (DACs), and industrial communication protocols like Modbus or PROFIBUS to enable seamless integration with control systems.
7. Renewable Energy
7.1 Solar Inverters
Solar inverters convert the direct current (DC) generated by photovoltaic panels into alternating current (AC) for grid integration or local consumption. The PCBs used in solar inverters must handle high power levels, efficient power conversion, and stringent safety requirements. They often incorporate power electronic components, such as IGBTs or MOSFETs, along with complex control and monitoring circuits to ensure optimal performance and reliability.
7.2 Wind Turbine Control Systems
Wind turbine control systems regulate the operation of wind turbines, optimizing power generation and ensuring safe operation under varying wind conditions. The PCBs used in these systems must be designed to withstand the harsh environment inside the turbine nacelle, including vibrations, temperature fluctuations, and moisture. They often feature robust power management, redundant circuits, and industrial-grade components to ensure long-term reliability.
7.3 Energy Storage Systems
Energy storage systems, such as battery management systems (BMS) and grid-scale storage solutions, rely on PCBs for monitoring, control, and protection functions. The PCBs used in these systems must handle high voltages and currents, provide accurate monitoring of cell voltages and temperatures, and implement safety features like over-voltage and over-temperature protection. They often incorporate advanced power management ICs, communication interfaces, and fail-safe mechanisms to ensure reliable operation.
8. Internet of Things (IoT)
8.1 Smart Sensors and Actuators
The Internet of Things (IoT) has enabled the development of a wide range of smart sensors and actuators that can collect data and interact with the physical world. The PCBs used in these devices must be compact, low-power, and capable of wireless communication. They often feature microcontrollers, wireless modules (e.g., Wi-Fi, Bluetooth, LoRa), and energy-efficient sensors to enable long battery life and seamless integration with IoT platforms.
8.2 Edge Computing Devices
Edge computing devices process and analyze data close to the source, reducing latency and bandwidth requirements compared to cloud-based solutions. The PCBs used in edge computing devices must support high-performance computing, efficient power management, and flexible connectivity options. They often incorporate powerful processors, memory modules, and acceleration hardware like FPGAs or ASICs to enable real-time data processing and analytics.
8.3 IoT Gateways
IoT gateways act as intermediaries between IoT devices and cloud platforms, providing protocol translation, data aggregation, and security functions. The PCBs used in IoT gateways must support various communication protocols (e.g., Wi-Fi, Ethernet, cellular), handle high data throughput, and implement robust security features. They often feature powerful processors, ample memory, and multiple connectivity options to enable seamless integration of diverse IoT devices and networks.
9. Lighting and Displays
9.1 LED Lighting Systems
PCBs play a crucial role in LED lighting systems, providing power management, control, and thermal management functions. The PCBs used in LED lighting must be designed to handle high currents, ensure efficient heat dissipation, and implement dimming and color control features. They often incorporate LED drivers, microcontrollers, and thermal management solutions like metal-core PCBs (MCPCBs) to ensure optimal performance and longevity of the LED components.
9.2 Digital Signage and Billboards
Digital signage and billboards rely on PCBs to control and power large-format displays. The PCBs used in these applications must support high-resolution video processing, efficient power management, and reliable operation in various environmental conditions. They often feature high-speed video interfaces, scalable power delivery, and modular designs to enable flexible configuration and easy maintenance.
9.3 Virtual and Augmented Reality Devices
Virtual reality (VR) and augmented reality (AR) devices use PCBs to create immersive visual experiences. The PCBs in these devices must support high-resolution displays, precise motion tracking, and low-latency processing to minimize motion sickness and ensure realistic experiences. They often incorporate high-performance graphics processors, inertial measurement units (IMUs), and specialized display interfaces like MIPI or DisplayPort.
10. Aerospace and Satellite Applications
10.1 Spacecraft Electronics
PCBs used in spacecraft electronics must withstand the extreme conditions of space, including vacuum, radiation, and wide temperature ranges. These PCBs are subject to rigorous qualification and testing processes to ensure they can operate reliably in the harsh space environment. They often feature radiation-hardened components, redundant circuits, and specialized materials like polyimide or ceramic substrates to minimize outgassing and ensure long-term reliability.
10.2 Satellite Communication Modules
Satellite communication modules use PCBs to enable reliable data transmission between ground stations and satellites. The PCBs in these modules must support high-frequency RF circuits, precise timing control, and efficient power management. They often incorporate high-performance RF components, low-noise amplifiers (LNAs), and frequency synthesizers to ensure clear and stable communication links.
10.3 Space Instrumentation
Space instrumentation, such as telescopes, spectrometers, and imaging systems, rely on PCBs for data acquisition, signal processing, and control functions. The PCBs used in these instruments must be highly sensitive, low-noise, and capable of operating in the extreme conditions of space. They often feature specialized analog front-ends, high-resolution ADCs, and radiation-tolerant digital processors to enable accurate and reliable measurements.
Conclusion
PCBs have become an indispensable part of modern electronics, enabling the creation of complex and reliable systems across a wide range of industries. From consumer electronics to aerospace, PCBs play a crucial role in powering and interconnecting the devices that shape our world. As technology continues to advance, PCBs will undoubtedly evolve to meet the ever-increasing demands for performance, efficiency, and reliability.
FAQs
1. What are the key advantages of using PCBs in electronic devices?
PCBs offer several key advantages, including:
– Compact and organized layout of components
– Reliable and stable electrical connections
– Efficient heat dissipation and thermal management
– Ease of mass production and assembly
– Flexibility in design and customization
2. How do PCBs used in aerospace and defense differ from those used in consumer electronics?
PCBs used in aerospace and defense applications must meet much higher standards of reliability, durability, and performance compared to consumer electronics. These PCBs are subject to rigorous testing and certification processes to ensure they can withstand extreme conditions like high altitudes, rapid temperature changes, and intense vibrations. They often incorporate high-reliability components, conformal coatings, and redundant circuits to ensure fail-safe operation.
3. What role do PCBs play in the development of 5G networks?
PCBs are crucial for the deployment of 5G networks, as they enable the creation of high-frequency, low-loss circuits capable of handling millimeter-wave signals. 5G infrastructure, such as base stations and small cells, requires advanced PCB materials, like low-loss dielectrics and high-performance laminates, to minimize signal attenuation and ensure reliable communication. PCBs also play a key role in the development of 5G-enabled devices, such as smartphones and IoT sensors, by providing compact and efficient interconnects for high-speed data transfer.
4. How do PCBs contribute to the growth of the Internet of Things (IoT)?
PCBs are essential for the growth of the IoT, as they provide the foundation for creating compact, low-power, and wireless-enabled devices that can collect data and interact with the physical world. IoT devices, such as smart sensors, actuators, and edge computing devices, rely on PCBs to integrate microcontrollers, wireless modules, and energy-efficient components, enabling long battery life and seamless connectivity with IoT platforms. PCBs also play a crucial role in the development of IoT gateways, which aggregate data from multiple devices and provide secure communication with cloud services.
5. What are some of the challenges faced by PCB designers in today’s fast-paced electronics industry?
PCB designers face several challenges in today’s electronics industry, including:
– Keeping up with rapidly evolving technologies and standards
– Designing for high-speed and high-frequency applications while maintaining signal integrity
– Minimizing electromagnetic interference (EMI) and ensuring electromagnetic compatibility (EMC)
– Optimizing thermal management and power distribution in dense, high-performance designs
– Ensuring reliability and durability in harsh environmental conditions
– Complying with various industry-specific regulations and certifications
– Balancing cost, performance, and time-to-market pressures in a competitive landscape
Leave a Reply