Introduction to PCB Materials
Printed Circuit Boards (PCBs) are the backbone of modern electronic devices. They provide a platform for mounting and interconnecting electronic components, ensuring the proper functioning of the device. The choice of PCB material is crucial in determining the performance, reliability, and cost of the final product. In this article, we will explore the various PCB materials available and the services offered based on these materials.
Types of PCB Materials
There are several types of PCB materials available, each with its own unique properties and advantages. The most common PCB materials include:
-
FR-4: FR-4 is the most widely used PCB material. It is a composite material made of woven fiberglass cloth with an epoxy resin binder. FR-4 is known for its excellent mechanical and electrical properties, making it suitable for a wide range of applications.
-
High-Frequency Materials: High-frequency PCB materials are designed to support high-speed digital and RF/microwave applications. These materials have low dielectric constant and low loss tangent, allowing for faster signal propagation and reduced signal distortion. Examples of high-frequency materials include Rogers, Teflon, and PTFE.
-
Flexible PCBs: Flexible PCBs are made from flexible substrates such as polyimide or polyester. They offer the advantage of being able to bend and flex, making them suitable for applications where space is limited or where the PCB needs to conform to a specific shape.
-
Metal Core PCBs: Metal core PCBs have a metal substrate, typically aluminum, instead of the traditional FR-4 substrate. The metal core provides excellent thermal conductivity, allowing for efficient heat dissipation. Metal core PCBs are commonly used in high-power applications such as LED lighting and power electronics.
Factors to Consider When Choosing PCB Materials
When selecting the appropriate PCB material for a specific application, several factors need to be considered:
-
Electrical Requirements: The electrical requirements of the application, such as the operating frequency, signal integrity, and power handling capability, play a crucial role in determining the suitable PCB material.
-
Thermal Requirements: The thermal management needs of the application must be taken into account. If the PCB will be subjected to high temperatures or needs to dissipate heat efficiently, materials with good thermal conductivity, such as metal core PCBs, may be preferred.
-
Mechanical Requirements: The mechanical properties of the PCB material, such as its flexibility, strength, and durability, should be considered based on the application’s requirements. Flexible PCBs, for example, are suitable for applications that require bending or flexing.
-
Cost: The cost of the PCB material is an important factor, especially for high-volume production. FR-4 is often the most cost-effective option, while specialized materials like high-frequency laminates or metal core PCBs may be more expensive.
PCB Services Based on Material Choice
PCB manufacturers offer a range of services based on the chosen PCB material. These services ensure that the PCB is designed, fabricated, and assembled to meet the specific requirements of the application.
Design Services
PCB design services involve creating the layout and schematic of the PCB based on the customer’s specifications. The choice of PCB material influences the design process in several ways:
-
Layer Stack-up: The number of layers and the arrangement of copper and insulating layers in the PCB Stack-up depend on the chosen material. The material’s dielectric constant and thickness affect the impedance and signal integrity of the PCB.
-
Trace Width and Spacing: The trace width and spacing on the PCB are determined based on the electrical requirements and the material’s properties. High-frequency materials, for example, may require narrower traces and tighter spacing to minimize signal loss and distortion.
-
Via Design: The design of vias, which are used to interconnect different layers of the PCB, is influenced by the material’s thermal and mechanical properties. The via size, shape, and placement need to be optimized to ensure reliable electrical connections and minimize stress on the PCB.
Fabrication Services
PCB fabrication services involve the actual manufacturing of the PCB based on the provided design files. The fabrication process varies depending on the chosen PCB material:
-
Lamination: The PCB material is laminated together with the copper layers under high temperature and pressure. The lamination process parameters, such as temperature and pressure, are adjusted based on the material’s properties to ensure proper bonding.
-
Drilling: Holes are drilled through the PCB to accommodate components and vias. The drilling process needs to be optimized based on the material’s properties to avoid delamination or other defects.
-
Plating: The drilled holes are plated with copper to create electrical connections between layers. The plating process may differ based on the material’s compatibility with the plating chemicals and the desired plating thickness.
-
Etching: The unwanted copper is etched away from the PCB surface, leaving only the desired traces and pads. The etching process parameters are adjusted based on the material’s properties to ensure precise and consistent results.
Assembly Services
PCB Assembly services involve the mounting and soldering of electronic components onto the fabricated PCB. The choice of PCB material affects the assembly process in several ways:
-
Soldering: The soldering process, whether through-hole or surface mount, needs to be optimized based on the material’s thermal properties. The soldering temperature and duration are adjusted to ensure proper bonding without damaging the PCB or components.
-
Compatibility with Components: The PCB material must be compatible with the components being used. Some materials may not be suitable for certain types of components due to differences in thermal expansion or chemical reactivity.
-
Inspection and Testing: After assembly, the PCB undergoes inspection and testing to verify its functionality and reliability. The choice of PCB material may influence the inspection and testing methods used, such as X-ray inspection for metal core PCBs or high-frequency testing for RF/Microwave PCBs.
Advantages of Choosing the Right PCB Material
Selecting the appropriate PCB material for a specific application offers several advantages:
-
Improved Performance: Choosing a PCB material that matches the electrical, thermal, and mechanical requirements of the application ensures optimal performance. For example, using high-frequency materials for RF/microwave applications minimizes signal loss and distortion, resulting in better overall system performance.
-
Enhanced Reliability: The right PCB material enhances the reliability of the final product. Materials with good thermal conductivity, such as metal core PCBs, can effectively dissipate heat, preventing component failure due to overheating. Similarly, using flexible PCBs in applications that require bending or flexing reduces the risk of PCB damage or failure.
-
Cost Optimization: Selecting the most suitable PCB material helps optimize the cost of the final product. Using cost-effective materials like FR-4 for general-purpose applications reduces the overall manufacturing cost. On the other hand, investing in specialized materials for critical applications ensures reliable performance and minimizes the risk of costly failures or redesigns.
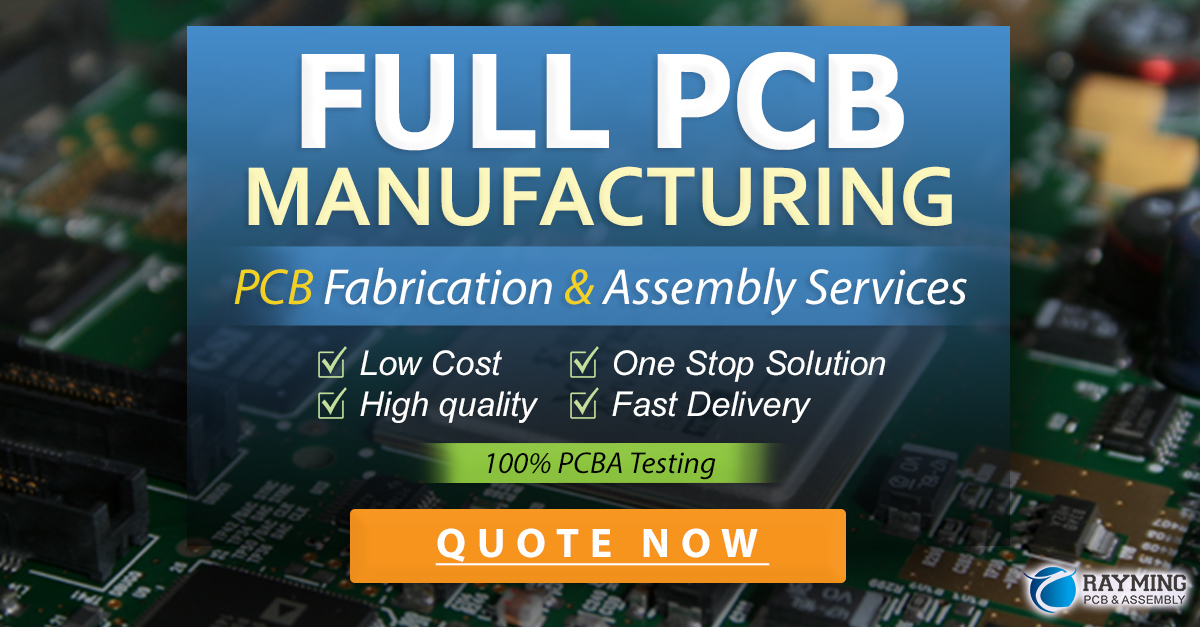
Common PCB Material Choices for Different Applications
Different applications have specific requirements that dictate the choice of PCB material. Here are some common PCB material choices for various applications:
Application | Common PCB Material Choice |
---|---|
Consumer Electronics | FR-4 |
High-Speed Digital | High-Frequency Materials |
RF/Microwave | Rogers, Teflon, PTFE |
Automotive Electronics | FR-4, High-Tg Materials |
Medical Devices | FR-4, Polyimide |
LED Lighting | Metal Core PCBs |
Wearable Electronics | Flexible PCBs |
Aerospace and Defense | High-Reliability Materials |
FAQ
-
Q: What is the most commonly used PCB material?
A: FR-4 is the most commonly used PCB material due to its excellent balance of electrical, mechanical, and thermal properties, as well as its cost-effectiveness. -
Q: What are high-frequency PCB materials used for?
A: High-frequency PCB materials are used for applications that require high-speed signal transmission, such as RF/microwave circuits, radar systems, and high-speed digital communication devices. These materials have low dielectric constant and low loss tangent, enabling faster signal propagation and reduced signal distortion. -
Q: When should I consider using a flexible PCB?
A: Flexible PCBs are suitable for applications where the PCB needs to bend or flex, such as in wearable electronics, medical devices, or compact electronic assemblies. They offer the advantage of conforming to specific shapes and saving space in tight packaging environments. -
Q: What are the benefits of using metal core PCBs?
A: Metal core PCBs offer excellent thermal conductivity, allowing for efficient heat dissipation. They are commonly used in high-power applications, such as LED lighting and power electronics, where heat management is critical. Metal core PCBs help prevent component failure due to overheating and improve the overall reliability of the system. -
Q: How does the choice of PCB material affect the cost of the final product?
A: The choice of PCB material has a direct impact on the cost of the final product. FR-4 is generally the most cost-effective option for general-purpose applications. Specialized materials, such as high-frequency laminates or metal core PCBs, may be more expensive due to their unique properties and manufacturing requirements. However, investing in the appropriate PCB material for critical applications can help optimize performance, reliability, and long-term cost savings by minimizing the risk of failures or redesigns.
Conclusion
The choice of PCB material is a critical factor in determining the performance, reliability, and cost of electronic devices. Understanding the properties and advantages of different PCB materials enables designers and manufacturers to select the most suitable option for their specific application requirements.
PCB services, including design, fabrication, and assembly, are tailored based on the chosen PCB material to ensure optimal results. By considering factors such as electrical, thermal, and mechanical requirements, as well as cost constraints, designers can make informed decisions when selecting PCB materials.
Choosing the right PCB material offers numerous benefits, including improved performance, enhanced reliability, and cost optimization. Different applications have specific material requirements, ranging from general-purpose FR-4 to specialized high-frequency materials, flexible PCBs, and metal core PCBs.
As technology advances and new applications emerge, the demand for innovative PCB materials and services continues to grow. PCB manufacturers and service providers play a crucial role in supporting these advancements by offering expertise and solutions based on the latest material technologies.
By understanding the importance of PCB material choice and leveraging the appropriate PCB services, designers and manufacturers can create high-quality, reliable electronic products that meet the ever-evolving needs of the market.
Leave a Reply