Types of PCB Laminates
There are several different types of PCB laminate materials, each with its own unique properties and characteristics. The most common types include:
FR-4
FR-4 (Flame Retardant 4) is the most widely used PCB laminate material. It is a composite material composed of woven fiberglass cloth with an epoxy resin binder.
Advantages of FR-4:
– Low cost
– Good mechanical strength
– Excellent electrical insulation
– Decent moisture and chemical resistance
– Suitable for most general purpose applications
Disadvantages of FR-4:
– Higher dielectric loss and signal attenuation at high frequencies
– Reduced performance above 1-2 GHz
– Higher thermal expansion than other laminates
High Tg FR-4
High Tg (glass transition temperature) FR-4 is a variation of standard FR-4 that uses a special high Tg epoxy resin. This improves its thermal stability and performance in high temperature environments.
Advantages of High Tg FR-4:
– Improved thermal stability up to 170-180°C
– Better heat resistance for lead-free soldering and high temp uses
– Lower thermal expansion and better plated through-hole reliability
Disadvantages of High Tg FR-4:
– Higher cost than standard FR-4
– Slightly lower glass transition temp than dedicated high-temp laminates
Polyimide
Polyimide laminates use a polyimide resin system rather than standard epoxy. This provides superior thermal stability and low thermal expansion for high reliability applications.
Advantages of Polyimide:
– Excellent thermal stability up to 260°C or higher
– Very low thermal expansion for outstanding reliability
– Superb chemical resistance
– Extremely low moisture absorption
Disadvantages of Polyimide:
– High cost, typically several times more than FR-4
– Requires specialized fabrication processes
– Lower peel strength of copper foil
PTFE/Teflon
PTFE (polytetrafluoroethylene) laminates, also known by the DuPont brand name Teflon, provide the best high frequency performance of any PCB base material. They have an extremely low dielectric constant and dissipation factor.
Advantages of PTFE:
– Best in class high frequency/low loss performance
– Stable electrical properties over temperature and frequency
– Low moisture absorption
– Useful to mm-wave frequencies >100 GHz
Disadvantages of PTFE:
– Very high cost
– Soft, flexible material difficult to process
– Poor dimensional stability
– Lower thermal conductivity and high expansion
Hydrocarbon/Rogers
Hydrocarbon ceramic laminates like Rogers 4000-series materials offer a balance of good high frequency performance, low loss, and reasonable cost. They fall between FR-4 and PTFE in performance and price.
Advantages of Rogers 4000-series:
– Good high frequency performance to 20-30 GHz
– Low dielectric constant and loss tangent
– Mechanically robust and easy to fabricate
– Relatively low thermal expansion
Disadvantages of Rogers 4000-series:
– Higher cost than FR-4, but lower than PTFE
– Some moisture absorption, requiring baking
– Bonding of layers in multilayer PCBs more difficult
The table below summarizes the key properties of these different PCB laminate materials:
Material | Dk @ 1 GHz | Df @ 1 GHz | Tg (°C) | CTE (ppm/°C) | Moisture Abs. | Cost |
---|---|---|---|---|---|---|
FR-4 | 4.2-4.5 | 0.015-0.025 | 130-140 | 12-16 | 0.1-0.2% | $ |
High Tg | 4.2-4.5 | 0.012-0.020 | 170-180 | 11-14 | 0.1-0.2% | $$ |
Polyimide | 3.5-4.0 | 0.005-0.010 | 220-260 | 12-30 | 0.4-0.8% | $$$$ |
PTFE | 2.0-2.8 | 0.001-0.005 | 327 | 100-200 | <0.03% | $$$$$ |
Rogers | 3.3-3.7 | 0.003-0.006 | 280-360 | 30-60 | 0.06-0.2% | $$$ |
Dk = dielectric constant, Df = dissipation factor, Tg = glass transition temp, CTE = coefficient of thermal expansion. Costs are relative, from lowest ($) to highest ($$$$$).
Key Properties of PCB Laminates
When selecting a PCB laminate material, there are several key properties to consider:
Dielectric Constant (Dk)
The dielectric constant (Dk) of a laminate is a measure of its ability to store electric field energy. In PCBs, a lower Dk is desirable as it allows electromagnetic waves to travel faster through the material. This is particularly important at high frequencies.
Dk values of common PCB laminates:
– FR-4: 4.2-4.5 @ 1 GHz
– Polyimide: 3.5-4.0 @ 1 GHz
– PTFE: 2.0-2.8 @ 1 GHz
– Rogers 4000-series: 3.3-3.7 @ 1 GHz
Dissipation Factor (Df)
The dissipation factor (Df), also known as loss tangent, is a measure of a laminate’s tendency to absorb energy from an alternating electric field. A lower Df indicates lower dielectric losses and is desirable for high frequency PCBs to minimize signal attenuation.
Df values of common PCB laminates:
– FR-4: 0.015-0.025 @ 1 GHz
– Polyimide: 0.005-0.010 @ 1 GHz
– PTFE: 0.001-0.005 @ 1 GHz
– Rogers 4000-series: 0.003-0.006 @ 1 GHz
Glass Transition Temperature (Tg)
The glass transition temperature (Tg) is the temperature at which a laminate transitions from a hard, glassy state to a soft, rubbery state. A higher Tg provides better thermal stability and resistance to deformation at elevated temperatures.
Tg values of common PCB laminates:
– Standard FR-4: 130-140°C
– High Tg FR-4: 170-180°C
– Polyimide: 220-260°C
– PTFE: 327°C
– Rogers 4000-series: 280-360°C
Coefficient of Thermal Expansion (CTE)
The coefficient of thermal expansion (CTE) is a measure of how much a material expands with increasing temperature. A lower CTE more closely matches that of copper (17 ppm/°C), providing better dimensional stability and reliability.
CTE values of common PCB laminates (ppm/°C):
– FR-4: 12-16
– High Tg FR-4: 11-14
– Polyimide: 12-30
– PTFE: 100-200
– Rogers 4000-series: 30-60
Moisture Absorption
Moisture absorption is the tendency of a laminate to absorb moisture from the environment. Excess moisture absorbed into the PCB can cause issues like delamination, warpage, and degraded electrical performance.
Moisture absorption of common PCB laminates:
– FR-4: 0.1-0.2%
– Polyimide: 0.4-0.8%
– PTFE: <0.03%
– Rogers 4000-series: 0.06-0.2%
Thermal Conductivity
Thermal conductivity is a measure of a material’s ability to conduct heat. Higher thermal conductivity allows the PCB to better dissipate heat generated by components and traces. This is important for power electronics and high-temperature applications.
Thermal conductivity of common PCB laminates (W/mK):
– FR-4: 0.3-0.4
– Polyimide: 0.4-0.7
– PTFE: 0.2-0.3
– Rogers 4000-series: 0.6-0.7
Peel Strength
Peel strength is the force required to peel the copper foil off the laminate base material. A higher peel strength provides better adhesion and resistance to delamination.
Typical peel strength specs for PCB laminates (lbs/in):
– FR-4: 6-10
– Polyimide: 4-8
– PTFE: 4-8
– Rogers 4000-series: 5-8
How to Select a PCB Laminate
With all the different laminate options and properties to consider, how do you go about selecting the right material for your PCB? Here are some guidelines:
-
Consider your operating frequency. For high frequency (>1 GHz), RF/microwave PCBs, choose a low loss laminate like PTFE or Rogers. For frequencies below 2 GHz, standard or high-Tg FR-4 is usually sufficient.
-
Determine your operating temperature range. If your PCB will be exposed to high temperatures (>130°C), select a high-Tg material like polyimide or Rogers. Standard FR-4 is suitable for temps up to 130°C.
-
Evaluate your PCB’s mechanical requirements. Will it be subjected to vibration or physical stress? Materials like polyimide and Rogers offer better mechanical strength and stability than PTFE.
-
Consider your budget and cost targets. FR-4 is the lowest cost material, followed by high-Tg FR-4, hydrocarbon ceramics (Rogers), polyimide, and PTFE. Choose the lowest cost material that meets your electrical, thermal, and mechanical needs.
-
Consult with your PCB fabricator. They can offer guidance on material selection and availability based on your specific PCB requirements.
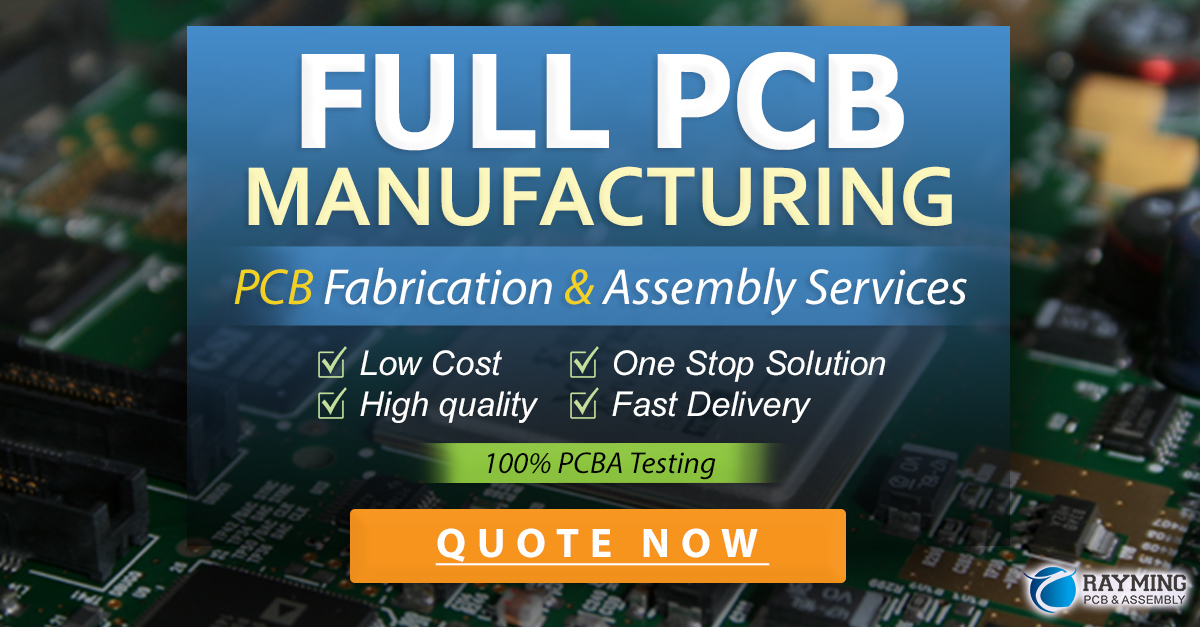
Industry Standards for PCB Laminates
There are several industry standards that specify requirements and grades for PCB laminates, including:
- IPC-4101: Specification for Base Materials for Rigid and Multilayer Printed Boards
- NEMA LI 1: Industrial Laminated Thermosetting Products
- MIL-S-13949: Military Specification for Plastic Sheet, Laminated, Metal-Clad (for Printed Wiring Boards)
- IPC-TM-650: Test Methods Manual
IPC-4101 classifies PCB laminates into different grades based on their performance characteristics, such as thermal resistance, flamability, peel strength, moisture resistance, etc.
Some common IPC-4101 laminate grades include:
– FR-4: Standard grade, designated by IPC-4101/21 and /26.
– High Tg FR-4: Designated by IPC-4101/126 and /129.
– Polyimide: Designated by IPC-4101/41 and /42.
– PTFE: Designated by IPC-4101/13.
Always refer to the relevant industry standards and specifications when selecting a PCB laminate to ensure it meets the requirements for your application.
FAQs about PCB Laminates
What is a PCB laminate?
A PCB laminate is the base insulating material used to construct a printed circuit board. It provides mechanical support for the circuit and electrically insulates the conductive copper traces. PCB laminates are typically a composite of a reinforcing material like fiberglass and a thermoset resin like epoxy.
What are the most common PCB laminate materials?
The most common PCB laminate materials are:
– FR-4: A composite of woven fiberglass and epoxy resin. The default choice for most PCBs.
– Polyimide: Uses a polyimide resin for higher thermal stability and lower expansion than FR-4.
– PTFE/Teflon: Best high frequency/microwave performance but higher cost and harder to fabricate.
– Hydrocarbon/Ceramic: A balance of good high frequency performance and cost. Rogers is a major brand.
How do I select a PCB laminate?
To select a PCB laminate, consider your operating frequency and temperature range, mechanical requirements, and budget/cost targets. For high frequency RF/microwave PCBs, use a low loss material like PTFE or Rogers. For high temp environments, use a high Tg material like polyimide or Rogers. FR-4 is suitable for most general purpose PCBs up to 2 GHz and 130°C. Consult with your PCB fabricator for guidance based on your specific application.
What properties of PCB laminates are important?
The key properties of PCB laminates are:
– Dielectric constant (Dk): Lower Dk for faster wave propagation, important at high frequencies.
– Dissipation factor (Df): Lower Df for lower dielectric losses and signal attenuation.
– Glass transition temp (Tg): Higher Tg for better thermal stability at high operating temps.
– Coefficient of thermal expansion (CTE): Lower CTE for better reliability and dimensional stability.
– Moisture absorption: Lower moisture absorption avoids issues like delamination and warping.
– Thermal conductivity: Higher thermal conductivity allows better heat dissipation.
– Peel strength: Higher peel strength means better copper adhesion and less risk of delamination.
Are there industry standards for PCB laminates?
Yes, there are several industry standards that specify requirements and grades for PCB laminates:
– IPC-4101 classifies laminates into different grades based on performance characteristics.
– NEMA LI 1 covers industrial laminated thermosetting products.
– MIL-S-13949 is a US military specification for metal-clad laminated plastic sheets for PCBs.
Always refer to the relevant specifications to ensure your selected laminate meets the requirements for your application.
Conclusion
PCB laminates are the foundation of every printed circuit board. By understanding the different types of laminates, their key properties, and how to select the right one for your application, you’ll be well on your way to designing reliable, high-performance PCBs.
Use this guide as a reference when evaluating PCB laminate materials for your next project. And don’t forget to consult with your PCB fabricator for their expert advice and guidance. With the right laminate selected, you can ensure your PCB will perform as intended for years to come.
Leave a Reply