The Importance of Accurate PCB Drill Sizes
Accurate PCB drill sizes play a critical role in the overall performance and reliability of electronic devices. Properly sized holes ensure that components fit securely, establish reliable electrical connections, and maintain the structural integrity of the PCB. Incorrect drill sizes can lead to a range of issues, including:
- Difficulty in component insertion or removal
- Poor electrical connections leading to signal integrity issues
- Mechanical stress on the PCB and components
- Increased risk of PCB failure due to structural weaknesses
Therefore, it is essential for PCB designers and manufacturers to have a thorough understanding of drill sizes and their implications.
Standard PCB Drill Sizes
PCB drill sizes are typically expressed in either inches or millimeters. In the electronics industry, drill sizes are often referred to by their decimal inch equivalents or by specific drill codes. Here are some commonly used PCB drill sizes:
Drill Size (Inch) | Drill Size (mm) | Typical Use |
---|---|---|
0.0135″ | 0.343 mm | Ultra-fine pitch components |
0.0160″ | 0.406 mm | Fine-pitch components |
0.0197″ | 0.500 mm | Standard component leads |
0.0280″ | 0.711 mm | Larger component leads and vias |
0.0390″ | 0.991 mm | Power component leads and mounting holes |
0.0625″ | 1.588 mm | Connector pins and large mounting holes |
It is important to note that these are just a few examples, and PCB drill sizes can vary depending on the specific requirements of the project and the components being used.
PCB Drill Size Tolerances
Maintaining tight tolerances on PCB drill sizes is crucial for ensuring proper fit and functionality of components. The acceptable tolerance range depends on various factors, such as the PCB material, drilling method, and the specific requirements of the components being used.
Typically, the tolerance for PCB drill sizes is expressed as a plus or minus value, indicating the acceptable deviation from the nominal drill size. For example, a drill size of 0.0197″ (0.500 mm) with a tolerance of ±0.002″ (±0.051 mm) means that the actual drill size can range from 0.0177″ to 0.0217″ (0.449 mm to 0.551 mm).
Tighter tolerances may be required for high-density PCB designs or when using components with strict mechanical specifications. In such cases, designers and manufacturers must work closely together to ensure that the drill sizes and tolerances are carefully controlled throughout the manufacturing process.
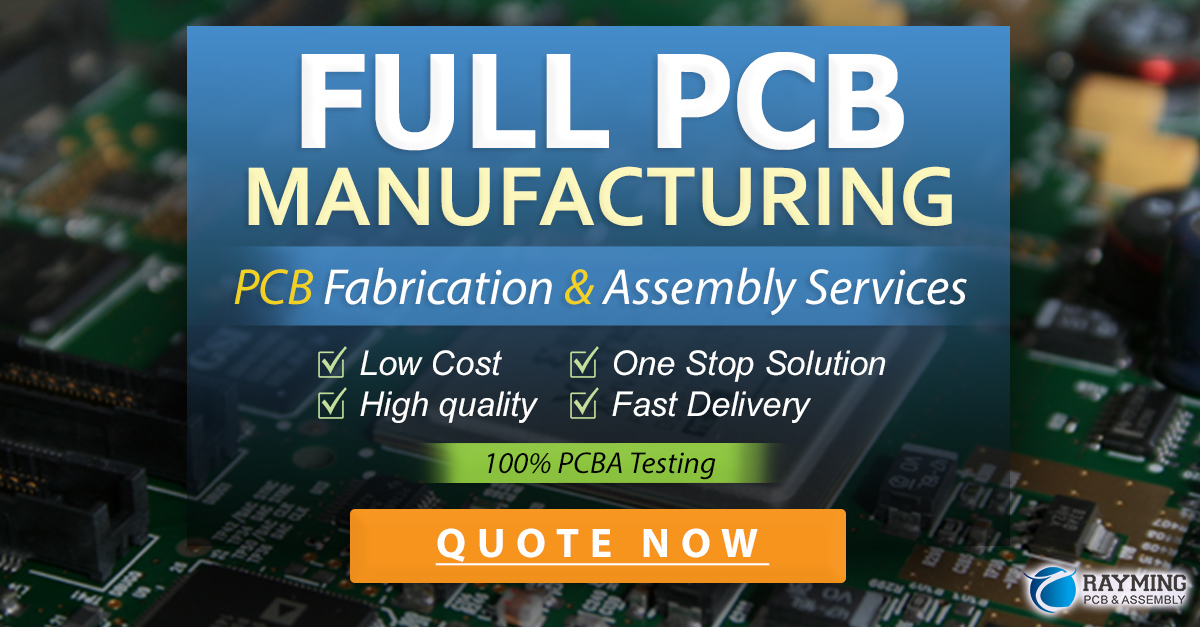
Drill Bit Materials and Their Impact on PCB Quality
The choice of drill bit material can significantly impact the quality and consistency of PCB drill holes. The most common drill bit materials used in PCB manufacturing are:
-
Carbide: Carbide drill bits are known for their exceptional hardness and wear resistance. They are suitable for drilling a wide range of PCB materials, including FR-4, high-Tg laminates, and metal-clad substrates. Carbide drill bits offer excellent hole quality and long tool life, making them a popular choice for high-volume production.
-
High-Speed Steel (HSS): HSS drill bits are a cost-effective option for drilling PCBs with less demanding requirements. They are best suited for drilling softer materials, such as standard FR-4 laminates. While HSS drill bits may not offer the same level of wear resistance as carbide, they can still provide satisfactory results when used with appropriate drilling parameters and regular replacement intervals.
-
Diamond-Coated: Diamond-coated drill bits feature a thin layer of synthetic diamond particles on the cutting edges. This coating enhances the drill bit’s hardness, wear resistance, and heat dissipation properties. Diamond-coated drill bits are particularly effective for drilling abrasive materials, such as ceramic substrates or metal-backed PCBs. They offer excellent hole quality and extended tool life, although they come at a higher cost compared to carbide or HSS drill bits.
The selection of drill bit material depends on factors such as the PCB material, required hole quality, production volume, and cost considerations. It is essential to consult with the PCB manufacturer and drill bit suppliers to determine the most suitable drill bit material for a specific project.
Optimizing PCB Drill Sizes for Manufacturability
To ensure the manufacturability and reliability of PCBs, designers should follow best practices when specifying drill sizes. Here are some guidelines to optimize PCB drill sizes for manufacturability:
-
Adhere to standard drill sizes: Whenever possible, use standard drill sizes that are readily available and commonly used in the industry. This approach reduces tooling costs, improves availability, and minimizes the risk of manufacturing issues.
-
Consider component requirements: Carefully review the mechanical specifications of the components being used and select drill sizes that provide a secure fit without compromising the component’s integrity. Consult component datasheets and application notes for recommended drill sizes and tolerances.
-
Allow for plating thickness: When specifying drill sizes, account for the thickness of the copper plating that will be deposited inside the holes. The plating thickness can reduce the effective hole diameter, so it is essential to adjust the drill size accordingly to ensure proper component fit.
-
Minimize drill size variations: Limit the number of different drill sizes used in a PCB design to reduce tooling costs and improve manufacturing efficiency. Whenever possible, consolidate similar drill sizes and use a common size for multiple components or vias.
-
Provide clear documentation: Include comprehensive and accurate drill information in the PCB design files and fabrication drawings. Clearly specify the nominal drill sizes, tolerances, and any special requirements for critical holes. Effective communication between the design team and the PCB manufacturer is crucial for avoiding misinterpretations and ensuring successful production.
By following these guidelines, PCB designers can optimize drill sizes for manufacturability, reducing the risk of production issues and ensuring the consistent quality of the final product.
Frequently Asked Questions (FAQ)
-
What is the most common PCB drill size?
The most common PCB drill size is 0.0197″ (0.500 mm), which is suitable for a wide range of standard component leads. -
How do I select the appropriate drill size for a specific component?
To select the appropriate drill size for a specific component, consult the component’s datasheet or application notes. These resources typically provide recommended drill sizes and tolerances for optimal fit and performance. -
Can I use any drill bit material for PCB Drilling?
While different drill bit materials can be used for PCB drilling, the choice depends on factors such as the PCB material, required hole quality, and production volume. Carbide and diamond-coated drill bits are commonly used for their hardness and wear resistance, while high-speed steel (HSS) drill bits are a cost-effective option for less demanding applications. -
What are the consequences of using incorrect PCB drill sizes?
Using incorrect PCB drill sizes can lead to various issues, such as difficulty in component insertion or removal, poor electrical connections, mechanical stress on the PCB and components, and an increased risk of PCB failure due to structural weaknesses. -
How can I ensure the consistency and accuracy of PCB drill sizes during manufacturing?
To ensure the consistency and accuracy of PCB drill sizes during manufacturing, follow best practices such as adhering to standard drill sizes, considering component requirements, allowing for plating thickness, minimizing drill size variations, and providing clear documentation to the PCB manufacturer. Regular maintenance and calibration of drilling equipment, along with strict quality control measures, are also essential for achieving consistent results.
Conclusion
PCB drill sizes play a crucial role in the performance, reliability, and manufacturability of electronic devices. Understanding the importance of accurate drill sizes, standard sizes, tolerances, drill bit materials, and best practices for optimizing manufacturability is essential for PCB designers and manufacturers.
By selecting appropriate drill sizes, maintaining tight tolerances, and following industry guidelines, designers can ensure that their PCB designs are compatible with the intended components and can be manufactured consistently and efficiently. Close collaboration between the design team and the PCB manufacturer is crucial for addressing any challenges and ensuring the successful production of high-quality PCBs.
As technology advances and electronic devices become more complex, the importance of accurate and well-designed PCB drill sizes will only continue to grow. By staying informed about the latest developments and best practices in PCB drilling, designers and manufacturers can stay ahead of the curve and deliver innovative, reliable, and cost-effective electronic solutions.
Leave a Reply