Introduction to PCB Panels
Printed Circuit Boards (PCBs) are the backbone of modern electronics. They provide a reliable and efficient means of connecting electronic components in a compact and organized manner. PCBs are used in a wide range of applications, from consumer electronics to industrial equipment and aerospace systems. In many cases, PCBs are manufactured and delivered in panels to optimize production efficiency and reduce costs. This article will explore the guidelines for PCBs delivered in a panel, with a focus on the key considerations for designers, manufacturers, and end-users.
What is a PCB Panel?
A PCB panel, also known as a PCB array or PCB matrix, is a larger PCB that contains multiple smaller PCBs. The individual PCBs are arranged in a grid pattern and connected by a frame or border, which is later removed during the depaneling process. PCB panels allow for the simultaneous production of multiple PCBs, reducing manufacturing time and costs.
Advantages of Using PCB Panels
There are several advantages to using PCB panels in the manufacturing process:
- Increased production efficiency: By producing multiple PCBs simultaneously, manufacturers can reduce setup time and optimize material usage.
- Reduced costs: PCB panels allow for the sharing of tooling and processing costs across multiple PCBs, resulting in lower per-unit costs.
- Improved quality control: With PCBs arranged in a panel, it is easier to maintain consistent quality across all boards during the manufacturing process.
- Simplified handling and storage: PCB panels provide a convenient means of handling and storing multiple PCBs, reducing the risk of damage during transportation and storage.
Designing PCBs for Panel Manufacturing
When designing PCBs that will be delivered in a panel, there are several key considerations to keep in mind. These guidelines will help ensure that your PCBs are compatible with panel manufacturing processes and meet the required specifications.
Board Size and Shape
The size and shape of the individual PCBs within a panel should be carefully considered to optimize material usage and minimize waste. When designing the board, keep the following points in mind:
- Rectangular shapes are preferred, as they allow for the most efficient use of panel space.
- If possible, design boards with standard dimensions to minimize the need for custom tooling.
- Consider the spacing between individual boards, known as the “route” or “mill” space, which is typically 2-3 mm wide.
Panelization Layout
The layout of the individual PCBs within the panel should be carefully planned to ensure proper spacing and alignment. Consider the following guidelines:
- Arrange boards in a grid pattern, with consistent spacing between each board.
- Include fiducial marks on the panel to aid in alignment during the manufacturing process.
- If using V-scoring or tab routing for depaneling, ensure that the scores or tabs are located in areas that will not affect the functionality of the individual PCBs.
Copper Balancing
Copper balancing is the process of ensuring that the copper distribution on the PCB panel is even, which helps prevent warping and other defects during the manufacturing process. To achieve proper copper balancing, consider the following:
- Distribute copper evenly across the panel, avoiding large concentrations in any one area.
- Use copper thieving techniques, such as adding non-functional copper pours or patterns, to balance copper distribution.
- If necessary, adjust the design of individual PCBs to achieve better copper balance across the panel.
Solder Mask and Silkscreen
When designing PCBs for panel manufacturing, it is important to consider the application of solder mask and silkscreen. Keep the following points in mind:
- Ensure that there is sufficient clearance between the edge of the PCB and any solder mask or silkscreen features.
- If using a border around the individual PCBs, make sure that the solder mask and silkscreen extend to the edge of the border to prevent exposed copper.
- Consider the color and finish of the solder mask and silkscreen to ensure compatibility with your application and any relevant standards.
Manufacturing PCBs in Panels
Once the PCB design is complete and optimized for panel manufacturing, the actual production process can begin. This section will outline the key steps involved in manufacturing PCBs in panels.
Material Selection
The first step in the manufacturing process is to select the appropriate materials for the PCB panel. The most common materials used for PCB substrates are:
- FR-4: A glass-reinforced epoxy laminate, FR-4 is the most widely used PCB material due to its good electrical and mechanical properties, as well as its cost-effectiveness.
- High-Tg FR-4: This variant of FR-4 offers improved thermal stability and is suitable for applications with higher operating temperatures.
- Polyimide: Polyimide substrates offer excellent thermal stability and are often used in high-temperature applications or for flexible PCBs.
- Aluminum: Aluminum PCBs are used in applications that require high thermal conductivity, such as LED lighting or power electronics.
Fabrication Process
The fabrication process for PCB panels typically involves the following steps:
- Inner layer processing: The inner layers of the PCB are etched with the desired circuit pattern using a photolithographic process.
- Lamination: The inner layers are laminated together with prepreg (pre-impregnated) and copper foil to form the complete PCB Stackup.
- Drilling: Holes are drilled through the PCB panel to accommodate through-hole components and vias.
- Plating: The drilled holes are plated with copper to create electrical connections between layers.
- Outer layer processing: The outer layers of the PCB are etched with the desired circuit pattern, and any additional features (such as solder mask and silkscreen) are applied.
Depaneling
Once the PCB panel is fully processed, the individual PCBs must be separated from the panel. This process is known as depaneling, and there are several methods available:
- V-scoring: V-shaped grooves are cut into the panel, allowing the individual PCBs to be easily snapped out.
- Tab routing: Small tabs are left connecting the individual PCBs to the panel frame, which can be broken off after processing.
- Laser cutting: A laser is used to cut the individual PCBs from the panel, providing a clean and precise edge.
- Die punching: A custom-shaped die is used to punch out the individual PCBs from the panel.
The choice of depaneling method will depend on factors such as the PCB design, material, and application requirements.
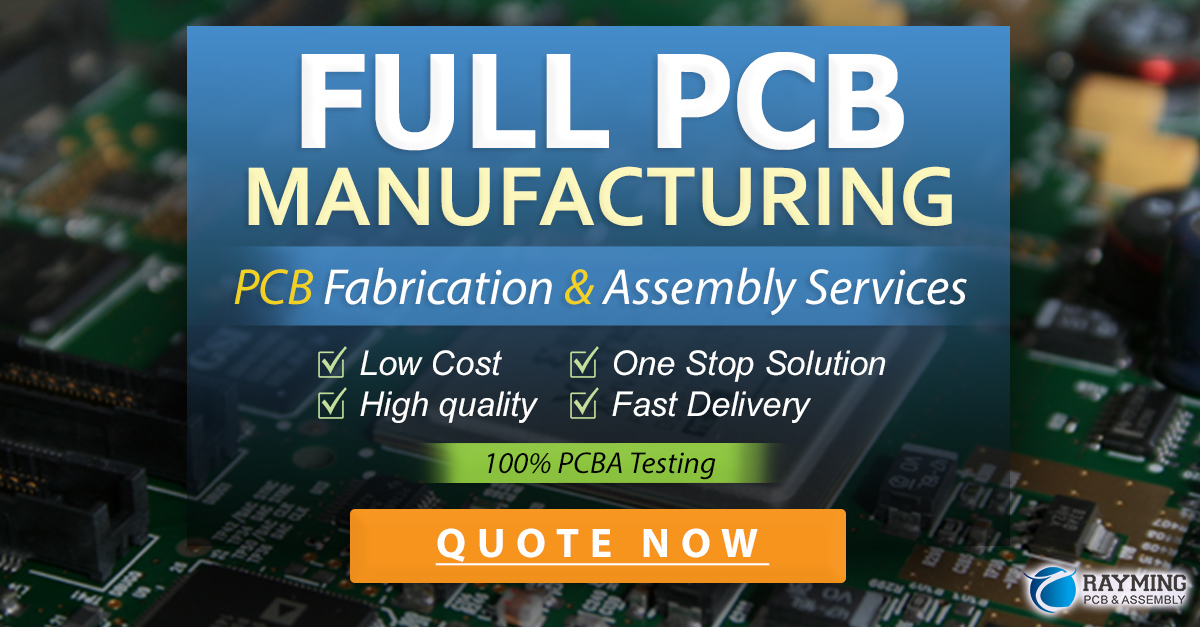
Quality Control and Testing
To ensure that PCBs manufactured in panels meet the required specifications and perform as intended, a rigorous quality control and testing process is essential. This section will outline the key steps involved in quality control and testing for PCB panels.
Visual Inspection
The first step in the quality control process is a visual inspection of the PCB panel. This inspection should check for:
- Proper alignment and registration of layers
- Correct hole sizes and locations
- Absence of surface defects, such as scratches, dents, or contamination
- Proper application of solder mask and silkscreen
Any panels that do not meet the required visual criteria should be rejected.
Electrical Testing
After visual inspection, the PCB panel undergoes electrical testing to verify the integrity of the circuits and the functionality of the individual PCBs. Common electrical tests include:
- Continuity testing: Verifies that all intended electrical connections are present and functional.
- Isolation testing: Ensures that there are no unintended electrical connections between circuits.
- Impedance testing: Measures the impedance of controlled impedance traces to ensure they meet the required specifications.
- Functional testing: Verifies that the individual PCBs perform as intended in their specific application.
PCB panels that pass all required electrical tests can proceed to the next stage of the quality control process.
Microsectioning
Microsectioning is a destructive testing method that involves cutting a small sample from the PCB panel and examining it under a microscope. This process allows for the inspection of the internal structure of the PCB, including:
- Laminate integrity and layer registration
- Drilled hole quality and plating thickness
- Copper trace dimensions and spacing
Microsectioning is typically performed on a sample basis, with the results used to validate the overall quality of the PCB panel batch.
Environmental Testing
Depending on the application and the requirements of the end-user, PCB panels may also undergo environmental testing to ensure their ability to perform under specific conditions. Common environmental tests include:
- Thermal cycling: Exposes the PCB panel to alternating high and low temperatures to simulate the effects of thermal stress over the product’s lifetime.
- Humidity testing: Subjects the PCB panel to high humidity levels to evaluate its resistance to moisture-related defects.
- Vibration and shock testing: Assesses the PCB panel’s ability to withstand mechanical stresses encountered during transportation, handling, and use.
PCB panels that pass all required environmental tests are deemed suitable for their intended application and can be released for final processing and shipment.
Handling and Storage Guidelines
Proper handling and storage of PCB panels are essential to maintain their quality and performance. This section will provide guidelines for the handling and storage of PCB panels throughout the manufacturing process and beyond.
Handling Guidelines
When handling PCB panels, it is important to observe the following guidelines to minimize the risk of damage or contamination:
- Wear clean, lint-free gloves to prevent the transfer of oils, salts, and other contaminants from the skin to the PCB surface.
- Handle panels by the edges to avoid touching the surface of the PCBs.
- Use a vacuum pen or tweezers to handle individual PCBs after depaneling.
- Avoid bending or flexing the panels, as this can cause damage to the PCBs or the panel frame.
Storage Guidelines
Proper storage of PCB panels is crucial to maintain their quality and performance over time. Follow these guidelines for storing PCB panels:
- Store panels in a cool, dry environment with a temperature range of 10-30°C and a relative humidity of 30-70%.
- Use clean, dust-free packaging materials, such as antistatic bags or containers, to protect the panels from contaminants and electrostatic discharge (ESD).
- Stack panels horizontally, with appropriate support to prevent warping or bending.
- Avoid exposing panels to direct sunlight or other sources of UV radiation, which can cause degradation of the PCB materials.
By following these handling and storage guidelines, manufacturers and end-users can ensure that PCB panels maintain their quality and performance throughout their lifecycle.
Frequently Asked Questions (FAQ)
- What is the minimum spacing required between individual PCBs on a panel?
-
The minimum spacing between individual PCBs, known as the “route” or “mill” space, is typically 2-3 mm wide. This spacing allows for the depaneling process and helps prevent damage to the PCBs during separation.
-
How does copper balancing help prevent defects in PCB panels?
-
Copper balancing ensures that the copper distribution on the PCB panel is even. This helps prevent warping and other defects during the manufacturing process, as uneven copper distribution can lead to stress and deformation of the panel.
-
What are the most common depaneling methods for PCB panels?
-
The most common depaneling methods for PCB panels are V-scoring, tab routing, laser cutting, and die punching. The choice of method depends on factors such as the PCB design, material, and application requirements.
-
Why is microsectioning performed on PCB panels?
-
Microsectioning is a destructive testing method that involves cutting a small sample from the PCB panel and examining it under a microscope. This process allows for the inspection of the internal structure of the PCB, including laminate integrity, layer registration, drilled hole quality, and copper trace dimensions.
-
What are the recommended storage conditions for PCB panels?
- PCB panels should be stored in a cool, dry environment with a temperature range of 10-30°C and a relative humidity of 30-70%. They should be packaged in clean, dust-free materials, such as antistatic bags or containers, and stacked horizontally with appropriate support to prevent warping or bending.
Conclusion
PCBs delivered in panels offer numerous advantages, including increased production efficiency, reduced costs, improved quality control, and simplified handling and storage. By following the guidelines outlined in this article, designers, manufacturers, and end-users can ensure that their PCB panels meet the required specifications and perform as intended.
Key considerations for designing PCBs for panel manufacturing include board size and shape, panelization layout, copper balancing, and the application of solder mask and silkscreen. During the manufacturing process, proper material selection, fabrication techniques, and depaneling methods are essential for producing high-quality PCB panels.
To ensure the quality and performance of PCB panels, a rigorous quality control and testing process is necessary, including visual inspection, electrical testing, microsectioning, and environmental testing. Proper handling and storage of PCB panels are also crucial to maintain their integrity and functionality over time.
By understanding and adhering to these panel guidelines, designers, manufacturers, and end-users can optimize the production and use of PCBs in a wide range of applications, from consumer electronics to industrial equipment and aerospace systems.
Leave a Reply