What is OSP?
Organic Solderability Preservative (OSP) is a chemical coating applied to the copper surfaces of a PCB to prevent oxidation and maintain solderability. OSP coatings are typically composed of organic compounds, such as benzimidazoles or benzotriazoles, which form a thin, transparent layer on the copper surface.
Advantages of OSP
- Cost-effective compared to other surface finishes
- Environmentally friendly (no heavy metals)
- Provides good solderability
- Suitable for fine-pitch components
- Allows for easy visual inspection of solder joints
Disadvantages of OSP
- Limited shelf life (typically 6-12 months)
- Susceptible to contamination and handling damage
- May require additional cleaning steps before assembly
- Not suitable for multiple reflow cycles or high-temperature applications
Common OSP PCB Issues
1. Poor Solderability
One of the most common issues with OSP-finished PCBs is poor solderability. This can be caused by several factors, including:
- Inadequate OSP coating thickness
- Contamination of the OSP coating
- Exposure to high humidity or temperature
- Prolonged storage beyond the recommended shelf life
Solutions
- Ensure proper OSP coating thickness (typically 0.2-0.5 µm)
- Maintain clean storage and handling conditions
- Use moisture barrier bags with desiccants for storage
- Assemble PCBs within the recommended shelf life
- Consider alternative surface finishes for longer shelf life or harsher environments
2. Solder Mask Adhesion Issues
OSP coatings can sometimes interfere with the adhesion of solder mask to the copper surface, leading to delamination or peeling of the solder mask.
Solutions
- Use compatible solder mask materials with OSP
- Ensure proper surface preparation before applying solder mask
- Optimize the solder mask curing process
- Consider alternative surface finishes or solder mask materials
3. Copper Etching and Undercut
OSP coatings can be affected by the copper etching process, resulting in uneven coating thickness or copper undercut at the edges of pads and traces.
Solutions
- Optimize the copper etching process to minimize undercut
- Use a controlled etching process, such as differential etching or pulse plating
- Consider alternative surface finishes for critical applications
4. Electrical Contact Resistance
OSP coatings can increase the electrical contact resistance between the PCB pads and component leads, particularly for press-fit connectors or test points.
Solutions
- Use a thicker OSP coating on contact areas
- Consider selective plating of contact areas with a more conductive surface finish
- Use a higher contact force for press-fit connectors
- Perform regular cleaning and maintenance of test points
5. Solder Joint Reliability
OSP-finished PCBs can be prone to solder joint reliability issues, such as poor wetting, voiding, or creeping.
Solutions
- Ensure proper solder paste selection and printing
- Optimize reflow profile and parameters
- Use a nitrogen atmosphere during reflow to reduce oxidation
- Consider alternative surface finishes for high-reliability applications
OSP Application Process
The OSP application process typically involves the following steps:
- Surface Preparation
- Cleaning: Remove contaminants and oxides from the copper surface
-
Microetching: Create a uniform surface roughness for better OSP adhesion
-
OSP Coating
- Dipping: Immerse the PCB in the OSP solution
- Spraying: Apply the OSP coating using a spray system
-
Roller Coating: Apply the OSP coating using a roller
-
Drying
- Prebaking: Remove moisture from the PCB
-
Final Baking: Cure the OSP coating at a specific temperature and duration
-
Inspection
- Visual Inspection: Check for coating uniformity, defects, or contaminants
- Thickness Measurement: Verify the OSP coating thickness using X-ray fluorescence (XRF) or other methods
OSP Application Parameters
Parameter | Typical Range |
---|---|
OSP Concentration | 2-5% |
Dipping Time | 30-60 seconds |
Drying Temperature | 80-120°C |
Drying Time | 10-30 minutes |
Final Thickness | 0.2-0.5 µm |
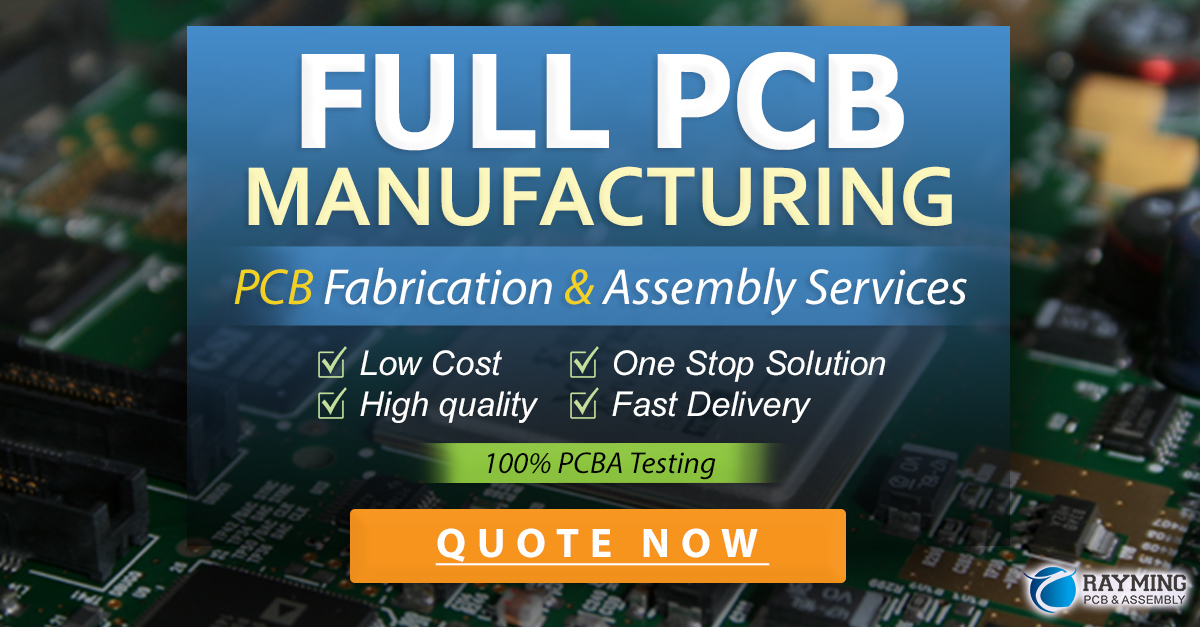
Frequently Asked Questions (FAQ)
1. What is the shelf life of OSP-finished PCBs?
The shelf life of OSP-finished PCBs is typically 6-12 months, depending on the storage conditions and the specific OSP formulation used. It is essential to store OSP-finished PCBs in a cool, dry environment and use them within the recommended shelf life to ensure optimal solderability.
2. Can OSP be used for high-temperature applications?
OSP coatings are generally not recommended for high-temperature applications, such as multiple reflow cycles or exposure to temperatures above 150°C. In these cases, alternative surface finishes, such as ENIG (Electroless Nickel Immersion Gold) or ENEPIG (Electroless Nickel Electroless Palladium Immersion Gold), may be more suitable.
3. How can I test the solderability of OSP-finished PCBs?
Solderability Testing of OSP-finished PCBs can be performed using various methods, such as:
- Wetting Balance Test: Measures the wetting force and time of a solder ball on the PCB surface
- Dip and Look Test: Involves dipping the PCB in molten solder and visually inspecting the solder coverage
- Edge Dip Test: Dips the edge of the PCB in molten solder and assesses the solder wetting along the edge
4. Can OSP be selectively applied to specific areas of a PCB?
Yes, OSP can be selectively applied to specific areas of a PCB using masking techniques or selective coating methods. This can be useful in situations where different surface finishes are required for different components or when OSP is not suitable for certain areas of the PCB.
5. How does OSP compare to other surface finishes in terms of cost?
OSP is generally one of the most cost-effective surface finishes for PCBs. It is typically less expensive than other finishes, such as HASL (Hot Air Solder Leveling), ENIG, or ENEPIG. However, the total cost of using OSP should also consider the potential need for additional cleaning steps, shorter shelf life, and the risk of rework or scrap due to solderability issues.
Conclusion
OSP is a widely used surface finish for PCBs, offering cost-effectiveness and environmental benefits. However, OSP-finished PCBs can be prone to various issues, such as poor solderability, solder mask adhesion problems, copper etching and undercut, electrical contact resistance, and solder joint reliability concerns.
By understanding these challenges and implementing appropriate solutions, such as optimizing the OSP application process, maintaining proper storage conditions, and considering alternative surface finishes when necessary, manufacturers can mitigate the risks associated with OSP and produce high-quality, reliable PCBs.
As with any surface finish, it is essential to carefully evaluate the specific requirements of the application and work closely with PCB manufacturers and assembly partners to select the most suitable solution for each project.
Leave a Reply