What is OSP PCB?
OSP (Organic Solderability Preservative) is a popular surface finish used on printed circuit boards (PCBs) to enhance their solderability and protect the exposed copper from oxidation. OSP PCB involves applying a thin, transparent layer of organic compounds on the copper pads and through-holes of the PCB. This organic coating acts as a barrier against oxidation, ensuring that the PCB remains solderable for a certain period.
Composition of OSP
The OSP coating typically consists of benzimidazole or benzotriazole compounds, which form a complex with the copper surface. These organic compounds bond with the copper, creating a protective layer that prevents oxidation and maintains solderability.
Advantages of OSP PCB
OSP PCB offers several advantages compared to other surface finishes:
- Cost-effective: OSP is one of the most economical surface finishes available, making it an attractive option for budget-conscious projects.
- Flat surface: The thin OSP coating maintains a flat surface on the copper pads, facilitating accurate component placement during assembly.
- Excellent solderability: OSP provides good solderability, ensuring reliable solder joints during the assembly process.
- Environmentally friendly: Unlike some other surface finishes, OSP does not contain lead or other hazardous materials, making it an eco-friendly choice.
- Suitable for various applications: OSP PCB is versatile and can be used in a wide range of applications, including consumer electronics, automotive, and industrial devices.
OSP PCB Manufacturing Process
The manufacturing process for OSP PCB involves several steps to ensure a high-quality finish:
Step 1: PCB Fabrication
The PCB is fabricated using standard processes, such as etching, drilling, and plating. The board is then cleaned to remove any contaminants or residues.
Step 2: Micro-etching
Before applying the OSP coating, the copper surface undergoes a micro-etching process. This step removes any oxide layer and roughens the surface slightly, promoting better adhesion of the OSP coating.
Step 3: OSP Application
The OSP coating is applied to the PCB using either a dipping or spraying method. The board is immersed in or sprayed with the OSP solution, ensuring complete coverage of the copper surfaces.
Step 4: Drying
After the OSP application, the PCB is dried in an oven to evaporate any excess solvent and allow the organic compounds to form a stable complex with the copper surface.
Step 5: Inspection
The OSP-coated PCB undergoes a visual inspection to ensure uniform coverage and the absence of any defects or contamination.
Shelf Life and Storage of OSP PCB
One of the limitations of OSP PCB is its relatively short shelf life compared to other surface finishes. The organic coating can degrade over time, affecting the solderability of the PCB. Factors that influence the shelf life of OSP PCB include:
- Temperature: High temperatures can accelerate the degradation of the OSP coating.
- Humidity: Exposure to high humidity levels can lead to the growth of copper oxide beneath the OSP layer.
- Handling: Improper handling, such as touching the OSP-coated surfaces with bare hands, can introduce contaminants that degrade the coating.
To maximize the shelf life of OSP PCB, it is essential to store the boards in a controlled environment with the following conditions:
Parameter | Recommended Range |
---|---|
Temperature | 10°C to 30°C |
Humidity | 30% to 70% RH |
Additionally, OSP PCBs should be packaged in moisture barrier bags with desiccants to protect them from humidity during storage and transportation.
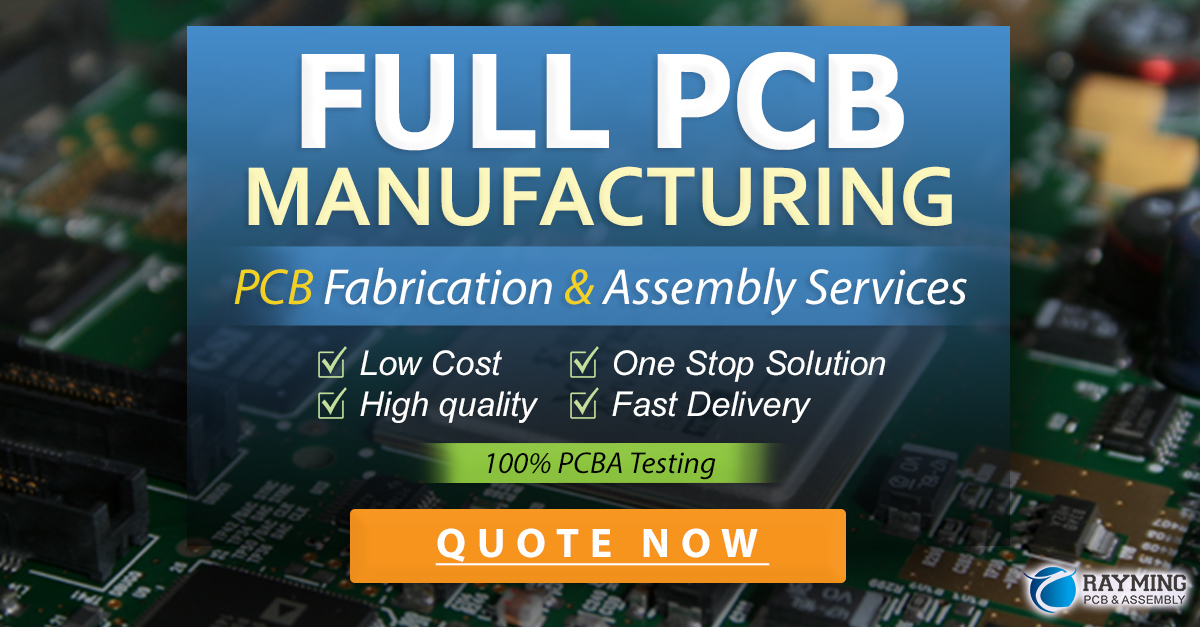
Soldering Considerations for OSP PCB
When soldering components onto an OSP PCB, there are a few considerations to keep in mind:
Soldering Temperature
OSP PCBs can be soldered using standard reflow or wave soldering processes. However, it is essential to control the soldering temperature to prevent damage to the OSP coating. Excessive heat can cause the organic compounds to decompose, compromising the solderability of the PCB.
Soldering Process | Recommended Temperature Range |
---|---|
Reflow Soldering | 230°C to 260°C |
Wave Soldering | 250°C to 280°C |
Flux Selection
The choice of Soldering Flux is crucial when working with OSP PCBs. It is recommended to use a mild, no-clean flux that is compatible with the OSP coating. Aggressive fluxes can attack the organic layer, leading to degradation and poor solderability.
Solder Paste
When using solder paste for reflow soldering, it is essential to choose a paste with a compatible flux and a suitable metal content. The solder paste should have good wetting properties to ensure reliable solder joints on the OSP-coated pads.
Comparing OSP with Other PCB Surface Finishes
OSP is one of several surface finishes used in PCB manufacturing. Here’s a comparison of OSP with other popular surface finishes:
Surface Finish | Advantages | Disadvantages |
---|---|---|
OSP | – Cost-effective – Flat surface – Good solderability – Environmentally friendly |
– Limited shelf life – Susceptible to contamination – Not suitable for multiple reflow cycles |
ENIG | – Excellent solderability – Long shelf life – Suitable for multiple reflow cycles |
– Higher cost – Potential for black pad formation – Requires precise process control |
Immersion Tin | – Good solderability – Flat surface – Suitable for press-fit connections |
– Limited shelf life – Prone to tin whisker formation – Incompatible with some lead-free solders |
HASL | – Excellent solderability – Low cost – Suitable for high-temperature applications |
– Uneven surface – Potential for bridging and shorts – Contains lead (in SnPb HASL) |
The choice of surface finish depends on various factors, including the specific application, budget, shelf life requirements, and environmental considerations.
FAQ
1. What is the typical thickness of the OSP coating?
The OSP coating is extremely thin, typically measuring between 0.2 and 0.5 microns (µm) in thickness. This thin layer is sufficient to protect the copper surface from oxidation while maintaining good solderability.
2. Can OSP PCBs be reworked?
Yes, OSP PCBs can be reworked, but it is essential to exercise caution. The rework process should be performed at a lower temperature than the initial soldering to avoid damaging the OSP coating. After rework, the exposed copper area may need to be re-coated with OSP to protect it from oxidation.
3. How long does the OSP coating last?
The shelf life of OSP PCBs varies depending on storage conditions and the specific OSP formulation used. Generally, OSP-coated boards can maintain good solderability for 6 to 12 months when stored in a controlled environment with proper packaging.
4. Is OSP suitable for high-frequency PCBs?
Yes, OSP is a suitable surface finish for high-frequency PCBs. The thin, flat nature of the OSP coating minimizes the impact on the electrical performance of the PCB, making it a good choice for high-speed and high-frequency applications.
5. Can OSP be used on Gold Fingers?
No, OSP is not recommended for use on gold fingers, which are the edge contacts used for plug-in connections. Gold fingers require a hard, wear-resistant surface finish, such as electroplated gold or hard gold, to withstand the repeated insertion and removal cycles. OSP is too soft and thin to provide the necessary durability for gold fingers.
Leave a Reply